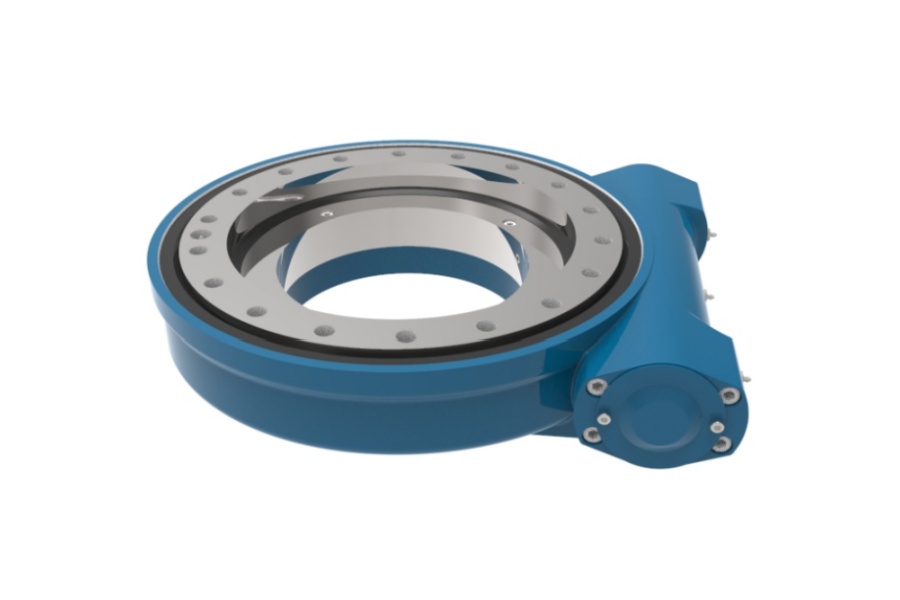
WE12 Worm Gear Drives Power and Precision for Demanding Applications
What is Worm Gear Drive WE12
Worm gear drive WE12 is a specific configuration within a series of standardized worm gear reducers. It features a cylindrical worm (the input screw) meshing with a worm wheel (the output gear), typically with a 90-degree shaft orientation. The "WE12" designation generally refers to a specific center distance (the distance between the worm and worm wheel shafts, often around 120mm in many standard series, though exact dimensions can vary slightly by manufacturer) and a defined frame size, indicating its physical dimensions, torque capacity range, and mounting characteristics. The core principle involves the worm's threads engaging the teeth of the worm wheel. As the worm rotates, it drives the worm wheel, resulting in a substantial reduction ratio determined by the number of threads (starts) on the worm and the number of teeth on the worm wheel. This design inherently provides a high reduction ratio in a single stage, self-locking capability (preventing back-driving under certain conditions, dependent on the lead angle and friction), and smooth, quiet operation when properly manufactured and lubricated.
WE12 Vibration Solutions
While known for smooth operation, excessive vibration in a WE12 worm gear drive can indicate underlying issues requiring attention. Key solutions focus on precision and maintenance:
Precise Alignment and Mounting: Ensuring the input motor shaft is perfectly aligned with the worm shaft and the entire reducer is rigidly and correctly mounted to its baseplate is paramount. Misalignment, even minor, is a primary cause of vibration and premature wear. Laser alignment tools are recommended for accuracy.
Minimizing Backlash: Excessive backlash between the worm and worm wheel teeth can lead to impact loads and vibration, especially during start-stop or reversing operations. Selecting a WE12 drive manufactured with tight initial backlash tolerances and ensuring proper meshing adjustment during installation is crucial. Backlash can increase over time due to wear, necessitating monitoring.
Optimal Lubrication: Using the correct type, viscosity, and quantity of high-quality lubricant specified by the manufacturer is essential. Insufficient lubrication causes increased friction, heat, and wear, leading to vibration. Contaminated or degraded lubricant loses its protective properties. Regular oil analysis and scheduled changes prevent lubrication-related issues.
Balancing Rotating Components: Imbalances in the input motor rotor, coupling, or the worm shaft itself can transmit significant vibration. Ensuring all rotating elements are dynamically balanced to appropriate standards minimizes this source.
