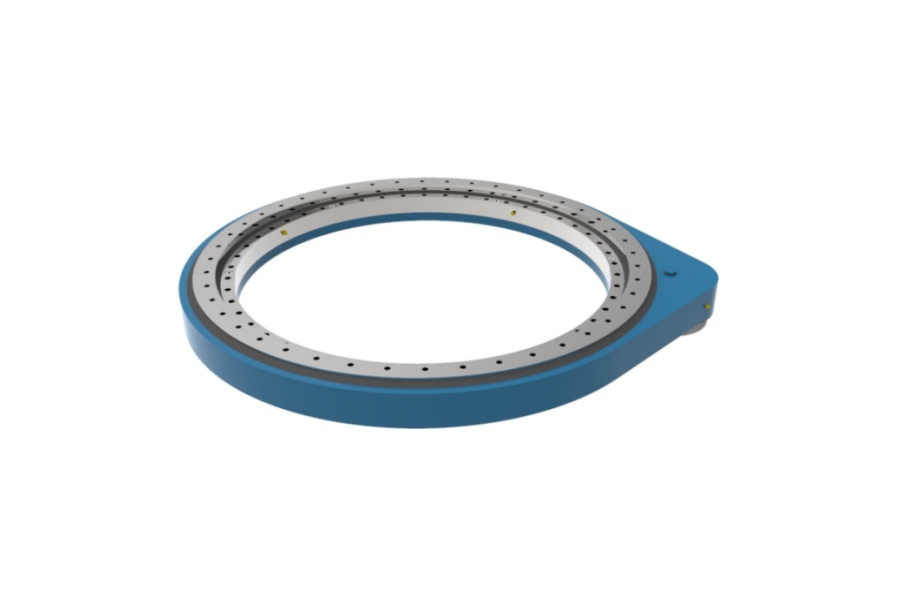
Unleash Unstoppable Torque: The Heavy Duty Gear Slewing Drive SP-H 0755 Engineered for Demanding Worlds
What is the Heavy Duty Gear Slewing Drive SP-H 0755?
The Heavy Duty Gear Slewing Drive SP-H 0755 represents a critical class of rotational power transmission components. At its core, it's a compact, integrated assembly combining a high-precision worm gear set with a large-diameter slewing bearing (often a crossed roller bearing or multi-row roller bearing). This unique configuration converts input rotation (typically from an electric or hydraulic motor) into high-torque, slow-speed, bi-directional rotation of an output platform or structure. Specifically designed for "heavy duty" service, the SP-H 0755 variant signifies a model engineered to withstand immense static and dynamic loads, resist shock and vibration, operate reliably in harsh conditions (dust, moisture, temperature extremes), and deliver long service life with minimal maintenance. Its internal gearing provides inherent self-locking capability when the input shaft is stationary, crucial for safety and stability in load-holding applications. This drive is the muscle behind critical movements in industries where failure is not an option.
Accessing SP-H 0755 CAD Drawings: Precision at Your Fingertips
Integrating a complex component like the SP-H 0755 into machinery design demands absolute dimensional accuracy and a clear understanding of its interfaces. Detailed SP-H 0755 CAD drawings are essential tools for engineers and designers. These digital blueprints, typically available in industry-standard formats like STEP, IGES, DWG, or DXF, provide comprehensive information. They meticulously define the drive's external envelope, mounting hole patterns (PCD, bolt sizes, quantity), input shaft details (spline or keyway specifications), output rotation surface, lubrication points, sealing arrangements, and weight distribution. Access to accurate SP-H 0755 CAD models allows for seamless virtual prototyping, interference checking, accurate load path analysis within larger assemblies, and efficient generation of manufacturing documentation. Reputable manufacturers like LYRADRIVE provide these detailed CAD resources, ensuring designers can confidently incorporate the SP-H 0755 into their projects with precision, minimizing integration risks and streamlining the development process.
