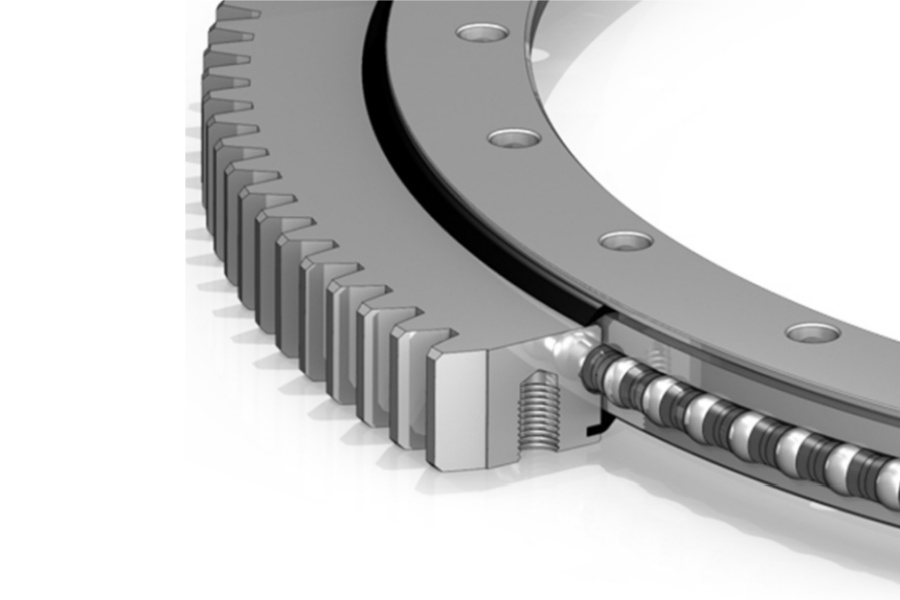
The Unshakeable Core: Mastering Motion with Flanged Four Contact Ball Slewing Bearings
What Exactly is a Flanged Four Contact Ball Slewing Bearing?
Imagine a critical component designed to manage immense forces while enabling smooth, controlled rotation between massive structures. That's the essence of a slewing bearing (or slewing ring). The flanged four contact ball slewing bearing represents a highly specialized and robust category within this family. Its defining features are twofold: an integrated mounting flange and a unique four-point contact ball raceway design. The flange, typically extending radially from either the inner or outer ring (or sometimes both), provides a secure, stable, and simplified bolting interface for attaching the bearing directly to structural components like an excavator's upper frame or boom. The "four contact" aspect refers to the geometry of the raceways machined into the inner and outer rings. These raceways are shaped such that each steel ball makes contact with the rings at four distinct points – two on each ring. This design is fundamentally different from single-row angular contact bearings and creates a highly efficient load path.
Delving Deeper into Flanged Four Contact Ball Slewing Bearing Design
The power of this bearing lies in its optimized geometry. The raceway grooves are precisely machined to specific angles relative to the bearing axis. When assembled under preload, this geometry forces each ball to make contact at four points simultaneously. This configuration provides significant advantages. It allows the single row of balls to simultaneously support substantial axial loads (parallel to the rotation axis), radial loads (perpendicular to the axis), and tilting moment loads (forces trying to tip one ring relative to the other). Effectively, it combines the load-carrying capabilities often requiring two separate rows of balls into a more compact single-row design. The integrated flange eliminates the need for separate, complex mounting housings, reducing overall system weight, simplifying assembly, and enhancing structural rigidity. Seals are crucial elements, integrated to protect the precision raceways and balls from harsh environmental contaminants like dirt, water, and debris, while retaining lubricant. Lubrication fittings ensure grease can be replenished to maintain smooth operation and bearing longevity.
