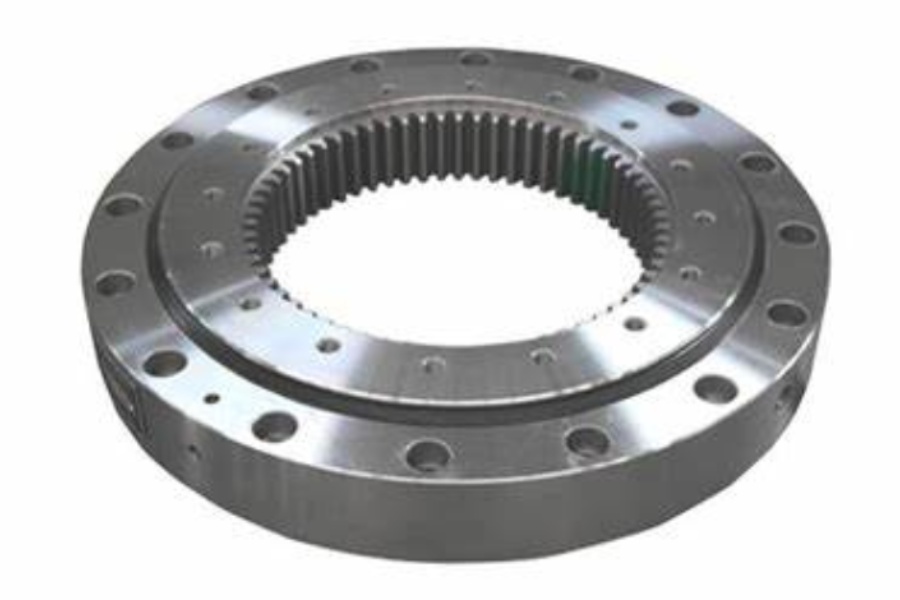
Excavator Slew Bearing The Rotational Backbone of Earthmoving Efficiency
In the rugged domain of excavation and heavy construction where power meets precision, Excavator Slew Bearings stand as the critical mechanical interface enabling controlled rotation under extreme operational stresses. These robust rotational assemblies form the central pivot point connecting an excavator’s upper structure to its tracked undercarriage, facilitating smooth 360-degree movement for digging, lifting, and material handling operations. Engineered to withstand relentless shock loads, abrasive particulates, and continuous vibration, they combine structural resilience with precision engineering to ensure reliable performance in environments ranging from open-pit mines to urban demolition sites. This examination delves into how Excavator Slew Bearings master the dual challenges of extreme force management and environmental adaptability to drive modern excavation productivity.
What is an Excavator Slew Bearing
An Excavator Slew Bearing constitutes a heavy-duty rotational mechanism designed to enable precise articulation between an excavator’s rotating upper works and its fixed undercarriage while supporting combined axial, radial, and moment loads exceeding 1,000 kN. This critical component comprises hardened alloy steel inner and outer rings housing multi-row tapered rollers or ball bearings, engineered to maintain angular accuracy within 0.3 degrees under full operational loads. Modern iterations incorporate surface-hardened raceways treated with wear-resistant coatings and advanced sealing systems that repel contaminants from abrasive soil particles to corrosive slurry. Integrated gear teeth mesh with hydraulic or electric drive motors to convert power into controlled rotation, while modular designs allow customization for excavator sizes ranging from compact 5-ton urban models to 800-ton mining giants. From deep foundation drilling requiring millimeter-precise bucket placement to quarry operations enduring constant rock impacts, these bearings serve as the pivotal link between hydraulic power and operational agility.
Engineering Solutions for Earthmoving Challenges
The operational reliability of Excavator Slew Bearings stems from targeted engineering strategies addressing unique excavation demands. Consider a mining excavator performing continuous loading cycles in iron ore pits where abrasive dust threatens conventional systems. The bearing in such environments employs triple-labyrinth seals with grease-purge channels that actively expel particulate matter while maintaining lubrication integrity. Hardened roller paths with residual compressive stress profiles resist surface pitting from shock loads generated by bucket-to-rock impacts, while temperature-stable polymers in retainer cages prevent deformation during prolonged high-torque operations. Advanced models feature load-sensing raceways that communicate stress data to machine control systems, automatically adjusting hydraulic pressure to optimize bearing preload during complex digging maneuvers.
