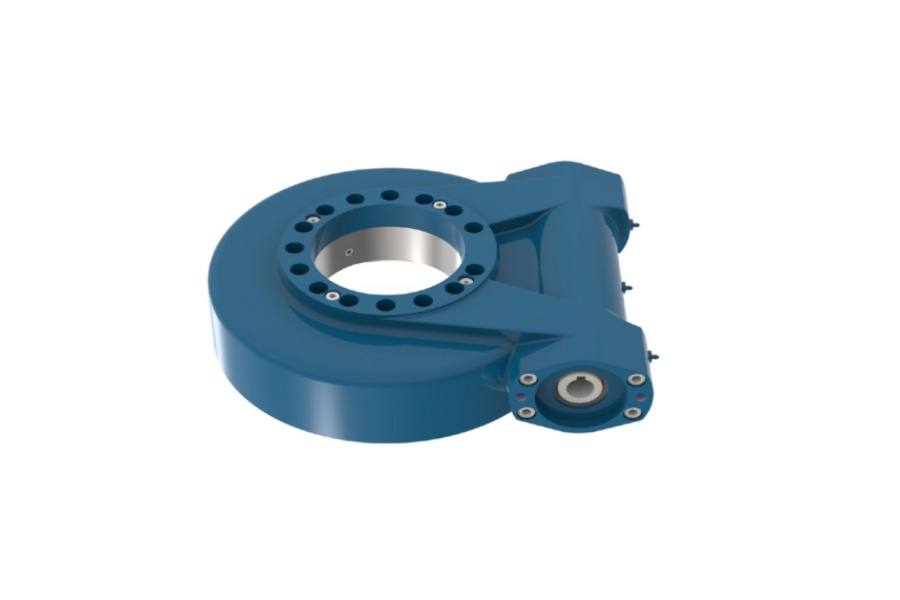
The SE9 Enveloping Slewing Drive: Revolutionizing Heavy-Duty Rotation with Unmatched Rigidity
What is the Enveloping Slewing Drive SE9?
Forget ordinary slewing rings; the Enveloping Slewing Drive SE9 from LYRADRIVE is a revolutionary integrated drive system. It fundamentally combines a high-torque planetary gearbox, a large-diameter enveloping worm gear set, and a robust slewing bearing into a single, exceptionally compact, and self-contained unit. The defining "enveloping" characteristic refers to the worm wheel design, where the worm gear partially or fully wraps around the worm screw. This ingenious geometry dramatically increases the contact area between the worm threads and the wheel teeth compared to standard worm drives. The result? Significantly higher torque density, vastly improved load distribution across the gear teeth, inherent resistance to shock loads, and a natural self-locking capability that prevents back-driving under load. The SE9 designation signifies LYRADRIVE's top-tier series, engineered for extreme duty cycles, maximum reliability, and built to deliver consistent performance in environments where failure is not an option. It's not just a component; it's the engineered core of heavy machinery rotation.
Wind Turbine Yaw Drive SE9: Mastering the Elements
Precision and unwavering reliability are non-negotiable in wind energy. The LYRADRIVE SE9 Enveloping Slewing Drive is the powerhouse behind wind turbine yaw systems, responsible for constantly orienting the massive nacelle and rotor assembly into the wind. This task demands incredible torque to overcome inertia and aerodynamic forces acting on blades sometimes exceeding 80 meters in length. The SE9 thrives here. Its enveloping worm design delivers the exceptional torque density needed in a compact package, fitting perfectly within the nacelle's constrained space. The high number of contact teeth ensures smooth, precise, and virtually backlash-free rotation, crucial for maximizing energy capture efficiency and minimizing stress on the tower structure. Furthermore, the SE9's inherent self-locking capability acts as a critical safety feature, preventing unwanted nacelle movement during high winds or maintenance, even if the drive motor loses power. Engineered with premium materials and advanced sealing (often IP66 or higher), the SE9 withstands constant exposure to salt spray, extreme temperature fluctuations, dust, vibration, and the relentless fatigue cycles inherent to wind operations, guaranteeing decades of low-maintenance service atop the tower.
