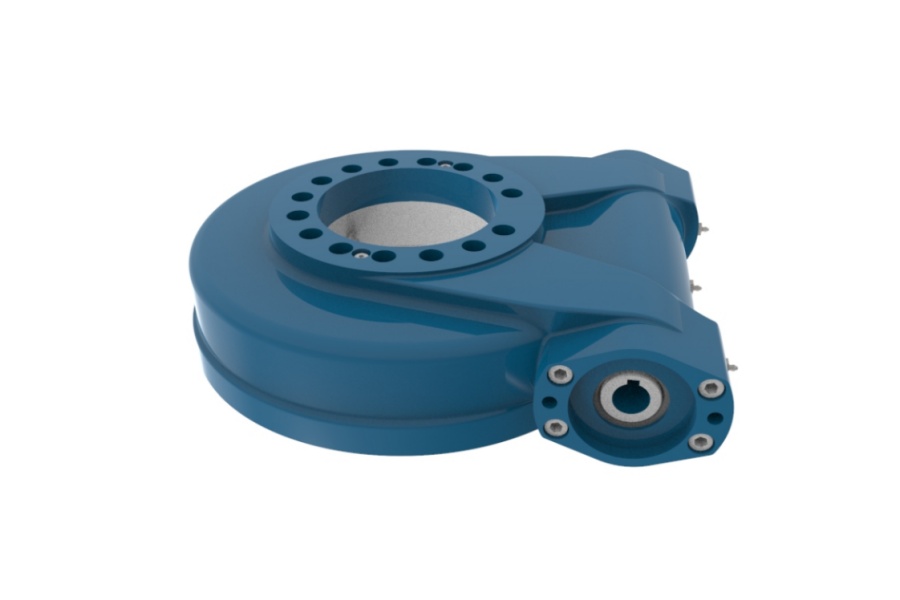
Unlocking Unstoppable Torque: Mastering Motion with WE9 Worm Gear Drives
What is a Worm Gear Drive WE9 Series?
A worm gear drive WE9, represents a specialized type of mechanical power transmission system. It consists of two primary components: a worm and a worm wheel (or gear). The worm resembles a threaded screw, while the worm wheel is a gear with teeth specially designed to mesh with the threads of the worm. The WE9 designation signifies adherence to specific dimensional standards, primarily DIN 3975, DIN 3976, and DIN 3974, ensuring interchangeability and predictable performance characteristics. WE9 drives are characterized by their compact housing design, standardized center distances, and optimized gear geometry for efficient power transfer. They are typically offered in a range of sizes, standardized by the center distance between the worm and worm wheel shafts (e.g., WE40, WE50, WE63, WE75, WE90, WE110), allowing engineers to select the appropriate size based on torque and speed requirements. This standardization simplifies design, procurement, and maintenance.
The Core Principle: How Worm Gear Drives Work
The operating principle of a worm gear drive is elegantly simple yet highly effective, revolving around the unique meshing action between the worm and the worm wheel. The worm, mounted on the input (drive) shaft, features helical threads. As the worm rotates, its threads push against the specially profiled teeth of the worm wheel, which is mounted on the output (driven) shaft. Crucially, the axes of these two shafts are non-intersecting and usually perpendicular (90° angle). The key to the system's high reduction ratio lies in the relationship between the number of threads (starts) on the worm and the number of teeth on the worm wheel. If the worm has a single thread (single-start), one full rotation of the worm advances the worm wheel by exactly one tooth. Therefore, the reduction ratio (i) is calculated as: i = Number of Teeth on Worm Wheel / Number of Starts on Worm. A significant feature arising from this sliding contact is the potential for self-locking. When the lead angle of the worm is sufficiently small, friction prevents the worm wheel from back-driving the worm. This inherent braking capability is invaluable for safety in applications like lifts, hoists, and conveyors where preventing reverse motion is critical. However, this sliding action also generates more heat and results in lower mechanical efficiency compared to spur or helical gears.