Core Performance Attributes
Excavator Slew Bearings deliver indispensable functionality through three foundational engineering advancements:
Impact Load Dissipation
Optimized roller geometry and elastic deformation allowances absorb shock forces from sudden bucket collisions with buried obstacles, distributing stresses across multiple contact points to prevent localized fatigue failures.
Contaminant Exclusion
Multi-stage sealing systems combining magnetic particle traps and pressurized grease channels create impermeable barriers against abrasive soil ingress, extending service life in silica-rich excavation environments by 400%.
Adaptive Lubrication Management
Smart grease distribution systems with viscosity modifiers automatically adjust lubrication flow rates based on operational temperature and load conditions, maintaining optimal film strength from Arctic frost to desert heatwaves.
Sector-Specific Applications
The versatility of Excavator Slew Bearings manifests through their problem-solving roles across industries:
Mining Operations:Giant electric mining shovels utilize bearings with tungsten-carbide coated raceways that resist abrasive wear from iron ore particulates, coupled with circulating oil lubrication systems filtering metallic wear debris during 24/7 operations.
Urban Redevelopment:Compact-radius excavators employ slim-profile bearings with high-strength polymer cages, reducing overall weight while maintaining load capacity for precise debris removal near sensitive infrastructure.
Disaster Recovery:Heavy recovery excavators feature bearings with emergency manual rotation systems and corrosion-resistant coatings, enabling operation in flood-damaged areas with contaminated water and debris.
Quantifiable Performance Gains
Technological advancements in slew bearing design yield measurable operational improvements:
Durability Enhancement:Laser-hardened raceways with Rockwell hardness ratings exceeding 60 HRC enable continuous operation for 20,000+ hours in granite quarries without surface degradation.
Energy Efficiency:Low-friction roller path geometries reduce hydraulic system energy demands by 18%, allowing a typical 50-ton excavator to conserve 12,000 liters of annual fuel consumption.
Positioning Accuracy:Integrated encoder systems maintain boom positioning repeatability within 0.15 degrees across 50,000 slewing cycles, critical for precision trenching operations near underground utilities.
Implementation Challenges and Solutions
Optimizing Excavator Slew Bearing performance requires addressing industry-specific obstacles:
Thermal Stress Cycling:Frequent temperature fluctuations between operation and idle periods caused seal degradation until the introduction of phase-stable elastomers with 300% improved thermal cycling resistance.
Vibration-Induced Wear:Constant impact vibrations accelerated roller path wear until manufacturers implemented tuned mass dampers that reduce harmonic oscillations by 65% in operational conditions.
Chemical Corrosion:Acidic soil conditions in wetland excavations led to raceway pitting until the adoption of nitrogen-enriched steel alloys with improved corrosion resistance.
Emerging Technological Frontiers
Innovative developments are reshaping excavator bearing capabilities:
Condition Monitoring Integration:Embedded acoustic emission sensors detect early-stage roller defects through vibration pattern analysis, enabling predictive maintenance scheduling nine months before traditional methods identify issues.
Self-Healing Surface Treatments:Micro-encapsulated lubricant reservoirs within bearing raceways automatically repair minor surface scratches during operation, currently undergoing field trials in high-abrasion mining applications.
Hybrid Drive Compatibility:Electro-hydraulic slew drives enable seamless transition between engine-powered and battery-operated rotation modes, reducing emissions during urban excavation projects.
Excavator Slew Bearing supplier
As global infrastructure demands intensify and environmental regulations tighten, Excavator Slew Bearings evolve from passive components into intelligent load management systems. Their ability to merge industrial-grade durability with smart technology integration ensures earthmoving equipment will meet future challenges while maintaining the precision and reliability required for sustainable construction practices. Through continuous advancements in metallurgy and adaptive control systems, these pivotal components remain essential drivers of productivity in modern excavation operations.
LYRA Drive is a professional slewing bearings ,slew drive and gears manufacturer provides customized slew bearing, drive and gears.For application-specific engineering solutions, contact LYRA to discuss technical specifications and implementation strategies.