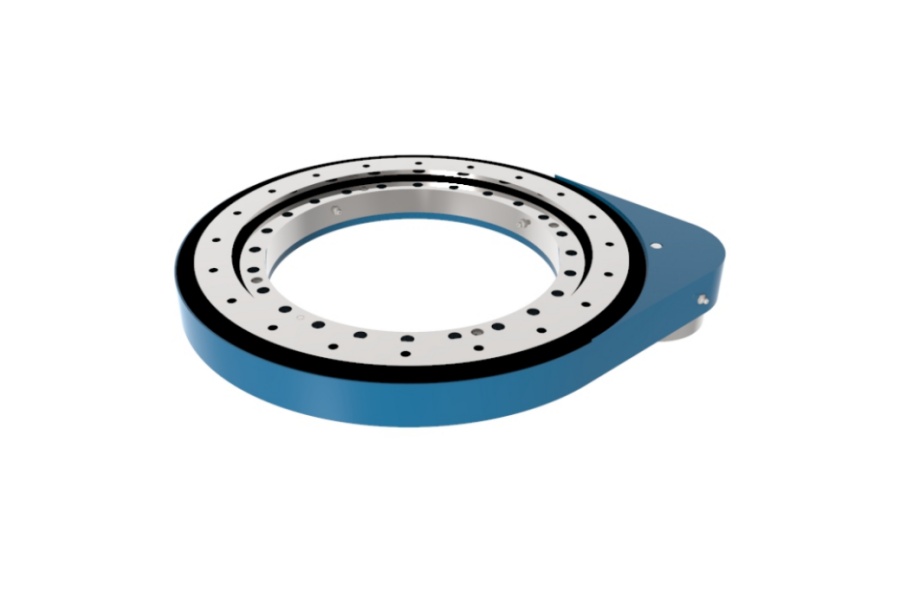
Revolutionize Motion: The Lightweight Slewing Ring Gear Drive SP-I 0411 Redefines Compact Power
What is the Lightweight Slewing Ring Gear Drive SP-I 0411?
The Lightweight Slewing Ring Gear Drive SP-I 0411 is a highly integrated, precision-engineered motion solution. It combines a robust slewing bearing (ring gear) with a compact, high-efficiency gearbox and often an integrated motor (or provisions for one) into a single, sealed unit. Designed specifically for applications where minimizing mass is critical without sacrificing strength or reliability, the SP-I 0411 utilizes advanced materials like high-strength alloys and optimized structural designs. Its core function is to enable controlled, high-torque rotational movement around a single axis, supporting substantial radial, axial, and moment loads simultaneously. The "0411" designation typically refers to its specific size and torque capacity within the SP-I lightweight series, indicating its suitability for mid-range load requirements within the lightweight category.
Lightweight vs. Standard Slewing Drive: The Critical Divide
The fundamental difference lies in the relentless focus on mass reduction achieved through sophisticated engineering, without compromising core performance. Standard slewing drives prioritize raw load capacity and durability, often utilizing thicker ring sections, larger gear teeth, and denser materials like standard carbon steels. This inherent robustness makes them heavier. The Lightweight SP-I 0411, conversely, employs strategic weight-saving tactics:
Advanced Materials: Extensive use of high-strength, low-alloy (HSLA) steels, aluminum alloys for non-critical housings, and sometimes composite elements where feasible.
Topology Optimization: Utilizing Finite Element Analysis (FEA) to design structures that remove material only where stresses are low, creating organic, weight-efficient shapes without sacrificing strength.
Precision Manufacturing: Tight tolerances and optimized gear tooth profiles ensure maximum power transmission efficiency with minimal material, reducing the need for bulk.
Integrated Design: Combining the bearing, gearing, and mounting structures into a single, optimized unit eliminates redundant housings and fasteners. The result is a drive like the SP-I 0411 that can be 30-50% lighter than a standard slewing drive of comparable torque rating, dramatically impacting system dynamics and energy consumption.
