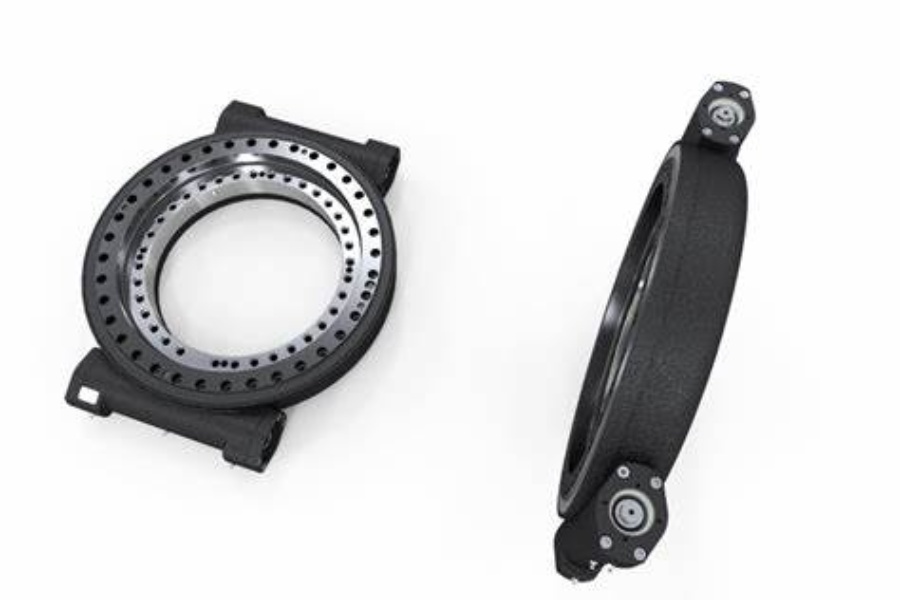
High-Performance Slew Drives Global Innovations and the Road Ahead
In today’s industrial landscape, machinery demands components that deliver strength, precision, and adaptability. Among these, the slew drive stands out as a critical enabler of rotational motion, powering everything from construction equipment to renewable energy systems. This unassuming yet vital device ensures that heavy loads rotate smoothly and accurately, even under extreme stress. As industries worldwide embrace automation and smarter technologies, the evolution of high-performance slew drives has become a focal point for engineers and manufacturers aiming to push the boundaries of efficiency and reliability.
What Is a Slew Drive and Why Does It Matter?
A slew drive is a compact mechanical system engineered to provide controlled rotational movement while supporting significant axial, radial, and moment loads. Its design integrates three core elements: a worm gear mechanism for torque amplification and speed reduction, a slewing bearing to handle multidirectional forces, and a motor that drives the entire assembly. The worm gear’s helical teeth mesh with the worm shaft to transmit motion at precise angles, enabling high torque output with minimal energy loss. Meanwhile, the slewing bearing—constructed from hardened steel and precision-machined rolling elements—ensures smooth rotation under heavy loads or uneven pressure.
What makes modern slew drives indispensable is their ability to merge power and precision within tight spaces. For example, in wind turbines, these drives adjust blade angles to optimize energy capture as wind conditions shift. In construction cranes, they enable 360-degree rotation of booms, lifting tons of materials with pinpoint accuracy. Solar tracking systems rely on them to tilt panels throughout the day, maximizing sunlight exposure. Even industrial robots depend on slew drives for repetitive tasks requiring exact positioning. Their modular architecture allows customization for specific load capacities, rotational speeds, and environmental challenges, making them versatile across industries.
Cutting-Edge Developments in Slew Drive Technology Worldwide
Breakthroughs in Precision and Durability
Nations with deep-rooted expertise in mechanical engineering, such as Germany and Japan, continue to lead in high-end slew drive innovation. German manufacturers leverage laser-hardened gear surfaces and zero-backlash designs to achieve unparalleled efficiency and longevity. These advancements stem from decades of refining gear-tooth profiles and adopting computerized quality control systems that detect micron-level deviations during production.
