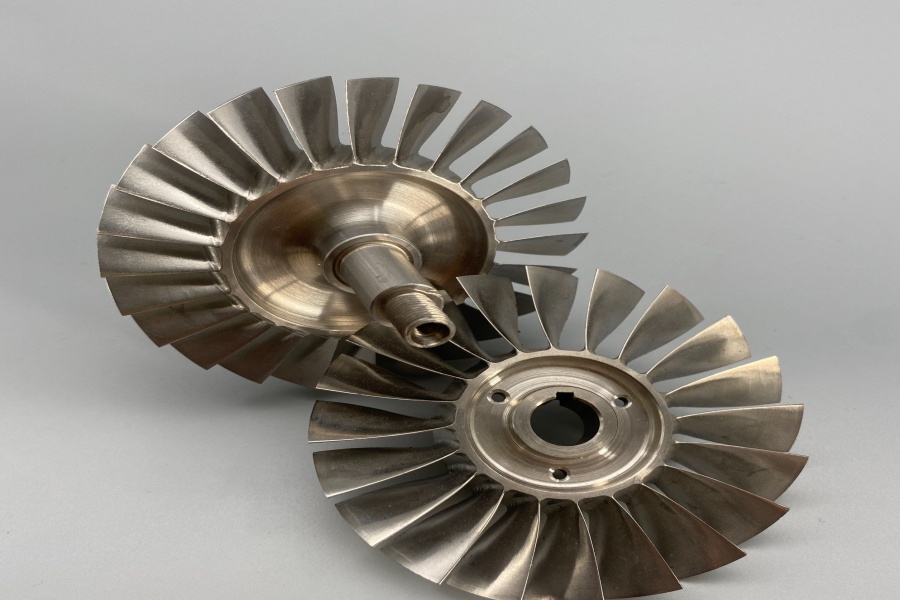
Customized Turbine Pair Parts The Engine of Industrial Progress and Innovation
In the dynamic world of industrial machinery and energy systems, turbines stand as pivotal assets, converting kinetic energy into power that drives entire sectors. At the core of their efficiency and reliability lie customized turbine pair parts, specialized components engineered to meet the exacting demands of modern applications. These bespoke elements ensure turbines operate at peak performance, whether propelling aircraft, generating electricity in power plants, or harnessing wind energy. As industries push for higher efficiency, reduced environmental impact, and smarter operations, the role of customized turbine pair parts has become central to innovation, bridging the gap between mechanical prowess and technological advancement.
What Are Customized Turbine Pair Parts
Customized turbine pair parts refer to precision-engineered components designed in matched sets to optimize the interaction between rotating and stationary elements within a turbine system. These parts include critical assemblies such as blade-disc pairs, seal rings, and shaft-bearing units, each tailored to withstand specific operational stresses like high temperatures, pressure differentials, and rotational speeds. The blade-disc pair, for instance, is meticulously balanced to minimize vibrational harmonics, while seal rings are crafted from advanced alloys to prevent gas leaks in high-pressure environments. Such components are often manufactured using computer-aided design (CAD) tools that simulate real-world conditions, ensuring compatibility and longevity even in extreme settings.
The importance of these parts stems from their ability to enhance turbine efficiency and durability. In gas turbines used for power generation, customized pairs reduce energy losses caused by friction or misalignment, directly improving fuel efficiency and lowering emissions. In aviation, turbine engines rely on precisely matched components to maintain thrust consistency and safety at altitudes where mechanical failure is not an option. Renewable energy sectors also benefit, as wind turbine pairs optimized for specific wind profiles maximize energy capture while reducing wear. By addressing the unique challenges of each application, customized turbine pair parts enable industries to achieve operational excellence and meet evolving regulatory standards.
Global Innovations Shaping the Future of Turbine Pair Components
Breakthroughs in Materials and Manufacturing
Nations with advanced engineering ecosystems, such as the United States, Germany, and Japan, lead the charge in developing next-generation turbine pair parts. Innovations in single-crystal superalloys have revolutionized high-temperature components, allowing turbines to operate at unprecedented thermal efficiencies without succumbing to creep or oxidation. Additive manufacturing, or 3D printing, enables the production of complex geometries—such as internally cooled turbine blades—that traditional methods cannot replicate, significantly enhancing heat dissipation and lifespan.
