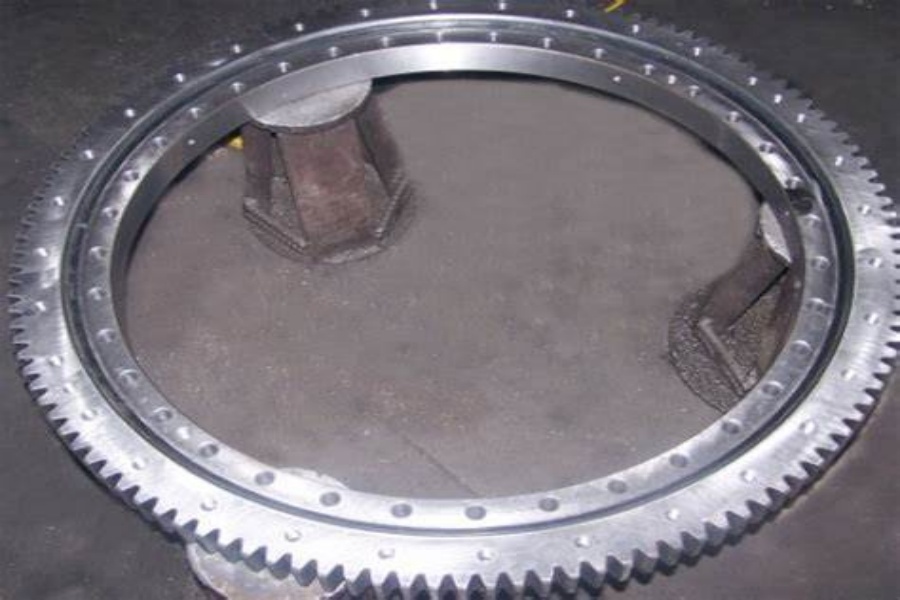
Heavy Load Slewing Bearings Powering Industrial Giants with Unmatched Strength
As industrial machinery evolves to confront unprecedented scale and endurance challenges, Heavy Load Slewing Bearings have become the unsung heroes powering the rotation of massive systems that form the foundation of modern infrastructure. These engineered giants enable critical operations—from harnessing wind energy through turbine yaw systems to maneuvering megaton construction loads—by transforming immense mechanical forces into controlled, reliable motion. Designed to withstand axial, radial, and moment stresses that would obliterate conventional components, they combine brute strength with precision engineering to meet the escalating demands of industries where operational continuity is non-negotiable. Beyond raw power, their evolution now integrates sustainability-focused materials and IoT-enabled monitoring systems, reflecting a shift toward intelligent, eco-conscious heavy machinery solutions. This examination reveals how these bearings not only endure extreme conditions but also drive innovation in sectors reshaping our physical and energy landscapes.
What is a Heavy Load Slewing Bearing
A Heavy Load Slewing Bearing is a rugged rotational assembly engineered to manage immense forces across multiple axes, often exceeding thousands of kilonewtons in load capacity. Unlike their compact counterparts, these industrial titans feature double or triple-row roller arrangements housed within massive forged steel rings that can span over 15 meters in diameter for mega-projects. The integration of hardened raceways and precision-ground rolling elements allows continuous rotation under full load for decades, with specialized variants incorporating gear teeth for direct drive engagement or custom flange patterns for structural integration. From offshore oil platforms resisting hurricane-force winds to tunnel boring machines grinding through bedrock, these bearings serve as the critical pivot points where brute strength meets precision engineering.
Engineering Principles Behind Massive Rotation Systems
The operational reliability of Heavy Load Slewing Bearings stems from meticulous design considerations that account for both extreme forces and environmental extremes. Consider a 6MW offshore wind turbine’s yaw system, where a 4.5-meter diameter bearing must maintain smooth rotation despite 150-ton nacelle weights and saltwater corrosion. Here, the bearing employs triple-row cylindrical rollers to distribute loads evenly across separate raceways while using seawater-resistant zinc-nickel coatings and multi-labyrinth seals to block abrasive particles. Hydraulic preload systems maintain optimal roller contact under fluctuating wind loads, preventing brinelling damage during storm conditions. Similarly, mining excavators use bearings with internal friction welds to handle shock loads from 50-ton bucket impacts, incorporating temperature sensors that trigger automatic lubrication during high-stress digging cycles.
