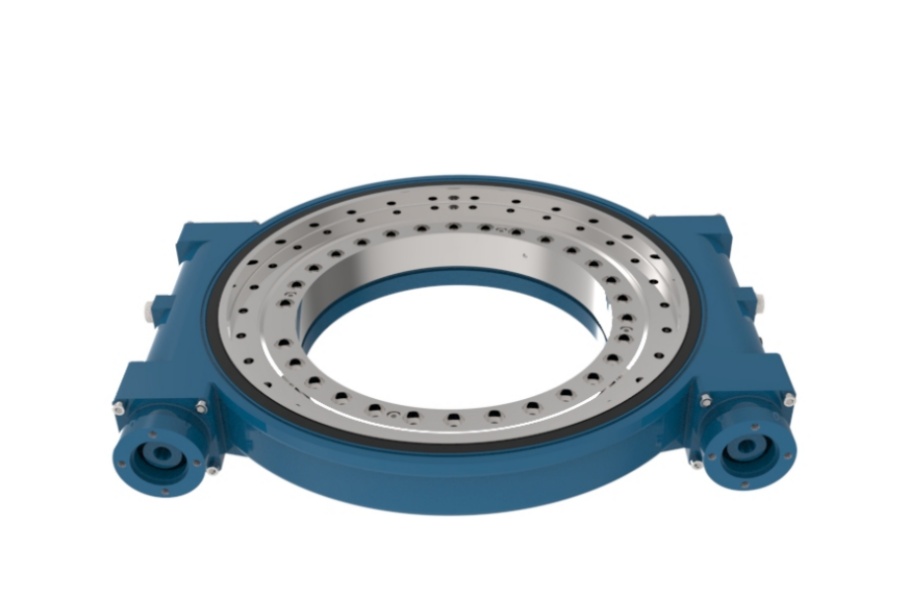
The Untapped Powerhouse: Mastering Heavy-Duty Rotation with Double Worm Slewing Drive Technology
What is the Double Worm Slewing Drive WED21?
The Double Worm Slewing Drive WED21 represents a pinnacle of rotational power transmission design. Unlike single-worm drives or simple gear sets, it incorporates two precisely meshed worm gears driving a single large output gear (slewing ring bearing). This unique configuration fundamentally transforms performance. Each worm is independently driven, typically by high-performance electric motors. The genius lies in the force distribution: the dual worms apply opposing forces to the central gear, effectively canceling out massive axial loads inherent in heavy rotation. This allows the slewing ring bearing to focus purely on handling radial loads and driving the torque, resulting in dramatically increased load capacity, enhanced rigidity, and significantly reduced deformation under extreme stress. It's engineered for situations where standard drives simply buckle.
Engineering Machinery Slewing Drive: The Critical Link
Slewing drives are the indispensable joints enabling pivotal movement in countless engineering machines. They are the mechanical heart allowing excavators to swing their booms, cranes to rotate their superstructures, solar trackers to follow the sun, and heavy-duty turntables to position massive loads. Performance demands are immense: these drives must withstand shock loads, continuous high torque, environmental extremes (dust, moisture, temperature swings), and relentless operational cycles. Failure isn't an option; it leads to catastrophic downtime, costly repairs, and potential safety hazards. The Slewing drive dictates the machine's operational envelope – its lifting capacity, its precision, its durability, and ultimately, its productivity and return on investment. Selecting the right drive technology is paramount.
Conquering the Torque Frontier: The Imperative for High Torque Slewing Drives
Many heavy machinery applications demand torque levels that push conventional drives to their breaking point. Think of:
Mega Excavators: Swinging massive buckets filled with dense material requires immense starting and stopping torque.
Heavy-Lift Cranes: Rotating multi-hundred-ton loads, often with significant outreach, generates colossal forces on the drive.
Large Wind Turbine Yaw Systems: Precisely positioning nacelles weighing hundreds of tons against powerful wind loads demands exceptional holding torque.
Industrial Positioning Tables: Handling giant castings, presses, or reactors requires smooth, powerful rotation under extreme weight.