The aerospace sector exemplifies these advancements, where turbine discs and blades are now coated with thermal barrier coatings (TBCs) using plasma spray techniques. These coatings insulate metal components from scorching exhaust gases, enabling engines to run hotter and cleaner. Similarly, the energy sector has adopted ceramic matrix composites (CMCs) for seal rings and shrouds, materials that retain strength at temperatures where conventional metals would fail. Such innovations are supported by rigorous testing protocols, including computational fluid dynamics (CFD) simulations that predict airflow dynamics and stress distribution across customized pairs.
Emerging Economies Accelerating Technological Adoption
While established markets dominate high-precision manufacturing, emerging industrial hubs are making strides by integrating automation and digital twin technologies. Countries investing in AI-driven predictive maintenance systems can now anticipate component wear in turbines, reducing unplanned downtime in power plants and industrial facilities. For example, manufacturers in these regions utilize sensor-equipped turbine pairs to monitor real-time performance metrics, enabling proactive replacements before failures occur.
Challenges remain, however, in mastering tolerance-critical machining and proprietary material formulations. Global leaders often employ proprietary alloys and finishing techniques—such as laser peening to enhance surface durability—that are less accessible in developing markets. Additionally, the integration of embedded sensors for smart diagnostics requires expertise in both hardware and data analytics, areas where workforce upskilling is still ongoing.
Overcoming Barriers in Customized Turbine Pair Production
The disparity between leading and emerging markets hinges on three pillars: material accessibility, precision engineering, and digital integration. High-performance turbine pairs from top-tier manufacturers leverage powder metallurgy and hot isostatic pressing (HIP) to eliminate material defects, ensuring uniformity under stress. In contrast, reliance on conventional metallurgy in some regions results in components prone to microfractures under cyclic loading, particularly in applications like steam turbines or industrial compressors.
Collaborative initiatives between universities and industry players aim to close this gap. Research into hybrid manufacturing techniques—combining additive and subtractive processes—promises to reduce material waste while achieving the tight tolerances required for aerospace-grade parts. Another focus area is blockchain-enabled supply chains, which enhance traceability of raw materials like cobalt and nickel, critical for alloy consistency. These efforts are complemented by training programs that equip engineers with skills in advanced CNC machining and IoT-enabled quality assurance systems.
The Future of Turbine Pair Parts Intelligence Meets Sustainability
The next evolution of customized turbine pair parts will prioritize energy-efficient designs, self-optimizing systems, and circular economy principles. Engineers are experimenting with active clearance control technologies that adjust seal gaps in real time during turbine operation, minimizing leakage and boosting efficiency. Sustainability initiatives drive the adoption of recyclable turbine blades made from bio-resins and carbon fibers, reducing the environmental impact of decommissioned components.
In smart industrial ecosystems, turbine pairs will function as integrated data nodes. For instance, a power plant could use AI algorithms to analyze vibration data from turbine shafts, automatically adjusting operational parameters to balance loads and extend component life. Wind farms might deploy pairs equipped with shape-memory alloys that adapt blade angles based on real-time wind shear data, maximizing output while minimizing structural fatigue.
Customized turbine pair parts supplier
Customized turbine pair parts embody the intersection of mechanical excellence and technological innovation. As global industries strive for greener and smarter operations, these components will remain indispensable in achieving performance benchmarks. While technological leaders continue to pioneer cutting-edge materials and digital solutions, emerging markets demonstrate that agility and strategic investments can narrow the innovation divide. The future lies not only in crafting stronger or faster turbine parts but in embedding intelligence and sustainability into their very design. For industries and engineers, embracing these advancements will be crucial to powering a world where efficiency and environmental stewardship go hand in hand.
LYRA Drive is a professional Customized turbine pair parts,slewing bearings,slew drive and gears manufacturer provides customized slew bearing, drive and gears.For application-specific engineering solutions, contact LYRA to discuss technical specifications and implementation strategies.