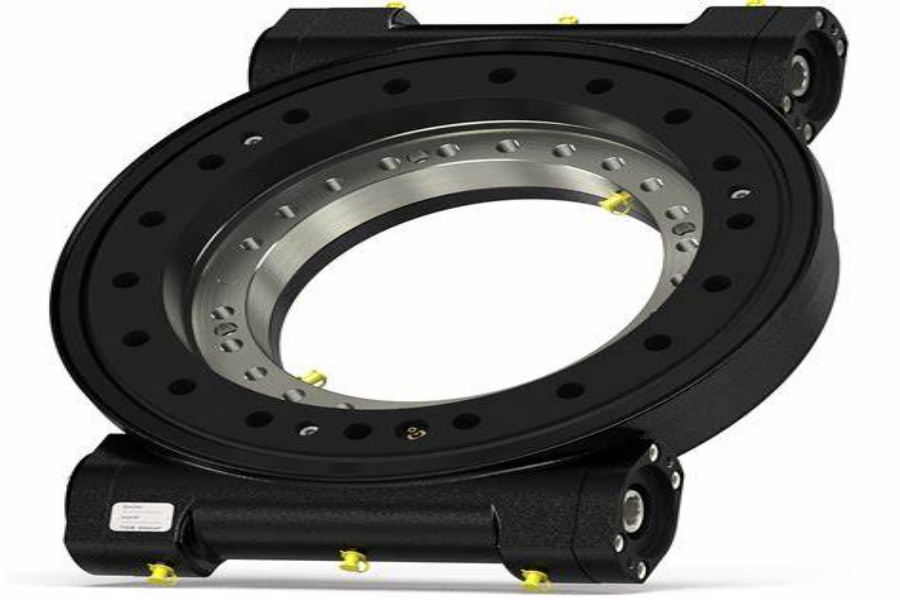
Aerial Work Vehicle Slew Drive Precision Rotation for Elevated Operations
When maintenance crews balance thirty stories above city streets or utility teams repair storm-damaged power lines in gale-force winds, aerial work platform slew drives become the mechanical anchors keeping operations steady. These compact rotation systems convert hydraulic muscle into controlled movement, enabling basket operators to position tools and personnel within millimeter precision despite swaying cables and shifting loads. Their hardened gears and adaptive braking systems counterbalance nature's unpredictability - compensating for sudden gusts that threaten stability while maintaining smooth articulation across thousands of elevation cycles. Modern designs now integrate collision avoidance sensors and automatic leveling features, transforming what were once passive mechanical components into active safety guardians that anticipate risks before human operators react. This evolution from simple rotation devices to intelligent motion control hubs redefines what's possible in vertical workspaces where equipment reliability directly determines worker safety and project viability.What is an Aerial Work Vehicle Slew Drive
An Aerial Work Vehicle Slew Drive constitutes an integrated rotational system combining a high-torque electric or hydraulic motor with precision gear reduction and robust bearing assemblies. Designed around hardened steel gear rings and multi-stage planetary gearboxes, these units provide smooth rotation while supporting combined axial and radial loads from extended booms and personnel baskets. Modern iterations incorporate fail-safe braking systems and position encoders that maintain angular accuracy within 0.1 degrees even under dynamic wind loading. From telecom tower maintenance platforms operating at 150-meter heights to fire rescue vehicles positioning water cannons on unstable terrain, these drives translate operator commands into precise movements while compensating for real-time environmental challenges.
Engineering for Elevated Challenges
The operational reliability of Aerial Work Vehicle Slew Drives stems from multi-layered engineering solutions addressing unique aerial platform requirements. Consider a wind turbine maintenance platform operating in offshore conditions where salt spray and gusting winds threaten conventional systems. Here, the slew drive employs marine-grade stainless steel gearing with hydrophobic grease formulations that repel moisture while maintaining lubrication integrity. Integrated torque-limiting couplings prevent gear tooth damage during sudden load shifts caused by unexpected wind gusts, while redundant position sensors ensure continuous feedback even if primary systems fail. Urban applications utilize drives with electromagnetic interference shielding to maintain precision near high-voltage power lines, incorporating thermal management systems that prevent overheating during prolonged operation in direct sunlight.
