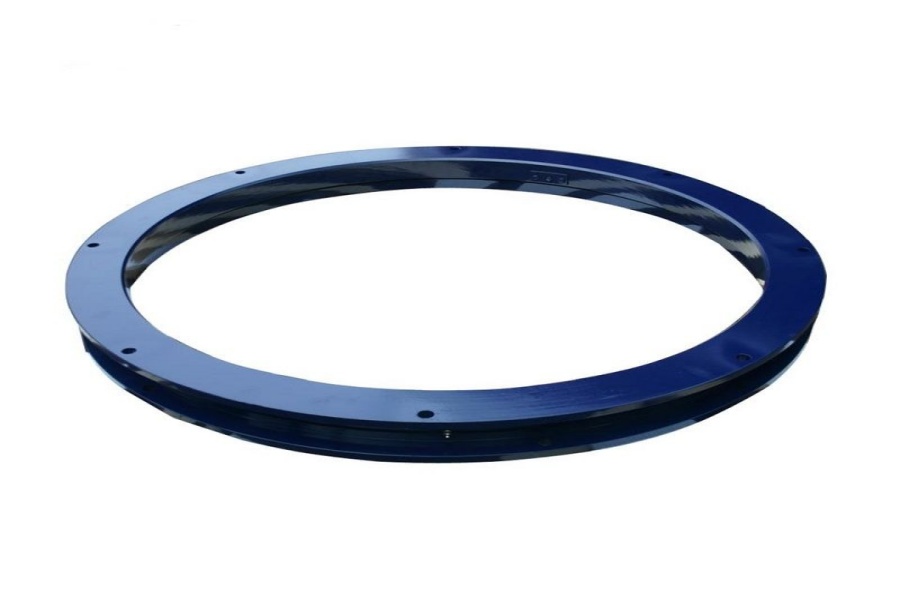
Crossed Roller Slewing Bearings Powering High-Precision Motion Systems
Where robotic arms perform surgery with hair-width precision and wind turbines adjust blades against gale-force winds, crossed roller slewing bearings act as the hidden pivot points enabling flawless motion under crushing loads. These precision-crafted components interlock rollers in a crisscross ballet, distributing stress across multiple axes to prevent even micron-level deviations during rapid rotations. Their hardened raceways, polished to mirror finishes, allow satellite dish antennas to track celestial movements with zero backlash while enduring decades of thermal cycling in orbit. Modern variants now double as data sources, with vibration sensors etched into roller paths that alert engineers to wear patterns months before failures disrupt production lines. This fusion of mechanical mastery and predictive intelligence makes them indispensable in industries where rotational perfection dictates success or catastrophic failure.
What Is a Crossed Roller Slewing Bearing
A crossed roller slewing bearing distinguishes itself through a meticulously arranged configuration where cylindrical or tapered rollers alternate orientation between two perpendicular raceways, creating an interlocking pattern that simultaneously manages axial, radial, and moment loads with exceptional rigidity. This structural innovation eliminates the need for multiple bearing assemblies by consolidating load-handling capabilities into a single compact unit while maintaining minimal rotational resistance through precision-ground rolling elements spaced at exact intervals. The crossed arrangement ensures uniform stress distribution across contact surfaces, preventing localized wear even during continuous oscillating motions in applications such as telescope azimuth drives or industrial robot wrist joints. Integrated sealing systems filled with specialized greases protect internal components from particulate ingress in harsh environments ranging from desert solar farms to underwater research vessels, while modular flange designs allow direct integration with machine frames through standardized bolt patterns. The bearing’s ability to maintain positional accuracy under dynamic loading conditions makes it particularly valuable in semiconductor manufacturing equipment where vibration-induced errors could ruin entire wafer batches, as well as in wind turbine pitch control systems requiring reliable operation despite constant exposure to salt spray and temperature fluctuations.
Global Advancements in Crossed Roller Bearing Technology
Established manufacturing centers in Europe and North America continue pushing material science boundaries through atomic-level surface treatments that extend bearing service life beyond traditional limits. German engineers have pioneered cryogenically stabilized raceways that reduce micro-deformation under heavy cyclic loads, a breakthrough benefiting high-speed packaging lines handling fragile glass containers. Japanese manufacturers leverage nano-particle lubricant additives that self-replenish worn surface layers, significantly reducing maintenance intervals for bearings in automated warehouse retrieval systems operating 24/7. Meanwhile, American aerospace suppliers are testing diamond-coated rollers capable of withstanding the extreme temperature swings experienced by Mars rover instrumentation arms without compromising rotational smoothness.
