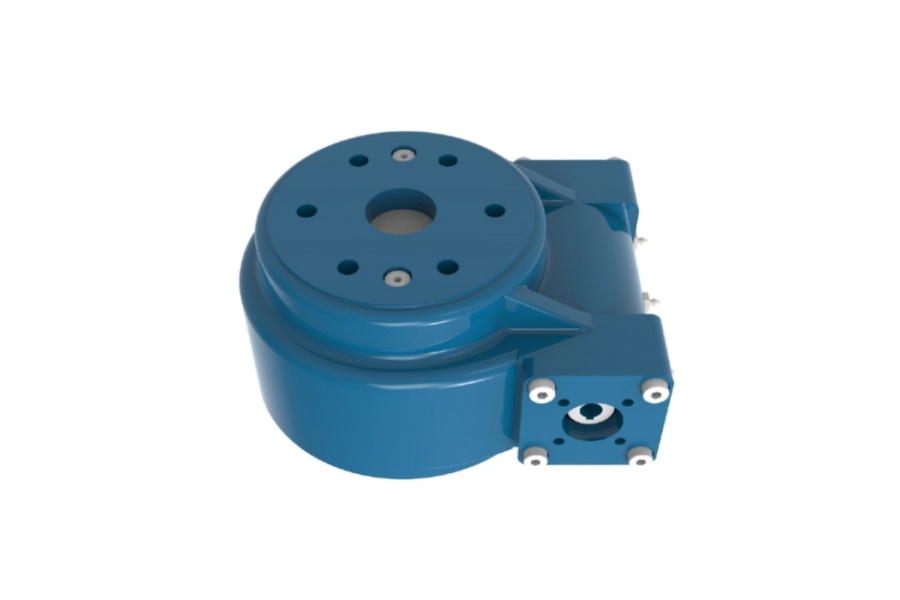
Enveloping Rotary Drive Unit SE5 Powering Precision Motion
What is the Enveloping Slewing Drive SE5?
The Enveloping Slewing Drive SE5 is a specific type of rotary actuator or slewing drive characterized by its utilization of an enveloping worm gear mechanism. Manufactured to exacting standards, the SE5 model is a compact, integrated unit housing a precision worm shaft and an enveloping worm wheel within a rigid casing, often incorporating pre-loaded bearings and sealing. This design provides a direct, high-ratio speed reduction in a single stage, delivering substantial output torque with minimal backlash and high torsional stiffness directly at the point of rotation. The "SE5" designation typically refers to a specific size or model series within a manufacturer's lineup, indicating its torque capacity, physical dimensions, and mounting interface specifications.
Enveloping Rotary Drive Principle
The core innovation lies in the "enveloping" geometry of the worm gear set. Unlike a standard cylindrical worm gear where the worm threads engage with the teeth of a spur-like gear wheel, an enveloping worm gear features a concave (hourglass-shaped) worm wheel. This concave profile partially wraps around or "envelops" the cylindrical worm. This geometry dramatically increases the number of teeth in contact simultaneously between the worm and the wheel at any given moment. While a standard worm gear might have only one or two teeth engaged, an enveloping design can have multiple teeth (often 5-10 or more) sharing the load. This fundamental characteristic yields several critical advantages:
High Torque Density: Distributing the load across multiple teeth significantly increases the torque capacity for a given unit size compared to standard worm gears or many other gear types.
Exceptional Rigidity: The multi-tooth contact creates a much stiffer connection between the input (worm) and output (wheel), minimizing angular deflection under load. This torsional stiffness is crucial for precise positioning and resisting external forces.
Low Backlash: Precision manufacturing of the enveloping profiles, combined with controlled pre-loading mechanisms within the drive unit, allows for extremely low backlash or even near-zero backlash operation. This is essential for repeatability and accuracy in automation.
Smooth Operation: The gradual engagement and disengagement of multiple teeth contribute to smoother, quieter operation with reduced vibration compared to some other high-ratio drives.
High Efficiency (for worm gears): While worm gears are generally less efficient than planetary or spur gears due to sliding friction, the enveloping design's increased contact area can lead to slightly higher efficiencies than standard single-start worm gears, especially under optimal lubrication conditions.
