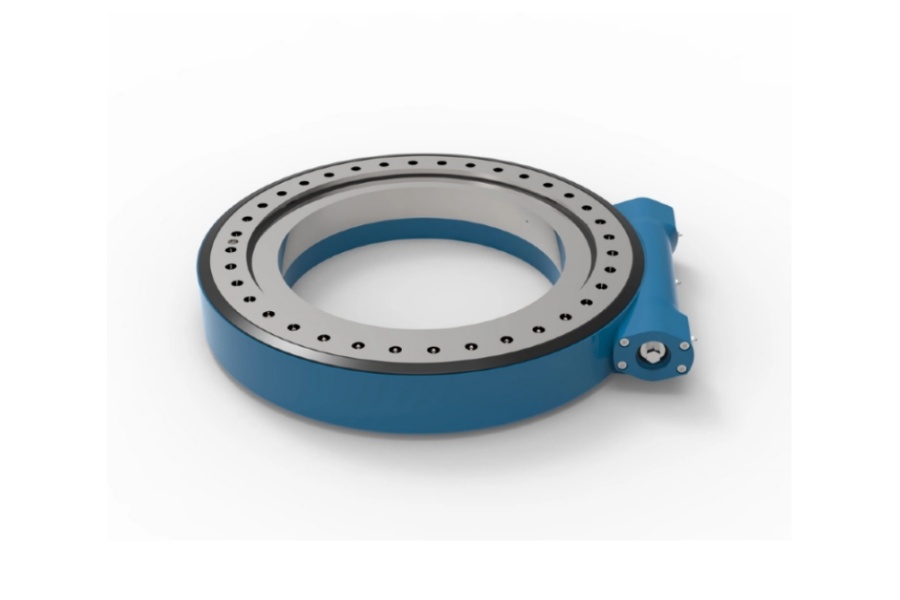
Comprehensive Guide to Worm Gear Drive WE25 Features, Applications, and Maintenance
What is Worm Gear Drive WE25
Worm Gear Drive WE25 consists of a threaded worm screw engaging with a helical gear (worm wheel), enabling compact torque transmission at right angles with inherent self-locking capability. Engineered for durability, the WE25 model features hardened steel worms and bronze alloy wheels to minimize wear, supporting load capacities up to 1,200 Nm. Its compact design suits space-constrained installations while maintaining 80-90% efficiency in power transfer.
Worm Gear Drive WE25 Common Failures and Maintenance
Premature wear arises from inadequate lubrication, misalignment, or overloading. Dust ingress accelerates abrasive damage, causing pitting on gear teeth. Overheating due to excessive friction leads to lubricant breakdown and component deformation. Self-locking failure occurs with improper backlash adjustment.
Maintenance protocols:
Lubrication: Use ISO VG 320 synthetic oil; replenish every 2,000 operational hours.
Alignment Checks: Verify perpendicularity monthly with laser tools (tolerance: ±0.05mm).
Load Monitoring: Install torque sensors to prevent exceeding 1,200 Nm dynamic limits.
Seal Inspections: Replace lip seals biannually to block contaminants.
Adhering to these steps extends service life beyond 15,000 hours.
Worm Gear Drive WE25 Technical Parameters
Ratio Range: 5:1 to 100:1 (standard), customizable to 300:1
Efficiency: 85% at 20:1 ratio; decreases to 60% for 100:1 configurations
Torque Capacity: 800–1,200 Nm (input-dependent)
Backlash: < 20 arc-min (adjustable via shim kits)
Operating Temp: -20°C to +120°C
IP Rating: IP65 (standard); IP68 optional
Mounting: Foot, flange, or shaft configurations
Characteristics of Worm Gear Drive WE25
Four key attributes define this system:
Silent Operation: Helical tooth profiling reduces noise to < 60 dB.
Vibration Damping: Bronze wheel material absorbs shock loads.
Zero Backdrive: Self-locking prevents reverse rotation under static loads.
Corrosion Resistance: Nickel-plated housings withstand humid/chemical environments.
These traits enable deployment in precision automation, where positional accuracy (±0.1°) is critical.
Applications of Worm Gear Drive WE25
Conveyor Systems: Drives heavy-material handling belts in mining, withstanding dust/impact.
Robotics: Powers joint actuators in assembly robots requiring exact angular control.
Medical Imaging: Adjusts CT/MRI scanner components silently and precisely.
HVAC: Operates damper valves in commercial ventilation, leveraging corrosion resistance.
Stage Machinery: Rotates theatrical platforms reliably with smooth torque delivery.
Factors Affecting the Price of Worm Gear Drive WE25
Cost variations (typically $500–$5,000/unit) stem from:
Material Grades: Aerospace-grade bronze alloys increase cost 30% vs. standard bronze.
Ratio Complexity: Ratios > 100:1 require specialized machining (+15–25% price).
Customization: IP68 sealing or anti-backlash gears add 10–40% to base pricing.
Order Volume: Bulk purchases (50+ units) reduce per-unit costs by 20%.
Certifications: ISO 9001/CE compliance adds 5–10% but streamlines integration.
Regional import duties and raw material fluctuations (e.g., copper prices) further impact final quotes.
Supplier of Worm Gear Drive WE25
LYRADRIVE manufactures industrial gear systems with ISO-certified facilities across Europe and Asia. Offering 12-year expertise in worm gear production, they provide WE25 units with 24-month warranties, global technical support, and rapid prototyping for custom configurations. Their digital platform enables real-time order tracking and CAD downloads for seamless integration planning.
This guide details critical aspects of Worm Gear Drive WE25, from failure prevention to procurement considerations. Proper maintenance ensures optimal performance in demanding sectors like robotics and energy, while technical adaptability supports evolving industrial requirements. For specialized applications, consult engineers to align specifications with operational demands.