Offshore Equipment: Deck cranes, pipelayers, and gangways operating in harsh marine environments need drives robust enough to handle both load and corrosion. Standard single-worm drives or pinion-gear systems often struggle with deformation, excessive wear, backlash, and premature failure under these conditions. This is the domain where high-torque solutions like the Double Worm Slewing architecture become essential, not optional.
Maximizing Uptime: Essential Maintenance for High-Load Double Worm Slewing Drives (Like WED21)
The immense power of a Double Worm Slewing drive like the WED21 demands rigorous maintenance to achieve its full lifespan potential. Neglect leads to accelerated wear and costly failures. Follow these critical practices:
Precision Lubrication is Paramount: Use only the manufacturer-specified high-performance, extreme-pressure grease. Adhere strictly to the recommended intervals and quantities. Over-greasing can be as detrimental as under-greasing, causing seal damage and overheating. Ensure grease purges old lubricant and contaminants effectively. Consider automatic lubrication systems for critical applications.
Religiously Monitor Seal Integrity: Seals are the primary defense against contaminants (dust, grit, water). Inspect seals visually and during lubrication purging for cracks, tears, or signs of extrusion. Replace damaged seals immediately. Keep seal running surfaces clean.
Conduct Regular Torque and Backlash Checks: Monitor the drive's operational torque and rotational backlash periodically. Significant increases can indicate internal wear (worm/wheel, bearings) or misalignment. Track trends and investigate deviations promptly.
Ensure Mounting Surface Perfection: Any distortion, warping, or unevenness in the mounting surfaces translates directly into internal stress and premature bearing/shaft failure. Verify flatness and rigidity according to WED21 specifications during installation and after major load events.
Implement Vibration & Temperature Monitoring: Use sensors to track vibration levels and operating temperature. Abnormal spikes often signal developing problems like misalignment, lubrication failure, or bearing issues, allowing for proactive intervention.
Keep it Clean: Prevent buildup of debris around the drive housing and seals. Washdowns should be performed carefully, avoiding direct high-pressure streams on seals. Contamination is a primary wear accelerator.
Unlocking Superior Performance: Key Features of the WED21 Double Worm Slewing Drive
The WED21 isn't just a Double Worm Slewing drive; it incorporates specific engineering features for peak heavy-duty performance:
Exceptional Axial Load Cancellation: The core Double Worm Slewing design inherently neutralizes axial forces, freeing the slewing bearing to handle pure radial loads and drive torque, maximizing its capacity and lifespan.
Massive Torque Density: Delivers extraordinarily high output torque relative to its physical size and input power, enabling compact machine designs with formidable strength.
Ultra-High Rigidity & Low Deformation: Engineered housing and optimized gear meshing minimize flexing under load, ensuring precise positioning and control even with maximum payloads.
Near-Zero Backlash: Precision manufacturing and pre-loading techniques result in minimal lost motion, crucial for applications requiring accurate positioning and repeatability.
Integrated High-Capacity Slewing Bearing: The drive incorporates a robust, multi-row roller slewing bearing specifically matched to handle the radial loads and drive torque efficiently.
Robust Housing Design: Constructed from high-strength materials with optimized ribbing to withstand extreme operational stresses and environmental conditions.
Precision Ground Gearing: Worms and wheel gears are precision ground for optimal contact patterns, smooth operation, high efficiency, and extended service life.
Advanced Sealing Solutions: Multi-labyrinth seals and often special sealing compounds provide superior protection against dust, water, and other contaminants in harsh environments.
Optimized Lubrication Paths: Internal channels ensure lubricant reaches critical meshing points and bearing surfaces effectively.
Where Power Meets Precision: Diverse Applications for the WED21
The WED21's unique capabilities make it the drive of choice across numerous demanding industries:
Heavy Construction & Mining: Excavators (especially large mining shovels), crawler cranes, drilling rigs, tunnel boring machine positioning, large material handlers. Handles the shock loads and relentless cycles.
Material Handling: Heavy-duty turntables for positioning presses, reactors, or large components; container handling cranes, port cranes, ship-to-shore cranes. Provides smooth rotation under massive, often off-center, loads.
