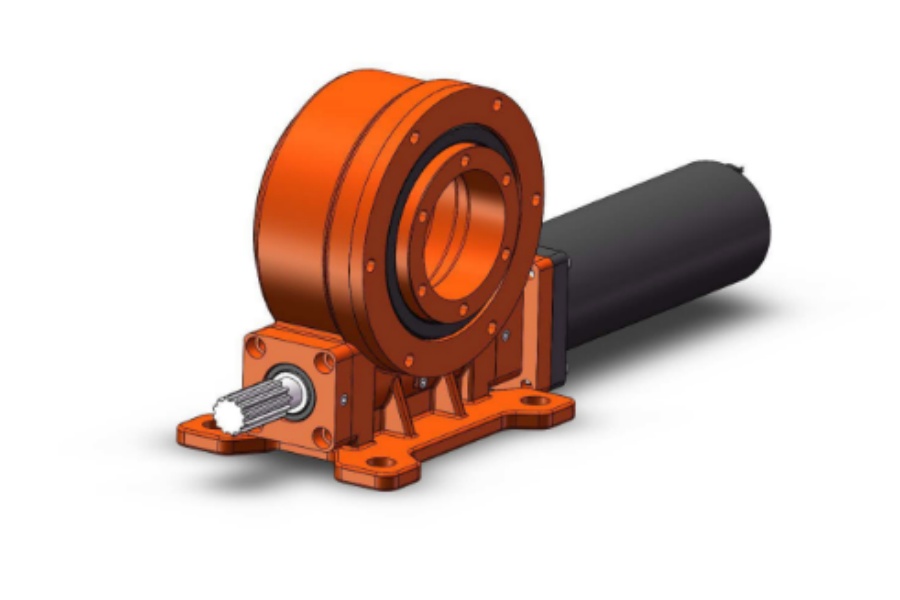
Worm Gear Slew Drives Precision and Power in Motion Systems
In the intricate world of mechanical motion control, few components strike the balance between raw power and meticulous accuracy as effectively as the worm gear slew drive. This compact yet formidable device serves as the backbone for machinery requiring precise rotational movement under heavy loads, from solar trackers aligning panels to the sun to construction cranes lifting massive payloads. As industries increasingly demand automation, energy efficiency, and reliability, the evolution of worm gear slew drives has become a linchpin for innovation, enabling smarter and more sustainable operations across sectors that depend on controlled, high-torque rotation.
What Is a Worm Gear Slew Drive
A worm gear slew drive is a specialized mechanical system designed to deliver controlled rotational motion through the interaction of a worm gear and a worm wheel. The worm gear, resembling a threaded shaft, meshes with the teeth of the worm wheel, which is typically mounted perpendicular to the worm. This configuration allows the drive to convert high-speed, low-torque input from a motor into low-speed, high-torque output, ideal for applications requiring precise positioning and substantial load-bearing capacity. The system often integrates a slewing bearing to handle axial, radial, and moment loads, while seals and lubrication systems protect internal components from contaminants and wear.
The uniqueness of worm gear slew drives lies in their self-locking capability, which prevents backdriving—ensuring that the load remains stationary when the drive is not actively powered. This feature is indispensable in scenarios like satellite antennas maintaining alignment or medical imaging equipment holding positions during scans. Additionally, their compact design allows installation in space-constrained environments without sacrificing performance. Industries such as renewable energy rely on these drives to adjust solar panels or wind turbine nacelles with millimeter accuracy, while material handling systems use them to rotate conveyor arms smoothly under heavy loads. By combining torque amplification with positional precision, worm gear slew drives address the dual challenges of power and control in modern machinery.
Global Innovations Driving Worm Gear Slew Drive Advancements
Precision Engineering and Material Breakthroughs
Countries with a legacy in precision manufacturing, such as Germany, Switzerland, and Japan, continue to set benchmarks in worm gear slew drive technology. German engineers, for instance, employ grinding processes with sub-micron accuracy to produce worm gears with near-zero backlash, minimizing energy loss and ensuring consistent torque transmission. Innovations in surface hardening techniques, such as induction hardening and nitriding, enhance gear durability, enabling these drives to withstand millions of cycles in harsh environments like mining or offshore installations.
