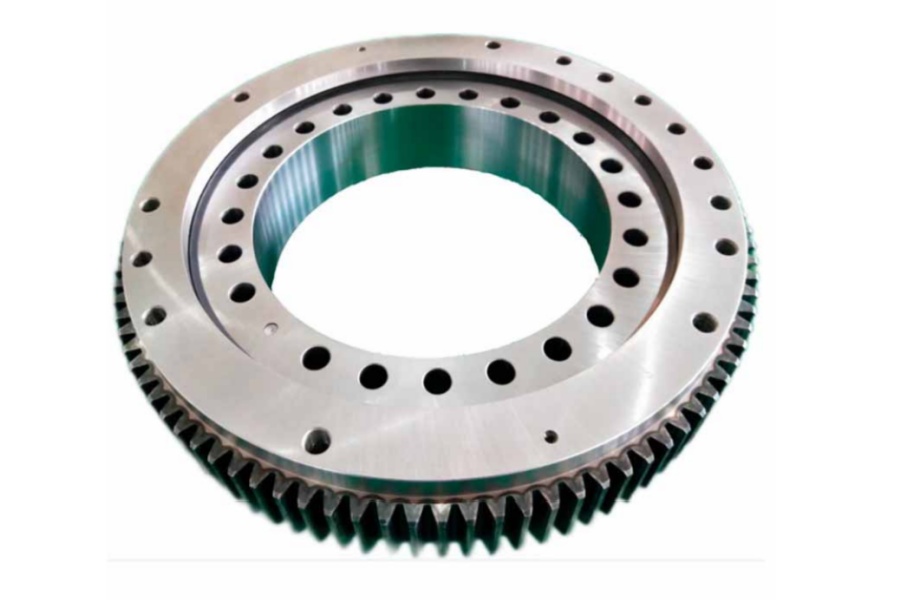
The Silent Powerhouse: How Truck Crane Slewing Bearings Lift the World on Wheels
What is a Truck Crane Slewing Bearing?
A Truck Crane Slewing Bearing is a specialized large-diameter bearing mounted between the crane's upperworks (the rotating superstructure housing the boom, engine, cab, and winches) and the undercarriage/carrier (the truck chassis). It serves a critical dual purpose:
Load Bearing: It supports the entire weight of the crane's upperworks, including the boom at various angles, the load being lifted, and the dynamic forces generated during lifting, lowering, and swinging operations.
Rotation Enabler: It allows the upperworks to slew (rotate) smoothly and precisely through 360 degrees or more, enabling the operator to position loads accurately anywhere around the crane.
Designed for the unique demands of mobile equipment, these bearings must be:
Strong & Durable: Engineered to withstand massive axial loads (from the weight), radial loads (from boom side forces), and significant tilting moments (forces trying to tip the crane), often under harsh, variable conditions.
Compact & Lightweight: Space and weight are premium on a truck chassis. Slewing bearings must deliver maximum performance in a minimal envelope to avoid compromising crane stability or payload capacity.
Precise & Smooth: Ensure controlled, low-friction rotation for accurate load placement and operator safety, even under full load.
Robust & Reliable: Resistant to shock loads, vibration, dust, moisture, and temperature extremes encountered in construction, utility, and recovery work.
Integrated: Often incorporate gear teeth (for the slewing drive motor/pinion) and mounting holes directly on the bearing races.
How to Replace Crane Slewing Bearing: A Major Undertaking Requiring Precision
Replacing a slewing bearing on a truck crane is a significant, safety-critical operation, not a simple DIY task. Here's a high-level overview of the complex process:
Preparation is Paramount:
Safety First: Secure the crane on level, stable ground. Engage all outriggers fully and use blocking/jacking points as per manufacturer specs. Implement lockout/tagout procedures. Ensure personnel are trained and equipped with proper PPE.
Gather Resources: Obtain the exact replacement bearing (OEM recommended), specialized lifting equipment (large capacity crane or gantry), calibrated torque wrenches/hydraulic tensioners, alignment tools (laser preferred), manufacturer service manuals, and all necessary hardware (new bolts, seals, grease).
Documentation: Review the specific service manual procedures meticulously. Understand bolt tightening sequences and torque specs.
Disassembly - Careful Deconstruction:
Unload & Secure: Lower the boom fully to the ground or a secure cradle. Remove any counterweights if possible/required.
Access: Remove deck plates, covers, hydraulic lines (cap ends!), electrical connections (label everything!), and the slewing drive motor/pinion assembly.
Separation: Carefully lift the entire upperworks off the undercarriage using appropriately rated lifting gear attached to designated lift points. This exposes the slewing bearing.
Bearing Removal & Preparation:
Bolt Removal: Remove all slewing bearing mounting bolts following the specified sequence to avoid warping flanges. This often requires significant force.