Robot Joint Drive Requirements
Modern robotics, particularly collaborative robots (cobots), industrial manipulators, and robotic joints for applications like welding, assembly, and material handling, impose stringent demands on their joint actuators:
High Torque in Compact Size: Joints, especially those closer to the base or handling heavy payloads, need to generate substantial torque within the very limited space constraints of the robot's arm structure.
Extreme Rigidity (Torsional Stiffness): Minimal angular deflection under load is paramount for maintaining precision positioning, path accuracy (e.g., during welding or machining), and high bandwidth control. Flexibility in the joint translates directly to inaccuracy and vibration.
Ultra-Low Backlash: Backlash, the small amount of free movement between meshing gears, causes positioning errors, vibration during direction reversals, and control instability. Near-zero backlash is critical for high-precision tasks.
High Precision & Repeatability: Joints must move to exact positions consistently, cycle after cycle, often requiring micron-level repeatability.
Reliability & Longevity: Industrial robots operate for thousands of hours; joint drives must be robust, durable, and require minimal maintenance.
Sealing & Contamination Resistance: Joints are exposed to factory environments; effective sealing against dust, debris, and sometimes coolants is essential.
Integrated Design: A compact, self-contained unit simplifies robot arm design, assembly, and maintenance.
Traditional solutions like harmonic drives (excellent precision but limited torque density and potential fatigue issues), planetary gearboxes (good efficiency but often larger for equivalent torque and can have higher backlash), or standard worm gears (compact, high ratio, but lower efficiency, rigidity, and higher backlash) each have compromises. The enveloping rotary drive principle directly addresses the critical needs of high torque density, extreme rigidity, and low backlash in a compact package.
Enveloping Slewing Drive SE5 Characteristics
The SE5 model, embodying the enveloping principle, offers a compelling set of characteristics tailored for demanding robotic and automation joints:
Unmatched Torsional Stiffness: The multi-tooth contact inherent in the enveloping design provides exceptionally high resistance to angular deflection under load, crucial for robot accuracy and dynamic performance. This stiffness often surpasses harmonic drives and significantly exceeds standard worm gears or planetary gearboxes of comparable size.
Very Low/Precision-Controlled Backlash: Precision manufacturing and assembly, often incorporating adjustable pre-loading mechanisms (like axial preload on the worm shaft), allow the SE5 to achieve and maintain ultra-low backlash levels, essential for precise positioning and smooth motion reversal.
High Torque-to-Size Ratio: The enveloping principle enables the SE5 to deliver remarkably high output torque within an extremely compact radial and axial envelope. This high torque density is ideal for space-constrained robot joints.
High Radial & Axial Load Capacity: Robust bearings integrated directly into the SE5 unit casing allow it to support significant radial and axial loads imposed by the robot arm structure and payloads, often eliminating the need for additional support bearings.
Compact, Integrated Design: The SE5 is a self-contained unit housing the gear set, bearings, seals, and often lubrication. This simplifies integration into robot joints, reducing assembly complexity and parts count.
High Overload Capacity: The robust gear teeth and multi-tooth engagement provide excellent resistance to shock loads and temporary overloads, enhancing durability in demanding applications.
Effective Sealing: Designed for industrial environments, the SE5 typically features high-quality seals (like labyrinth or radial shaft seals) protecting the precision gear set and bearings from contaminants.
Precision Ground Gears: The worm and worm wheel are usually precision ground from high-strength alloy steels (e.g., case-hardened), ensuring smooth operation, low noise, and long wear life.
High Positional Accuracy & Repeatability: The combination of low backlash, high stiffness, and precision gearing translates directly into excellent positional accuracy and repeatability for the joint.
Mounting Flexibility: Designed with standardized mounting flanges and output interfaces (e.g., splined shafts, bolt patterns) compatible with common robot joint designs and servo motors.
Enveloping Slewing Drive SE5 Applications
The unique strengths of the SE5 make it the drive solution of choice for numerous high-performance applications:
Robotic Joints (Primary Application):
Cobots (Collaborative Robots): Ideal for joints requiring high torque density and stiffness in a compact size, especially base and elbow joints of payload-carrying cobots.
Industrial Manipulators: Used in joints of welding robots, painting robots, assembly robots, and material handling robots where precision, rigidity, and reliability are paramount.
SCARA Robots: Excellent for the vertical (Z-axis) lift joint requiring high thrust load capacity and rigidity.
Delta Robots: Can be used in the central rotary joint handling significant inertial loads.
