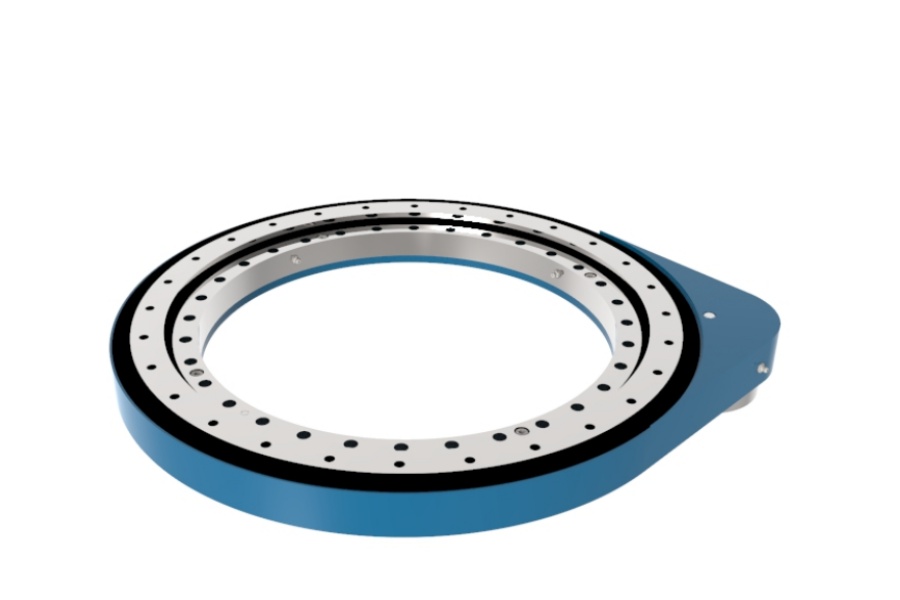
Revolutionize Motion: The SP-I 0541 Lightweight Slewing Ring Gear Drive Unleashed
What is the Lightweight Slewing Ring Gear Drive SP-I 0541?
This innovative component is an ultra-compact, high-torque solution integrating a slewing ring bearing with a precision gear drive. Engineered for scenarios where weight directly impacts performance and energy consumption, the SP-I 0541 delivers robust rotational force and precise positioning capabilities. Its unique design replaces traditional bulky assemblies, offering a significant reduction in mass—often exceeding 40%—without sacrificing load capacity or durability. It functions as the critical rotational heart in machines requiring smooth, controlled, and efficient slewing motion under substantial stress. The "SP-I 0541" designation signifies its specific size, torque rating, and optimized gear geometry within a standardized product line, ensuring reliability and interchangeability.
The Imperative of Non-Magnetic Materials
Certain high-tech environments impose a non-negotiable demand: absolute magnetic neutrality. In applications like advanced medical imaging (MRI), sensitive scientific instruments, or specialized semiconductor processes, even minute magnetic fields can cause catastrophic interference or data corruption. The SP-I 0541 addresses this critical need through the strategic use of non-magnetic materials. Key structural components, particularly the raceways and rolling elements, are meticulously crafted from high-strength, non-ferrous alloys like specific titanium grades or specialized austenitic stainless steels (e.g., AISI 316L). These materials undergo rigorous processing to ensure they retain zero magnetic permeability while meeting the stringent mechanical requirements for hardness, fatigue resistance, and dimensional stability under load. This eliminates parasitic magnetic fields, safeguarding sensitive operations.
Semiconductor Wafer Handling Drive: Precision at the Nanoscale
The semiconductor manufacturing industry presents arguably the most demanding environment for motion control components. Wafer handling robots operate within ultra-clean vacuum chambers, manipulating silicon wafers worth thousands of dollars each with nanometer-level precision at high speeds. Contamination, vibration, or positional inaccuracy are catastrophic. Here, the SP-I 0541 excels. Its lightweight construction minimizes moving mass, enabling faster acceleration/deceleration and reducing vibration that could dislodge microscopic particles. Precision-ground gearing ensures backlash-free motion for flawless positioning. Crucially, versions manufactured with non-magnetic materials and ultra-clean compatible lubricants prevent metallic particle generation and magnetic interference that could disrupt delicate fabrication processes like lithography or ion implantation. The drive’s compactness allows for denser tool designs within expensive cleanroom footprints.
Lightweight Slewing Bearing: The Foundation of Performance
The core enabling technology within the SP-I 0541 is its advanced lightweight slewing bearing. This isn't merely a scaled-down bearing; it's a re-engineered solution. Traditional slewing bearings rely heavily on thick steel sections for strength. The lightweight approach utilizes sophisticated finite element analysis (FEA) to optimize material distribution, removing metal only where stress levels permit. High-strength, low-alloy steels or advanced aluminum alloys replace standard materials. Innovative cross-section designs, such as optimized raceway profiles and strategically placed stiffening ribs, maximize structural integrity while minimizing weight. Advanced heat treatment processes ensure the retained material achieves superior hardness and fatigue life. This bearing provides the low-friction rotational platform upon which the integrated gear drive transmits high torque efficiently.