Checking for Wear and Damage: Inspect the worm and wheel teeth for signs of pitting, scoring, excessive wear, or plastic deformation. Worn gears will inevitably run less smoothly and cause vibration. Bearing wear or failure is another common source; check bearings for smooth operation and noise.
Securing Couplings and Connections: Loose set screws, keyways, coupling bolts, or mounting bolts can create significant vibration. Ensure all fasteners are tightened to the correct torque specifications using a calibrated torque wrench.
Adequate Foundation Rigidity: Mounting the WE12 drive on a sufficiently rigid baseplate or structure prevents the structure itself from amplifying vibrations. Flexible mounts are generally not suitable for gear reducers unless specifically designed for vibration isolation, which is rare for worm gears due to torque reaction forces.
WE12 Load Capacity
The load capacity of a WE12 worm gear drive is its most critical performance parameter, defining the maximum torque and axial/radial forces it can reliably transmit without exceeding design limits for wear, tooth breakage, or bearing life. Key factors influencing WE12 load capacity include:
Material Selection: The worm wheel is typically made from bronze alloys (e.g., phosphor bronze, aluminum bronze) chosen for their excellent wear resistance against the hardened steel worm. The specific alloy composition significantly impacts surface durability and load-bearing capability. The worm is usually case-hardened steel (e.g., 16MnCr5, 20MnCr5) ground to high precision for smooth engagement and reduced friction.
Heat Treatment and Surface Hardness: The worm undergoes heat treatment (carburizing, hardening, tempering) to achieve high surface hardness (typically 58-62 HRC) for wear resistance while maintaining a tough core. The worm wheel bronze may also undergo heat treatments to optimize its microstructure.
Precision Manufacturing: Accurate tooth profile generation (often involute or convolute), precise lead and profile grinding of the worm, optimal surface finish, and controlled backlash are essential for distributing loads evenly across the tooth faces, minimizing stress concentrations, and maximizing capacity.
Lubrication and Cooling: Efficient lubrication reduces friction and wear, directly impacting load capacity. Adequate cooling (natural convection, fans, or forced oil cooling for high-power units) prevents overheating, which can degrade lubricant and soften metal surfaces, drastically reducing capacity.
Bearing Selection and Arrangement: The bearings supporting the worm and worm wheel shafts must be sized to handle the significant radial and thrust (axial) loads generated by the gear mesh. High-quality bearings with appropriate dynamic load ratings are essential.
Thermal Rating: Often the limiting factor for continuous operation. The drive's ability to dissipate heat generated by friction determines its permissible continuous input power without exceeding safe operating temperatures for the lubricant and components. Load capacity decreases as ambient temperature increases or cooling efficiency decreases.
Service Factor (Application Factor): Manufacturers provide nominal torque/power ratings based on ideal conditions. Selecting a WE12 drive requires applying a service factor (greater than 1.0) to the calculated required torque to account for real-world variables like shock loads, intermittent operation, duty cycle, and environmental conditions. This derated value must be less than the drive's nominal capacity.
Worm Gear Drive WE12 Features
WE12 worm gear drives offer a distinct combination of features making them suitable for numerous industrial applications:
High Reduction Ratios: Achieve significant speed reduction (ratios commonly from 5:1 up to 100:1 or higher in a single stage) in a compact space, simplifying drivetrain design.
Compact Design: The intersecting 90-degree shaft configuration allows for efficient use of space compared to some other gear types needing multiple stages for similar ratios.
Self-Locking Capability: Due to the high friction inherent in the sliding contact between worm and wheel, many WE12 drives exhibit self-locking behavior (where the worm wheel cannot back-drive the worm). This is highly valuable for holding loads without needing a separate brake, though it depends on the specific lead angle, friction coefficient, and efficiency, and should not be solely relied upon for safety-critical applications.
Smooth and Quiet Operation: When well-made and lubricated, the sliding action produces less noise and vibration compared to some other gear types like spur gears, especially at higher reduction ratios.
High Shock Load Tolerance: The robust design and the inherent damping effect of the sliding contact make WE12 drives relatively tolerant of shock and impact loads.
Right-Angle Power Transmission: The 90-degree shaft orientation efficiently changes the direction of power flow, simplifying machine layout.