WE9 Powerhouse: Understanding Load Capacity
The WE9 series is engineered for substantial power transmission, but its actual load capacity is a nuanced interplay of several critical factors:
Torque Transmission: The primary measure of a WE9 drive's strength is its rated output torque (in Nm or lb-ft) at a specified input speed. This rating dictates the maximum load the drive can reliably handle under defined operating conditions without premature failure.
Axial & Radial Forces: The worm transmits significant axial thrust forces along its shaft due to the meshing action. Simultaneously, the worm wheel experiences substantial radial forces. WE9 housings and bearing arrangements are specifically designed to absorb these forces effectively. Ignoring these forces in system design leads to bearing overload and rapid failure.
Thermal Capacity: The sliding friction inherent in worm gear operation generates considerable heat. The thermal rating is the maximum continuous power the drive can transmit without exceeding safe operating temperatures, determined by factors like lubrication type/quantity, housing material/fins, ambient temperature, and cooling methods. Exceeding thermal limits causes lubricant breakdown and accelerated gear wear.
Dynamic Load & Shock Resistance: WE9 drives are robust but have limits regarding shock loads and severe vibrations. While they handle moderate impacts well, extreme dynamic loads can cause tooth breakage or bearing damage. Proper sizing includes a service factor to account for load variations.
Material & Hardness: High-strength materials are essential. Worms are typically hardened steel (e.g., case-hardened 16MnCr5 or 20MnCr5), while worm wheels often use wear-resistant bronze alloys (e.g., CuSn12Ni, GZ-CuSn12Ni) to withstand the sliding contact. Precise hardening processes ensure surface durability.
Lubrication: Correct lubricant selection (viscosity, EP additives) and adequate quantity are paramount for minimizing friction, wear, and heat generation, directly impacting achievable load capacity and lifespan.
Hallmarks of Performance: Key WE9 Worm Gear Drive Characteristics
The WE9 series distinguishes itself through a combination of inherent worm gear advantages and design optimizations:
High Reduction Ratios: Achieves significant speed reduction (ratios commonly from 5:1 up to 100:1 or more in a single stage) in an extremely compact package compared to other gear types.
High Torque Density: Delivers exceptional output torque relative to its physical size and weight, maximizing power transmission in space-constrained applications.
Smooth & Quiet Operation: The gradual, multi-tooth engagement results in very low noise and vibration levels, crucial for environments requiring quiet machinery or precise motion control.
Self-Locking Capability: The inherent friction at low lead angles provides a reliable, maintenance-free braking action, preventing back-driving and enhancing safety (critical note: not all ratios are self-locking; consult manufacturer data).
Right-Angle Configuration: The standard 90° shaft orientation offers significant design flexibility, simplifying machine layout and integration.
Compact Design: The integrated housing and efficient use of space make WE9 drives ideal where footprint is a premium.
Durability & Reliability: Built to DIN standards using high-quality materials and precision manufacturing, WE9 drives offer long service life under demanding conditions.
Standardization: Adherence to DIN standards ensures dimensional consistency, interchangeability of components from different reputable manufacturers, and simplified sourcing.
Driving Industry: Diverse Applications of WE9 Worm Gear Drives
The unique blend of high torque, compact size, right-angle power transmission, and smooth operation makes WE9 drives ubiquitous across numerous sectors:
Material Handling: Conveyor systems (driving rollers, belts), palletizers, stacker cranes, lifts, hoists, winches, dock levelers (leveraging self-locking for safety).
Industrial Automation: Rotary index tables, positioning stages, robotic arms, assembly line equipment, packaging machinery, filling machines.
Construction Equipment: Concrete mixers, screed drives, vibrators, small crane mechanisms, gate operators.
Food & Beverage Processing: Mixers, agitators, conveyors for ovens/coolers, bottling/canning lines, auger drives.
Agricultural Machinery: Grain augers, feed mixers, spreaders, small harvester mechanisms, irrigation systems.
Medical & Laboratory Equipment: Adjustable beds, patient lifts, precise positioning devices in imaging systems (benefiting from smooth motion).
Theater & Stage Technology: Rigging systems, stage lifts, curtain controls (requiring quiet operation and reliability).
HVAC & Building Management: Large valve actuators, damper controls, cooling tower fan drives.
