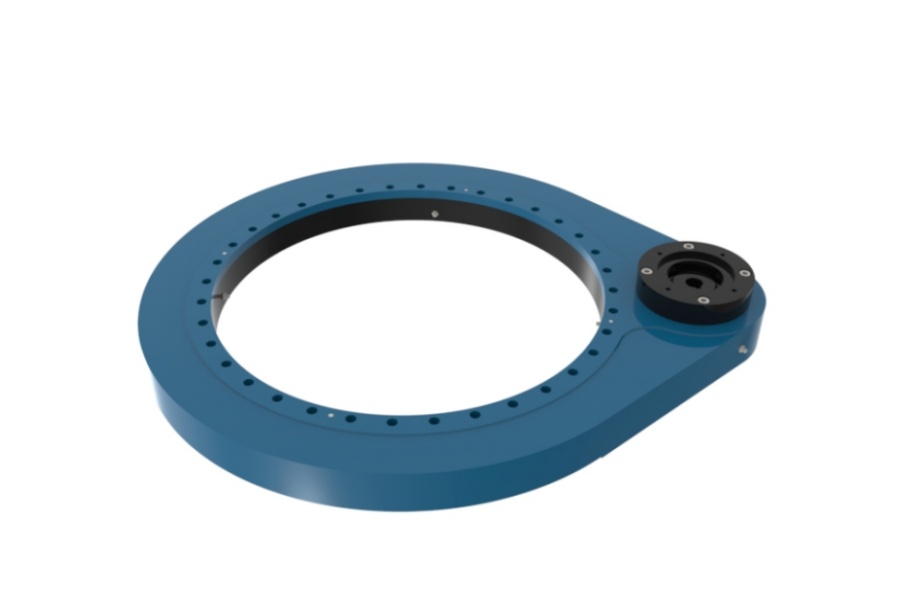
The SP-I 0641: Revolutionizing Compact Motion Systems with Featherlight Precision
What is the Lightweight Slewing Ring Gear Drive SP-I 0641?
The Lightweight Slewing Ring Gear Drive SP-I 0641 is not just a bearing or a gearbox; it's a fully integrated drive solution. At its core lies a slewing ring bearing – a large-diameter bearing designed to handle combined axial, radial, and moment loads while enabling smooth rotation. Crucially integrated within this bearing structure is a precision gear train. The defining characteristic of the SP-I 0641 is its radical weight reduction achieved through advanced materials (like high-strength, lightweight alloys or specialized composites), sophisticated structural optimization (using techniques like topological optimization in design), and compact integration that eliminates redundant housings and components. This results in a drive unit significantly lighter than traditional slewing drives or separate bearing/gearbox assemblies of comparable capacity, all packaged within an exceptionally small envelope. Its design focuses on maximizing power density: delivering high torque and load capacity relative to its minuscule size and weight. This makes it ideal for space-constrained applications where every gram and cubic millimeter counts, fundamentally changing design possibilities in mobile platforms and compact machinery.
The Imperative of Precision Slewing Drives
Precision is paramount in modern rotational motion control. A precision slewing drive goes beyond simple rotation; it demands exact control over position, speed, repeatability, and minimal backlash. This level of accuracy is critical for applications like robotic arms performing delicate assembly tasks, satellite communication antennas precisely tracking signals across vast distances, advanced manufacturing equipment requiring micron-level positioning, or sophisticated camera gimbals capturing stable footage. Precision slewing drives incorporate high-quality gear manufacturing (often involving grinding processes for superior tooth profile accuracy), optimized bearing preload to eliminate internal play, and potentially integrated feedback systems like encoders. They ensure smooth, predictable motion without unwanted vibration or positional drift, enabling complex automation and high-fidelity control systems. The SP-I 0641 embodies this precision philosophy, engineered to provide high torsional stiffness and low backlash essential for demanding tasks. Its integrated nature inherently contributes to precision by minimizing misalignment errors common in multi-component assemblies.
Demanding Excellence: Medical Slewing Bearings and Drives
The medical industry presents some of the most stringent requirements for motion components. Medical slewing bearing applications, often found within advanced imaging systems (CT, MRI gantries), surgical robots, radiation therapy equipment, and patient positioning devices, demand unparalleled reliability, smoothness, cleanliness, and precision. Failure is not an option. These environments necessitate components that operate silently to avoid patient distress, are exceptionally cleanable and resistant to harsh sterilization chemicals, generate minimal particulate matter (crucial in sterile fields), and exhibit extreme reliability over long operational lifetimes. Medical slewing drives must often handle significant loads while maintaining precise, vibration-free motion to ensure diagnostic image quality or the accuracy of robotic surgical instruments. Materials must be biocompatible or suitably isolated, and designs must prevent lubricant migration. While the SP-I 0641's lightweight nature might be secondary in some stationary medical devices, its compactness, potential for clean design, inherent precision, and high rigidity make the underlying technology highly relevant for next-generation medical equipment where space within complex machines is always at a premium.
