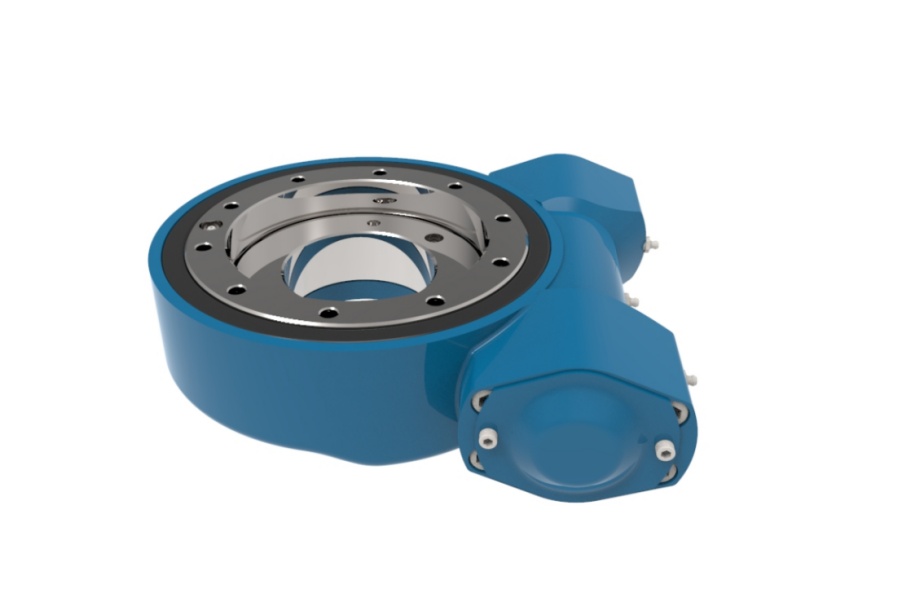
Worm Gear Drive WE7: The Power Heart of Heavy-Duty Mixing Equipment
What is the WE7 Worm Gear Drive?
A worm gear drive is a classic mechanical power transmission form. Its core principle utilizes the meshing of a worm (usually the driving part, resembling a screw) and a worm wheel (the driven part, with special tooth geometry) to convert high-speed rotary motion from the input shaft into low-speed, high-torque rotary motion at the output shaft. The WE7 is an outstanding representative model of this principle in the field of industrial reducers. Provided by professional manufacturers like LYRADRIVE, the WE7 series worm gear typically feature a golden combination of a high-strength alloy steel precision worm and a wear-resistant copper alloy worm wheel, housed in a high-strength cast iron casing. This design ensures rigidity and stability when transmitting large torques. Its most notable characteristics include providing an extremely high single-stage reduction ratio (typically i=7.5-100, or even higher), enabling spatially crossed-axis transmission (usually at 90 degrees), and possessing inherent self-locking capability (under specific conditions). The WE7 series excels with its compact design, robust structure, smooth operation, low noise, and strong load-carrying capacity, making it particularly suitable for demanding industrial scenarios like mixing equipment that require large reduction ratios, high output torque, space constraints, and high demands for shutdown safety.
Core Guide: How to Precisely Select a WE7 Worm Gear Reducer for Your Mixing Equipment?
Selecting the right WE7 worm gear reducer for mixing equipment is a critical decision directly impacting operational efficiency, lifespan, and safety. Here are the core selection considerations based on WE7 characteristics:
Accurately Calculate Required Output Torque: This is the primary parameter for selection. Torque demand is determined by the shape, size, and number of impeller blades, the density and viscosity of the mixing medium, tank size, fill level, and the desired mixing effect (e.g., blending, suspension, dispersion). Detailed calculation or empirical formulas must be used to determine the maximum resistance torque generated during mixing. The rated output torque of the selected WE7 reducer must be greater than or equal to this maximum resistance torque, incorporating a safety factor (typically 1.5-2.0) to account for start-up shock, medium fluctuations, etc. LYRADRIVE provides professional torque calculation support.
