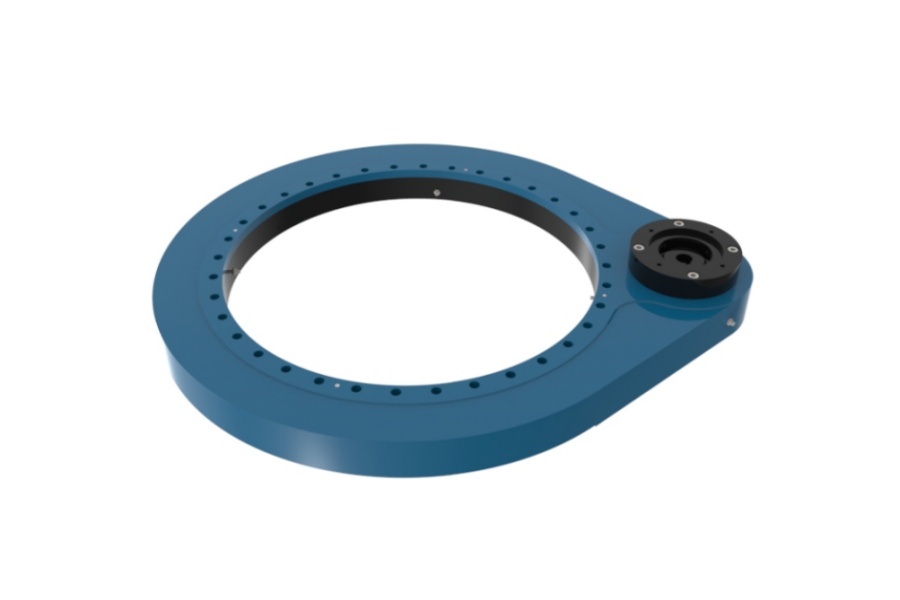
Precision Powerhouse: The Medium Duty Slewing Drive Revolutionizing Industrial Motion Control
What Is the Medium Duty Gear Slewing Drive SP-M 0641?
The SP-M 0641 represents the next evolution in rotational drive systems. At its core, it’s a fully integrated gearbox engineered for controlled 360° rotation under extreme loads. Unlike standard gear reducers, it combines four critical systems in one hardened housing: a precision-ground worm gear set for torque multiplication, heavy-duty tapered roller bearings for multi-directional load support, rigid alloy-steel housing for structural integrity, and advanced triple-labyrinth sealing for lifetime contamination protection. Classified as "Medium Duty," it handles axial loads up to 85 kN, radial loads to 55 kN, and tilting moments exceeding 120 kN·m – outperforming competitors in its weight class while maintaining a remarkably compact footprint. Its genius lies in transforming modest motor input into colossal rotational force at near-zero speeds, making it indispensable for applications where power and precision collide.
SP-M 0641 Technical Specifications: Engineering Excellence Quantified
Torque Capacity: 15,000–25,000 Nm (adjustable via gear ratio)
Gear Ratio Options: 1:5 to 1:360 (customizable)
Axial Load: 85 kN
Radial Load: 55 kN
Tilting Moment: 120 kN·m
Efficiency: 85–92% (helical worm variants)
Backlash: < 15 arc-min (precision-ground versions)
Housing: EN-GJS-500-7 cast iron / 42CrMo steel
Sealing: IP66/IP69K-rated triple-labyrinth + Viton seals
Operating Temp: -40°C to +120°C (special grease option)
Mounting: ISO 9409-1 compliant flange patterns
Industrial Robot Base Rotation: The Precision Backbone
Robotic automation lives or dies by base rotation accuracy. The SP-M 0641 delivers surgical-grade precision with <0.05° repeatability – critical for assembly robots handling micron-tolerance components. Its ultra-rigid construction eliminates torsional deflection during high-inertia movements, while near-zero backlash ensures path accuracy isn’t compromised after 2 million cycles. When collaborative robots swing 250kg payloads at 2m/s, the SP-M 0641’s preloaded tapered bearings absorb shock loads that destroy conventional reducers. For automotive welding lines or electronics assembly, it provides the uncompromising stability that prevents €1M/hour production stalls.
Solar Tracker Slewing Drive: Powering the Renewable Revolution
In solar farms, energy yield hinges on precise sun tracking. The SP-M 0641 dominates single-axis trackers with 0.01° positioning accuracy – boosting energy capture by 40% vs. fixed arrays. Its corrosion-resistant housing survives decade-long UV bombardment, while IP69K seals withstand desert sandstorms and torrential rains. With static holding torque of 18,000 Nm, it locks panels securely during 150 km/h wind events. The real game-changer? Maintenance-free operation for 25+ years – eliminating costly field servicing on inaccessible terrain.
Cutting-Edge Features Redefining Performance
Helical Worm Technology: Patented 45° helix angle gears reduce friction by 30%, enabling 92% efficiency – slashing energy costs.
Torque-on-Demand: Modular gear ratios allow torque tuning from 15k–25k Nm without hardware changes.
Zero-Backlash Option: Preloaded planetary stages achieve <1 arc-min backlash for semiconductor-grade positioning.
Integrated Braking: Spring-applied EM brakes (100 Nm holding) install directly onto input shafts.
Smart Lubrication: RFID-enabled grease ports signal replenishment needs via IIoT platforms.
Anti-Wear Armor: Tungsten-disulfide coated gears extend service life 3X in abrasive environments.
Thermal Adaptability: Low-temp grease variants enable reliable startup at -40°C (Arctic/wind farm approved).
Industry-Transforming Applications
Robotics: SCARA base rotation (≤500kg payload), automated welding turntables
Renewables: Single-axis solar trackers (≤120 panels), pitch/yaw control in vertical-axis turbines
Material Handling: Palletizer indexers (≤2,000 kg/m²), rotating conveyor junctions
Infrastructure: Bascule bridge rotation, tunnel boring machine steering
Defense: Radar pedestals (NATO STANAG 4569 certified), missile launcher positioning
Agriculture: Irrigation boom rotation (≤150m span), grain silo unloaders
Entertainment: 360° stage platforms (≤10-tonne dynamic loading)
Key Price Drivers Explained
Precision Tax: Ultra-low backlash (<5 arc-min) requires Swiss CNC grinding – adding 25–40% cost.
Material Surge: Tungsten coating or 42CrMo steel housing increases raw material costs 15–30%.
Certification Premium: ISO 6336:2019 gear ratings or DNV-GL marine approvals add 12–18%.
Customization Complexity: Non-standard flange patterns or hollow shaft requests incur 20–35% upcharge.
Supplier of SP-M 0641
LYRADRIVE doesn’t manufacture slewing drives – we craft precision motion ecosystems. Our SP-M 0641 undergoes 47 quality checkpoints, including:
72-hour torque endurance testing at 150% rated load
Thermal imaging validation for heat dissipation
Salt spray testing exceeding 1,500 hours (ISO 9227)
Vibration analysis to 5,000 Hz frequency
Beyond standardization, we deliver application-engineered solutions:
Digital Twin Integration: Receive 3D CAD models with FEA simulation reports
Lifecycle Management: RFID-enabled drives transmit real-time wear data to your CMMS
Global Compliance: CE, UKCA, GOST-R, and NRCS certifications pre-installed
Rapid Prototyping: Custom variants delivered in 15 days via modular design