Core Performance Attributes
Aerial Work Vehicle Slew Drives deliver critical value through three pillars of engineering excellence refined through real-world applications:
Dynamic Load Compensation
Advanced models utilize real-time load monitoring through strain gauge arrays that adjust gear meshing forces automatically as platform loads shift during operation. This technology proved vital in bridge inspection vehicles where workers frequently move heavy testing equipment across the platform, maintaining stability despite constantly changing weight distributions.
Environmental Resistance
Arctic-grade units maintain functionality at minus 40 degrees Celsius through heated lubrication reservoirs and cold-tolerant seal compounds, while desert-operating variants employ solar-reflective coatings and sand expulsion vanes that clear abrasive particles from critical components.
Safety System Integration
Dual-circuit braking systems with independent power sources ensure immediate rotation cessation during emergencies, while integrated inclination sensors disable operation when platform leveling exceeds safe thresholds.
Sector-Specific Adaptations
The versatility of Aerial Work Vehicle Slew Drives becomes evident through their specialized implementations:
Urban Infrastructure Maintenance:High-rise window cleaning platforms utilize ultra-quiet electric slew drives with anti-vibration mounts, enabling precise positioning near occupied office spaces without disturbing building occupants through noise pollution.
Emergency Response Systems:Fire rescue vehicles employ explosion-proof hydraulic slew drives capable of operating in flammable vapor environments, featuring rapid deployment mechanisms that achieve full torque output within seconds of activation.
Renewable Energy Servicing:Wind farm maintenance vehicles incorporate slew drives with gust response algorithms that automatically counter sudden wind shifts, allowing technicians to work safely during variable weather conditions common at turbine nacelle heights.
Measurable Operational Improvements
Technological advancements in slew drive design translate directly into quantifiable performance gains:
Positioning Accuracy:Laser-calibrated encoders and backlash elimination systems now achieve angular positioning repeatability within 0.05 degrees, enabling precise alignment of heavy equipment during cell tower antenna installations.
Duty Cycle Expansion:Hardened gear tooth profiles with diamond-like carbon coatings extend maintenance intervals from 500 to 5,000 operating hours in municipal utility fleets, dramatically reducing vehicle downtime.
Energy Efficiency:Regenerative hydraulic systems in modern units recover up to 30% of rotational energy during platform lowering operations, significantly reducing overall power consumption during extended work shifts.
Implementation Considerations
Successful deployment of Aerial Work Vehicle Slew Drives requires addressing common operational challenges:
Thermal Management:Early adopters in tropical regions encountered fluid breakdown in hydraulic systems until implementing phase-change cooling modules that maintain optimal oil temperatures despite ambient heat.
Vibration-Induced Wear:Routine operation on uneven terrain accelerated component wear until the introduction of active damping systems that counteract chassis vibrations before they reach gear assemblies.
Cyclic Stress Fatigue:Frequent start-stop cycles in urban applications led to premature failures until manufacturers developed gradient-hardened gear teeth that develop compressive stress layers under operational loads.
Emerging Technological Frontiers
Innovative developments promise to redefine aerial platform capabilities:
Autonomous Positioning Systems:Prototype drives integrating LiDAR and machine vision enable automated platform alignment with work surfaces, currently undergoing trials in high-voltage line maintenance applications.
Energy-Independent Operation:Solar-assisted hydraulic systems with battery buffers allow extended operation in remote areas, eliminating dependence on vehicle power systems during critical tasks.
Predictive Health Monitoring:Embedded acoustic emission sensors detect early-stage gear pitting and lubrication degradation, transmitting maintenance alerts through wireless networks to fleet management systems.
Aerial Work Vehicle Slew Drive supplier
As urban landscapes grow denser and maintenance requirements more complex, Aerial Work Vehicle Slew Drives evolve from simple rotational components into intelligent motion control systems. Their ability to combine mechanical robustness with advanced control technologies ensures elevated work platforms will meet future safety and efficiency demands while maintaining the precision required for delicate operations at height. Through continuous innovation in materials science and smart system integration, these critical components remain essential partners in advancing aerial work safety and productivity across industries.
LYRA Drive is a professional slewing bearings ,slew drive and gears manufacturer provides customized slew bearing, drive and gears.For application-specific engineering solutions, contact LYRA to discuss technical specifications and implementation strategies.