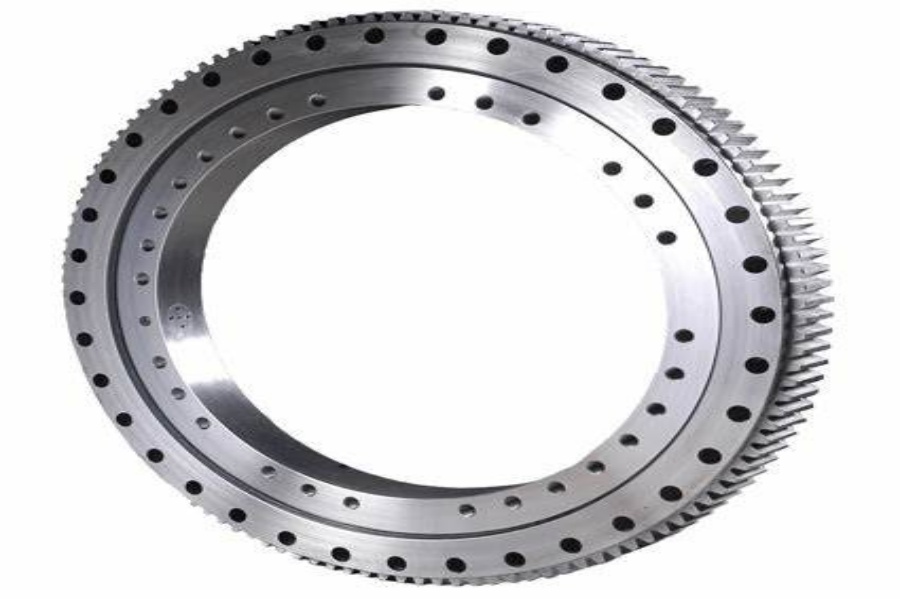
Slewing Bearings Powering Modern Machinery Innovations and the Path Forward
From rotating cranes shaping city skylines to wind turbines harvesting ocean winds, slewing bearings operate as the invisible pivot points powering industrial motion. These precision-engineered rings endure crushing loads and relentless rotations, enabling machinery to turn massive structures with the finesse required for millimeter-accurate operations. Their hardened steel raceways and precisely spaced rolling elements convert raw torque into controlled movement—whether aligning solar farms to track the sun’s arc or stabilizing medical scanners during life-saving diagnostics. As industries push for smarter, greener machinery, slewing bearings evolve beyond static components into integrated systems with embedded sensors and self-lubricating designs, balancing brute-force durability with the delicate demands of modern automation.
What is a Slewing Bearing
A slewing bearing, also known as a turntable bearing, is a specialized rotational component designed to support heavy axial, radial, and moment loads while enabling smooth 360-degree rotation. Unlike conventional bearings, slewing bearings are characterized by their large diameter and integrated design, which combines an outer ring, an inner ring, rolling elements (such as balls or rollers), and often gear teeth machined directly into one of the rings. The outer and inner rings are typically manufactured from high-strength alloy steel, heat-treated to withstand wear and fatigue, while the rolling elements distribute loads evenly to prevent deformation. Seals and lubrication systems are integrated to protect against contaminants and reduce friction, ensuring longevity even in harsh environments.
The significance of slewing bearings lies in their versatility and critical role across industries. In wind turbines, they facilitate the precise adjustment of blade angles to capture wind energy efficiently, a process vital for maximizing power generation. Construction cranes rely on them to rotate booms and platforms smoothly, enabling the safe lifting and placement of heavy materials. Medical imaging devices, such as CT scanners, use slewing bearings to rotate gantries with pinpoint accuracy, ensuring high-resolution diagnostics. Their ability to handle complex load combinations while maintaining rotational accuracy makes them irreplaceable in applications ranging from military radar systems to solar tracking installations.
Global Innovations in Slewing Bearing Technology
Advancements in Material Science and Engineering
Countries with longstanding expertise in precision engineering, such as Germany, Sweden, and Japan, continue to pioneer advancements in slewing bearing technology. German manufacturers, for instance, employ laser-cladding techniques to enhance the surface hardness of gear teeth, significantly reducing wear and extending operational life. Innovations in carburizing processes—a method of infusing carbon into steel surfaces—have enabled the production of bearings that resist pitting and micro-cracking under cyclic stresses, a common challenge in heavy machinery.
