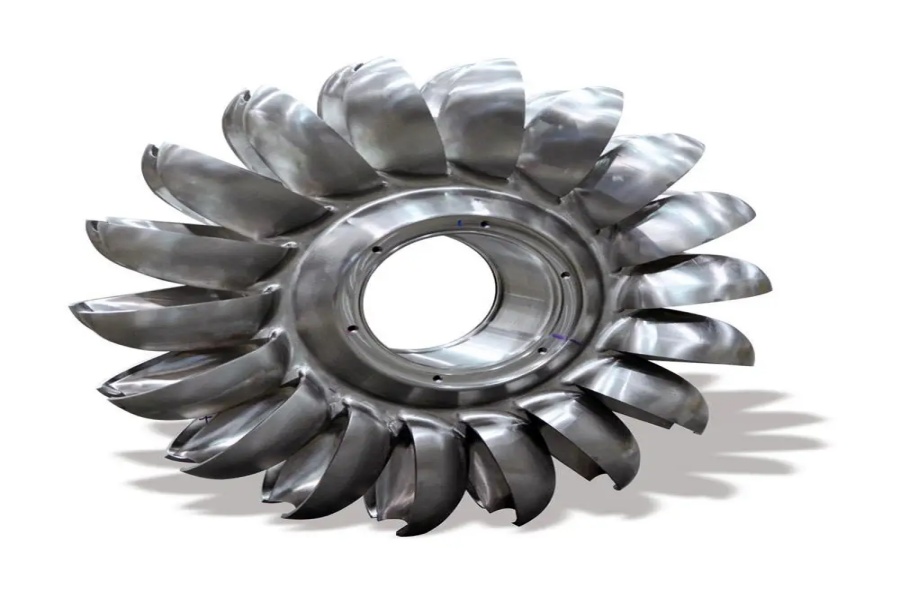
Customized Turbine Pair Parts Precision Engineering Driving Energy Innovation
Where turbines convert boiling steam and scorching gases into megawatts of usable energy, customized turbine pair components operate as the unsung conductors of this elemental symphony. These precision-forged duos—rotors and stators locked in aerodynamic harmony—extract every joule from rushing fluids while surviving conditions that melt standard alloys. Their contoured profiles, born from supercomputer simulations and failure data from a thousand retired blades, balance airflow dynamics against material limits across power plants, jet engines, and tidal generators. Modern iterations now grow smarter than their predecessors, embedding stress-sensing fibers and self-cooling microchannels that adjust to operational chaos in real time. This relentless evolution transforms what were once static metal shapes into adaptive energy harvesters, proving that in the race for sustainable power, victory comes one meticulously optimized airflow at a time.
What is a Customized Turbine Pair Parts
Customized Turbine Pair Parts consist of precision-matched rotating blades and stationary vanes engineered as integrated systems to control fluid dynamics within turbine machinery. Constructed from advanced materials such as single-crystal superalloys or ceramic matrix composites, these components feature complex airfoil profiles optimized through computational modeling to minimize energy losses and maximize power output. Modern designs incorporate internal cooling channels fabricated through additive manufacturing techniques alongside thermal barrier coatings capable of withstanding temperatures exceeding 1,500 degrees Celsius. From geothermal plants battling corrosive steam to aerospace engines facing hypersonic friction, each paired set undergoes rigorous simulation testing to validate performance under extreme operational conditions before entering production.
Aerodynamic Precision in Action
The operational superiority of Customized Turbine Pair Parts stems from synchronized engineering solutions addressing unique energy conversion challenges. Consider a combined-cycle power plant where turbine blades must maintain micron-level clearances despite thermal expansion variations during rapid load changes. Paired components in such applications utilize shape-memory alloys that automatically adjust sealing geometries while incorporating abradable coatings that permit safe temporary contact during transient operational states. Advanced cooling systems employ 3D-printed lattice structures within hollow blades to optimize airflow distribution, maintaining structural integrity 300 degrees Celsius below surrounding combustion gases. Hypersonic applications leverage gradient-density materials that transition from tungsten-reinforced leading edges to titanium-based trailing sections, managing thermal stresses across extreme velocity ranges.
