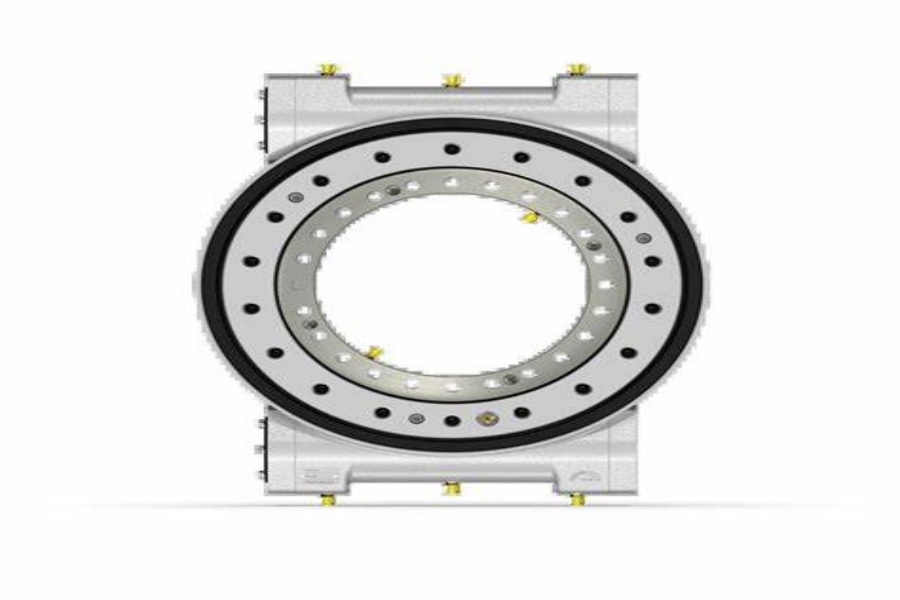
Double Worm Slew Drives Redefining Precision in Heavy-Duty Rotation
Where industrial systems can't afford stutters—whether positioning satellite antennas during solar storms or stabilizing crane loads on heaving oil rigs—dual worm gear slew drives deliver the mechanical certainty that keeps operations intact. These twin-drive systems pair redundant gears that share punishing torque loads, ensuring rotation continues even if one worm fails mid-operation. Their hardened teeth mesh with micron precision, distributing stress across dual contact paths to prevent the localized wear that cripples single-gear setups. Modern versions now embed vibration analytics that predict gear fatigue months before failure, transitioning from dumb rotators to self-aware motion guardians. This fusion of brute-force reliability and predictive intelligence makes them indispensable in industries where equipment downtime translates to six-figure losses per hour.
What Is a Double Worm Slew Drive
A double worm slew drive is a robust rotational system characterized by its dual worm gear configuration, where two parallel worm gears engage with a single worm wheel or two separate wheels. This design doubles the contact area between the worms and the wheel, distributing load more evenly and significantly enhancing torque capacity while reducing wear. Each worm gear can act as a primary or backup drive, providing redundancy—a feature critical in applications where unexpected downtime could lead to catastrophic consequences. The system typically integrates high-strength slewing bearings to manage axial, radial, and moment loads, alongside advanced sealing mechanisms to protect against contaminants like dust, water, or corrosive agents.
The superiority of double worm slew drives lies in their ability to deliver fail-safe operation and precise motion control under extreme conditions. For instance, in offshore oil rigs, these drives ensure crane booms rotate smoothly despite turbulent waves, with the redundant worm system engaging instantly if the primary gear fails. Similarly, in military applications, double worm drives enable radar antennas to maintain uninterrupted tracking during missions, where system reliability directly impacts safety. Their enhanced load distribution also minimizes heat buildup, extending component lifespan in high-duty cycles such as mining excavators or automated storage retrieval systems. By combining redundancy with superior torque management, double worm slew drives address the growing industrial demand for resilience and precision.
Global Innovations Elevating Double Worm Slew Drive Performance
Engineering Excellence in Traditional Powerhouses
Nations renowned for mechanical innovation, including Germany, the United States, and South Korea, continue to push the boundaries of double worm slew drive technology. German manufacturers utilize multi-axis CNC grinding machines to achieve micron-level accuracy in worm gear profiles, ensuring seamless meshing and near-silent operation even under maximum load. Breakthroughs in dual-frequency induction hardening allow selective hardening of gear teeth roots and flanks, optimizing durability without compromising the core material’s toughness. These advancements are validated through rigorous testing protocols, such as accelerated life cycling in environmental chambers simulating Arctic cold or desert heat.
