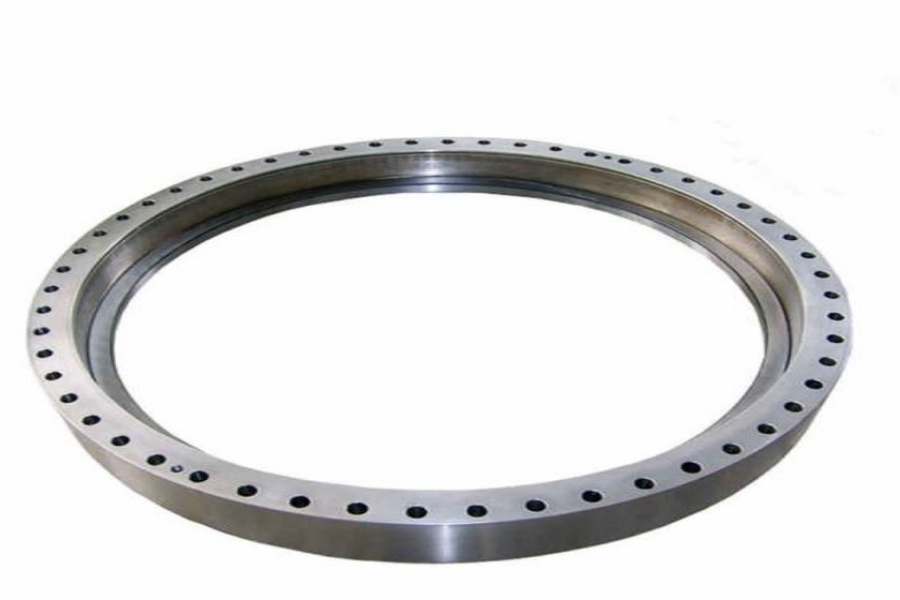
Excavator Slewing Bearings The Core of Earthmoving Precision
When excavator arms heave multi-ton boulders in quarries or carve precise trenches for urban pipelines, the relentless rotation hinges on slewing bearings—forged steel titans hidden within the machine's core. These components endure forces that would warp ordinary metal, their multi-row rollers distributing stress from violent digs while maintaining micron-level alignment across thousands of swing cycles. Modern versions now outsmart wear, with embedded sensors mapping load patterns to predict maintenance needs before downtime strikes. As global infrastructure races against deadlines, these bearings evolve from passive pivots to intelligent motion guardians, enabling machinery to conquer both raw power demands and finesse tasks without compromise.
What Is an Excavator Slewing Bearing
An excavator slewing bearing is a heavy-duty rotational component that serves as the central pivot point connecting the machine’s upper structure to its undercarriage, enabling 360-degree continuous rotation under full load. This engineered assembly consists of large-diameter inner and outer steel rings housing multiple rows of balls or rollers, designed to withstand extreme axial, radial, and moment forces generated during digging, lifting, and swinging operations. The bearing integrates hardened raceways for durability, gear teeth for drive system engagement, and advanced sealing mechanisms to protect against abrasive contaminants like soil, rock fragments, and moisture.
The critical role of these bearings lies in their ability to maintain precise movement under dynamic stress. When an excavator operator rotates a 20-ton load of excavated material to deposit it into a waiting truck, the slewing bearing ensures smooth motion despite uneven weight distribution and ground vibrations. In mining applications, these components endure constant shock loads from rock breaking while maintaining alignment accuracy over thousands of operating hours. Their sealed lubrication systems prevent contamination in muddy conditions, while specialized heat treatments ensure performance stability in temperature extremes ranging from -30°C Arctic sites to +50°C desert operations.
Global Innovations in Excavator Slewing Bearing Technology
Engineering Advancements in Established Industrial Centers
Countries with deep expertise in heavy machinery manufacturing, including Germany, Japan, and Sweden, continue to drive technological breakthroughs. German manufacturers employ laser-cladded gear teeth that self-repair minor surface damage during operation, extending service life in high-abrasion environments. Japanese engineers have developed asymmetric roller bearing designs that optimize load distribution during counterweighted swings, reducing stress concentrations by 35% in large mining excavators. Swedish firms utilize cryogenic stabilization processes, treating bearing components at -150°C to enhance dimensional stability under thermal cycling.