The Indispensable Role of Slewing Bearings in Construction Equipment
Construction equipment operates under some of the most punishing conditions imaginable. Machines like excavators, mobile cranes, tower cranes, concrete pumpers, and drilling rigs rely on slewing bearings as their literal pivot points. These bearings are fundamental to the core functionality of the machine. They enable the crucial 360-degree rotation of the upper structure (superstructure) relative to the undercarriage. This rotation is what allows an excavator operator to dig, lift, swing, and precisely place loads. Without a robust, reliable slewing bearing, these machines would be static and useless. The bearing must handle not just the dead weight of the machine's upper components and attachments but also dynamic loads from digging forces, lifted loads, wind, and machine movement over uneven terrain. Failure is not an option; it leads to catastrophic downtime, costly repairs, and significant safety hazards.
Why the Flanged Four Contact Ball Design Reigns Supreme for Excavators
Excavators are the workhorses of construction, and their slewing bearings face a brutal combination of demands. The flanged four contact ball slewing bearing is frequently the optimal choice for modern excavators due to its exceptional blend of strength, efficiency, and compactness. Excavator operations generate massive axial loads (from the boom and bucket forces), significant radial loads (especially during side-loading or uneven digging), and substantial tilting moments (as loads are extended away from the center of rotation). The four-point contact design excels at handling this complex combination of loads within a single-row bearing. The integrated flange provides a direct, robust connection to the excavator's upper frame and swing gearbox, ensuring efficient force transfer and structural integrity. Its relatively compact height profile compared to double-row designs is advantageous within the space-constrained design of an excavator's rotating platform. The ability to handle high moment loads efficiently makes it ideal for the long booms and heavy buckets characteristic of modern excavators.
Key Characteristics Defining Flanged Four Contact Ball Slewing Bearings
The superiority of this bearing type stems from several inherent design characteristics. Exceptional Combined Load Capacity: Its core strength is the ability to simultaneously manage high axial, radial, and moment loads efficiently within a single row, outperforming standard ball slewing rings. High Stiffness and Rigidity: The four-point contact and precise preload result in minimal elastic deformation under load, ensuring precise positioning and control, critical for tasks like fine grading or precise lifting. Compact Design: Delivering high load capacity in a single row translates to a more compact bearing height, saving valuable space in machinery design. Integrated Mounting: The flange drastically simplifies installation and enhances connection stiffness compared to bearings requiring separate adapter rings or complex housings. Smooth Operation: Despite high load capacity, precision manufacturing ensures low friction torque and smooth, controlled rotation. Robustness: Designed with heavy-duty applications in mind, featuring large-diameter balls, hardened raceways, and effective sealing for longevity in harsh environments. Versatility: While excelling in excavators, the fundamental characteristics make it suitable for a wide range of other applications demanding high load capacity and compact design.
Diverse Applications Beyond the Construction Site
While construction equipment, particularly excavators, are prime beneficiaries, the capabilities of flanged four contact ball slewing bearings find utility across numerous demanding industries. Wind Turbines: Used in yaw drives to precisely orient the nacelle into the wind and sometimes in pitch control mechanisms for blade angle adjustment. Material Handling: Found in stacker-reclaimers, ship loaders/unloaders, and large robotic arms requiring robust rotation under heavy loads. Industrial Automation: Integral to heavy-duty turntables, welding positioners, and large robotic platforms needing precise motion control with high moment load capacity. Medical Imaging: Used in advanced CT and MRI scanners where smooth, precise, and vibration-free rotation is paramount. Defense and Aerospace: Employed in radar platforms, missile launchers, and satellite communication dishes requiring reliable rotation under challenging conditions. Mining Equipment: Essential for large drills, draglines, and mineral processing machinery operating in extremely abrasive environments. Port Equipment: Critical for the smooth operation of ship-to-shore cranes and mobile harbor cranes handling massive container loads.
