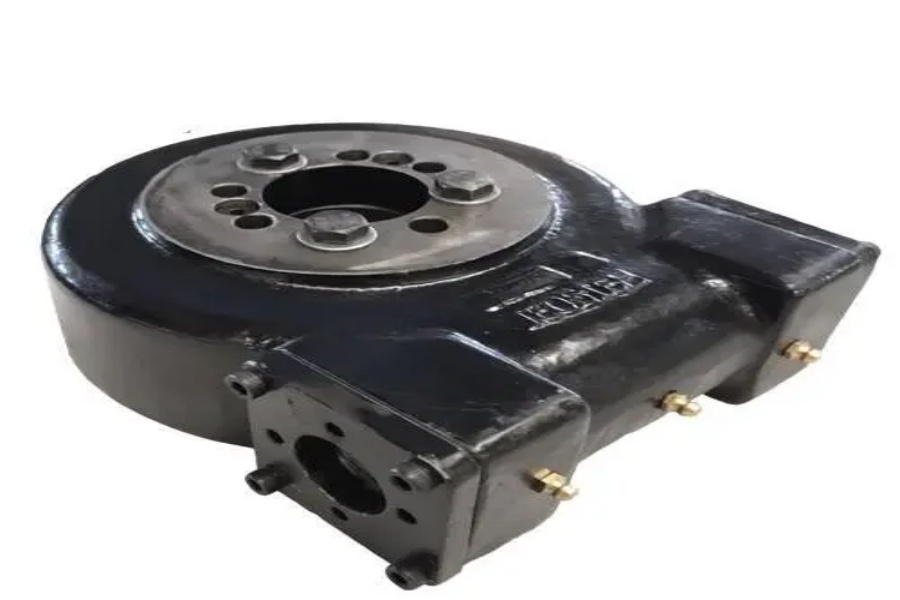
Truck Crane Slewing Drive The Power Behind Precision Lifting Operations
When construction cranes swing steel beams over crowded job sites or recovery teams hoist wrecked vehicles from ravines, the unseen heroism lies in the truck crane's rotational heart—slewing drives that transform hydraulic power into precision movement. These gear-driven systems act as dynamic stabilizers, allowing operators to pivot multi-ton loads within centimeter accuracy while compensating for ground instability and sudden weight shifts. Their hardened helical teeth and adaptive braking mechanisms endure decade-spanning abuse from desert dust storms to Arctic ice buildup, maintaining fluid rotation control even when shock loads from dropped materials threaten to strip conventional gears. Modern units now integrate load-sensing algorithms that automatically adjust torque distribution, preventing dangerous sway during high-wind lifts while preserving delicate cargo integrity. This evolution from simple rotation devices to intelligent motion managers redefines mobile crane capabilities in industries where lifting precision directly impacts project safety and profitability.
What is a Truck Crane Slewing Drive
A Truck Crane Slewing Drive represents an integrated mechanical-electrical system designed to convert hydraulic or electric power into controlled rotational motion under extreme load conditions. Constructed around hardened steel gear rings and multi-stage planetary gearboxes, these drives support combined axial and radial forces exceeding 500 kN while maintaining angular accuracy within 0.3 degrees. Modern designs incorporate fail-safe braking mechanisms and absolute position encoders that provide real-time feedback to crane operators, ensuring precise load placement even during wind-induced platform oscillations. From urban construction sites requiring compact electric drives to offshore installations demanding corrosion-resistant hydraulic systems, these units adapt to diverse operational requirements while delivering consistent performance across thousands of lifting cycles.
Engineering for Demanding Applications
The operational reliability of Truck Crane Slewing Drives stems from targeted engineering solutions addressing unique mobile crane challenges. Consider a port container crane operating in salt-laden coastal environments where corrosion threatens conventional components. The slewing drive in such applications employs marine-grade aluminum-bronze gear alloys with hydrophobic grease formulations that repel moisture while maintaining lubrication efficiency. Integrated torque-limiting sensors prevent gear tooth damage during sudden load shifts caused by swinging containers, while redundant sealing systems block abrasive salt particles from entering critical gear meshes. Mountainous terrain operations utilize drives with inclination compensation algorithms that automatically adjust lubrication flow rates when working on steep gradients, maintaining optimal gear contact pressures regardless of chassis orientation.