Articulated Welding Arms: Provides the necessary stiffness and precision for accurate weld seam tracking.
Precision Rotary Indexing Tables: Where high positioning accuracy, repeatability, and rigidity against machining forces are critical (e.g., CNC tool changers, inspection stations).
Pan-Tilt Units (PTUs): For surveillance, radar, laser scanning, or communication systems requiring smooth, precise, and stable positioning under wind load or motion.
Satellite Communication Antennas: Requires precise pointing accuracy and stability, often in harsh environments.
Medical and Laboratory Automation: Robotic sample handling, diagnostic equipment positioning stages requiring smooth, precise, and reliable motion.
Aerospace Test Rigs: Actuating flight control surface simulators or positioning heavy test components with high precision.
Packaging Machinery: High-speed, precise rotary motion for filling, capping, or labeling stations demanding accuracy and reliability.
Semiconductor Manufacturing Equipment: Precision stages for wafer handling and processing where nanometer-level stability is often required.
Heavy-Duty Industrial Turntables: For positioning large workpieces in manufacturing or assembly lines.
Solar Tracking Systems: For precisely orienting large solar panels or concentrators.
Factors Influencing Enveloping Slewing Drive SE5 Pricing
The cost of an Enveloping Slewing Drive SE5 is influenced by several key factors:
Precision Level & Tolerances: Achieving ultra-low backlash (e.g., <1 arcmin) and high positional accuracy requires significantly more precise machining, grinding, metrology, and assembly processes, directly impacting cost. Tighter tolerances demand higher manufacturing skill and time.
Materials and Heat Treatment: The use of high-performance alloy steels (e.g., 18CrNiMo7-6, 16MnCr5) for the worm and wheel, coupled with specialized case-hardening processes (carburizing, nitriding) and precision grinding, contributes substantially to the cost. These processes ensure the necessary surface hardness, core toughness, and wear resistance for longevity under high load.
Bearing Quality and Type: The integrated bearings (typically large cross-roller bearings or tapered roller bearings) are critical for handling loads and stiffness. High-precision, high-capacity bearings from reputable manufacturers add significant cost. The specific type and preload level required influence price.
Sealing Technology: Effective sealing against ingress of contaminants (IP ratings like IP65, IP67) using advanced labyrinth seals, specialized radial shaft seals, or even magnetic seals increases complexity and cost compared to basic seals.
Gear Quality (Grinding vs. Cutting): Precision ground gears offer superior surface finish, accuracy, and noise performance but are significantly more expensive than hobbed or cut gears. The SE5's performance relies heavily on ground gears.
Pre-loading Mechanism: Sophisticated mechanisms to apply and maintain precise axial preload on the worm shaft (critical for maintaining low backlash) add design complexity and manufacturing cost.
Customization: Modifications to standard SE5 dimensions, mounting interfaces, output shafts, sealing specifications, or lubrication ports involve engineering time and non-standard manufacturing steps, increasing the unit price.
Lubrication System: The type and complexity of the lubrication system (e.g., lifetime grease, oil bath with seals, provisions for external lubrication) affect cost. Sealed-for-life units may use higher-cost specialty greases.
Manufacturing Volume: Like most engineered components, higher production volumes generally lead to lower per-unit costs due to amortization of setup and tooling costs. Low-volume or prototype units will be more expensive.
Brand Reputation & Quality Assurance: Manufacturers with established reputations for quality, reliability, and rigorous testing (e.g., ISO 9001 certified, extensive life testing data) often command a price premium reflecting the reduced risk of failure for the end-user. Certifications and comprehensive documentation add value and cost.
Geographical Origin: Manufacturing location influences labor costs, overhead, and logistics, impacting the final price.
Supplier of Enveloping Slewing Drive SE5 series
LYRADRIVE is a recognized specialist in the design and manufacture of high-precision rotary drive solutions, including the Enveloping Slewing Drive SE5 series. Leveraging expertise in gear technology and precision engineering, LYRADRIVE focuses on delivering drives characterized by exceptional torsional rigidity, minimal backlash, high torque density, and robust construction. Their SE5 units are engineered specifically to meet the demanding requirements of modern robotics and automation, particularly in joint applications where performance, compactness, and reliability are non-negotiable. LYRADRIVE provides technical support and customization options to integrate the SE5 effectively into complex motion systems.