Conquering the Cube: The Science of Space-Constrained Design
The relentless drive towards miniaturization and increased functionality within fixed volumes defines modern engineering. Achieving space-constrained applications success requires a multi-faceted approach. It involves:
Integration: Combining multiple functions (bearing, gearing, sometimes motor and control) into a single unit eliminates bulky interfaces, housings, and mounting hardware.
Material Science: Utilizing advanced lightweight alloys (e.g., specific high-strength aluminum or titanium alloys), composites, or high-performance engineering plastics to reduce mass without sacrificing strength or stiffness.
Topological Optimization: Using sophisticated software algorithms to design components that remove material only where it contributes minimally to structural integrity, resulting in organic, weight-efficient shapes impossible with traditional design methods.
Compact Gearing: Employing high-precision, high-helix or specialized gear profiles that maximize torque transmission within minimal axial space.
Advanced Manufacturing: Leveraging techniques like precision casting, additive manufacturing (3D printing), and high-tolerance machining to produce complex, optimized geometries cost-effectively.
The SP-I 0641 is a poster child for this philosophy. Its very existence is predicated on conquering space limitations through radical integration and weight-saving measures, enabling capabilities previously impossible within such tight confines. This space-constrained applications focus is its core value proposition.
Lightweight Slewing Ring Gear Drive SP-I 0641: Hallmark Features
The SP-I 0641 distinguishes itself through a constellation of advanced features engineered for peak performance in demanding, compact environments:
Radical Weight Reduction: Achieves weight savings often exceeding 30-50% compared to traditional slewing drives of similar capacity through advanced materials and structural optimization. This is critical for mobile platforms (drones, robotics) where weight directly impacts battery life, payload, and agility.
Exceptional Compactness: Features an ultra-low height profile and minimized outer diameter, maximizing usable space within the application. Ideal for integration into tight machinery envelopes.
High Power Density: Delivers impressive torque output relative to its size and weight, a result of efficient gear design, high-quality materials, and optimized load paths within the integrated structure.
Precision Performance: Engineered for low backlash and high torsional rigidity, ensuring accurate positioning, smooth motion control, and resistance to deflection under load. Essential for automation and instrumentation.
Robust Load Capacity: Despite its lightweight nature, it handles significant combined loads (axial, radial, and moment loads) simultaneously, thanks to the integrated slewing ring bearing design and optimized internal geometry.
Integrated Sealing: High-performance seals protect internal gearing and bearings from contaminants like dust, dirt, and moisture, enhancing longevity and reliability in harsh environments.
Versatile Mounting: Designed for straightforward integration into various systems, typically featuring standardized bolt patterns and mounting interfaces.
Optimized Lubrication: Pre-lubricated with high-performance, long-life greases suitable for the expected operating temperature range and load conditions, minimizing maintenance needs.
Lightweight Slewing Ring Gear Drive SP-I 0641: Powering Diverse Applications
The unique blend of compactness, lightness, and strength opens doors across numerous industries:
Robotics & Automation: Joints in lightweight robotic arms (collaborative and industrial), rotary tables for assembly, positioning stages, tool changers. Reduces overall robot arm mass, improving speed, payload capacity, and energy efficiency.
Aerospace & UAVs/Drones: Antenna positioning systems, sensor gimbals, camera turrets, landing gear mechanisms, actuator systems in satellites and aircraft. Weight savings are paramount for flight endurance and payload.
Medical Equipment: Advanced imaging systems (rotating components within CT/MRI), robotic surgery arms, patient positioning platforms, diagnostic equipment requiring precise rotation. Compactness allows for more complex machine designs within limited space.
Semiconductor Manufacturing: Precision wafer handling robots, inspection station rotators, stage positioning. Demands cleanliness, precision, and reliability in tight cleanroom equipment footprints.
Material Handling: Lightweight rotary indexing tables, automated guided vehicle (AGV) turntables, compact conveyor diverters. Enhances efficiency in space-limited factories or warehouses.
Renewable Energy: Solar tracker azimuth drives (especially for distributed, smaller-scale trackers), pitch/yaw mechanisms for small wind turbines. Weight reduction lowers structural costs.
Defense & Security: EO/IR sensor turrets on vehicles/UAVs, weapon stations, targeting systems, communication arrays. Requires robustness, precision, and minimal size/weight in mobile platforms.
Test & Measurement: Precision rotary stages for calibration, positioning in compact test fixtures, optical equipment rotators. Needs accuracy and stability in often confined lab settings.
Packaging Machinery: Rotary fillers, cappers, labelers where compact, precise rotation is needed within dense machine layouts. Improves machine speed and flexibility.