SP-I 0541: Engineering Features That Define Excellence
The Lightweight Slewing Ring Gear Drive SP-I 0541 distinguishes itself through a suite of engineered features. Its ultra-low weight-to-torque ratio is paramount, achieved via material science and structural optimization. Precision is guaranteed through ground gear teeth with minimal backlash (<1 arcmin) and high concentricity/runout tolerances. Robustness is inherent, with high static and dynamic load ratings (axial, radial, moment) and resistance to shock loads. Integrated sealing systems provide high IP ratings (IP65/IP67 standard, higher optional) for reliable operation in harsh, dusty, or washdown environments. Versatility shines with multiple mounting configurations (flange, foot, shaft options), customizable gear ratios, and lubrication options (grease, oil, or specialized vacuum/cleanroom lubricants). Options for integrated motors, encoders, or brakes streamline system design. Rigorous quality control, including 100% torque testing and traceability, ensures consistent performance.
Where Innovation Spins: Key Applications of the SP-I 0541
The unique advantages of the SP-I 0541 drive adoption across diverse sectors. In robotics, it powers articulated arms for material handling, assembly, and precision welding, where reduced weight enhances speed and payload. Within renewable energy, it enables precise pitch and yaw control in solar trackers and small wind turbines, maximizing energy capture while minimizing structural costs. Advanced medical imaging systems leverage its non-magnetic versions for precise component positioning in MRI and CT scanners. The semiconductor industry relies on it for vacuum-compatible wafer handling robots and stage positioning. Industrial automation utilizes it in rotary indexing tables, packaging machinery turntables, and CNC rotary axes. Aerospace and defense applications benefit from its lightweight precision in gimbal systems, radar platforms, and targeting mechanisms. Even specialized camera cranes and broadcast equipment utilize its smooth, vibration-free motion.
Decoding the Price: Factors Influencing SP-I 0541 Cost
Several key factors determine the investment required for the SP-I 054Material selection is fundamental; standard high-strength steel offers an economical baseline, while titanium or specialized non-magnetic alloys significantly increase cost due to material expense and complex machining. Precision level is critical; drives requiring ultra-low backlash (sub-arcminute) or extreme runout tolerances demand more meticulous manufacturing and inspection, escalating price. Customization drives costs up – unique mounting flanges, special shaft configurations, non-standard gear ratios, or integrated components (motors, brakes, encoders) require dedicated engineering and production setup. Volume plays a major role; high-volume orders benefit from economies of scale, lowering unit cost, while prototypes or small batches incur higher per-unit engineering and setup charges. Finally, certifications (e.g., ISO 9001, specific industry standards like SEMI) and rigorous testing protocols add value but also cost. The quality and reputation of the manufacturer inherently influence pricing, reflecting engineering expertise, reliability, and support.
Supplier of Lightweight Slewing Ring Gear Drive SP-I 0541
When sourcing the critical Lightweight Slewing Ring Gear Drive SP-I 0541, partnering with a leader in engineered motion solutions is paramount. LYRADRIVE stands at the forefront, renowned for its deep expertise in slewing technology and commitment to innovation. They don't just supply the SP-I 0541; they offer comprehensive engineering support. LYRADRIVE's team collaborates closely with customers to understand specific application challenges – load profiles, environmental conditions, space constraints, and performance goals. This enables them to recommend the optimal SP-I 0541 configuration or even develop tailored solutions if standard offerings require modification. Their state-of-the-art manufacturing facilities employ advanced CNC machining, precision grinding, and rigorous quality control processes, ensuring every drive meets exacting specifications for performance, durability, and reliability. Beyond the product, LYRADRIVE provides invaluable technical support, from initial design integration assistance to installation guidance and maintenance expertise. Their global logistics network ensures timely delivery, minimizing downtime. Choosing LYRADRIVE means securing not just a component, but a reliable partnership dedicated to the success of your most demanding motion control applications.
Embracing the Lightweight Revolution
The Lightweight Slewing Ring Gear Drive SP-I 0541 is more than a component; it's an enabler of next-generation machinery. By shattering the traditional trade-off between strength and weight, it unlocks new levels of efficiency, speed, and precision across robotics, clean technology, medical diagnostics, semiconductor manufacturing, and beyond. Its integration of advanced materials, precision engineering, and robust design directly translates to enhanced machine performance, reduced energy consumption, and lower operational costs. As industries relentlessly push the boundaries of what's possible, solutions like the SP-I 0541 become indispensable. Partnering with a technologically advanced supplier like LYRADRIVE ensures access to this cutting-edge capability, providing the engineering support and manufacturing excellence needed to turn innovative concepts into reliable, high-performing reality. The future of motion is lightweight, powerful, and precise – embodied in drives like the SP-I 0541.