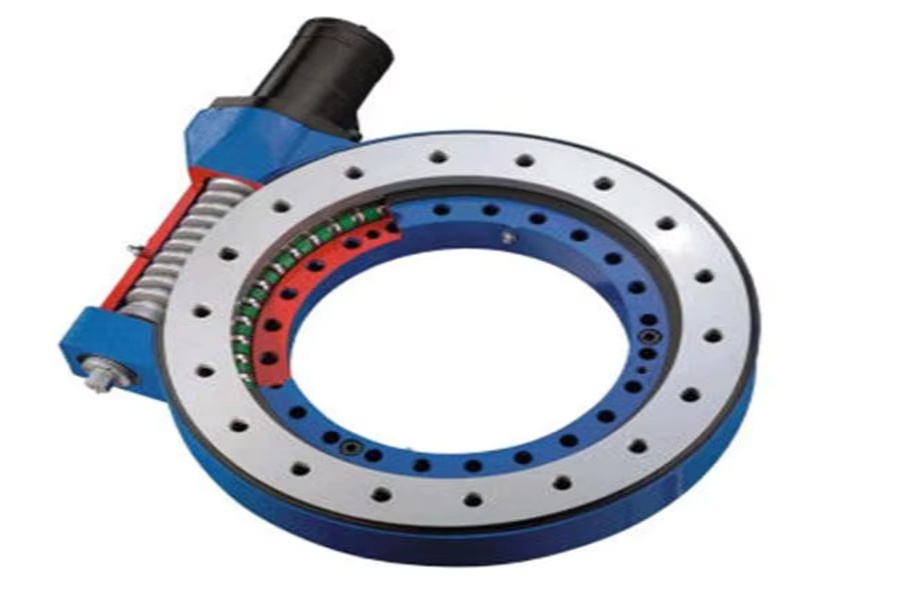
Pump Truck Slewing Drive The Precision Core of Mobile Concrete Placement
When concrete pumps snake their booms across skyscraper skeletons or bridge frameworks, the hidden choreography of precise material placement relies on pump truck slewing drives – rotational maestros converting hydraulic power into millimeter-accurate concrete flow control. These gear-driven systems endure a brutal cocktail of vibrating slurry lines, abrasive cement dust, and unpredictable job site terrain while maintaining smooth 360° articulation. Their helical teeth, hardened through cryogenic treatment, bite through torque spikes caused by sudden aggregate jams, while adaptive sealing systems purge concrete particulates before they compromise critical components. Modern iterations now integrate AI-assisted pressure modulation that anticipates boom whip during high-rise pours, automatically adjusting fluid dynamics to maintain placement accuracy as pump lines snake upward through 60-story rebar forests. This transformation from brute-force rotators to intelligent material-flow regulators redefines concrete placement efficiency in projects where schedule delays cost thousands per minute.What is a Pump Truck Slewing Drive
A Pump Truck Slewing Drive constitutes an integrated power transmission system designed to convert hydraulic energy into controlled rotational movement for concrete distribution booms. Built around hardened alloy steel gears and multi-stage planetary gearboxes, these drives support axial loads exceeding 250 kN while maintaining angular positioning accuracy within 0.5 degrees during continuous operation. Modern designs incorporate wear-compensation mechanisms and sealed lubrication systems that maintain optimal gear meshing forces despite constant exposure to concrete dust and vibration. From urban high-rise projects requiring precise overhead placement to rural infrastructure sites operating on uneven terrain, these systems ensure smooth boom articulation across thousands of pumping cycles.
Engineering Solutions for Harsh Environments
The operational reliability of Pump Truck Slewing Drives stems from targeted engineering approaches addressing concrete pumping challenges. Consider a bridge deck pouring operation where boom positioning requires millimeter precision despite constant vibration from concrete flow. The slewing drive in such applications employs shock-absorbing gear mounts and real-time pressure monitoring that automatically adjusts hydraulic flow to compensate for sudden load changes. Sealed bearing assemblies with triple-lip seals prevent contamination from cement particles, while heated grease reservoirs maintain lubrication viscosity in sub-zero temperatures during winter construction projects. Advanced models feature automatic backlash adjustment systems that preserve gear tooth engagement as components wear, ensuring consistent performance throughout the drive’s service life.