Determine Operating Speed Range: Mixing processes have specific speed requirements. The WE7 reducer's role is to drastically reduce the motor's high speed (e.g., 1440 rpm or 960 rpm) to the low speed required by the mixing shaft (typically a few to several tens of RPM). Determine the target output shaft speed based on process needs, combine it with the motor input speed, and calculate the required reduction ratio (i). Then, select a WE7 model offering that ratio. Note that the same WE7 model may offer multiple ratio options.
Evaluate Installation Space & Connection Method: The WE7's inherent structural compactness is a highlight for space-constrained mixing equipment. However, carefully measure the reserved installation space to ensure the selected model fits. Also, define the connection method between the reducer and motor (direct coupling, belt pulley, etc.), the alignment connection method between the output shaft and mixing shaft (e.g., coupling type), and the mounting orientation (foot mounting, flange mounting, etc.). WE7 typically offers flexible mounting options.
Consider Medium Properties & Environmental Factors: The mixing medium may be corrosive, abrasive, high-temperature, or flammable/explosive. This directly impacts the requirements for the WE7 reducer's sealing performance and material selection:
Sealing: For volatile, corrosive, or clean-environment media (e.g., food, pharmaceuticals), high-performance shaft seals (e.g., double-lip oil seals, mechanical seals) are needed to prevent medium ingress into the reducer or lubricant leakage contaminating the medium. LYRADRIVE WE7 offers various sealing solutions.
Material: In highly corrosive environments, special anti-corrosion treatment or materials (e.g., stainless steel options, albeit at higher cost) for the casing or parts may be required. The standard WE7 casing is high-strength cast iron, offering good rigidity and economy.
Ambient Temperature & Protection Rating: High ambient temperatures require attention to the lubricant's temperature resistance; humid or dusty environments demand higher Ingress Protection (IP) ratings, like IP65, to ensure internal component safety. WE7 typically has good basic protection capabilities.
Match Motor Power: Once the WE7 model (determining rated torque and ratio) is selected, the required motor power and type (e.g., standard 3-phase induction motor, explosion-proof motor, variable frequency drive motor) must be deduced. Ensure the motor power is sufficient to deliver the required torque and speed through the WE7 reducer, while avoiding energy waste from an oversized motor ("big horse pulling small cart"). Formula: `Motor Power ≈ (Output Torque Output Speed) / (9550 Reducer Efficiency)`. WE7 worm gear drive efficiency is typically in the 70%-90% range (single-stage); larger ratios generally have lower relative efficiency – this loss must be factored into selection.
Core Strength: In-Depth Analysis of WE7 Worm Gear Drive Output Torque
Output torque is the most critical indicator measuring the driving capability of the WE7 worm gear reducer and its core value in heavy-duty mixing applications. The core advantage of the WE7 series lies in its ability to deliver exceptionally strong low-speed output torque. The scientific principles behind this are its unique meshing method:
High Reduction Ratio Achieves Torque Amplification: Worm drives inherently achieve ultra-large single-stage reduction ratios (WE7 typical range i=7.5-100). Based on power conservation principles (ignoring efficiency losses): `Output Torque ≈ Input Torque Reduction Ratio Efficiency`. This means that with a given input power, a higher reduction ratio results in lower output speed and significantly amplified output torque. The WE7 leverages this principle to efficiently transform the motor's smaller input torque and higher speed into the massive torque and very low speed required by mixing equipment.
Multi-Tooth Engagement Distributes Load: The meshing between the worm and worm wheel is line contact, and relatively more teeth are engaged simultaneously (compared to gear drives). This disperses the load over a larger contact area, endowing the WE7 with outstanding load capacity and impact resistance. It can stably deliver the calculated high torque, even facing viscous materials during mixing or start-up shock loads.