Broadcast & Cinematography: Camera jibs, compact robotic camera heads, remote pan-tilt units. Enables complex shots with lighter support structures.
Understanding Lightweight Slewing Ring Gear Drive SP-I 0641 Pricing Factors
The investment in an SP-I 0641 is influenced by several key factors:
Material Costs: The use of high-strength, lightweight alloys (e.g., specialized aluminum, titanium, or magnesium alloys) or advanced composites significantly increases raw material costs compared to standard steel components. Material grade and certifications (e.g., aerospace-grade) also impact price.
Manufacturing Complexity: Achieving radical weight reduction involves complex design features (thin walls, intricate shapes) and demanding manufacturing processes. Techniques like precision casting, high-tolerance CNC machining, specialized heat treatment, topological optimization execution, and potentially additive manufacturing all contribute to higher production costs.
Precision Requirements: Meeting stringent specifications for low backlash, high rigidity, and tight dimensional tolerances necessitates advanced gear grinding, super-finished bearing surfaces, meticulous assembly processes, and rigorous quality control – all adding cost.
Bearing and Gear Specifications: The size, type (e.g., cross-roller vs. four-point contact), precision grade, and load rating of the integrated slewing ring bearing significantly impact cost. Similarly, gear quality (AGMA or DIN class), material, tooth profile complexity, and hardening processes affect price.
Customization: While the SP-I 0641 is a specific model, modifications like special seals, coatings (anodizing, specialized platings), custom shaft configurations, integrated sensors (encoders), or unique mounting flanges incur additional engineering and production expenses.
Volume: As with most manufactured goods, unit price generally decreases with higher order quantities due to amortized setup costs and more efficient production runs.
Supplier Expertise & Reputation: Suppliers with proven expertise in lightweight, high-precision drive manufacturing, stringent quality systems (like ISO 9001, AS9100), and strong technical support often command a premium reflecting their reliability and value-added services.
Ancillary Components: Costs for mounting hardware, lubrication systems (if beyond standard), or optional motor adapters/flanges are typically additional.
Supplier of Lightweight Slewing Ring Gear Drive SP-I 0641
When seeking the performance and reliability of the Lightweight Slewing Ring Gear Drive SP-I 0641, partnering with an experienced and capable supplier is critical. LYRADRIVE stands as a premier provider of advanced motion solutions, specializing in precisely the kind of high-performance, integrated drive systems exemplified by the SP-I 064.We understand the intricate challenges of space-constrained applications and the relentless pursuit of weight reduction without compromising on strength or precision. LYRADRIVE's commitment extends beyond just supplying components:
Deep Engineering Expertise: Our team possesses extensive knowledge in slewing ring technology, precision gearing, lightweight design principles, and system integration, allowing us to offer expert guidance and support.
Focus on Innovation: We continuously invest in research and development, leveraging advanced materials and manufacturing techniques to push the boundaries of what's possible in compact motion control, including refining solutions for demanding sectors like medical slewing bearing requirements.
Quality Assurance: Rigorous quality control processes are embedded throughout manufacturing, ensuring every SP-I 0641 meets exacting performance and reliability standards, often adhering to international quality certifications.
Customization Capability: While offering the standard SP-I 0641, LYRADRIVE can often provide tailored solutions – modifying seals, coatings, mounting interfaces, or integrating sensors to perfectly match unique application demands.
Technical Support: We provide comprehensive technical assistance, from initial selection and integration guidance to troubleshooting and maintenance support.
Global Reach & Reliability: LYRADRIVE is positioned to support customers worldwide with consistent quality and dependable supply chains. Our focus on manufacturing precision slewing drive systems ensures dependable performance.
LYRADRIVE is more than just a vendor; we are a partner dedicated to enabling your innovation through superior motion technology. Our mastery in creating ultra-compact, high-performance drives like the SP-I 0641 makes us the ideal choice for engineers tackling the most demanding space and weight challenges.
Embrace the Future of Compact Motion
The Lightweight Slewing Ring Gear Drive SP-I 0641 represents a significant leap in motion control technology. By masterfully integrating a robust slewing ring bearing with a precision gear drive into an ultra-lightweight, incredibly compact package, it overcomes traditional design barriers. Its ability to deliver high torque, exceptional rigidity, and reliable performance within minimal space and mass unlocks new possibilities across robotics, aerospace, medical technology, automation, and beyond. Understanding its features, diverse applications, and the factors influencing its cost empowers designers to make informed decisions. When selecting this advanced component, partnering with a specialized supplier like LYRADRIVE, with proven expertise in lightweight, high-precision drive solutions, ensures access to the technology, quality, and support needed to bring groundbreaking compact motion designs to life. The SP-I 0641 isn't just a component; it's an enabler for the next generation of lightweight, agile, and powerful machinery.