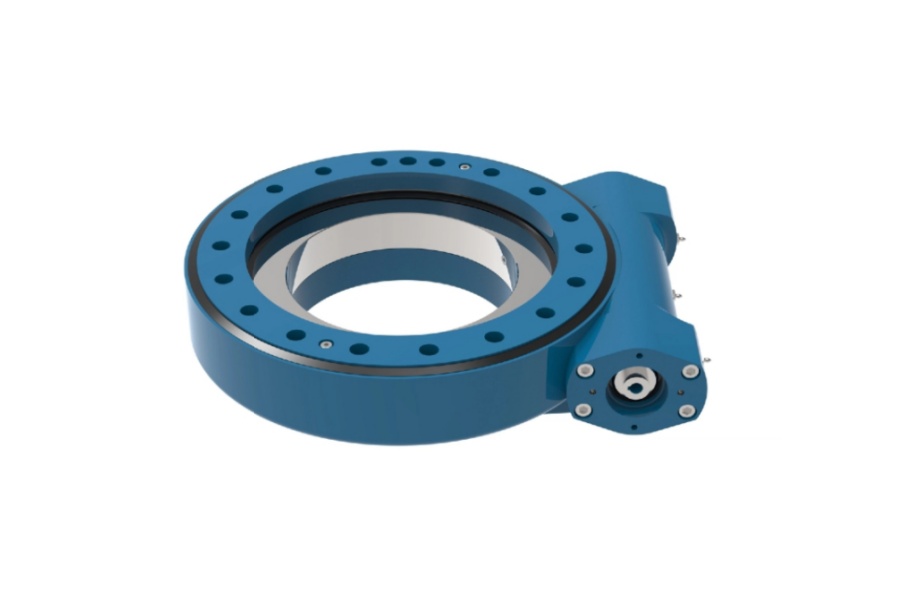
The Enveloping Revolution: How SE12 Redefines Heavy-Duty Motion Control
What is the Enveloping Rotary Drive SE12?
Traditional slewing drives often feature a ring gear mounted externally or within a simple housing. The Enveloping Rotary Drive SE12 fundamentally changes this paradigm. Its defining characteristic is the "enveloping" design: the slewing bearing is fully encapsulated within a massive, rigid, single-piece forged or precision-cast housing. This housing doesn't just hold the bearing; it becomes an integral structural component, forming the primary load path. The internal ring gear meshes with a high-precision pinion driven by a planetary gearbox, which is itself coupled to a high-torque hydraulic or electric motor. All critical components – bearing, gearing, motor interface – are sealed within this protective fortress, shielded from external elements and contributing directly to the system's immense strength. The "SE12" designation typically signifies a specific size, torque capacity, or design iteration within this enveloping drive series, engineered for ultra-heavy-duty applications where failure is not an option.
Supercharged Joints: The Heartbeat of Modern Mega-Projects
Modern engineering marvels – colossal tunnel boring machines chewing through bedrock, mammoth offshore cranes building wind farms in stormy seas, towering mining excavators moving mountains, and agile heavy-lift robots in automated factories – all share a critical dependency: high-performance motion joints. These joints must withstand astronomical loads, relentless vibration, punishing environmental conditions, and millions of operational cycles without faltering. They are the pivots upon which billion-dollar projects turn. Conventional slewing bearings and drives, while powerful, often reach their limits in these scenarios. Bending moments can distort ring gears, external contamination destroys lubrication, shock loads fracture housings, and extreme temperatures compromise materials. The demand is clear: motion systems need radical evolution towards greater intrinsic strength, resilience, and self-protection to meet the escalating demands of 21st-century super-engineering. This is the challenge the enveloping design philosophy directly confronts.
Defying Disaster: The Explosion-Proof Slewing Bearing Imperative
In hazardous environments where flammable gases, vapors, or combustible dusts are present – oil & gas platforms, chemical plants, grain silos, coal mines, paint booths – standard equipment becomes a potential ignition source. Sparks from motors, electrical faults, or even excessive surface temperatures can trigger catastrophic explosions. Explosion-proof (Ex-proof) slewing bearings and drives are not a luxury; they are a mandatory safeguard for life and infrastructure. Achieving Ex-proof certification (like ATEX, IECEx, or NEC) for a slewing system is immensely complex. It requires:
Containment: The entire drive housing must be robust enough to contain any internal explosion without rupturing, preventing flames or hot gases from escaping to the hazardous atmosphere.
Flame Path Engineering: Precise machining of joints (e.g., between housing halves, shaft seals) creates long, narrow gaps that cool escaping gases below ignition temperature before they reach the external environment.
Temperature Control: Motors and gearing must operate below the auto-ignition temperature of the surrounding hazardous substances, often requiring special cooling or derating.
Spark Mitigation: All internal components and electrical systems must be designed to prevent sparking under normal and fault conditions.
Integrating these stringent requirements into a high-load slewing drive like the SE12 demands exceptional engineering, specialized materials, and rigorous testing. The enveloping housing design inherently provides a strong foundation for achieving the necessary containment strength.