Actual Torque Range: The specific output torque range of WE7 worm gear reducers is very broad, ranging from several hundred Newton meters (Nm) to several thousand Newton meters (Nm). This entirely depends on the specific model size (e.g., WE70, WE80, WE100, etc. – larger numbers generally indicate higher torque) and the chosen reduction ratio. For example, a medium-sized WE7 reducer at a high ratio can easily exceed 2000 Nm or more, sufficient to drive heavy impellers in large mixing tanks. The product manuals provided by LYRADRIVE for WE7 detail the rated output torque values for each model at different ratios – this is the key basis for selection. Always ensure the selected model's rated torque meets the mixing process requirements with a safety margin.
Outstanding Features: Core Characteristics of the WE7 Worm Gear Drive
The WE7 worm gear reducer is a popular choice for mixing equipment drives due to its series of irreplaceable, significant characteristics:
Ultra-Large Single-Stage Reduction Ratio: As mentioned, a single stage achieves ratios from 7.5 to 100 or larger. This simplifies structure, shortens the drive chain, enhances reliability, and offers good cost-effectiveness.
Excellent Self-Locking Property: This is a hallmark feature of worm drives, especially crucial for mixing equipment. When the worm's lead angle is less than the equivalent friction angle of the meshing teeth, the drive is self-locking. This means the worm can drive the wheel, but the wheel cannot back-drive the worm. In mixing equipment, this ensures the mixing shaft stops immediately when the motor stops, preventing reversal due to material gravity or inertia. This greatly enhances operational safety, particularly for top-entry mixers or handling hazardous materials.
Compact Structure, High Space Utilization: The WE7 design is refined, delivering large ratios and high torque output while maintaining a relatively small footprint. Its input and output shafts are spatially crossed at 90 degrees, facilitating flexible arrangement within equipment, especially suitable for installation in space-constrained tops or sides of mixing vessels.
Smooth Operation, Low Noise: The meshing of the worm and wheel teeth is progressive, continuous multi-tooth contact. The transmission process is smooth and steady, generating significantly less vibration and noise compared to some gear drives, contributing to an improved working environment.
Strong Load Capacity, Good Impact Resistance: Line contact and a large contact area give the WE7 good load distribution capability. It can withstand significant overload and impact loads (e.g., impellers encountering lumps or start-up surges), making it suitable for complex mixing applications.
Precise and Stable Transmission Ratio: Well-manufactured WE7 reducers (like those from LYRADRIVE) ensure constant and precise transmission ratios, guaranteeing stable mixing speeds. This is vital for processes requiring precise mixing control (e.g., chemical reactions, precision batching).
Relatively Simple Maintenance: Mature design and a reliable lubrication system (typically oil bath lubrication) ensure long service life with relatively low maintenance requirements under conditions of correct selection, installation, and lubricant use.
In Action: Wide Application of WE7 Worm Gear Drives in Mixing Equipment
Leveraging its core advantages of low-speed high torque, self-locking safety, compactness, and reliability, the WE7 worm gear reducer acts as the "power heart" in numerous industrial fields requiring powerful mixing:
Chemical Industry: Driving various reactor agitators for material mixing, dissolution, polymerization, sulfonation, nitration, etc. Corrosion-resistant options (special seals, coatings) handle harsh environments like strong acids/bases.
Food & Beverage Industry: Applied in sauce mixing tanks, candy cooking kettles, dairy fermentation tanks, beverage blending tanks, etc. High hygiene requirements necessitate food-grade lubricants and well-sealed WE7 models.
Water Treatment & Environmental Protection: Driving mixers in wastewater flocculation basins, coagulation tanks, neutralization tanks, and sludge digesters to promote chemical mixing and reactions. Its powerful torque handles high-viscosity sludge.
Pharmaceutical Industry: Used in bio-fermenters, solution preparation tanks, mixing/homogenizing equipment, requiring smooth operation, contamination-free, and easy cleaning. High IP ratings and good sealing are key.
Building Materials Industry: Driving mortar mixers, putty powder blenders, paint dispersers, etc., handling high-density, highly abrasive materials.