Mining Slewing Drive SE9: Built for Brutal Conditions
Mining operations are synonymous with extreme environments: crushing loads, pervasive abrasive dust, constant vibration, shock impacts from blasting or digging, and limited maintenance windows. Equipment failure means costly downtime and lost production. This is precisely where the LYRADRIVE SE9 Enveloping Slewing Drive proves its mettle. Found in critical applications like excavator superstructures, stacker-reclaimers, tunnel boring machines, and large material handling shovels, the SE9 handles the massive overturning moments, axial forces, and radial loads encountered daily. The enveloping gear design is key to its mining prowess. The increased contact area distributes the immense stresses over more teeth, drastically reducing localized wear and dramatically extending service life even under shock loading when buckets strike hard rock. Robust seals and specialized lubrication systems effectively exclude abrasive contaminants, protecting the vital internal components. The SE9's compact integration simplifies installation and maintenance in the tight confines of heavy machinery. Its legendary durability translates directly into reduced unplanned downtime, lower total cost of ownership, and increased productivity for mining operators facing relentless pressure to deliver.
Ultra-High Load Slewing Drive: The SE9 Standard
When specifications demand the absolute highest load capacity in the smallest possible envelope, the Enveloping Slewing Drive SE9 stands alone. Its core advantage lies in the enveloping worm principle, which fundamentally enables higher torque transmission and better load sharing than any conventional single-axis worm drive or many large-diameter gear drives. The SE9 is engineered from the ground up to handle staggering combined loads – axial forces exceeding 10,000 kN, radial loads surpassing 5,000 kN, and tilting moments well over 50,000 kNm are achievable within specific models. This capability stems not only from the gear design but also from the integration of a massive, high-strength slewing bearing and an optimized housing structure that acts as a unified load path. Finite element analysis (FEA) optimizes every component for stress distribution under maximum load scenarios. Premium alloy steels, specialized heat treatment processes (like case hardening and tempering), and precision manufacturing ensure material integrity. The SE9 is the definitive solution for applications like giant container cranes, heavy-lift offshore cranes, massive radar platforms, satellite communication dishes, and advanced artillery systems – anywhere where ultimate structural integrity and rotational control under extreme weight and force are paramount.
Dominant Features of the Enveloping Slewing Drive SE9
The LYRADRIVE SE9 isn't just powerful; it's intelligently engineered for superior performance and reliability. Its defining features create a compelling package:
Exceptional Torque Density & High Efficiency: The enveloping worm gear design delivers significantly more torque in a smaller space than conventional drives, while optimized gear geometry minimizes friction losses.
Superior Load Distribution & Shock Resistance: Multiple simultaneous tooth contact spreads loads evenly, drastically reducing peak stresses on individual teeth and enabling the drive to absorb severe shock loads without damage.
Inherent Self-Locking: The high friction angle of the enveloping worm prevents back-driving under load without needing additional brakes (in most orientations), enhancing safety and holding precision.
Minimal Backlash & High Rigidity: Precision manufacturing and preloaded bearing arrangements ensure extremely low rotational backlash and high torsional stiffness, enabling precise positioning and control.
Robust Construction & Durability: Manufactured from high-grade alloy steels, subjected to rigorous heat treatment, and featuring hardened gear surfaces, the SE9 is built for maximum wear resistance and long service life.
Integrated Design: Combining gearbox, bearings, and often the mounting structure into one unit simplifies installation, reduces alignment issues, and saves valuable space.
Advanced Sealing & Lubrication: Multi-layered sealing systems (labyrinths, V-rings, special grease) effectively exclude contaminants, while optimized internal lubrication ensures consistent performance in harsh environments. Corrosion-resistant options are available.
Low Maintenance Requirements: Designed for longevity and reliability, the SE9 typically requires only periodic lubrication checks/replenishment under normal operating conditions.