Conquering the Cryosphere: Extreme Low Temperature Slewing Drive Challenges
Operating reliably at temperatures plunging to -40°C, -50°C, or even lower – common in Arctic oil exploration, LNG terminals, high-altitude infrastructure, and specialized cryogenic facilities – presents unique obstacles for slewing drives:
Material Embrittlement: Standard steels become brittle and lose toughness at very low temperatures, increasing fracture risk under impact or high stress. Special low-temperature alloys (like specific grades of nickel steel) are essential for critical components like the housing, bearing rings, and gears.
Lubrication Failure: Conventional greases solidify and oils thicken dramatically, leading to inadequate lubrication, massively increased friction, wear, and potential seizure. Specially formulated synthetic lubricants with exceptional low-temperature flow characteristics and pour points are critical.
Sealing Catastrophe: Standard elastomer seals (O-rings, lip seals) harden, shrink, and lose elasticity, becoming brittle and ineffective, allowing contamination ingress and lubricant leakage. Seals must use specialized low-temperature elastomers (e.g., fluorocarbon, silicones rated for extreme cold) or advanced polymer compounds.
Contraction & Clearances: Different materials contract at different rates when cooled. This can dangerously alter critical internal clearances (e.g., gear backlash, bearing preload) if not meticulously designed and manufactured to compensate.
Power & Hydraulics: Electric motors require special windings and lubricants; hydraulic systems need specialized cold-weather fluids and heating elements to maintain viscosity and prevent freezing.
An Extreme Low Temperature Slewing Drive, such as an Arctic-rated SE12 variant, is engineered from the ground up with these factors in mind. Material selection, lubrication systems, seal design, thermal contraction calculations, and component specifications are all optimized to ensure reliable starting, smooth operation, and long service life in the planet's coldest environments.
Unpacking the Powerhouse: Key Features of the Enveloping Rotary Drive SE12
The SE12's enveloping architecture delivers a suite of compelling features that set it apart in the heavy-duty drive market:
Unmatched Structural Rigidity: The massive single-piece housing enveloping the bearing creates an incredibly stiff structure. This minimizes deflection under high bending moments and radial loads, ensuring precise gear meshing (pinion to ring gear) and optimal load distribution across the bearing raceways, directly translating to longer life and higher load capacity for a given size.
Superior Load Capacity & Moment Resistance: By integrating the bearing as a core structural element within the robust housing, the SE12 achieves exceptional ratings for axial load, radial load, and crucially, tilting moment. It excels in applications where overturning forces are dominant.
Enhanced Protection & Sealing: The enveloping design provides a natural fortress. Combined with multi-layered, high-performance seals (often including labyrinth paths and exclusionary seals), it offers outstanding defense against water, dust, mud, abrasive particles, and corrosive agents, significantly extending component life in harsh environments.
Optimized Power Density: Integrating the motor, high-ratio planetary gearbox, and the enveloping slewing bearing assembly into a compact unit delivers exceptional torque output relative to its footprint. This saves valuable space in machinery design.
Simplified Installation & Alignment: The SE12 typically presents a straightforward mounting interface. The critical alignment between the slewing bearing and the gearing is handled internally during precision manufacturing, eliminating complex and error-prone field alignment procedures common with separate bearing and drive systems.
Integrated Design Flexibility: The core enveloping concept can be adapted with various motor types (high-torque hydraulic, AC/DC electric), gear ratios, bearing configurations (single or double row ball, cross roller), and mounting orientations to suit diverse application needs.
Improved Serviceability (Design Dependent): While robust, many SE12 designs incorporate features like removable end caps or inspection ports, allowing for easier maintenance access to seals, lubrication points, and sometimes pinion gears without full disassembly.
Where Power Meets Precision: Diverse Applications of the SE12 Enveloping Drive
The unique combination of strength, durability, and protection makes the Enveloping Rotary Drive SE12 the prime mover for countless demanding applications across heavy industries:
Heavy Lifting & Material Handling: The core application domain. Giant offshore pedestal cranes lifting modules onto platforms, high-capacity harbor cranes handling containers, demanding shipboard cranes, heavy-duty forklifts, and specialized lifting equipment all rely on the SE12's moment resistance and reliability.
Mining & Quarrying: Large excavators (especially high-capacity models), massive rope shovels, bulk material handling stackers and reclaimers operating in highly abrasive and dusty environments demand the SE12's robustness and sealing.
Construction Mega-Machinery: Tunnel boring machines (TBMs) where continuous rotation under immense thrust and ground pressure is critical, large piling rigs, and sophisticated heavy-duty drilling platforms benefit from the integrated strength and precision.
Forestry Processing: Delimbers, harvesters, and forwarders operating in rugged, dirty conditions utilize the SE12's power and environmental protection for swing and boom functions.
Renewable Energy: Installation vessels and port cranes handling massive wind turbine components, and the slew mechanisms on large solar trackers requiring high precision and durability under environmental stress.