Petroleum & Daily Chemicals Industry: Applied in lubricant blending tanks, cosmetic emulsifying kettles, detergent batching tanks, etc.
Other Industrial Mixing Fields: Such as for pigments, dyes, adhesives, feed, battery slurries, etc.
In these applications, the WE7 reducer provides continuous, stable, and powerful rotational force to the impellers, ensuring materials achieve the desired mixing, dispersion, suspension, or reaction effects. It is a key component guaranteeing product quality and production efficiency.
Investment Analysis: Key Factors Affecting WE7 Worm Gear Drive Pricing
The price of a WE7 worm gear reducer is not fixed; it is influenced by several factors. Understanding these helps users make more reasonable procurement budgets and selection decisions:
Raw Material Cost: The most fundamental factor. Material costs for the copper alloy worm wheel (e.g., tin bronze) and alloy steel worm constitute a significant portion, and their market price fluctuations directly impact unit cost. The grade and weight of the high-strength cast iron casing also contribute. Special materials (e.g., stainless steel) cost more.
Model Size & Load Capacity: The WE7 series includes different center distance sizes (e.g., WE70, WE80, WE100...). Larger sizes with higher rated output torque/power use more material and involve more complex manufacturing, naturally commanding higher prices. Within the same size, models designed for higher load capacity usually imply stronger structures/materials.
Reduction Ratio: While large ratios are a WE7 feature, within the same size, different ratios involve variations in worm/wheel design parameters (e.g., number of worm starts, worm wheel teeth), potentially causing slight differences in manufacturing difficulty/material usage and price.
Manufacturing Process & Precision Grade: Machining precision (e.g., worm grinding, casing machining) directly affects meshing quality, transmission efficiency, noise, and lifespan. High-precision manufacturing requires more sophisticated equipment and stricter process control, increasing costs. Heat treatment quality (e.g., worm surface hardening) also affects price and performance. Reputable brands like LYRADRIVE typically invest more in process and quality control.
Configuration & Customization Level:
Input/Output Form: Standard is solid shaft. Special requirements like hollow shaft (with locking assembly), flange input/output, special keyways/splines increase cost.
Motor Matching: Whether a matched motor (standard, explosion-proof, VFD, etc.) is included significantly affects total price. Explosion-proof and VFD motors are more expensive.
Sealing Grade: Standard sealing suffices for general use. Higher-grade seals (double seals, special materials, even magnetic seals) for harsh conditions increase cost.
Lubrication Method: Standard is oil bath. Special requirements like forced lubrication systems add complexity and cost.
Surface Treatment & Painting: Special anti-corrosion coatings (e.g., Teflon) or higher-grade surface treatments add cost.
Accessories: Add-ons like backstops, forced cooling fans, oil temperature/level sensors, special mounting bases.
Brand & Market Supply/Demand: Reputable brands command a premium based on technical expertise, quality reputation, and after-sales service. Market supply and demand also influence price; prices may rise during material shortages or high demand periods.
Procurement Channel & Quantity: Buying directly from the manufacturer (like LYRADRIVE) or large authorized distributors usually offers better pricing than multi-layer agents. Bulk purchases typically secure better discounts.
Therefore, when requesting quotes or purchasing WE7 worm gear reducers, always provide detailed technical parameters (torque, power, ratio, mounting) and operating conditions (medium, temperature, protection, sealing grade), plus any customization needs. The professional team at LYRADRIVE will provide the most cost-effective WE7 solution and technical support based on your specific requirements.
Supplier of Worm Gear Drive WE7
LYRADRIVE , deeply rooted in the transmission field, provides you with high-performance, high-reliability WE7 worm gear reducer products and professional mixing equipment drive solutions. From precise selection consultation to comprehensive after-sales service, we are committed to being your trusted power partner, helping your mixing processes run efficiently, stably, and safely! Contact us immediately for a customized selection plan and quotation!