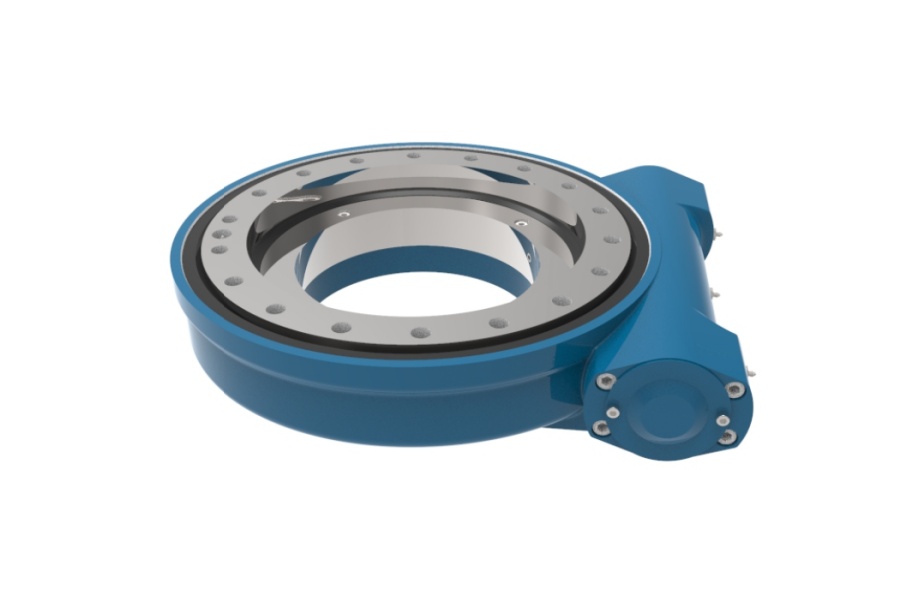
Worm Gear Drive WE12: The Precision Heart of Industrial Power, A Mighty Foe to Hot Rolling Mill Challenges!
What is the Worm Gear Drive WE12?
The core of the Worm Gear Drive WE12 lies in its unique meshing design of the worm and worm wheel. The worm resembles a precision screw. When it rotates as the driving component, its threaded tooth surface tightly meshes with the tooth surface of the worm wheel (a specially designed helical gear), efficiently transmitting motion and power at a 90-degree angle. WE12 represents a specific series or model within this transmission form, typically signifying that its size specifications, load capacity, and performance parameters comply with specific industrial standards. It is developed for applications demanding compact structure, large transmission ratio, reliable self-locking, and the ability to withstand heavy loads and impacts. It is a key component in modern machinery for achieving speed reduction and torque increase, precise indexing, and transmission in space-constrained situations.
WE12 Maximum Output Torque: Robust Guarantee of Powerful Torque
One of the core advantages of the WE12 worm gear drive is its powerful torque output capability. Its maximum output torque can reach an astonishing 8000 Nm or even higher (specific values need confirmation based on the actual model specifications). This means that at the low-speed output end, it can generate immense rotational force, effortlessly driving heavy loads. This characteristic makes it an ideal power transmission hub for mining machinery, metallurgical equipment, large mixing systems, heavy-duty conveyor lines, and other occasions requiring overcoming significant resistance. The robust torque-bearing design ensures stable operation and long service life under high loads.
WE12 Worm Gear Reducer: Compact and Efficient Power Hub
The WE12 Worm Gear Reducer is a highly integrated power unit combining the worm, worm wheel, precision bearings, high-strength housing, and lubrication system. Its core advantages lie in:
Large Transmission Ratio: Achieves a very large reduction ratio (typically from 5:1 to 100:1 or higher) in a single stage, with an extremely compact structure.
Smooth and Quiet Operation: The characteristic of multiple teeth meshing simultaneously results in smooth operation and low noise levels.
Reverse Self-Locking: Under specific lead angle designs, it possesses good reverse self-locking performance, preventing load reversal and enhancing safety.
High Load Capacity: Optimized tooth profile design and material selection give it excellent impact resistance and overload capacity. The WE12 reducer is a model of integration and high performance, providing reliable power for complex machinery.
Guardian Against Thermal Deformation in Hot Rolling Mills: WE12's Robust Solution
Hot continuous rolling mills are the core of steel production, where components like roller tables and screw-down mechanisms operate in the harsh environment of nearly thousand-degree Celsius temperatures. Ordinary transmission components are prone to loss of precision, jamming, or even damage due to thermal expansion. The WE12 worm gear drive demonstrates extraordinary value in this scenario:
Material and Process Advancement: Uses special high-temperature-resistant alloy steel worms and high-strength wear-resistant copper alloy worm wheels, supplemented by strengthening processes like deep carburizing and quenching, ensuring high-temperature hardness and wear resistance.
Thermal Expansion Compensation Design: The housing employs ductile iron or special alloys, applying precise thermo-symmetric structural design and preload adjustment technology to effectively offset the uneven expansion of different materials at high temperatures, maintaining stable meshing clearance.
Efficient Heat Dissipation Solution: Optimized housing cooling fin design, integrating forced circulation cooling systems (oil/air cooling) when necessary, rapidly expelling internal friction heat and environmental radiant heat to control temperature rise.