Critical Performance Attributes
Truck Crane Slewing Drives deliver operational excellence through three core engineering achievements refined through real-world applications:
Dynamic Load Adaptation
Real-time pressure monitoring systems adjust hydraulic flow rates proportionally to load weight variations, preventing gear slippage during critical lifting operations. This technology proved vital in bridge girder installations where asymmetric loads require continuous torque adjustments to maintain rotational stability.
Environmental Resilience
Arctic-certified units maintain functionality at -40°C through heated lubrication reservoirs and cold-tolerant seal compounds, while desert-operating variants employ thermal-reflective coatings and particle expulsion vanes that clear sand from critical components during frequent dust storms.
Safety System Integration
Dual-circuit braking systems with independent power sources enable immediate rotation cessation during emergencies, while integrated load moment indicators prevent operation when crane configuration exceeds safe working limits.
Industry-Specific Implementations
The adaptability of Truck Crane Slewing Drives becomes evident through their specialized applications across sectors:
Infrastructure Development:Bridge construction cranes utilize ultra-precise drives with anti-backlash gearing, enabling millimeter-accurate placement of concrete segments during cantilever erection processes at heights exceeding 200 meters.
Energy Sector Logistics:Wind turbine installation cranes incorporate intelligent drives that automatically counter blade oscillation during hoisting operations, using predictive algorithms to adjust rotation speed based on real-time wind speed data.
Disaster Response:Emergency recovery cranes employ rapid-response hydraulic drives capable of achieving full operational torque within 3 seconds, featuring heat-resistant seals that maintain functionality in post-fire environments with ambient temperatures surpassing 120°C.
Quantifiable Performance Enhancements
Technological advancements in slewing drive design translate into measurable operational benefits:
Positioning Accuracy:Laser-calibrated encoder systems achieve 0.2-degree angular repeatability across 15,000 operational cycles, enabling precise repetitive positioning for steel beam placement in high-rise construction projects.
Maintenance Optimization:Wear-resistant gear coatings with diamond-like carbon treatments extend service intervals from 1,000 to 10,000 operational hours in port logistics applications, reducing downtime by 60% annually.
Energy Efficiency:Regenerative hydraulic systems recover 35% of kinetic energy during boom lowering operations, decreasing fuel consumption by 18% in typical mobile crane applications.
Implementation Challenges and Solutions
Optimizing Truck Crane Slewing Drive performance requires addressing common operational hurdles:
Thermal Expansion Effects:Frequent temperature swings in tropical regions caused gear mesh misalignment until the introduction of thermal compensation spacers that automatically adjust gear clearances based on real-time temperature readings.
Vibration-Induced Fatigue:Prolonged operation on uneven surfaces accelerated component wear until manufacturers developed active damping systems that neutralize harmonic vibrations before they reach gear assemblies.
Cyclic Load Stress:High-frequency load cycling in urban construction applications led to premature failures until the adoption of gradient-hardened gear teeth with residual compressive stress profiles that improve fatigue resistance by 250%.
Emerging Technological Innovations
Cutting-edge developments are reshaping Truck Crane Slewing Drive capabilities:
Autonomous Load Positioning:Machine learning-assisted drives now enable automated load tracking and placement using LiDAR-based spatial mapping, currently undergoing field tests in prefabricated construction material handling applications.
Energy Recovery Systems:Hybrid hydraulic-electric designs capture and store rotational energy in supercapacitor arrays, providing auxiliary power for onboard systems and reducing engine idling time by 40%.
Predictive Maintenance Integration:Embedded vibration spectrum analyzers detect early-stage gear tooth wear patterns six months before traditional inspection methods, enabling proactive component replacement during scheduled maintenance periods.
Truck Crane Slewing Drive supplier
As global infrastructure demands escalate and safety regulations intensify, Truck Crane Slewing Drives evolve from basic rotation mechanisms into intelligent load management systems. Their ability to combine mechanical robustness with advanced control technologies ensures mobile cranes will meet future lifting challenges while maintaining the precision and reliability required for critical material handling operations. Through continuous innovation in materials science and smart system integration, these components remain indispensable partners in advancing lifting efficiency and worksite safety across industries.
LYRA Drive is a professional slewing bearings ,slew drive and gears manufacturer provides customized slew bearing, drive and gears.For application-specific engineering solutions, contact LYRA to discuss technical specifications and implementation strategies.