In aerospace, slew drives are mission-critical for satellite positioning mechanisms, where failure could mean losing a multi-million-dollar asset. Foreign-engineered units incorporate ceramic-coated components and vacuum-rated lubricants to endure the harsh conditions of space, including extreme temperatures and radiation. Similarly, the automotive sector benefits from ultra-compact drives embedded in robotic arms, which assemble vehicle parts with sub-millimeter precision. Such innovations are underpinned by breakthroughs in materials science, such as lightweight alloys that reduce inertia without compromising strength.
Emerging Markets Rising to the Challenge
While established players dominate the premium segment, manufacturers in rapidly industrializing regions are making significant strides. Investments in automated production lines and advanced metallurgy have enabled local producers to offer cost-effective slew drives with performance metrics rivaling mid-tier international models. For instance, some now provide drives capable of handling dynamic loads in construction machinery or agricultural equipment, backed by improved sealing technologies that resist dust and moisture ingress.
However, gaps remain in mastering high-torque density designs and adaptive control systems. Foreign competitors often integrate proprietary algorithms that optimize motor performance in real time, adjusting torque output based on load fluctuations. Domestic solutions, while functional, may lack the same responsiveness, particularly in applications requiring rapid acceleration or sudden directional changes. Additionally, achieving consistent reliability in corrosive environments—such as offshore installations or mining sites—remains a challenge due to limited access to advanced anti-corrosion coatings and composite materials.
Key Challenges in Closing the Technology Gap
The divide between global leaders and emerging manufacturers centers on three areas: material science, manufacturing precision, and smart integration. High-performance alloys and polymer composites used abroad enhance load-bearing capacity and reduce wear, whereas reliance on conventional steels locally can lead to premature fatigue under cyclic stresses. Similarly, the absence of embedded IoT sensors in many domestic products limits their appeal to industries prioritizing predictive maintenance and data-driven optimization.
To bridge this gap, collaborative efforts between research institutions and manufacturers are accelerating. Projects focus on 3D-printed gear prototypes for custom geometries and machine learning algorithms that predict component wear based on operational data. These innovations aim to create self-monitoring slew drives capable of alerting operators to potential failures before they occur, minimizing downtime in critical applications.
The Future of Slew Drives Efficiency Meets Intelligence
The next wave of slew drives will prioritize energy-efficient designs, modular scalability, and seamless digital integration. Engineers are exploring magnetic levitation techniques to eliminate mechanical contact in bearings, drastically cutting friction and maintenance needs. Meanwhile, sustainability initiatives are driving the adoption of bio-based lubricants and recyclable polymer housings, aligning with global green manufacturing trends.
In smart factories, slew drives equipped with wireless connectivity will feed real-time performance metrics into centralized systems, enabling predictive analytics and remote diagnostics. This shift toward intelligent systems aligns with Industry 4.0’s vision of interconnected machinery that adapts autonomously to operational demands. For example, a solar farm could use data from slew drives to optimize panel angles based on weather forecasts, boosting energy output without human intervention.
Slew drives supplier
Slew drives may not grab headlines, but their role in modern machinery is irreplaceable. As global industries demand higher efficiency, smarter controls, and greener solutions, innovation in this field will remain relentless. While technological leaders continue to set benchmarks with cutting-edge materials and digital integration, emerging markets are proving that agility and targeted R&D can narrow the gap. The future promises slew drives that are not just stronger and more precise but also integral to building sustainable, adaptive industrial ecosystems. For businesses and engineers, staying competitive will hinge on embracing change, investing in innovation, and understanding that even the smallest components can drive the biggest transformations.
LYRA Drive is a professional slewing bearings ,slew drive and gears manufacturer provides customized slew bearing, drive and gears.For application-specific engineering solutions, contact LYRA to discuss technical specifications and implementation strategies.