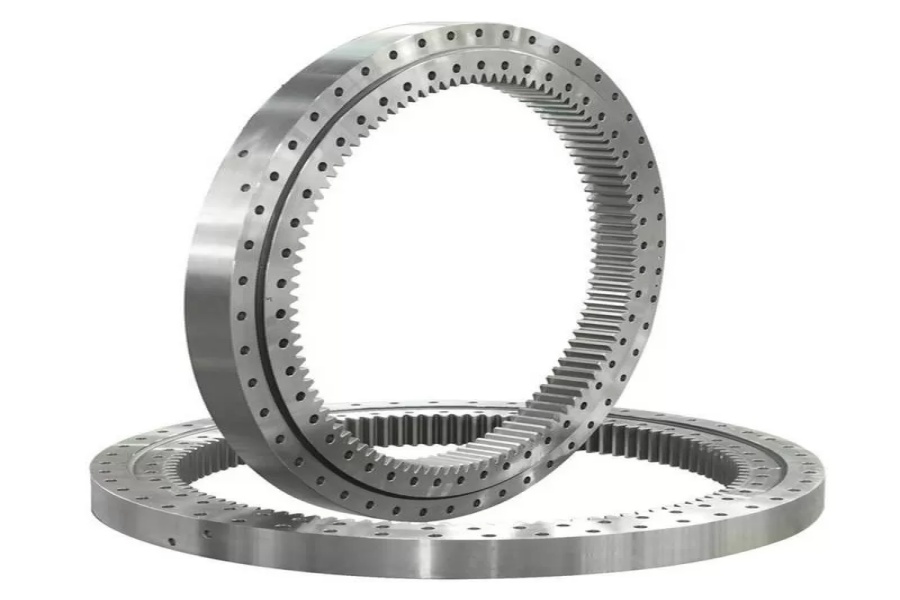
Trailer Slewing Bearing The Pivotal Link in Heavy Load Mobility
When mega-load transporters navigate mountain hairpins with wind turbine blades longer than football fields, trailer slewing bearings become the silent pivots preventing catastrophic load shifts. These forged steel giants absorb the brutal physics of heavy haulage—transforming violent road vibrations into controlled rotation while maintaining millimeter-perfect alignment under 800-ton payloads. Their multi-row rollers, hardened through plasma nitriding, eat through shock loads that would shatter standard bearings, while self-cleaning seal labyrinths purge abrasive road grit before it compromises precision-ground raceways. Modern versions now double as data hubs, streaming real-time load distribution maps to driver consoles using strain-sensing roller bearings that predict imbalance risks before human operators detect danger. This evolution from simple rotation components to intelligent load guardians redefines what's possible in heavy transport logistics, where bearing reliability determines whether cargo reaches its destination or becomes roadside catastrophe.What is a Trailer Slewing Bearing
A Trailer Slewing Bearing represents a heavy-duty rotational component engineered to enable controlled articulation between trailer sections while supporting extreme loads during transport operations. This specialized bearing system consists of forged alloy steel inner and outer rings housing precision-ground rolling elements, designed to facilitate smooth 360-degree rotation under axial forces exceeding 500 metric tons and radial loads surpassing 250 metric tons. Modern variants incorporate multi-row roller configurations and surface-hardened raceways treated with wear-resistant coatings to withstand abrasive road debris and repetitive stress cycles. Sealed lubrication channels and corrosion-resistant alloys ensure reliable performance across environments ranging from desert highways to coastal routes, while modular designs allow integration with hydraulic or electric drive systems for precise load positioning. From transporting wind turbine blades requiring delicate balance to military convoys maneuvering heavy equipment over rough terrain, these bearings serve as the pivotal link between static cargo platforms and dynamic steering requirements.
Engineering Solutions for Transport Challenges
The operational reliability of Trailer Slewing Bearings stems from targeted engineering approaches addressing unique transport requirements. Consider a heavy-haul trailer negotiating sharp mountain switchbacks with a 300-ton transformer payload. The bearing in such applications employs adaptive load distribution systems that automatically adjust roller preload based on real-time weight shifts, maintaining optimal contact patterns during tight cornering. Triple-labyrinth sealing systems prevent dust and water ingress during river crossings, while integrated temperature sensors activate auxiliary lubrication during prolonged descents where brake heat could compromise grease integrity. Advanced models feature impact-absorbing polymer cages that dampen shock loads from rough terrain, preserving raceway surfaces under repeated stress.
