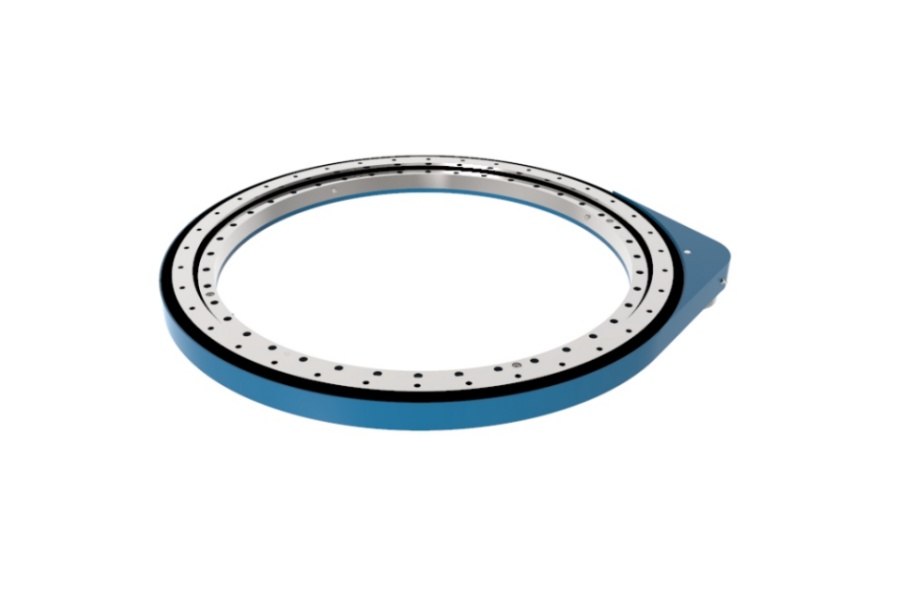
Uncompromising Rotational Force: The SP-M 0841 Medium Duty Slewing Drive Revolution
What Is the Medium Duty Gear Slewing Drive SP-M 0841?
The SP-M 0841 is a fully integrated rotational drive system merging a hardened gear mechanism with a heavy-duty slewing bearing in a single compact housing. Designed for medium-duty industrial applications, it efficiently converts motor input into smooth bidirectional rotation while simultaneously supporting massive axial, radial, and moment loads. Its "SP-M" series designation signifies optimized robustness for high-stress environments like mining, construction, and material handling where component failure would trigger catastrophic downtime. Unlike conventional bearings, this drive actively generates motion rather than merely supporting it.
How to Select the Perfect Medium Duty Slewing Drive
Choosing the right slewing drive demands rigorous analysis of five critical parameters. First, quantify dynamic loads: calculate peak axial forces, radial stresses, and tilting moments during operation. Second, determine torque requirements including start-up torque and safety margins. Third, evaluate environmental hazards like abrasive dust, water immersion, temperature extremes, or corrosive chemicals. Fourth, verify mechanical constraints: measure bolt circle diameters, housing height limits, and shaft interface specifications. Finally, define motion precision needs: industries like radar positioning demand near-zero backlash under 0.05°. Always exceed operational torque by 20% for longevity in variable-load scenarios.
SP-M Slewing Drive Specifications: Power Decoded
The SP-M 0841 series delivers industry-leading performance metrics. Axial load capacity ranges from 50 to 85 kilonewtons while radial load handling spans 25-40 kilonewtons. Torque transmission peaks between 8,500 and 12,000 newton-meters depending on configuration. Gear ratios extend from 10:1 for speed-intensive applications to 160:1 for high-torque precision tasks. Standard backlash remains under 0.05 degrees ensuring positional accuracy. Environmental protection meets IP65+ standards blocking dust and water jets. Operating temperatures span from -30°C in arctic conditions to +80°C in desert heat without performance degradation.
Slewing Ring Drive vs. Gear Slewing Drive: Critical Distinctions
"Slewing ring drive" is frequently misused interchangeably with gear slewing drives – a costly misunderstanding. Passive slewing rings solely provide rotational support without drive mechanics. They require external motors and gearboxes to generate motion. Conversely, gear slewing drives like the SP-M 0841 integrate gearing within the unit. This active design directly converts motor input into rotation while handling structural loads. The unified architecture eliminates alignment issues, reduces maintenance points, and cuts installation space by 40% compared to modular systems.
Six Dominant Features Defining the SP-M 0841
Crossed Roller Bearing Core: Distributes axial, radial, and moment loads evenly across hardened raceways for 20% longer fatigue life.
Surface-Hardened Gearing: Carburized alloy steel teeth rated at HRC 58-62 resist pitting and wear under shock loads exceeding 150% of nominal capacity.
Triple Defense Sealing: Multi-lip seals combined with grease purge ports create impenetrable barriers against silica dust and high-pressure water in mining or marine applications.
Thermal Regulation Architecture: Ribbed aluminum housing dissipates heat 30% faster than cast iron during continuous rotation cycles.
Precision Backlash Control: Adjustable pre-load mechanisms enable ultra-tight meshing for applications demanding under 0.01° positioning repeatability.
Fail-Safe Braking: Spring-applied electromagnetic brakes instantly lock positions during power failures – critical for aerial platforms and lifting gear.
Industrial Applications: Where SP-M 0841 Excels
Crane Systems: Powers boom rotation in 15-25 ton knuckle boom cranes with uncompromising safety margins.
Solar Energy: Drives precision tracking in utility-scale photovoltaic farms and concentrated solar heliostats.
Automated Manufacturing: Enables 24/7 operation of robotic welding turntables and palletizing arms.
Heavy Machinery: Rotates excavator attachments and directional drilling heads in mining operations.
Wind Energy: Controls yaw orientation in mid-size turbines up to 2.5MW capacity.
Defense Systems: Delivers missile launcher turret rotation and radar scanning with military-grade reliability.
Price Determinants: Understanding SP-M 0841 Cost Factors
Investment in an SP-M 0841 reflects sophisticated engineering with these key cost drivers: Material selection causes 15-25% price variance – aircraft-grade aluminum alloys cost more than standard steel housings. Gear manufacturing precision adds over 20% for ground teeth versus hobbed alternatives but minimizes backlash. Load ratings significantly impact cost; units rated for 12,000 Nm torque carry 30% premiums over 8,500 Nm versions. Environmental sealing escalates prices 10-15% when upgrading from IP54 to IP66/67 protection. Customizations like non-standard bolt patterns or shaft interfaces incur engineering fees. Volume discounts of 18-22% apply for orders exceeding ten units.
Supplier of SP-M 0841
LYRADRIVE engineers slewing drives that redefine reliability standards. Every SP-M 0841 unit undergoes brutal validation: vibration spectrum analysis simulates decade-long wear in weeks; accelerated life testing runs 5,000+ hours under 130% overload conditions; torque calibration ensures sub-3% output deviation. Full material traceability includes EN 10204 3.1 certifications with laser-etched serial numbers. Beyond supply, LYRADRIVE delivers application engineering support: free load validation, 3D integration models, and dynamic FEA simulations. Global logistics hubs in Germany, Ohio, and Singapore enable 72-hour emergency deliveries. The 24-month warranty – double the industry standard – proves our commitment to eliminating your downtime.