Unleashing Power: The High Torque Compact Slewing Drive Advantage
The term "High Torque Compact Slewing Drive" perfectly encapsulates the core achievement of designs like the SP-I 0411. "Compact" refers to its minimized spatial envelope – it occupies less volume than traditional solutions capable of similar output. "High Torque" signifies its ability to generate and handle significant rotational force relative to its size and weight. This is made possible by:
Efficient Gear Design: Utilizing high-ratio, multi-stage planetary or worm gear sets within the integrated gearbox to amplify motor torque dramatically.
Optimized Load Path: Precision machining ensures perfect alignment between the slewing ring and the gearbox, minimizing internal losses and maximizing force transfer.
Robust Bearing Geometry: Despite weight reduction, the slewing ring's raceway and rolling element (ball or roller) design is engineered to handle the concentrated stresses from high torque output and combined external loads.
High-Quality Components: Premium bearings, hardened and ground gear teeth, and superior lubricants ensure the compact unit reliably transmits high forces without premature wear. The SP-I 0411 exemplifies this, packing substantial rotational power into a remarkably small and light package.
Precision in Motion: The Robotic Joint Slewing Drive
In the realm of robotics, especially advanced mobile platforms, collaborative robots (cobots), and automated systems requiring dexterity, slewing drives like the SP-I 0411 are increasingly vital as robotic joints. These joints demand:
Extreme Precision: Minimal backlash and high positional repeatability are non-negotiable for accurate movement and control.
High Stiffness: Resistance to deflection under load ensures stability and accuracy during operation.
Smooth Motion: Low friction and vibration are essential for seamless, jerk-free movement, critical for sensitive tasks or human interaction.
Integrated Feedback: Compatibility with or integration of encoders/resolvers for closed-loop position and velocity control.
Compactness & Lightweight: Directly impacting the robot's speed, agility, payload capacity, and energy efficiency. The SP-I 0411, designed with precision gearing, high rigidity, and minimal backlash, meets these stringent demands. Its lightweight nature allows robotic arms to be faster, carry more payload relative to their own weight, and operate longer on battery power, making it an ideal actuator for rotary joints in base rotation, shoulder, elbow, or wrist axes.
Key Features of the Lightweight Slewing Ring Gear Drive SP-I 0411
The SP-I 0411 distinguishes itself through a suite of advanced features:
Exceptional Torque-to-Weight Ratio: Delivers high output torque while minimizing system inertia and weight penalty.
Ultra-Compact Design: Minimizes the spatial footprint, freeing up valuable real estate in tightly packed machinery.
Integrated Slewing Bearing: Provides direct support for radial, axial, and moment loads, simplifying mounting and structure.
High Efficiency Gearbox: Precision-engineered gearing (often planetary or worm) minimizes energy loss and heat generation.
Low Backlash: Critical for precise positioning and repeatability in automation and robotics applications.
Robust Sealing: Integrated seals protect internal components (gears, bearings) from dust, moisture, and contaminants, ensuring long life in harsh environments.
Versatile Mounting Options: Facilitates easy integration into diverse system architectures.
Integrated Motor Compatibility: Designed for seamless coupling with various motor types (electric, hydraulic) or available as pre-assembled units.
High Rigidity: Maintains structural integrity and precision under significant operational loads.
Durability: Manufactured from high-quality materials and subjected to rigorous testing for reliable, long-term performance.
Diverse Applications: Where the SP-I 0411 Excels
The unique blend of lightweight construction, compactness, high torque, and precision makes the SP-I 0411 ideal for numerous demanding sectors:
Robotics & Automation: Rotary bases for mobile robots, collaborative robot joints, automated guided vehicle (AGV) steering modules, turntables for assembly, welding, and material handling.