Factors Influencing the Price of Flanged Four Contact Ball Slewing Bearings
The cost of these precision-engineered components is driven by several key factors. Size and Dimensions: Larger diameter bearings require significantly more raw material (forgings) and extensive machining time. Load Capacity Requirements: Bearings specified for higher static and dynamic load ratings necessitate larger cross-sections, larger balls, higher-grade materials, and more stringent manufacturing processes. Material Specifications: The grade and quality of steel used for rings and balls (e.g., vacuum-degassed, high-hardness alloys) significantly impact cost. Special coatings for corrosion resistance add expense. Precision and Tolerances: Tighter manufacturing tolerances for raceway geometry, parallelism, and runout demand more advanced machinery, rigorous quality control, and increase production time and cost. Heat Treatment: Sophisticated hardening and tempering processes (like induction or case hardening) are critical for durability and add considerable cost. Sealing System: The complexity, quality, and materials of seals (double-lip, labyrinth, specific elastomers) needed for the operating environment affect price. Gear Teeth: If integrated external or internal gear teeth are required (common in many applications), the precision machining and hardening of these gears add substantial cost. Customization: Bearings designed to non-standard dimensions or with special features (unusual bolt patterns, lubrication systems, sensor integration) incur higher engineering and production costs than standard catalog items. Certification Requirements: Meeting specific industry certifications (e.g., DNV-GL for marine, CE) involves additional testing and documentation costs. Order Quantity: Economies of scale apply; larger production runs generally reduce the unit cost.
Partnering with Precision: Your Source for Flanged Four Contact Ball Solutions
Selecting the right supplier for flanged four contact ball slewing bearings is as critical as the bearing design itself. This is where LYRADRIVE establishes itself as a leading force in the industry. We are not merely distributors; we are manufacturers deeply committed to engineering excellence and delivering solutions built to withstand the most demanding applications. LYRADRIVE's core strength lies in our vertically integrated manufacturing process. We control every critical stage: sourcing high-integrity steel forgings, precision machining raceways and flanges to exacting tolerances, applying advanced heat treatment for optimal hardness and toughness, meticulously assembling with high-grade balls and custom-engineered sealing systems, and conducting rigorous final inspection and performance testing. This comprehensive control ensures unparalleled consistency, traceability, and quality in every bearing that bears our name. Our engineering team possesses deep expertise in slewing bearing dynamics and application requirements. We collaborate closely with clients, offering not just standard products but also providing extensive customization capabilities. Whether you need non-standard dimensions, specific gear configurations (spur or helical, internal or external), specialized sealing solutions for extreme environments (dust, water, chemical exposure), unique mounting interfaces, or integrated sensor systems for condition monitoring, LYRADRIVE has the technical prowess to deliver.
Supplier of Flanged Four Contact Ball Slewing Bearing
Engineered for Extreme Performance: Our bearings are designed and manufactured to handle the highest axial, radial, and moment loads with exceptional rigidity and longevity.
Uncompromising Quality: Rigorous quality control protocols at every stage, from forging inspection to final testing, guarantee reliability and performance.
Deep Application Expertise: Decades of experience across construction, material handling, renewable energy, and industrial sectors ensure we understand your specific challenges.
Advanced Manufacturing: State-of-the-art CNC machining, controlled heat treatment processes, and precision assembly ensure consistent high performance.
Customization Powerhouse: We excel at tailoring solutions to meet unique application demands, offering true engineering partnership.
Robust Sealing Solutions: Expertise in designing seals that effectively protect against the harshest contaminants, extending bearing life significantly.
Global Support: Dedicated technical support and service teams ready to assist with selection, installation guidance, and maintenance recommendations worldwide.
Proven Reliability: LYRADRIVE bearings are trusted components in critical machinery operating 24/7 across the globe, minimizing downtime and maximizing productivity.
Invest in Unshakeable Performance. Partner with LYRADRIVE for your Flanged Four Contact Ball Slewing Bearing requirements and experience the difference that precision engineering and manufacturing excellence make at the very core of your machinery's motion.