Good Durability: With proper material selection, heat treatment, and lubrication, WE12 drives offer long service life in demanding environments.
Modularity: Many manufacturers offer WE12 drives as part of a modular system, allowing easy combination with other gear stages, motors (as gearmotors), or different mounting options.
Worm Gear Drive WE12 Applications
The unique features of WE12 worm gear drives make them indispensable across a vast spectrum of industries:
Material Handling: Conveyor systems (belt, roller, chain), palletizers, stackers, reclaimers, bucket elevators, lifting tables, hoists, winches.
Construction Equipment: Concrete mixers, cranes (slewing and hoisting mechanisms), excavator attachments, screed drives, vibratory compactors.
Food and Beverage Processing: Mixers, agitators, conveyors (belt, screw, flighted), packaging machines, filling lines, bottling lines.
Agriculture: Grain augers, feed mixers, irrigation systems (pivot drives), manure spreaders, harvesting equipment.
Mining and Minerals: Crushers, screens, feeders, slurry pumps, stackers, reclaimers, winches.
Packaging Machinery: Cartoners, case packers, shrink wrappers, labeling machines, filling machines.
Industrial Machinery: Mixers and agitators for chemicals/paints/plastics, rotary kilns, rolling mill drives, paper mill equipment, textile machinery, printing presses.
Automation and Robotics: Positioning stages, rotary actuators, automated guided vehicles (AGVs), palletizing robots (auxiliary axes).
Energy: Valve actuators (especially for large valves), damper controls, biomass handling equipment.
Water and Wastewater Treatment: Aerators, clarifier drives, screen cleaners, sludge collectors, pump drives.
Worm Gear Drive WE12 Price Influencing Factors
The price of a WE12 worm gear drive is not fixed and depends on several key variables:
Material Costs: Fluctuations in the prices of raw materials, particularly copper (for bronze worm wheels) and specific steel alloys, significantly impact manufacturing costs. Higher-grade, specialized alloys increase the price.
Manufacturing Complexity and Precision: Drives requiring tighter tolerances (e.g., very low backlash), special tooth profiles, super-finished surfaces, or complex heat treatment processes demand more sophisticated and time-consuming manufacturing, increasing cost. The precision grinding of the worm is a critical cost factor.
Size and Power Rating: While WE12 defines a frame size, variations within this size related to the specific torque/power capacity (often denoted by a size number or letter after WE12) affect material volume and component size, influencing price. Higher capacity units cost more.
Reduction Ratio: Drives with very high reduction ratios may require different manufacturing approaches or slightly larger components within the same frame, potentially impacting cost. Custom ratios outside standard offerings also increase cost.
Special Features: Options like special shaft configurations (hollow shafts, dual output shafts), specific flanges (PAM, IEC, NEMA), integrated brakes, forced cooling systems (fans, cooling coils), special seals (labyrinth, lip seals for harsh environments), custom paint, or specific surface treatments add to the base price.
Backlash Requirement: Drives manufactured and assembled to achieve "precision" or "very low" backlash levels require more meticulous production and inspection, increasing cost compared to standard backlash units.
Efficiency Class: Drives designed for higher efficiency (often involving optimized tooth profiles, premium lubricants, and lower-friction bearings) typically command a higher price due to the engineering and materials involved.
Quantity and Customization: Bulk orders often benefit from economies of scale, lowering the unit price. Conversely, highly customized drives designed for a specific application involve non-recurring engineering (NRE) costs and low-volume production, significantly increasing the unit price compared to standard catalog items.
Manufacturer and Brand Reputation: Established manufacturers with a reputation for high quality, reliability, extensive testing, and strong technical support often price their products higher than lesser-known brands. Certifications (ISO, etc.) also contribute.
Geographical Factors: Production location, labor costs, import/export duties, and local market dynamics can influence the final price to the customer.
Worm Gear Drive WE12 Supplier
LYRADRIVE is a prominent supplier of high-quality industrial power transmission solutions, including robust and reliable WE12 worm gear drives and gearmotors. They offer a comprehensive range of standard WE12 units known for precise manufacturing, durability, and efficient performance in demanding applications. LYRADRIVE also provides strong technical support and customization capabilities to meet specific customer requirements.