The construction sector benefits from sensor-embedded bearings that provide real-time data on load distribution and wear patterns, enabling predictive maintenance in fleet management systems. Mining operations utilize tungsten carbide-coated raceways to resist gouging from rock particulates, tripling component lifespan in hard rock excavation. Specialized variants for underwater dredging equipment feature corrosion-resistant alloys and pressurized lubrication systems that maintain performance in submerged conditions.
Emerging Markets Enhancing Production Capabilities
Manufacturers in industrializing regions are rapidly adopting advanced technologies to compete globally. Chinese producers now implement AI-driven grinding systems that adjust machining parameters in real time, achieving surface finishes comparable to premium European bearings. Indian engineers have pioneered composite seal materials combining graphene and fluoroelastomers, outperforming traditional seals in high-dust environments. Brazilian firms employ blockchain-tracked steel sourcing to ensure material consistency for bearings used in Amazonian infrastructure projects.
Persistent challenges include mastering dynamic load simulation and fatigue life prediction. European manufacturers use multi-physics modeling software that simulates decade-long wear patterns in weeks, while emerging markets often rely on physical testing protocols that extend development cycles. Access to ultra-clean steel alloys with controlled inclusion sizes remains limited in some regions, affecting bearing reliability in high-cycle applications like urban demolition projects.
Overcoming Technical Challenges in Excavator Bearing Applications
The performance gap between industry leaders and developing manufacturers centers on three key areas: material science, predictive maintenance integration, and manufacturing precision. Premium bearings utilize micro-alloyed steels with vanadium and niobium additives, enhancing toughness without compromising hardness—critical for withstanding impact loads during rock excavation. In contrast, conventional steels used in cost-sensitive markets exhibit accelerated spalling in applications requiring 800,000+ rotation cycles.
Collaborative initiatives are accelerating progress. University partnerships are developing self-lubricating bearing surfaces using MXene nanocomposites that reduce friction by 45% in arid environments. Another innovation involves edge computing modules integrated into bearing housings, analyzing vibration data to predict raceway wear six months before failure. Workforce training programs using augmented reality simulators are reducing installation errors by 60% through interactive 3D guidance systems.
The Future of Excavator Slewing Bearings Smart and Sustainable Solutions
Next-generation bearings will prioritize energy efficiency, self-diagnostic capabilities, and circular economy principles. Prototype kinetic energy recovery systems now under development capture swing braking energy to power onboard sensors and hydraulic assists. Material scientists are experimenting with bio-based lubricants derived from industrial algae, reducing environmental impact while maintaining performance in extreme temperatures.
In smart construction ecosystems, bearings will evolve into intelligent system nodes. Imagine excavators where slewing bearings communicate with site management software to optimize swing paths based on real-time terrain data, minimizing fuel consumption. Autonomous mining equipment could utilize bearings with embedded strain gauges to automatically adjust digging angles when encountering unexpected rock formations, preventing equipment damage.
Strategic Implementation Guidelines
Precision Installation Protocols:Deploy laser alignment tools to ensure bearing concentricity within 0.1mm tolerance during assembly, critical for achieving advertised service life in high-duty cycle mining equipment.
Environment-Specific Material Selection:Specify boronized surface treatments for quarry excavators facing abrasive granite dust and chromium-nitride coatings for coastal applications combating salt corrosion.
Condition Monitoring Integration:Implement acoustic emission sensors that detect subsurface raceway cracks through ultrasonic frequency analysis, enabling proactive replacements during scheduled downtime.
Circular Design Practices:Develop modular bearing architectures allowing individual roller replacement, reducing material waste during overhauls and supporting sustainability goals.
Excavator slewing bearings supplier
Excavator slewing bearings represent the intersection of mechanical endurance and technological innovation, enabling the earthmoving feats that build modern civilization. As global industries push for greener practices and smarter machinery, these components are transitioning from passive load carriers to active system contributors. While established manufacturers continue advancing through nano-engineered materials and IoT integration, emerging markets prove that digital manufacturing adoption and collaborative R&D can bridge technological divides. The future promises bearings that not only withstand immense forces but also optimize energy use, predict maintenance needs, and adapt to operational challenges—transforming from steel assemblies into intelligent partners in construction evolution. For industry stakeholders, embracing both technological leaps and sustainable principles will be essential in shaping the next era of earthmoving excellence.
LYRA Drive is a professional slewing bearings ,slew drive and gears manufacturer provides customized slew bearing, drive and gears.For application-specific engineering solutions, contact LYRA to discuss technical specifications and implementation strategies.