The Indispensable Slewing Drive for Construction Machinery
Construction machinery operates in some of the most demanding environments imaginable, subjecting components to relentless shock loads, abrasive dust, moisture, temperature fluctuations, and continuous heavy lifting. The slewing drive is often the literal pivot point upon which the machine's functionality depends. In excavators, robust slewing drives enable the upper structure to rotate smoothly and powerfully under full bucket loads. Tower cranes rely on massive, high-torque slewing drives to rotate the boom and jib, precisely positioning heavy materials hundreds of feet in the air. Concrete pump booms utilize slewing drives to articulate sections, directing concrete flow with accuracy. Drilling rigs depend on them for precise positioning. The Heavy Duty Gear Slewing Drive SP-H 0755 is engineered explicitly for this brutal arena. Its hardened gear teeth withstand shock loads, its premium seals keep contaminants out and lubricant in, its large-diameter bearings distribute immense loads effectively, and its robust housing resists deformation. Choosing a drive like the SP-H 0755 translates directly to reduced downtime, enhanced operator safety, improved machine reliability, and lower total cost of ownership for construction equipment manufacturers and operators.
Commanding Features of the Heavy Duty Gear Slewing Drive SP-H 0755
The SP-H 0755 stands apart due to a suite of features meticulously designed for peak performance in heavy-duty applications:
Exceptional Torque Density: Engineered with optimized gear geometry and high-quality materials, it delivers immense rotational force relative to its compact size, maximizing power transmission efficiency.
Unmatched Load Capacity: Designed to handle colossal axial, radial, and moment loads simultaneously, thanks to its integrated large-diameter slewing bearing and robust structural design.
Superior Durability & Longevity: Features hardened and ground gear teeth (often case-hardened steel), premium rolling elements in the bearing, and specialized heat treatment processes ensure extended service life even under continuous high stress.
Robust Sealing System: Multi-layered, labyrinthine seals, often combined with high-performance grease, provide outstanding protection against ingress of water, dust, mud, and other contaminants, critical for construction, mining, and marine environments.
Precision & Smooth Operation: High manufacturing tolerances and precision grinding ensure low backlash, smooth rotation, and accurate positioning, essential for tasks requiring fine control.
Inherent Safety: The worm gear design typically offers a self-locking characteristic when the input is stationary, preventing unintended rotation and enhancing operational safety, especially in load-holding scenarios.
Integrated Design: Combines the bearing and gearbox into a single, pre-assembled, and pre-lubricated unit, simplifying installation, reducing maintenance points, and enhancing overall structural integrity.
Corrosion Resistance: Critical surfaces and housings often feature specialized coatings, paints, or material choices (like stainless steel options) to combat corrosion in harsh outdoor or marine settings.
Versatile Mounting & Input Options: Designed for flexible integration with various mounting configurations (face mount, flange mount) and input drive types (electric motor flanges, hydraulic motor adapters, manual input options).
Optimized Lubrication: Engineered for efficient grease distribution and retention, often featuring accessible lubrication points and designs that promote long lubrication intervals.
Diverse Applications Demanding the SP-H 0755 Powerhouse
The capabilities of the Heavy Duty Gear Slewing Drive SP-H 0755 make it indispensable across a wide spectrum of demanding industries:
Construction Machinery: The backbone of excavator rotation, crane slewing (tower, mobile, crawler), concrete boom pump articulation, drilling rig positioning, pile driver rotation, and heavy material handler operation.
Renewable Energy: Crucial for precisely tracking the sun in solar tracker systems (single-axis and dual-axis), ensuring maximum energy capture from photovoltaic panels, and for positioning components in concentrated solar power (CSP) plants.
Material Handling: Powering the rotation of heavy-duty industrial cranes (gantry, overhead), large manipulators, rotating conveyors, automated storage and retrieval systems (AS/RS), and port equipment like ship loaders/unloaders and reach stackers.
Forestry & Mining: Driving feller buncher heads, delimber rotators, harvester heads, and rotating platforms on mining equipment like blast hole drills, stackers, and reclaimers, enduring extreme dust and vibration.
Agriculture: Enabling rotation in large irrigation systems (center pivots, linear moves), heavy-duty manure spreaders, and specialized harvesting equipment.
Robotics & Automation: Providing robust, precise rotational axes for heavy payload industrial robots and automated guided vehicles (AGVs) in manufacturing and logistics.