The aerospace sector exemplifies cutting-edge applications, where worm gear slew drives are used in satellite deployment mechanisms. These units incorporate lightweight titanium alloys and vacuum-compatible lubricants to function reliably in space’s extreme temperatures and radiation. Similarly, the robotics industry benefits from ultra-compact drives with integrated encoders that provide real-time feedback for closed-loop control, enabling robotic arms to perform delicate assembly tasks with repeatable precision. Such advancements are supported by advanced simulation tools like finite element analysis (FEA), which optimize gear tooth profiles for minimal wear and maximum load distribution.
Emerging Markets Bridging the Technology Gap
While established players dominate high-precision markets, manufacturers in rapidly industrializing regions are leveraging automation and digital tools to enhance their competitiveness. By adopting CNC machining centers and AI-powered inspection systems, emerging producers achieve tighter tolerances and faster production cycles. For example, drives manufactured in these regions now feature improved sealing solutions that resist dust and moisture, making them suitable for agricultural machinery or outdoor solar installations.
However, challenges persist in mastering high-efficiency gear geometries and advanced thermal management. Global leaders often utilize proprietary software to design worm gears with optimized helix angles, reducing friction and heat generation. In contrast, manufacturers in developing markets may rely on standardized designs, limiting their ability to compete in applications requiring custom thermal dissipation solutions, such as high-speed industrial mixers or continuously operating conveyor systems. Additionally, access to high-performance polymers for seals and specialized lubricants remains uneven, affecting drive longevity in corrosive environments.
Addressing Challenges in Worm Gear Slew Drive Development
The technological divide centers on three key areas: material science, manufacturing precision, and smart integration. High-end drives from leading markets often use case-hardened steels and composite-bearing cages, which reduce weight while maintaining strength. In contrast, reliance on conventional materials in some regions can lead to premature wear in high-cycle applications, such as automated warehouse rotators or amusement park ride mechanisms.
Collaborative efforts between academia and industry aim to close this gap. Research into additive manufacturing allows the production of worm gears with internal cooling channels, a breakthrough for applications requiring continuous operation under high thermal stress. Another focus is embedded IoT sensors, which monitor parameters like vibration, temperature, and lubrication levels. These sensors transmit data to predictive maintenance platforms, enabling operators to schedule repairs before failures disrupt operations—a critical feature for industries like energy production, where downtime costs millions per hour. Training programs focused on digital twin technology further empower engineers to simulate drive performance under varying loads, accelerating design optimization.
The Future of Worm Gear Slew Drives Intelligence and Sustainability
The next generation of worm gear slew drives will prioritize energy efficiency, modular adaptability, and eco-conscious design. Engineers are experimenting with magnetic gear hybrids that replace physical meshing with magnetic fields, eliminating friction and reducing maintenance needs. Sustainability initiatives are driving the adoption of biodegradable lubricants and recyclable aluminum housings, aligning with global efforts to minimize industrial waste.
In smart industrial ecosystems, these drives will act as intelligent nodes within IoT networks. For instance, a solar farm could use real-time data from slew drives to adjust panel angles based on cloud cover predictions, maximizing energy harvest while minimizing mechanical wear. Autonomous construction equipment might leverage drive-generated torque metrics to dynamically redistribute loads, enhancing safety and operational efficiency. Such innovations align with Industry 4.0’s vision of interconnected, self-optimizing machinery.
Worm gear slew drives supplier
Worm gear slew drives exemplify the synergy between mechanical ingenuity and technological progress. As industries push toward automation and sustainability, these components will remain vital in applications demanding both brute force and delicate control. While technological pioneers continue to refine materials and digital integration, emerging markets demonstrate that strategic innovation and collaboration can narrow development gaps. The future of worm gear slew drives lies not just in greater strength or precision but in their evolution into intelligent, adaptive systems that drive the next wave of industrial transformation. For engineers and industries alike, embracing these trends will be key to thriving in an era where efficiency and sustainability define success.
LYRA Drive is a professional slewing bearings ,slew drive and gears manufacturer provides customized slew bearing, drive and gears.For application-specific engineering solutions, contact LYRA to discuss technical specifications and implementation strategies.