Mining & Minerals: Screw conveyors, small feeder drives, classifier mechanisms.
General Industrial Machinery: Mixers, agitators, rotary kilns (smaller units), test stands, anywhere high torque at low speed is needed compactly.
Investment Factors: What Influences WE9 Worm Gear Drive Pricing?
The cost of a WE9 worm gear drive is not a single figure; it's determined by a complex combination of specifications and market factors:
Size & Center Distance: Larger drives (e.g., WE90, WE110) inherently require more material and complex manufacturing, commanding a higher price than smaller units (e.g., WE40, WE50).
Gear Ratio: Higher reduction ratios often require a larger worm wheel (more teeth), increasing material cost and machining time. Complex multi-start worms can also add cost.
Materials & Heat Treatment: Premium bronze alloys (e.g., nickel bronze) for the worm wheel and high-grade, precisely case-hardened steel for the worm significantly increase cost over standard materials but are essential for high load/long life. Special coatings can add cost.
Precision & Quality Grade: Drives manufactured to tighter tolerances (e.g., DIN Class 6 or better) for lower noise, higher efficiency, and better positional accuracy involve more meticulous machining and inspection, increasing price.
Housing Construction & Features: Cast iron housings offer superior rigidity and damping but cost more than aluminum. Integrated cooling fins, special seals (lip seals vs. labyrinth), specific flange types (B5, B14), and output shaft configurations (solid, hollow, keyed, splined) impact cost.
Efficiency Level: Achieving higher mechanical efficiency (e.g., through optimized tooth profile grinding, superior surface finishes, premium lubricants) requires advanced manufacturing processes, increasing price.
Lubrication System: Pre-lubricated units are standard, but options for grease nipples, oil level indicators, or integrated oil circulation systems add cost.
Brand Reputation & Engineering Support: Established manufacturers with proven reliability records, extensive testing, and strong technical support typically command a premium over generic suppliers.
Order Volume & Customization: Larger orders often benefit from economies of scale. Any deviation from standard catalog specifications (custom shaft lengths/sizes, special paints, unique mounting flanges) incurs additional engineering and setup costs.
Supply Chain & Market Dynamics: Raw material costs (copper, steel), energy prices, labor costs, and global supply chain fluctuations directly impact the final price. Lead times can also influence cost, especially for rush orders.
Supplier of WE9 worm gear drive
When performance, reliability, and technical expertise are non-negotiable for your WE9 worm gear drive requirements, LYRADRIVE stands as your premier partner. We are not just suppliers; we are solution providers deeply versed in the intricacies of power transmission engineering. LYRADRIVE offers a comprehensive range of high-quality WE9 worm gear drives manufactured to exacting DIN standards. Our commitment extends beyond the product:
Precision Engineering: Utilizing advanced manufacturing techniques and rigorous quality control, LYRADRIVE ensures every WE9 unit delivers optimal performance, durability, and efficiency straight out of the box.
Extensive Inventory & Range: We stock a wide variety of standard WE9 sizes (WE40 to WE110) and ratios, ensuring rapid availability to meet your project timelines. Our range covers diverse torque and speed requirements.
Technical Expertise: Our experienced engineering team provides unparalleled technical support. We assist with optimal drive selection based on your specific load, speed, duty cycle, and environmental conditions, ensuring perfect integration into your application.
Customization Capabilities: While standard units meet most needs, LYRADRIVE possesses the engineering prowess to develop customized WE9 solutions – tailored shaft configurations, special flanges, unique lubrication systems, or material upgrades – to tackle your most challenging requirements.
Quality Assurance: Every LYRADRIVE WE9 drive undergoes stringent testing protocols, guaranteeing adherence to specifications for noise, vibration, efficiency, and load capacity. You receive a drive built for reliability.
Global Support & Logistics: Supported by a robust global network, LYRADRIVE ensures timely delivery and responsive local support wherever your operations are located.
Value Beyond Price: We focus on delivering Total Cost of Ownership (TCO) advantage through long service life, reduced maintenance needs, minimal downtime, and optimized energy efficiency.