Bearing Removal: Carefully lift the old bearing off the mounting surfaces. Clean the mounting flanges on both the upperworks and the undercarriage meticulously. Inspect for corrosion, damage, or warping. Repair or machine surfaces if necessary.
New Bearing Installation - Precision is Key:
Positioning: Carefully lower the new bearing into place, ensuring correct orientation (gear teeth alignment, lubrication ports). Use alignment pins if provided.
Bolt Installation & Torquing: Install new, high-grade bolts lubricated as specified. Follow the manufacturer's EXACT bolt tightening sequence and torque specifications in multiple stages (often including an initial torque, followed by a final torque, and sometimes an angular turn). Using incorrect torque is a leading cause of premature bearing failure. Hydraulic tensioners are often preferred for accuracy and safety on large bolts.
Sealing & Lubrication: Install new seals if required. Fill the bearing raceways with the specified type and quantity of grease through the lubrication ports before reassembly progresses too far.
Reassembly & Commissioning:
Lower Upperworks: Carefully lower the upperworks back onto the new bearing and undercarriage, ensuring alignment pins engage (if used).
Reconnect: Reattach hydraulic lines, electrical connections, the slewing drive motor/pinion (ensuring proper gear mesh backlash), deck plates, and covers.
Functional Checks: Before lifting loads, perform slow, controlled slewing in both directions without load. Check for smooth operation, unusual noises, leaks, and verify slewing drive functionality. Gradually perform load tests per manufacturer recommendations.
Single Row Ball Slewing Bearing: The Compact Workhorse for Truck Cranes
The most common type found on many truck cranes, especially mid-range models, is the Single Row Ball Slewing Bearing, typically designed as a Four-Point Contact Ball Bearing. Its popularity stems from key advantages:
Compact Design: Offers a high load capacity relative to its size and weight, crucial for mobile crane weight distribution.
Smooth Operation: Ball bearings provide lower starting torque and very smooth rotation, enhancing control for precision lifting.
Cost-Effectiveness: Generally simpler to manufacture than multi-row designs, offering good value.
Handles Combined Loads: The four-point contact design allows each ball to transmit axial loads in both directions and radial loads simultaneously, efficiently handling the complex forces experienced by a truck crane.
Integrated Gearing: Easily accommodates gear teeth machining on the inner or outer race for slewing drive engagement.
While incredibly capable, their load capacity has limits compared to roller designs. They are ideally suited for cranes where compactness, smoothness, and cost are balanced against the lifting capacity demands.
Slewing Bearing Torque Specs: The Critical Tightness Factor You Can't Ignore
Proper bolt tightening is arguably THE most critical factor in slewing bearing installation and longevity. Ignoring or incorrectly applying torque specifications is a direct path to catastrophic failure. Here's why torque specs matter so much:
Prevents Fretting & Loosening: Insufficient torque allows micro-movement between the bearing race and the mounting flange. This causes fretting corrosion, damaging the mating surfaces, and eventually leads to bolt loosening under vibration.
Distributes Load Evenly: Correct torque ensures the clamping force is evenly distributed across the entire flange and through all bolts. Uneven clamping creates stress concentrations that can crack the bearing races or flanges.
Prevents Race Distortion: Excessive torque can warp or distort the bearing races, compromising the precision geometry of the raceways. This leads to premature wear, increased friction, binding, and eventual failure.
Maintains Gear Mesh: Proper flange clamping ensures the gear teeth on the bearing race maintain correct alignment and backlash with the slewing pinion gear. Incorrect torque alters this mesh, causing noisy operation, accelerated wear, and potential tooth breakage.
Key Aspects of Torque Specs:
Manufacturer Dictates: Torque values and sequences are SPECIFIC to the crane model, bearing size, and bolt specification. NEVER guess or use generic values. ALWAYS consult the official [Crane Brand] service manual.
Sequence is Crucial: Bolts must be tightened in a specific cross-pattern sequence (like tightening a cylinder head) to ensure even clamping and prevent distortion. Skipping the sequence invalidates the torque.
Multiple Stages: Torquing often involves multiple passes (e.g., 50% torque, then 100% torque, sometimes followed by a specific angle turn) to achieve uniform preload gradually.
Calibrated Tools: Use only properly calibrated torque wrenches or, preferably, hydraulic bolt tensioners for the highest accuracy and safety, especially on large bolts.
Lubrication Matters: Torque specs assume bolts are lubricated as specified (often with molybdenum disulfide paste). Dry bolts or incorrect lubricant drastically alter the achieved clamping force.
Retorquing: Follow the manufacturer's recommendation for re-torquing bolts after an initial operational period (e.g., 50-100 hours of operation) as bolts can settle.
Truck Crane Slewing Bearing Applications: Where Mobile Rotation Powers Progress
The versatility of truck cranes, enabled by their slewing bearing, makes them indispensable across numerous sectors:
Construction: Lifting steel beams, precast concrete panels, HVAC units, machinery, and materials on building sites of all sizes.