High-Temperature Long-Life Lubrication: Uses synthetic high-temperature grease or forced circulation filtered oil systems to ensure full lubrication of tooth surfaces under extreme temperatures, reducing wear and seizure risk. These targeted designs allow the WE12 to stand firm amidst high-temperature heat waves, ensuring continuous high-precision operation of the rolling mill, significantly reducing downtime caused by thermal deformation, acting as the stable and efficient "steel backbone" of the hot continuous rolling production line.
The Outstanding Features of Worm Gear Drive WE12
The WE12 worm gear drive has become the preferred choice for numerous demanding applications because it combines multiple advantages:
Exceptional Torque Density: Generates powerful torque within a compact structure, saving installation space.
Superlative Durability and Reliability: Carefully selected materials and advanced manufacturing processes ensure long life and high reliability, reducing maintenance costs.
Precise and Smooth Transmission: Smooth transmission, low noise and vibration, high output precision, meeting precise control requirements.
Excellent Self-Locking Performance: (Under specific conditions) Effectively prevents load reversal, ensuring system safety.
Superior Environmental Adaptability: Professional sealing design (IP65/IP66 or higher) effectively prevents dust and water ingress. Particularly, the optimized anti-thermal deformation design for high-temperature conditions (like the aforementioned hot rolling mills) is its core competitive strength, making it irreplaceable in industries like metallurgy and building materials.
Easy Maintenance: Reasonable structural design facilitates inspection, lubrication, and maintenance.
The Vast Application Realm of Worm Gear Drive WE12
Leveraging its unique advantages, the WE12 worm gear drive excels in numerous industrial fields:
Metallurgical Industry: Core power source for roller tables, screw-down devices, pushers, tension levelers, and shearing equipment in hot/cold continuous rolling mills, especially adept at handling high-temperature challenges.
Heavy Mining Machinery: Drive and reduction unit for ball mills, crushers, large conveying equipment, and lifting machinery.
Building Materials Industry: Key transmission component for cement rotary kiln drives, large mixers, brick machines, and glass production lines.
Material Handling: Lifting and traveling mechanisms for heavy cranes (overhead cranes), large stacker-reclaimers, and port handling equipment.
Chemical and Rubber/Plastics Machinery: Power transmission for heavy equipment like internal mixers, large extruders, and calenders.
Energy and Environmental Protection: Wind turbine yaw/pitch systems (some designs), flue gas desulfurization agitators, large gate hoists for water treatment.
Special Equipment: Stage machinery, large radars, ship deck machinery, and other occasions requiring large reduction ratios and reliability.
WE12 Worm Gear Drive Price Decoded: Key Factors Behind the Value
The price of the WE12 worm gear drive is not a single number; it is shaped by multiple core factors:
Specification and Torque Rating: Output torque requirements (e.g., 5000Nm vs 10000Nm) directly affect material size, processing difficulty, and cost.
Transmission Ratio Range: Different reduction ratio designs affect the size and complexity of the worm and wheel.
Materials and Processes: High-temperature anti-deformation alloy worm gears/wheels, special heat treatment processes (like deep carburizing and quenching), and high-precision gear grinding costs are far higher than those for ordinary materials and processes. Housing material (e.g., high-strength cast iron vs welded steel) is also key.
Manufacturing Precision Grade: Higher precision requirements (e.g., higher grades in DIN or AGMA standards) mean more precise machining and inspection, significantly increasing costs.
Special Designs like Anti-Thermal Deformation: Customized thermo-symmetric structures, enhanced cooling systems, high-temperature seals, and lubrication schemes for environments like hot rolling mills inevitably increase technical content and manufacturing costs.
Configuration and Accessories: Inclusion of forced cooling systems, special seals (e.g., double-lip skeleton oil seals), specific mounting flanges/output shaft forms, sensor interfaces (e.g., temperature control, vibration monitoring), etc., affects the price.
Brand and Technical Service: Technical assurance from well-known brands, comprehensive after-sales service networks, and customized engineering support capabilities usually command a premium.
Purchase Volume and Customization Level: Bulk purchases usually offer price advantages, while highly customized non-standard products have a higher unit price.
The Worm Gear Drive WE12 is undoubtedly a "heavy-duty workhorse" in the field of industrial power transmission. It combines high torque, high reliability, excellent anti-thermal deformation capability, and a compact structure into one, demonstrating irreplaceable value, especially in the most severe high-temperature, heavy-load environments (like the heart of hot rolling mills). Understanding its powerful torque output, ingenious reduction structure, targeted anti-heat solutions, broad application scenarios, and the key factors shaping its pricing system is crucial for engineer selection and procurement decisions. Choosing WE12 is not just selecting a transmission product; it's choosing a durable, stable, and efficient power foundation for critical equipment. When your production line faces the dual challenges of high temperature and heavy load, WE12 is the key to breaking through—resolving thermal expansion with precision structure and driving industrial progress with surging torque!
Supplier of Worm Gear Drive WE12
Seeking the optimal power solution for your critical equipment? Contact LYRADRIVE Bearing's technical team immediately for personalized Worm Gear Drive WE12 selection advice and consultation.