In the renewable energy sector, slewing bearings engineered for offshore wind turbines incorporate corrosion-resistant coatings and seawater-compatible lubricants to endure saltwater exposure and humidity. These bearings are subjected to rigorous simulations during design, using finite element analysis (FEA) to predict load distribution and identify potential weak points. Similarly, the aerospace industry leverages slewing bearings with ceramic hybrid rolling elements, which reduce weight and thermal expansion, critical for satellite deployment mechanisms and aircraft landing gear systems.
Emerging Markets Embracing Technological Leapfrogging
While traditional powerhouses dominate high-end markets, manufacturers in rapidly industrializing nations are narrowing the gap through strategic investments. By adopting automated grinding machines and AI-driven quality inspection systems, emerging producers now achieve tolerances once exclusive to premium brands. For example, slewing bearings for mining equipment produced in these regions now feature improved load ratings and sealing solutions that withstand abrasive dust and vibrations, catering to the growing demand for ruggedized components.
However, challenges persist in mastering large-diameter bearing manufacturing and integrated sensor technologies. Established players often utilize proprietary software to optimize gear tooth profiles for minimal backlash, a feature critical in robotics and precision machinery. Meanwhile, domestic manufacturers may rely on standardized designs, limiting their competitiveness in applications requiring custom configurations. Additionally, the scarcity of advanced anti-corrosion alloys in some regions hinders the production of bearings suitable for marine or chemical processing environments.
Overcoming Barriers to Global Competitiveness
The technological divide in slewing bearing production centers on three key areas: material innovation, precision manufacturing, and digital integration. High-performance bearings from leading markets often utilize vacuum-degassed steels and polymer-composite cages, which enhance fatigue resistance and reduce friction. In contrast, reliance on conventional steels in developing regions can lead to premature failure under high cyclic loads, particularly in applications like steel mill cranes or tunnel boring machines.
Efforts to bridge this gap are gaining momentum through partnerships between academic institutions and manufacturers. Research initiatives focus on additive manufacturing for producing custom bearing rings with internal cooling channels, a breakthrough that could revolutionize thermal management in high-speed applications. Another promising area is the development of smart slewing bearings equipped with embedded sensors that monitor vibration, temperature, and load distribution in real time. These sensors transmit data to predictive maintenance platforms, enabling operators to address wear before catastrophic failures occur, a feature increasingly demanded by industries prioritizing uptime and safety.
The Future of Slewing Bearings Intelligence and Sustainability
The next generation of slewing bearings will emphasize energy efficiency, modular design, and seamless connectivity. Engineers are exploring magnetic bearing hybrids that reduce mechanical contact, slashing friction losses and eliminating the need for traditional lubrication. Sustainability is also driving the adoption of bio-degradable greases and recyclable material composites, aligning with global initiatives to reduce the environmental footprint of industrial components.
In smart manufacturing ecosystems, slewing bearings will serve as data hubs, integrating with IoT platforms to optimize machinery performance. For instance, a wind farm could leverage real-time data from bearings to adjust turbine alignment based on predictive weather models, enhancing energy output while minimizing mechanical stress. Similarly, autonomous construction equipment might use bearing-generated data to recalibrate load distribution dynamically, improving safety and operational efficiency.
Slew drives supplier
Slewing bearings exemplify the synergy between mechanical ingenuity and technological progress. As industries evolve toward automation and sustainability, these components will continue to underpin innovations that demand both brute strength and delicate precision. While established leaders set the pace with cutting-edge materials and digital integration, emerging markets demonstrate that rapid advancement is achievable through targeted innovation and collaboration. The future of slewing bearings lies not only in their ability to bear heavier loads or rotate faster but in their capacity to become intelligent, adaptive systems that drive the next era of industrial transformation. For businesses and engineers alike, embracing these trends will be key to thriving in a world where efficiency and sustainability are no longer optional—they are imperative.
LYRA Drive is a professional slewing bearings ,slew drive and gears manufacturer provides customized slew bearing, drive and gears.For application-specific engineering solutions, contact LYRA to discuss technical specifications and implementation strategies.