Infrastructure: Erecting power lines, cell towers, bridges (girders, formwork), and road signs. Assisting in pipeline work.
Utilities: Installing and maintaining transformers, poles, and lines for power and telecom companies. Often using specialized "digger derrick" cranes.
Oil & Gas: Supporting maintenance, equipment handling, and pipeline activities in refineries and on remote sites.
Transport & Logistics: Loading/unloading heavy machinery, containers (smaller ports/yards), and oversized cargo onto trucks, railcars, or ships.
Manufacturing: Handling heavy components within factories and fabrication shops.
Emergency Services & Recovery: Critical for vehicle recovery (accidents, rollovers), disaster relief (debris removal), and rescue operations.
Landscaping & Tree Care: Placing large boulders, trees, and heavy landscape features.
Truck Crane Slewing Bearing Characteristics: Engineered for Demanding Mobility
These bearings possess distinct features tailored to their challenging mobile environment:
High Strength-to-Weight Ratio: Optimized design and materials (e.g., 50Mn, 42CrMo alloy steel) deliver maximum load capacity within strict weight constraints.
Robust Sealing: Multi-lip seals or labyrinth seals combined with high-quality grease are essential to keep out abrasive dirt, dust, water, and road salt, preventing internal wear and corrosion.
Precision Gear Teeth: Accurately machined internal or external gear teeth ensure smooth, reliable engagement with the slewing drive pinion under load.
Hardened Raceways: Raceways undergo surface hardening (induction hardening or carburizing) for exceptional resistance to wear, rolling contact fatigue, and brinelling (dent marks from shock loads).
Pre-Greased & Sealed: Typically supplied pre-filled with long-life, high-performance grease suitable for the operating temperature range.
Mounting Flexibility: Designed with bolt hole patterns and often centering features (spigots) to ensure accurate and secure mounting to both upper and lower structures.
Reliability Focus: Built for long service life with minimal maintenance, though regular lubrication is critical. Designed to withstand shock loads from rough terrain travel and dynamic lifting operations.
Decoding the Price Tag: Factors Influencing Truck Crane Slewing Bearing Cost
The cost of a truck crane slewing bearing isn't arbitrary; it's driven by several key factors:
Size & Load Capacity: Larger diameter bearings handling higher loads require significantly more material and complex manufacturing, increasing cost substantially.
Bearing Type & Complexity: A standard single-row four-point contact ball bearing is generally more economical than a larger double-row ball bearing or a custom-designed roller bearing needed for higher capacity cranes. Integrated gear teeth add cost.
Material Grade & Quality: High-strength, high-purity alloy steels (like 42CrMo4) cost more than standard grades. Consistency and traceability add value.
Manufacturing Precision: Achieving micron-level tolerances on large diameters requires advanced CNC machining and grinding equipment, along with skilled labor. Heat treatment processes (hardening) are energy-intensive and critical for performance.
Brand & Origin: Genuine OEM (Original Equipment Manufacturer) bearings typically command a premium due to brand reputation, exact design matching, and warranty support. Premium aftermarket brands also cost more than generic options. Geographic manufacturing location impacts labor and material costs.
Gear Specifications: The type (internal/external), size, module (tooth size), and precision class of the gear teeth significantly influence machining time and cost.
Sealing System: High-performance seals designed for harsh environments add cost compared to basic seals.
Certifications & Testing: Bearings requiring specific certifications (e.g., ISO 9001, DNV for marine variants) or undergoing rigorous load testing will be more expensive.
Customization: Bearings designed for specific crane models or unique requirements cost more than standardized designs.
Supply & Demand: Market conditions, raw material price fluctuations, and lead times can impact pricing.
The Essential Pivot Point: Keeping the World Lifting and Turning
The truck crane slewing bearing is far more than a simple component; it is the fundamental mechanical heart enabling the crane's most vital function: rotation. Its silent, robust performance under immense pressure allows operators to lift, swing, and place loads with precision and safety, driving progress on countless job sites worldwide. Understanding its critical role, the intricacies of replacement (especially the non-negotiable importance of torque specs), the common types used, its widespread applications, defining characteristics, and the factors shaping its cost, empowers crane owners, fleet managers, and service technicians. Investing in quality, ensuring proper installation and maintenance, particularly diligent lubrication and bolt torque checks, is paramount to maximizing uptime, safety, and the long-term value of these indispensable mobile lifting giants. When a crane smoothly swings a load against the horizon, remember the immense, silent force transmitted through its slewing bearing – the true pivot point of mobile lifting power.
Supplier of Truck Crane Slewing Bearing
LYRADRIVE is a professional slewing bearings ,slew drive and gears manufacturer provides customized slew bearing, drive and gears.For application-specific engineering solutions, contact LYRA to discuss technical specifications and implementation strategies.