The energy sector showcases these innovations, where double worm drives in wind turbine yaw systems adjust nacelle orientation with precision, maximizing energy capture while withstanding decades of saltwater exposure. Aerospace applications employ drives crafted from titanium matrix composites, reducing weight by up to 40% compared to steel while maintaining strength—a critical factor in satellite solar array deployment mechanisms. Robotics further benefits from compact double worm units with integrated torque sensors, enabling collaborative robots to handle fragile objects without risk of overload, thanks to real-time feedback loops adjusting motor output.
Emerging Economies Advancing Through Technology Adoption
While established markets lead in high-complexity designs, manufacturers in industrializing regions are closing the gap through strategic automation and digital integration. By deploying AI-driven predictive maintenance platforms, these producers minimize unplanned downtime in drives used for port logistics or construction equipment. For example, double worm systems in automated container cranes now feature self-lubricating polymers and wireless condition monitoring, allowing operators in emerging hubs to compete on reliability metrics previously dominated by premium brands.
Challenges remain in mastering asymmetric load distribution algorithms and ultra-high-precision backlash control. Global leaders employ proprietary software to simulate load scenarios across both worms, ensuring balanced torque sharing—a capability still evolving in regions reliant on off-the-shelf simulation tools. Additionally, access to high-purity alloy steels and space-grade lubricants remains uneven, affecting the performance consistency of drives in extreme environments like deep-sea exploration or high-altitude defense systems.
Navigating Challenges in Double Worm Slew Drive Development
The divide between industry leaders and emerging players centers on three pillars: material innovation, manufacturing agility, and intelligent system integration. Premium drives often incorporate nanostructured coatings on worm gears to reduce friction coefficients by up to 30%, a technology still scaling in cost for wider adoption. Conversely, reliance on conventional coatings in some markets leads to faster degradation in high-speed applications like tunnel boring machines or steel coil handlers.
Cross-industry collaborations are accelerating progress. Universities partner with manufacturers to develop hybrid additive-subtractive manufacturing techniques, enabling the production of worm gears with internal cooling channels for thermal management in continuous operation. Another frontier is edge computing-enabled drives, where onboard processors analyze vibration patterns to predict bearing wear weeks in advance. Workforce development programs focusing on digital twin integration allow engineers to virtually test drive configurations under simulated operational stresses, reducing physical prototyping costs by over 60%.
The Future of Double Worm Slew Drives Intelligence and Sustainability
Next-generation double worm slew drives will prioritize energy recovery systems, modular redundancy, and closed-loop sustainability. Engineers are prototyping regenerative braking systems that convert rotational inertia into stored energy during deceleration, slashing power consumption in applications like electric crane slewing. Eco-design initiatives promote bio-based hydraulic fluids and modular housing designs that allow 90% of drive components to be disassembled and recycled at end-of-life.
In smart industrial networks, these drives will function as autonomous decision-makers. Imagine a container ship’s cargo handling system where double worm drives communicate with weather satellites to pre-adjust crane slew speeds based on incoming storm data, preventing load swing accidents. Or consider smart agriculture systems where irrigation tower drives automatically recalibrate rotation angles using soil moisture sensors, optimizing water distribution across fields. Such innovations align with the global shift toward autonomous, data-driven industrial ecosystems.
Double worm slew drives supplier
Double worm slew drives epitomize the fusion of mechanical robustness and technological sophistication. As industries worldwide prioritize uptime, precision, and environmental responsibility, these components will remain indispensable in critical applications. While technological pioneers continue to redefine performance ceilings through advanced materials and AI integration, emerging markets prove that rapid capability-building through digitization and collaboration is achievable. The future of double worm slew drives lies not merely in greater power or redundancy but in their transformation into intelligent, sustainable systems that drive industrial progress. For businesses and engineers, staying ahead will require embracing both innovation and adaptability—the twin engines powering tomorrow’s industrial landscape.
LYRA Drive is a professional slewing bearings ,slew drive and gears manufacturer provides customized slew bearing, drive and gears.For application-specific engineering solutions, contact LYRA to discuss technical specifications and implementation strategies.