Emerging industrial economies are making strategic leaps through smart manufacturing adoption, with Indian factories implementing AI-driven quality control systems that detect sub-micron roller alignment deviations during high-volume production. Brazilian researchers have developed bio-based polymer retainers that maintain dimensional stability in humid tropical climates while meeting strict sustainability certifications for bearings used in European offshore energy projects. Chinese laboratories recently demonstrated graphene-enhanced seal materials that repel corrosive chemicals in petrochemical plant rotating platforms, addressing a longstanding challenge in heavy industry applications.
Technical Challenges and Innovative Solutions
The primary hurdles in crossed roller bearing development revolve around balancing precision tolerances with mass production feasibility, particularly as demand surges for customized configurations in niche applications. Traditional manufacturing methods struggle with achieving consistent surface finish quality across large-diameter bearings used in radar antenna bases, where even minor imperfections can distort signal accuracy. Advanced grinding machines equipped with real-time laser measurement feedback now compensate for tool wear during production, ensuring raceway flatness within 0.0002-inch tolerances for bearings in particle accelerator beam steering mechanisms.
Material compatibility remains critical in extreme environments, prompting innovations like ceramic hybrid bearings for MRI machine gantries that eliminate magnetic interference while withstanding repeated sterilization cycles. Researchers are experimenting with shape-memory alloys for roller elements that automatically adjust preload based on temperature changes in spacecraft docking mechanisms. A recent breakthrough involves 3D-printed bearing cages with integrated strain gauges that provide real-time load distribution data without compromising structural integrity in collaborative robot joints.
Smart Integration and Sustainable Evolution
Next-generation crossed roller bearings are evolving into intelligent system components through embedded sensor networks that transform mechanical rotation into actionable operational data. Prototype units currently under trial feature vibration energy harvesters powering wireless transmitters that relay bearing health metrics to plant maintenance systems, enabling predictive servicing before audible wear symptoms emerge. Solar tracking systems now employ bearings with integrated light sensors that automatically optimize panel angles while monitoring structural stress patterns caused by wind loading.
Environmental considerations drive material innovation, with manufacturers developing fully recyclable aluminum alloy bearings that maintain steel-grade load capacities for consumer electronics assembly robots. Experimental mycelium-based composite retainers show promise in disposable medical imaging equipment bearings, combining sterilization resistance with compostable end-of-life properties. Production process improvements include AI-optimized machining paths that reduce material waste by 40% during raceway grinding operations while maintaining micron-level precision standards.
Implementation Strategies for Optimal Performance
Precision Installation Protocols:Utilize thermally stabilized mounting fixtures to prevent bearing distortion during installation in climate-controlled clean rooms manufacturing optical lenses, ensuring raceway alignment remains within 0.001mm tolerance specifications.
Environment-Specific Customization:Select silver-plated rollers with molybdenum disulfide coatings for ultra-high vacuum applications in space simulation chambers, while opting for food-grade stainless steel variants with PTFE seals in beverage canning line rotary fillers.
Condition Monitoring Integration:Implement acoustic emission analysis systems that detect early-stage roller brinelling through high-frequency vibration pattern recognition, allowing scheduled replacements during planned maintenance shutdowns in steel mill rotary hearth furnaces.
Circular Economy Adaptation:Adopt modular bearing designs enabling individual roller replacement instead of complete unit disposal, coupled with blockchain-tracked material passports ensuring proper recycling channel routing for end-of-life components from decommissioned wind turbine yaw systems.
Crossed roller slewing bearings supplier
Crossed roller slewing bearings stand at the convergence point of mechanical engineering excellence and digital transformation, evolving from passive rotation facilitators to active contributors in smart industrial ecosystems. As additive manufacturing enables complex internal cooling channels and sensor integration previously unimaginable, and material breakthroughs allow operation in environments from deep-sea hydrothermal vents to lunar regolith, these components will continue enabling technological leaps across industries. The challenge for engineers lies not just in selecting bearings that meet current specifications, but in anticipating how these precision systems can unlock new capabilities in machinery yet to be conceived – whether in quantum computing cooling systems or neural interface surgical robots. By embracing crossed roller solutions that combine nanometer-level precision with environmental intelligence and data transparency, industries position themselves to lead in an era where rotational components become strategic assets driving both operational efficiency and sustainable progress.
LYRA Drive is a professional slewing bearings ,slew drive and gears manufacturer provides customized slew bearing, drive and gears.For application-specific engineering solutions, contact LYRA to discuss technical specifications and implementation strategies.