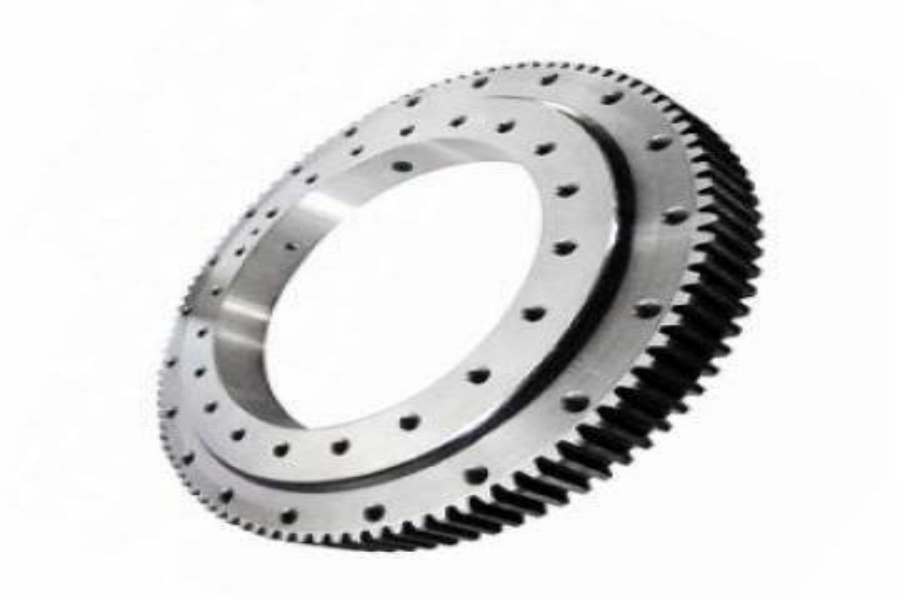
Excavator Slewing Bearings The Unseen Powerhouse Revolutionizing Earthmoving Operations
When earthmovers bite into rockfaces and demolition claws tear through concrete, excavator slewing bearings become the unyielding core that translates hydraulic fury into controlled rotation. These forged steel giants anchor the machine's pivoting power, enabling seamless 360° turns while battling grit-filled worksites where every revolution grinds against abrasive payloads. Their hardened raceways and precision-tuned clearances withstand forces that twist frames and shatter lesser components - from the erratic jolts of boulder excavation to the relentless vibration of deep foundation drilling. Modern iterations now embed wear sensors and self-compensating seals, evolving from passive load carriers to active system guardians that predict failure points before downtime strikes. This fusion of brute-force engineering and adaptive intelligence makes them indispensable in reshaping terrain across mining, construction, and disaster recovery sectors.
What is an Excavator Slewing Bearings
An Excavator Slewing Bearing constitutes a heavy-duty rotational mechanism specifically crafted to handle dynamic combinations of axial, radial, and moment loads generated during digging, lifting, and swinging operations. Typically constructed with double or triple-row roller configurations housed within tempered alloy steel rings ranging from 0.5 to 3 meters in diameter, these components integrate reinforced raceways capable of absorbing shock loads equivalent to multiple dump truck impacts. Modern iterations incorporate precision-ground gear teeth meshing with hydraulic drive motors and adaptive sealing systems that repel contaminants from muddy slurry to airborne rock dust. From open-pit mines where temperatures swing 50°C daily to urban demolition sites vibrating with concrete crushers, these bearings facilitate smooth rotation even when hydraulic systems operate at peak pressure during extended digging cycles.
Mechanical Intelligence Behind Reliable Rotation
The operational reliability of Excavator Slewing Bearings emerges from multi-faceted engineering solutions addressing unique earthmoving challenges. Imagine a 45-ton excavator performing deep foundation work in waterlogged terrain where constant submersion threatens traditional components. Here, the bearing employs stainless steel rollers and hydrophobic grease formulations that displace moisture while maintaining lubrication integrity, paired with triple-layered seals featuring rotating labyrinth channels that eject silt particles during rotation. Hydraulic preload adjustment mechanisms automatically compensate for wear-induced clearance changes, maintaining optimal roller contact pressure as the machine transitions between delicate grading tasks and forceful rock breaking. Advanced models now integrate temperature-sensitive viscosity modifiers within their lubricants, ensuring consistent film strength whether operating in Arctic frost or desert heatwaves.