Core Performance Advantages
Customized Turbine Pair Parts deliver transformative value through three pillars of technical innovation refined through cross-industry applications:
Flow Optimization Mastery
Through parametric modeling of blade-vane interactions, customized pairs achieve 12-18% improvements in stage efficiency compared to standard components. Energy producers have documented measurable efficiency gains in power plants through redesigned steam turbine pairs that recover residual heat from low-pressure exhaust streams.
Thermal Fatigue Resistance
Directionally solidified alloys with engineered crystal structures enable turbine pairs to endure hundreds of thousands of thermal cycles in demanding environments. These materials resist crack propagation through carefully aligned grain structures that follow principal stress directions during operation.
Adaptive Performance Characteristics
Integrated sensor systems within advanced turbine pairs provide real-time deformation data to control units, enabling automatic adjustments to maintain optimal operational parameters during fluctuating load conditions.
Industry-Specific Applications
The versatility of Customized Turbine Pair Parts manifests through their problem-solving capabilities across multiple sectors:
Aerospace Propulsion Systems:Next-generation turbofan engines utilize variable-geometry stator vanes that automatically adjust angles to maintain efficiency across diverse flight conditions, significantly reducing fuel consumption during long-haul operations.
Renewable Energy Integration:Compressed air energy storage systems employ turbine pairs capable of rapid transition between generation and compression modes, achieving high round-trip efficiency through optimized blade profiles that minimize energy losses during flow reversal.
Marine Power Solutions:Turbine pairs designed for marine environments incorporate erosion-resistant materials to handle particulate-laden flows while withstanding saltwater corrosion, ensuring reliable performance in offshore energy applications.
Measurable Performance Enhancements
Technological advancements in turbine pair customization yield quantifiable operational improvements:
Efficiency Improvements:Aerodynamically tuned wind turbine pairs demonstrate increased energy capture in low-wind conditions through optimized lift-to-drag ratios that enhance torque generation at sub-optimal wind speeds.
Maintenance Cycle Extension:Advanced erosion protection systems on steam turbine pairs have significantly extended inspection intervals in high-velocity environments by dramatically reducing wear rates from particulate impact.
Emissions Reduction:Precision-engineered gas turbine pairs achieve substantial reductions in harmful emissions through optimized combustion gas temperature control, helping energy producers meet stringent environmental regulations.
Implementation Considerations
Successful deployment of Customized Turbine Pair Parts requires addressing inherent engineering challenges:
Vibration Management:Advanced mass-balancing techniques and vibration damping systems prevent destructive resonance in high-speed turbine applications, ensuring reliable operation across diverse rotational regimes.
Thermal Stress Mitigation:Innovative coating technologies with graduated material properties help manage thermal expansion differentials between turbine components, preventing stress-related failures in extreme temperature environments.
Manufacturing Precision:State-of-the-art machining and additive manufacturing techniques enable production of complex geometries with micron-level tolerances, ensuring perfect aerodynamic alignment in critical applications.
Emerging Technological Frontiers
Cutting-edge developments promise to redefine Customized Turbine Pair capabilities:
Self-Repairing Surface Technologies:Experimental coatings containing microencapsulated healing agents demonstrate potential for automatic erosion damage repair during turbine operation, currently undergoing validation in high-wear environments.
Adaptive Morphing Structures:Pioneering designs incorporating smart materials enable real-time blade geometry adjustments, optimizing efficiency across variable flow conditions in next-generation energy systems.
Predictive Maintenance Integration:Advanced monitoring platforms combine operational data with machine learning algorithms to predict component lifespan with unprecedented accuracy, revolutionizing maintenance scheduling practices.
Customized Turbine Pair Parts supplier
As global energy demands escalate and sustainability requirements intensify, Customized Turbine Pair Parts evolve from static components into intelligent energy conversion systems. Their ability to combine precision engineering with adaptive functionality ensures turbine technology will continue breaking efficiency barriers while maintaining the reliability required in critical power generation and propulsion applications. Through continuous innovation in materials science and manufacturing techniques, these specialized components remain at the forefront of efforts to optimize energy conversion processes across industries.
LYRA Drive is a professional slewing bearings ,slew drive and gears manufacturer provides customized slew bearing, drive and gears.For application-specific engineering solutions, contact LYRA to discuss technical specifications and implementation strategies.