Forestry & Recycling: Harvester heads, forwarders, large shredders, shear balers. Withstands the harsh, abrasive environments and high inertial loads.
Renewable Energy: Yaw drives for large multi-megawatt wind turbines, solar tracker azimuth drives for utility-scale installations. Offers the holding torque needed against wind forces and precise solar tracking.
Specialized Industrial Machinery: Large robotic welding positioners, heavy-duty indexing tables, vessel turntables, radar pedestals, stage machinery. Delivers precision and power simultaneously.
Offshore & Marine: Deck cranes, pipelaying equipment, mooring turrets, gangways. Built to endure saltwater corrosion and demanding marine operations.
Investing Wisely: Factors Influencing WED21 Double Worm Slewing Drive Pricing
The cost of a WED21 Double Worm Slewing drive reflects its sophisticated engineering and robust construction. Key pricing factors include:
Torque & Load Capacity: The single biggest driver. Higher required torque ratings and load capacities necessitate larger gears, bearings, and more robust housings, significantly increasing material and manufacturing costs.
Slewing Bearing Specification: Size, type (ball vs. roller, number of rows), internal clearance, raceway hardness, and special treatments (induction hardening, coatings) greatly impact cost. Custom bearing designs add more.
Gear Quality & Manufacturing: Precision grinding of worms and the large wheel gear is complex and time-consuming. Higher precision grades (e.g., DIN 5 or better) and special tooth profiles increase cost. Material quality (case-hardened steels) is critical.
Housing Complexity & Material: Cast or fabricated housings? Complexity of internal ribbing, machining tolerances, and the grade of steel or cast iron used all contribute. Corrosion-resistant requirements add cost.
Sealing & Environmental Protection: IP ratings matter. Achieving high IP (e.g., IP65, IP67) or specific corrosion resistance (e.g., salt spray testing, special coatings like Hempadur) requires advanced sealing designs and materials.
Input Drive Options: The type, size, and quality of the required input motors, gearboxes (if used), and brakes integrated or specified alongside the drive unit affect the overall system price.
Customization: Standard sizes offer better value. Customizations like special mounting flanges, shaft extensions, unique lubrication ports, specific paint requirements, or non-standard backlash tolerances add engineering and production costs.
Certification & Documentation: Requirements for specific certifications (CE, DNV-GL, ABS, etc.) or extensive documentation packages add administrative and testing overhead.
Order Volume & Supply Chain: Economies of scale apply. Larger orders typically achieve better pricing. Current raw material costs (steel, alloys) and component availability also influence market price.
Engineering Excellence Realized: Partnering with LYRADRIVE
When sourcing a Double Worm Slewing Drive WED21, partnering with an experienced and capable manufacturer is crucial for performance, reliability, and long-term support. LYRADRIVE stands as a premier global supplier specializing in high-performance Slewing drive solutions, including the advanced WED21 series. What sets LYRADRIVE apart?
Deep Technical Expertise: Decades of focused engineering in Slewing drive technology, particularly in heavy-duty and high-torque applications.
Proven Manufacturing Capability: State-of-the-art facilities equipped for precision machining, grinding, heat treatment, and assembly of complex drive systems under strict quality control (ISO 9001 certified).
Rigorous Testing: Comprehensive in-house testing protocols validate torque capacity, efficiency, backlash, durability, and environmental sealing before units leave the factory.
Application Engineering Support: LYRADRIVE engineers collaborate closely with customers to understand specific needs, perform load calculations, and ensure the optimal WED21 configuration is selected and integrated.
Global Support & Service: Providing technical assistance, spare parts, maintenance guidance, and repair services worldwide to maximize uptime throughout the drive's lifecycle.
Commitment to Quality & Innovation: Continuous investment in R&D and process improvement ensures LYRADRIVE drives meet evolving market demands for higher performance, efficiency, and reliability.
Choosing LYRADRIVE means investing not just in a component, but in a partnership dedicated to the success of your most demanding rotational applications. The WED21 embodies their commitment to pushing the boundaries of what's possible in heavy-duty motion control