Robotics & Automation: Heavy-duty robotic arms for casting, forging, or large part manipulation in manufacturing, where high payloads and precise, repeatable rotation are needed in potentially harsh factory settings.
Specialized Vehicles: Advanced military vehicles, firefighting turrets, and specialized recovery equipment requiring compact, powerful, and protected rotational drives.
Hazardous & Extreme Environments: As discussed, specifically engineered SE12 variants are indispensable in explosion-proof zones (oil & gas, chemical) and extreme low-temperature operations (Arctic logistics, LNG).
Investing in Performance: Factors Influencing Enveloping Rotary Drive SE12 Pricing
The Enveloping Rotary Drive SE12 is a premium engineered component, and its price reflects the significant technology, materials, and manufacturing investment. Key cost drivers include:
Size & Load Capacity: Larger drives (e.g., SE12-1500 vs. SE12-800) designed for higher axial loads, radial loads, and crucially, tilting moments, require significantly more material, larger bearings, and heavier gearing, escalating cost substantially.
Bearing Type & Quality: The choice of slewing bearing (single row ball, double row ball, cross roller) and its internal precision, material grade (standard vs. vacuum-degassed clean steel), heat treatment, and raceway hardening processes significantly impact cost. High-precision, high-capacity bearings are a major cost component.
Gearbox Specifications: The planetary gearbox's ratio, torque rating, precision grade (e.g., AGMA class), gear material, heat treatment, and bearing quality directly influence complexity and price. High reduction ratios for high torque output add cost.
Housing Material & Manufacturing: The massive enveloping housing is central. Whether forged (highest strength, highest cost) or high-quality cast, and the extensive machining required to precise tolerances represent a significant portion of the drive's cost. Complex geometries add machining time.
Drive Motor Type & Integration: The cost of the integrated motor (high-torque hydraulic motor or large electric motor) and the complexity of its interface/mounting within the drive assembly contribute to the overall price.
Sealing & Protection Level: Standard IP ratings cost less than achieving IP69K water resistance or specialized sealing for extreme environments (like Arctic cold or chemical exposure). Explosion-proof certification adds significant engineering, testing, and component cost premiums.
Material Specifications: Standard structural steel suffices for many applications. However, drives requiring special materials for corrosion resistance (stainless components, special coatings), extreme low-temperature operation (nickel alloy steels), or enhanced wear resistance add cost.
Precision & Tolerances: Applications demanding ultra-precise positioning or minimal backlash require higher manufacturing precision throughout (gears, bearings, housing machining), increasing production time and cost.
Customization & Special Features: Modifications from standard designs (unusual mounting flanges, special shaft configurations, integrated sensors, custom lubrication systems, specific paint requirements) incur additional engineering and manufacturing expenses.
Certification & Testing: Meeting specific industry standards (ISO, DNV-GL, ABS, API), undergoing rigorous load testing, or obtaining explosion-proof (ATEX/IECEx) certification involves significant time and cost.
Volume & Supplier: Economies of scale apply. Lower volume production runs are inherently more expensive per unit than high-volume manufacturing. Reputable manufacturers with proven quality and reliability command a premium over generic suppliers.
The Pinnacle of Rotational Power
The Enveloping Rotary Drive SE12 is far more than just a slewing drive; it represents a fundamental shift towards integrated, ultra-robust motion solutions for the world's most challenging applications. By enveloping the critical slewing bearing within a fortress-like housing, it achieves levels of structural integrity, load capacity (especially moment resistance), and environmental protection that traditional designs struggle to match. From the depths of mines and tunnels to the freezing Arctic and hazardous industrial zones, from building wind farms offshore to automating heavy factory tasks, the SE12 provides the reliable, powerful, and protected rotation that modern super-engineering demands. While representing a significant investment, its design directly addresses the core failure modes of conventional systems, offering superior longevity, reduced downtime, and enhanced safety – factors that ultimately deliver compelling value in the most critical operations. It stands as a testament to advanced mechanical engineering, enabling machines to move heavier loads, work in tougher places, and push the boundaries of what's possible.
Supplier of Enveloping Slewing Drive SE12
Selecting LYRADRIVE's Enveloping Slewing Drive SE12 is an investment in uncompromising performance and operational certainty. It transcends being a mere component; it is the engineered solution for applications where conventional drives falter under immense loads, harsh environments, and the relentless demand for precision and uptime. From harnessing the wind's power atop towering turbines to excavating the earth's riches deep in a mine, from positioning critical radar on naval vessels to lifting thousands of tons in a port crane, the SE12 delivers the robust, reliable rotational force that keeps industries moving. Its enveloping worm design is the cornerstone of its superiority, offering unmatched torque density, load distribution, and inherent safety. While the initial investment reflects its advanced capabilities, the SE12 pays dividends for years through reduced maintenance, minimized downtime, extended service life, and the sheer reliability that defines operational excellence. For engineers and operators facing the toughest rotational challenges, the LYRADRIVE SE12 Enveloping Slewing Drive isn't just an option; it's the definitive answer.