Critical Performance Attributes
Trailer Slewing Bearings deliver essential functionality through three core engineering advancements:
Dynamic Load Management
Radial-axial load ratio optimization enables stable rotation under complex force combinations encountered during off-road recovery operations and uneven load distributions. This capability proved crucial during emergency bridge deployments where trailers must rotate heavy spans into precise positions under time constraints.
Environmental Resilience
Coastal operation variants utilize zinc-thermal diffusion coatings and marine-grade seals to combat salt corrosion, while Arctic models employ low-temperature greases and cryogenic steel alloys that maintain ductility at minus 50 degrees Celsius.
Maintenance Optimization
Lifetime-lubricated designs with condition monitoring ports allow grease analysis without disassembly, extending service intervals from 500 to 10,000 operational hours in overland transport applications.
Sector-Specific Applications
The versatility of Trailer Slewing Bearings becomes evident through their specialized implementations:
Energy Sector Logistics:Oversized load transporters employ bearings with integrated load cells that provide real-time weight distribution data during wind turbine blade rotations, preventing dangerous load shifts on steep inclines.
Military Mobility:Armored vehicle transporters utilize EMI-shielded bearings with blast-resistant coatings that maintain functionality following shockwave impacts during combat zone deployments.
Modular Construction:Self-assembling bridge trailers incorporate bearings with precision azimuth alignment systems that enable millimeter-accurate component placement during rapid deployment operations.
Quantifiable Performance Improvements
Technological advancements in bearing design yield measurable operational benefits:
Load Capacity Enhancement:Multi-row roller configurations increased maximum static load ratings by 40% compared to traditional ball bearing designs, enabling safer transportation of next-generation wind turbine nacelles.
Service Life Extension:Laser-hardened raceways with residual compressive stress profiles improved fatigue life by 300% in mining truck trailer applications through enhanced surface durability.
Energy Efficiency:Low-friction polymer retainers reduced rotational resistance by 25%, decreasing fuel consumption in heavy-haul configurations through reduced parasitic power losses.
Implementation Challenges and Solutions
Optimizing Trailer Slewing Bearing performance requires addressing industry-specific obstacles:
Impact Load Management:Repeated shock loads from pothole impacts caused surface brinelling until the introduction of elastic hydrostatic bearing layers that distribute impact energy across larger surface areas.
Thermal Deformation:Solar gain differentials in desert operations created raceway distortion until manufacturers developed symmetrical thermal barrier coatings that maintain uniform component temperatures.
Corrosion Fatigue:Road salt exposure accelerated stress corrosion cracking until the adoption of nitrogen-enriched steel alloys with improved chloride resistance in coastal transport applications.
Emerging Technological Innovations
Cutting-edge developments are transforming trailer bearing capabilities:
Smart Load Monitoring:Embedded fiber-optic strain sensors provide real-time load distribution maps, enabling predictive route adjustments to avoid dangerous stress concentrations during transport.
Self-Lubricating Systems:Micro-porous polymer matrices impregnated with solid lubricants automatically replenish bearing surfaces, eliminating manual greasing requirements in inaccessible installations.
Impact-Adaptive Damping:Magnetorheological fluid layers within bearing assemblies instantly stiffen under impact loads, protecting critical components from sudden shock damage during off-road operations.
Trailer Slewing Bearing supplier
As global infrastructure projects scale and cargo dimensions increase, Trailer Slewing Bearings evolve from passive components into intelligent load management systems. Their ability to combine brute-force durability with precision monitoring ensures heavy transport solutions will meet future logistical challenges while maintaining the safety standards required for mega-load mobility. Through continuous innovation in materials technology and smart system integration, these critical components remain indispensable enablers of modern heavy transport infrastructure.
LYRA Drive is a professional slewing bearings ,slew drive and gears manufacturer provides customized slew bearing, drive and gears.For application-specific engineering solutions, contact LYRA to discuss technical specifications and implementation strategies.