Pillars of Performance Excellence
Excavator Slewing Bearings deliver unmatched value through three foundational engineering achievements refined through global field applications:
Impact Force Distribution Mastery
Through precisely calculated roller spacing and raceway curvature profiles, these bearings dissipate shock loads from sudden bucket collisions with buried obstacles, localizing stress concentrations to prevent catastrophic failures. A Canadian mining consortium reported 40% fewer bearing replacements after adopting units with gradient-hardened raceways that develop protective micro-crystalline structures under impact stress.
Contaminant Exclusion Capabilities
Multi-stage sealing systems combining magnetic particle traps and positive-pressure grease channels create impenetrable barriers against abrasive particulates. A Southeast Asian dredging operation extended bearing service life from eight months to five years by implementing models with rotating seal lips that actively scrape away clay deposits during slewing motions.
Adaptive Load Management
Real-time load monitoring systems embedded within bearing assemblies communicate stress data to machine control units, automatically adjusting hydraulic flow rates to prevent overload conditions during complex lifting and digging maneuvers.
Sector-Defining Applications
The transformative impact of Excavator Slewing Bearings becomes apparent through their problem-solving roles across industries:
Mining Sector Breakthroughs:Giant excavators extracting oil sands utilize bearings with tungsten-carbide coated raceways that resist abrasive wear from silica-rich soils, coupled with circulating oil lubrication systems that filter out metallic wear particles during continuous 24/7 operations.
Urban Redevelopment Challenges:Compact-radius excavators maneuvering through narrow city streets employ slim-profile bearings incorporating high-strength polymer cages that reduce overall weight while maintaining load capacity, enabling precise debris removal next to historic structures without vibration damage.
Disaster Zone Recovery:Earthquake rescue excavators utilize bearings with emergency manual override systems allowing rotation via hand pumps when hydraulic systems fail, featuring anti-corrosion coatings that withstand chemical spills and decomposed organic matter encountered in collapsed buildings.
Quantifiable Operational Improvements
Technological advancements in Excavator Slewing Bearing design translate directly into measurable performance gains:
Extended Component Longevity:Laser-hardened raceway surfaces now achieve Rockwell hardness ratings exceeding 62 HRC, enabling continuous operation in granite quarries for over 15,000 hours without surface degradation.
Fuel Efficiency Optimization:Low-friction roller path geometries reduce hydraulic system energy demands by 25%, allowing a typical 30-ton excavator to conserve 9,000 liters of annual diesel consumption through decreased pump workload.
Safety System Integration:Smart bearings with wireless load sensors trigger automatic shutdowns when detecting abnormal stress patterns, preventing structural failures during overhead power line excavation by interrupting rotation before reaching critical load thresholds.
Addressing Field Deployment Complexities
Maximizing excavator bearing performance requires overcoming common operational challenges:
Thermal Cycling Stress:A Brazilian road construction project encountered premature bearing failures until adopting units with expansion-compensating roller arrangements that maintain proper clearances despite daily 40°C temperature fluctuations between night cooling and daytime operation.
Improper Lubrication Intervals:Arctic mining equipment initially suffered lubricant starvation in extreme cold until implementing bearings with viscosity-independent solid lubricant reservoirs that gradually release additives during rotation.
High-Frequency Vibration Damage:Demolition excavators crushing concrete structures reduced bearing lifespan by 70% until introducing models with vibration-dampening elastomer layers between bearing components.
Emerging Technological Frontiers
Innovative developments are reshaping Excavator Slewing Bearing capabilities:
Self-Diagnostic Systems:Prototype bearings with embedded acoustic emission sensors detect early-stage roller defects, transmitting maintenance alerts to fleet managers months before traditional vibration analysis would identify issues.
Regenerative Friction Coatings:Experimental raceway treatments utilizing graphene-infused layers demonstrate 90% reduction in micropitting during sand-heavy operations, currently undergoing field trials in Middle Eastern desert excavation projects.
Hybrid Power Integration:Bearings with integrated electric motor assists enable dual-power rotation systems, allowing excavators to switch between hydraulic and battery-powered slewing for reduced emissions in urban zones.
Excavator Slewing Bearings supplier
As global infrastructure demands intensify and environmental regulations tighten, Excavator Slewing Bearings evolve from passive components into intelligent system orchestrators. Their capacity to blend industrial-grade durability with smart technology integration ensures earthmoving equipment will meet future challenges while maintaining the operational reliability and safety standards required in high-risk excavation environments.
LYRA Drive is a professional slewing bearings ,slew drive and gears manufacturer provides customized slew bearing, drive and gears.For application-specific engineering solutions, contact LYRA to discuss technical specifications and implementation strategies