Aerospace & Defense: Actuators for satellite antenna positioning, drone gimbal systems, lightweight radar platforms, hatch mechanisms, and unmanned ground vehicle (UGV) components.
Solar Tracking: Driving azimuth and elevation axes in single-axis and dual-axis solar trackers, where low weight reduces structural costs and wind loading.
Material Handling: Compact rotary actuators for conveyor diverters, indexing tables, palletizers, and lightweight crane jibs.
Medical & Rehabilitation Equipment: Precision positioning in imaging devices, patient transfer systems, and exoskeleton joints.
Construction Machinery: Lightweight slew functions in compact excavator attachments, aerial work platforms (AWPs), and specialized access equipment.
Test & Simulation Equipment: Precision rotary stages for positioning sensors, samples, or components under test.
Marine & Offshore: Actuators for antenna masts, small crane functions, and hatch controls on vessels where weight and corrosion resistance are critical.
Understanding the Price Factors of the SP-I 0411
The investment in a high-performance lightweight slewing drive like the SP-I 0411 reflects its advanced engineering and materials. Key factors influencing its price include:
Material Costs: Premium high-strength steels, specialized alloys, and advanced sealing materials are significantly more expensive than standard components.
Precision Manufacturing: Achieving the tight tolerances, complex geometries (often from topology optimization), and superior surface finishes requires advanced CNC machining, grinding, and heat treatment processes, increasing production costs.
Complexity of Design: Integrating the slewing bearing, gearbox, seals, and often motor interface into a single, optimized unit is inherently more complex than manufacturing separate components.
Quality of Components: High-precision gears (e.g., ground teeth), premium-grade slewing ring bearings, and long-life seals contribute to performance and reliability but also cost.
Gearbox Type & Ratio: Multi-stage planetary gearboxes or high-ratio worm drives cost more than simpler single-stage solutions. Higher ratios generally add complexity.
Integrated Features: Options like integrated motors, brakes, or absolute encoders add directly to the unit cost.
Customization: Modifications to standard designs (special mounts, seals, lubrication, coatings) incur additional engineering and manufacturing expenses.
Volume & Order Quantity: Economies of scale apply; larger production runs typically reduce the unit cost.
Testing & Certification: Rigorous quality control, performance testing, and obtaining industry certifications add to the overall cost but ensure reliability. While the initial cost per unit might be higher than a standard drive, the SP-I 0411's weight savings often lead to substantial downstream cost reductions in supporting structures, motors, energy consumption, and transportation.
Supplier of Lightweight Slewing Ring Gear Drive SP-I 0411
When seeking the advanced engineering and reliable performance embodied by the Lightweight Slewing Ring Gear Drive SP-I 0411, partnering with a specialized manufacturer is paramount. LYRADRIVE stands as a leading innovator and supplier in this precise field. They distinguish themselves through:
Deep Expertise: Focused specialization in the design, engineering, and manufacturing of high-performance slewing drives, particularly lightweight and compact solutions.
Advanced Engineering Capabilities: Utilizing cutting-edge design tools (like FEA and topology optimization) and in-depth material science knowledge to push the boundaries of torque density and weight reduction.
Precision Manufacturing: Operating state-of-the-art production facilities with stringent quality control processes to ensure every SP-I 0411 meets exacting specifications for performance, durability, and low backlash.
Customization Focus: Offering significant engineering support to adapt the SP-I platform or develop bespoke solutions tailored to unique application requirements beyond the standard SP-I 0411 offering.
Quality Commitment: Building drives to withstand demanding operational environments, backed by rigorous testing protocols.
Technical Support: Providing comprehensive application engineering assistance from concept through integration. For engineers and designers demanding the pinnacle of lightweight, high-torque, compact rotational motion, LYRADRIVE's SP-I 0411 represents a proven, cutting-edge solution backed by specialized manufacturing excellence. Their commitment to innovation makes them the go-to partner for overcoming the challenges of weight and space without compromising on power or precision.