Strategic Advantages in Demanding Environments
Heavy Load Slewing Bearings dominate industrial applications through three core strengths that justify their substantial footprint:
Uncompromising Load Management
By utilizing multiple load paths and optimized contact angles, these bearings achieve load capacities surpassing 30,000 kN·m while maintaining sub-millimeter rotational accuracy. A German-made bearing in container cranes handles 65 million load cycles annually, rotating 80-ton shipping containers with positional accuracy tighter than 0.1 degrees through eight years of continuous service.
Environmental Resilience
Advanced sealing systems combine hydrophobic compounds and pressurized grease chambers to create barriers against contaminants ranging from desert sand to molten steel mill splatter. A copper mine in Chile extended bearing service life from 9 months to 5 years by adopting bearings with triple-layer seals and graphene-enhanced grease capable of repelling acidic slurry infiltration.
Custom Integration Capabilities
Manufacturers now offer integrated solutions where bearings arrive pre-assembled with mounting rings, gear drives, and condition monitoring ports. A Scottish shipyard reduced offshore crane installation time by 40% using bearings with laser-aligned bolt patterns that eliminate traditional alignment shimming processes.
Sector-Specific Applications Redefining Possibilities
The true measure of Heavy Load Slewing Bearings lies in their transformative impact across industries:
Renewable Energy Expansion:Offshore wind installations now employ 10-meter bearings with predictive maintenance systems, using vibration analysis to schedule component replacements during seasonal low-wind periods. These units withstand North Sea conditions where wave impacts generate momentary loads equivalent to 300 elephants standing on a single gear tooth.
Mega-Construction Innovations:Dubai’s rotating skyscraper project utilizes 56 custom bearings measuring 8 meters in diameter, each containing 3.2 km of roller channels to support 30,000-ton rotating sections while maintaining energy-efficient operation through low-friction polymer cages.
Mining Evolution:Autonomous haul trucks in Australian iron ore mines use AI-optimized bearings that adjust preload based on real-time payload data, reducing roller stress during steep incline ascents and extending maintenance intervals by 70% compared to conventional designs.
Quantifiable Operational Breakthroughs
Data-driven improvements underscore the value proposition of modern Heavy Load Slewing Bearings:
Extended Service Life:Advanced heat treatment processes now produce raceway surfaces with Rockwell hardness ratings of 60 HRC, enabling continuous operation in cement plant kilns for over 100,000 hours without surface degradation.
Energy Efficiency Gains:Low-torque designs featuring polished roller paths and synthetic lubricants reduce rotational resistance by 22%, saving a typical steel mill $280,000 annually in reduced drive motor energy consumption.
Safety Enhancements:Smart bearings with embedded fiber-optic strain sensors provide early warning of abnormal load conditions, preventing catastrophic failures in amusement park observation wheels by detecting microscopic raceway cracks six months before traditional inspection methods would flag issues.
Navigating Implementation Challenges
Successful deployment of Heavy Load Slewing Bearings requires awareness of common operational pitfalls:
Thermal Expansion Miscalculations:A Brazilian hydroelectric project experienced bearing seizure after engineers neglected to account for 40°C temperature swings between nighttime reservoir cooling and turbine operation, necessitating redesigned clearance tolerances incorporating climate data.
Improper Lubrication Practices:Arctic mining equipment initially suffered from grease solidification in -50°C conditions until switching to aerogel-infused lubricants with pour points below -70°C, maintaining consistent film strength across extreme temperature gradients.
Dynamic Load Underestimation:Early offshore wave energy converters saw premature bearing failures until designers incorporated real-time wave force modeling that revealed momentary load spikes 800% higher than steady-state calculations predicted.
Heavy Load Slewing Bearings supplier
As industries continue demanding higher loads, smarter operation, and greener solutions, Heavy Load Slewing Bearings evolve from passive components to intelligent system enablers. Their ability to combine raw power with precision ensures they’ll remain indispensable in building tomorrow’s infrastructure while maintaining the delicate balance between industrial might and technological finesse.
LYRA Drive is a professional slewing bearings ,slew drive and gears manufacturer provides customized slew bearing, drive and gears.For application-specific engineering solutions, contact LYRA to discuss technical specifications and implementation strategies.