Critical Performance Attributes
Pump Truck Slewing Drives deliver essential functionality through three core engineering advancements:
Dynamic Load Management
Adaptive pressure control systems modulate hydraulic output based on real-time boom angle and concrete flow rate data, preventing gear slippage during critical vertical pours. This technology proved vital in skyscraper construction where boom extensions exceeding 60 meters require precise torque adjustments to maintain placement accuracy.
Environmental Durability
Coastal operation variants utilize marine-grade coatings and corrosion-resistant alloys to withstand salt spray exposure, while desert-ready models employ sand expulsion vanes and thermal-reflective surfaces that prevent abrasive particle ingress in dusty conditions.
Safety System Integration
Dual-circuit braking mechanisms engage within milliseconds of operator commands or system overload detection, while integrated inclination sensors disable rotation when truck stabilization exceeds safe operational limits.
Sector-Specific Applications
The versatility of Pump Truck Slewing Drives becomes evident through their specialized implementations:
High-Rise Construction:Tower-grade pumps utilize ultra-precise drives with laser-guided positioning systems that enable concrete placement accuracy within 2 cm at 200-meter heights, compensating for building sway and wind loads.
Tunnel Engineering:Underground boring machine support pumps employ explosion-proof drives with enhanced cooling systems that maintain functionality in high-humidity, confined space environments.
Disaster Recovery:Rapid-deployment concrete pumps feature drives with emergency manual override systems, allowing critical infrastructure repairs when primary power systems fail during natural disasters.
Quantifiable Performance Improvements
Technological advancements in slewing drive design yield measurable operational benefits:
Positioning Accuracy:Gyro-stabilized control systems now achieve 0.3-degree angular consistency during continuous pumping operations, enabling precise concrete placement around complex rebar configurations.
Maintenance Reduction:Diamond-like carbon gear coatings extended service intervals from 500 to 5,000 operational hours in commercial fleet applications through enhanced wear resistance and reduced friction.
Energy Efficiency:Regenerative hydraulic systems recover 30% of rotational energy during boom retraction, reducing fuel consumption by 15% in typical pumping operations.
Implementation Challenges and Solutions
Optimizing Pump Truck Slewing Drive performance requires addressing industry-specific challenges:
Abrasive Contamination:Concrete dust infiltration caused premature bearing failures until the development of positive-pressure seal systems that actively expel particulate matter from critical components.
Thermal Stress:Frequent temperature cycling between pumping operations and idle periods led to seal degradation until the introduction of phase-stable elastomers with 200% improved thermal tolerance.
Vibration Fatigue:Constant material flow vibrations accelerated component wear until manufacturers implemented tuned mass dampers that reduce harmonic vibrations by 70% in operational conditions.
Emerging Technological Innovations
Cutting-edge developments are enhancing concrete pump capabilities:
Automatic Boom Positioning:Machine vision systems integrated with drive controls now enable automated concrete placement following pre-programmed building information models, currently being tested in modular construction applications.
Predictive Wear Monitoring:Embedded acoustic sensors detect early-stage gear tooth degradation through spectral analysis, enabling proactive maintenance scheduling six months before traditional inspection methods identify issues.
Hybrid Power Integration:Electric-hydraulic drive systems allow silent operation in urban night work zones while maintaining full pumping capacity through battery-stored energy reserves.
Pump Truck Slewing Drive supplier
As construction methodologies advance and project complexity increases, Pump Truck Slewing Drives evolve from simple rotation mechanisms into intelligent material placement systems. Their ability to combine mechanical robustness with precision control ensures mobile concrete pumps will meet future construction challenges while maintaining the accuracy and reliability required for modern building techniques. Through continuous innovation in materials science and adaptive control technologies, these critical components remain essential partners in shaping the built environment.
LYRA Drive is a professional slewing bearings ,slew drive and gears manufacturer provides customized slew bearing, drive and gears.For application-specific engineering solutions, contact LYRA to discuss technical specifications and implementation strategies.