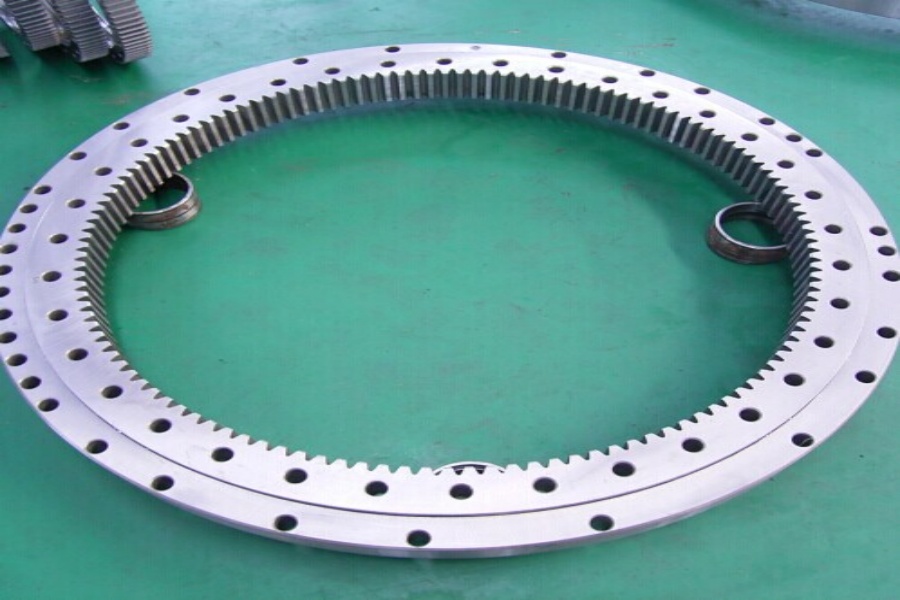
Truck Crane Slewing Bearings The Silent Force Behind Mobile Lifting Excellence
At the intersection of mobile power and precision engineering, Truck Crane Slewing Bearings act as the silent orchestrators behind critical lifting operations that shape skylines and save lives. These rotational cores transform hydraulic energy into controlled motion, enabling cranes to pivot multi-ton payloads across chaotic construction zones and disaster sites with surgical accuracy. Engineered to withstand relentless vibration, unpredictable shock loads, and environmental extremes—from desert heatwaves to coastal salt spray—they reconcile the paradox of industrial machinery: delivering uncompromised strength within compact, mobile frameworks. As urbanization accelerates and infrastructure projects grow increasingly complex, these bearings evolve beyond mere mechanical components into intelligent systems that adapt to dynamic load conditions while extending equipment longevity. Their role in modern mobile crane operations reflects a technological tightrope walk between raw lifting capacity and nuanced control, proving essential for industries where operational precision directly impacts project timelines and human safety.
Understanding Truck Crane Slewing Bearing Fundamentals
A Truck Crane Slewing Bearing represents a specialized rotational assembly engineered to handle complex load combinations while maintaining smooth 360-degree rotation under constantly changing stress conditions. Characterized by single or double-row ball/roller configurations encased within hardened steel rings, these components typically range from 1 to 4 meters in diameter to accommodate various crane sizes. Their design integrates reinforced raceways capable of withstanding axial forces from boom weight, radial stresses during side pulls, and moment loads created by extended load radii. Modern variants incorporate integrated gear teeth for hydraulic motor drives and custom mounting provisions that allow direct attachment to crane turntables, eliminating alignment issues during field maintenance. From recovering overturned trucks on mountain passes to positioning wind turbine components at dizzying heights, these bearings translate hydraulic power into controlled rotational movement where both payload and human lives depend on flawless operation.
Engineering Dynamics of Mobile Rotation Systems
The operational excellence of Truck Crane Slewing Bearings stems from multilayered engineering strategies addressing unique mobile equipment challenges. Consider a 300-ton mobile crane performing precision lifts at a petrochemical plant where explosive atmospheres demand non-sparking materials. Here, the bearing utilizes copper-nickel alloy rollers and conductive grease to prevent static discharge while maintaining load capacity through tapered roller geometry that compensates for chassis flexing during outrigger deployment. Sealing systems employ triple-lip designs with labyrinth extensions to exclude abrasive concrete dust and rainwater during monsoon season operations, coupled with grease purging ports that enable field servicing without disassembly. Advanced models now feature load-sensing raceways that communicate real-time stress data to crane control systems, automatically adjusting hydraulic pressure to maintain optimal roller contact when handling irregularly shaped cargo.
Core Strengths Defining Operational Superiority
Truck Crane Slewing Bearings deliver indispensable value through three pillars of engineering excellence refined through decades of field experience:
Shock Load Absorption Mastery
Through optimized roller path geometries and elastic deformation allowances, these bearings dissipate sudden impact forces encountered when catching swinging loads or recovering from emergency stops. A North American crane operator association reported 60% reduction in bearing replacement rates after adopting models with progressive hardness gradient raceways that localize stress concentrations during shock events.