Expansive Applications of the Enveloping Slewing Drive SE9
The unique combination of power, precision, compactness, and robustness makes the SE9 indispensable across heavy industry:
Renewable Energy: The undisputed leader for wind turbine yaw and pitch drives, and increasingly used in solar tracker azimuth drives for large utility-scale installations.
Mining & Heavy Construction: Excavators (crawler, hydraulic), bucket-wheel excavators, stacker-reclaimers, tunnel boring machines (TBM cutterhead drives), material handlers, and large drilling rigs.
Material Handling: Ship-to-shore cranes, rubber-tyred gantry (RTG) cranes, rail-mounted gantry (RMG) cranes, bulk handling stackers, and heavy-duty industrial robotic arms.
Defense & Aerospace: Radar and satellite communication (SATCOM) antenna positioning, missile launcher systems, tank turret drives, and advanced weapons platforms requiring precise movement under load.
Industrial Machinery: Large indexing tables, pallet changers, mixer drives for heavy materials, foundry equipment, and specialized automation requiring high torque and positioning accuracy.
Marine & Offshore: Offshore crane slew drives, davit systems, deck machinery, and dynamic positioning thrusters.
Infrastructure: Bridge inspection units, large ventilation systems, and specialized construction equipment.
Factors Influencing the Price of the Enveloping Slewing Drive SE9
While the SE9 delivers exceptional value through performance and longevity, its price reflects its advanced engineering and capabilities. Key cost drivers include:
Size & Load Capacity: Larger diameter drives designed for higher axial/radial loads and tilting moments require significantly more material and complex manufacturing, increasing cost substantially.
Gear Ratio & Complexity: Drives requiring very high reduction ratios or custom gearing configurations involve more complex gear sets and machining, impacting price.
Material Specifications: The use of specialized high-strength, corrosion-resistant alloys (e.g., specific grades of steel, sometimes coatings) adds material costs.
Precision & Manufacturing Tolerances: Achieving the ultra-precise gear profiles, bearing races, and assembly tolerances demanded by the enveloping design requires advanced CNC machining, grinding, and meticulous quality control, contributing significantly to cost.
Bearing Type & Configuration: The integrated slewing bearing's size, type (ball, roller, cross roller), number of rows, and preload requirements are major cost factors.
Sealing & Environmental Protection: Higher IP ratings (e.g., IP66, IP69K) necessitate complex multi-stage sealing systems and specialized lubricants, adding expense. Corrosion protection treatments also add cost.
Customization & Special Features: Any deviation from standard models – custom mounting flanges, special shaft configurations, integrated sensors (encoders, temperature, vibration), unique lubrication systems, or specific surface treatments – increases engineering and manufacturing costs.
Quantity & Order Volume: Economies of scale apply; larger production runs typically reduce the unit cost compared to single, highly customized units.
Ancillary Components: The cost of motors, brakes (if required beyond self-locking), frequency drives, and control systems specified for integration is usually separate but part of the total system cost.
Testing & Certification: Drives requiring specific certifications (e.g., for wind industry, marine, or defense) undergo rigorous additional testing and documentation, adding to the cost.
Supplier of Enveloping Slewing Drive SE9
Selecting LYRADRIVE's Enveloping Slewing Drive SE9 is an investment in uncompromising performance and operational certainty. It transcends being a mere component; it is the engineered solution for applications where conventional drives falter under immense loads, harsh environments, and the relentless demand for precision and uptime. From harnessing the wind's power atop towering turbines to excavating the earth's riches deep in a mine, from positioning critical radar on naval vessels to lifting thousands of tons in a port crane, the SE9 delivers the robust, reliable rotational force that keeps industries moving. Its enveloping worm design is the cornerstone of its superiority, offering unmatched torque density, load distribution, and inherent safety. While the initial investment reflects its advanced capabilities, the SE9 pays dividends for years through reduced maintenance, minimized downtime, extended service life, and the sheer reliability that defines operational excellence. For engineers and operators facing the toughest rotational challenges, the LYRADRIVE SE9 Enveloping Slewing Drive isn't just an option; it's the definitive answer.