Defense & Aerospace: Used in radar antenna positioning systems, missile launcher turrets, and ground support equipment requiring high reliability and precision.
Marine & Offshore: Powering deck cranes, winch positioning systems, hatch covers, and offshore equipment like gangways and crane jibs, demanding high corrosion resistance.
Specialty Vehicles: Enabling rotation in firefighting turrets, aerial work platforms (boom lifts), mobile screening/crushing plants, and broadcast antenna vehicles.
Understanding the Factors Influencing Heavy Duty Gear Slewing Drive SP-H 0755 Price
The investment in an SP-H 0755 reflects its engineered quality and performance. Several key factors significantly impact its price:
Material Specifications: The grade and quality of steel used for gears, bearing rings, and housings (e.g., high-carbon chromium bearing steel, alloy steels) directly affect cost, durability, and load capacity. Stainless steel components drastically increase price.
Manufacturing Precision & Complexity: The processes involved – precision forging, CNC machining, specialized heat treatment (carburizing, hardening, tempering), grinding of gears and raceways to micron-level tolerances – are capital-intensive and time-consuming, driving up cost.
Bearing Type & Size: The integrated slewing bearing is a major cost component. Larger diameters, multi-row designs (3-row, 4-row), and specialized roller types (crossed roller vs. ball vs. cylindrical roller) significantly influence price. Higher load ratings require larger/more complex bearings.
Gear Design & Quality: Helical worm gears, precision grinding, low-backlash specifications, and special surface treatments enhance performance but add cost. Gear ratio also plays a role.
Sealing & Protection: High-performance seals (multi-lip, PTFE, specialized elastomers), labyrinth designs, and advanced corrosion protection (coatings, paints, passivation) add cost but are essential for harsh environments.
Customization: Modifications from the standard SP-H 0755 design – special mounting flanges, unique input shaft configurations, specific seals for extreme temperatures/chemicals, custom lubrication systems, or special testing requirements – incur additional engineering and manufacturing costs.
Quality Control & Testing: Rigorous in-process and final inspection protocols, including noise testing, backlash measurement, load testing, and potentially full-scale fatigue testing, add to the manufacturing overhead but ensure reliability.
Volume & Supply Chain: Economies of scale apply. Higher volume purchases typically reduce unit cost. Fluctuations in raw material prices (steel, alloys) and energy costs also impact final pricing.
Supplier Expertise & Reputation: Established manufacturers with proven expertise in heavy-duty slewing drives often command a premium based on reliability, engineering support, warranty, and brand reputation.
Supplier of SP-H 0755
When the demands of your application require the proven strength and reliability of a Heavy Duty Gear Slewing Drive like the SP-H 0755, sourcing from a trusted and capable supplier is paramount. LYRADRIVE stands as a premier manufacturer and global supplier of high-performance slewing drives and slewing bearings. They bring deep engineering expertise specifically focused on the design, development, and production of robust rotation solutions for the world's most challenging industries. Choosing LYRADRIVE for your SP-H 0755 needs means accessing:
Deep Technical Expertise: Engineers who understand heavy-duty applications and can provide technical support for integration and optimization.
Proven Manufacturing Quality: Commitment to stringent quality control processes throughout manufacturing, ensuring every SP-H 0755 meets rigorous performance and durability standards.
Reliability & Consistency: A track record of supplying dependable components that minimize downtime and maximize equipment uptime.
Comprehensive Support: Access to detailed technical documentation (specifications, CAD drawings, manuals), application engineering assistance, and responsive customer service.
Customization Capability: Ability to tailor the SP-H 0755 platform to meet specific application requirements beyond standard offerings.
Global Reach: Supply chain and logistical capabilities to support international projects and customers.
Focus on Innovation: Continuous investment in R&D to enhance product performance, efficiency, and lifespan. Partnering with LYRADRIVE provides more than just a component; it delivers engineered rotational solutions backed by expertise and a commitment to powering your most demanding machinery reliably and efficiently. Their focus on the SP-H 0755 exemplifies their dedication to meeting the extreme torque and durability needs of modern industry.