All-Terrain Performance Consistency
Arctic-grade variants maintain operational integrity at minus 50 degrees Celsius using low-temperature tolerant steels and synthetic lubricants with pour points below minus 60 degrees Celsius, enabling winter construction projects in Siberian oil fields where traditional bearings would seize within hours. Conversely, desert-operating cranes utilize bearings with solar-reflective coatings and dust expulsion vanes that prevent sand particle ingress during frequent sandstorm conditions.
Maintenance Optimization Features
Quick-disconnect lubrication lines and magnetic debris collectors integrated into bearing assemblies allow technicians to perform essential servicing during routine safety inspections without crane downtime. A European crane fleet operator achieved 98% operational availability by implementing bearings with RFID-tagged maintenance ports that track lubrication history and wear patterns through handheld scanners.
Industry-Transforming Application Scenarios
The versatility of Truck Crane Slewing Bearings becomes evident through their problem-solving roles across diverse sectors:
Urban Infrastructure Development:Tower crane assembly/disassembly using mobile cranes relies on bearings capable of handling rapidly changing load dynamics during component rotations. A bearing designed for bridge construction cranes in earthquake-prone regions incorporates seismic dampening elements that allow continuous operation during minor tremors while locking rotation automatically when ground motion exceeds safety thresholds.
Disaster Response Operations:Hurricane recovery cranes utilize corrosion-resistant bearings with emergency manual rotation systems that enable load positioning when hydraulic systems fail. These units feature stainless steel components and seawater-neutral lubricants allowing operation in flooded areas where submerged bearing surfaces must resist brackish water corrosion for weeks.
Renewable Energy Logistics:Oversized bearing designs with extended gear teeth profiles facilitate the precise positioning of wind turbine nacelles during roadside assembly procedures. A specialized variant used in mountainous terrain incorporates inclination compensation mechanisms that maintain lubrication distribution even when the crane operates on 15-degree slopes during turbine installations.
Measurable Performance Advancements
Quantifiable improvements in Truck Crane Slewing Bearing technology directly translate into operational benefits:
Extended Duty Cycles:Advanced case carburizing techniques now enable raceways to withstand over 500,000 load cycles without surface pitting, allowing municipal crane fleets to extend bearing replacement intervals from 5 to 12 years under normal operating conditions.
Energy Consumption Reduction:Low-friction designs incorporating diamond-like carbon coatings on rolling elements reduce hydraulic system pressure requirements by 18%, enabling a typical 200-ton crane to save 7,000 liters of annual fuel consumption through decreased pump workload.
Safety Factor Enhancements
Smart bearings with embedded strain gauges and wireless telemetry provide real-time load distribution maps to crane operators, preventing dangerous overload conditions by automatically disabling rotation when stress patterns exceed engineering limits.
Overcoming Field Deployment Challenges
Maximizing Truck Crane Slewing Bearing performance requires addressing common operational hurdles:
Improper Storage Practices:Bearing failures increased 300% in tropical regions when warehouses neglected climate control, causing condensation-induced false brinelling until suppliers implemented vacuum-sealed packaging with humidity indicators.
Dynamic Load Misinterpretation:Early attempts at automated load chart calculations failed to account for centrifugal forces during high-speed rotation, resulting in premature bearing wear until updated algorithms incorporated angular momentum variables into load limit warnings.
Cross-Continent Compatibility Issues:Global crane fleets faced interchangeability challenges until ISO standardized mounting dimensions and lubrication specs, allowing bearings manufactured in Asia to seamlessly replace European units in South American mining operations.
Future Innovations in Mobile Rotation Technology
Emerging developments promise to redefine Truck Crane Slewing Bearing capabilities:
Energy Harvesting Systems:Prototype bearings with piezoelectric elements convert vibration energy into electricity to power onboard monitoring systems, undergoing field tests in remote area cranes where consistent power supply remains challenging.
Adaptive Surface Treatments:Nanoparticle-infused raceway coatings that modify friction coefficients based on temperature fluctuations are being tested in extreme environment cranes, potentially eliminating seasonal lubricant change requirements.
Augmented Reality Maintenance:Field technicians now use AR glasses that overlay bearing wear patterns and torque specifications during servicing, reducing maintenance errors by 75% in pilot programs with national crane rental companies.
Truck Crane Slewing Bearings supplier
As urbanization accelerates and infrastructure demands grow more complex, Truck Crane Slewing Bearings continue evolving from passive mechanical components into intelligent load management systems. Their ability to merge unyielding durability with sophisticated monitoring capabilities ensures mobile cranes will meet tomorrow’s lifting challenges while maintaining the safety standards and operational efficiency required in high-stakes environments.
LYRA Drive is a professional slewing bearings ,slew drive and gears manufacturer provides customized slew bearing, drive and gears.For application-specific engineering solutions, contact LYRA to discuss technical specifications and implementation strategies.