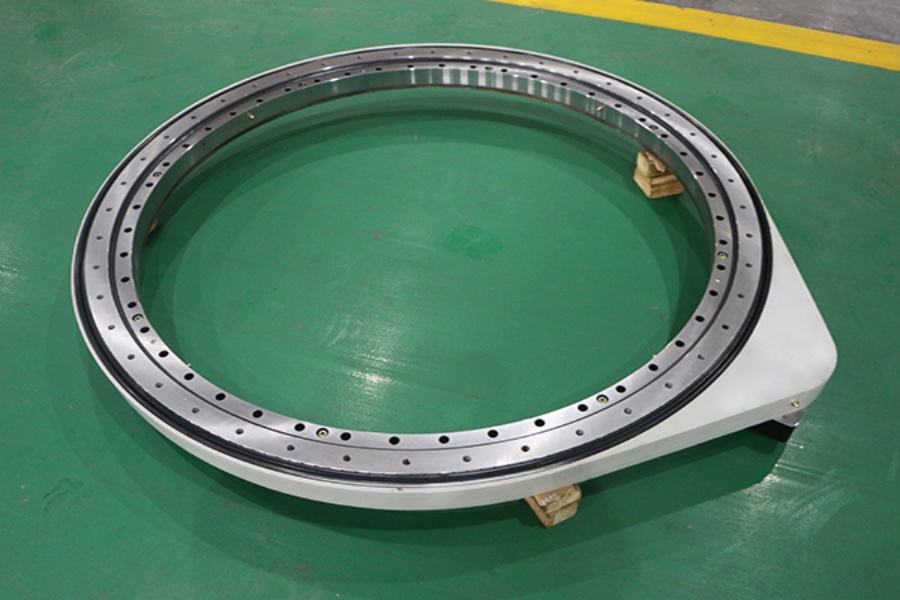
What is Spur Gear Slew Drive
What is Spur Gear Slew Drive?
A spur gear slew drive is a mechanical system that combines a spur gear (a straight-toothed gear) with a slewing ring bearing to enable controlled rotational movement in machinery. Unlike worm gears, which use a screw-like gear, spur gears have teeth parallel to the gear’s axis, making them simpler in design and more efficient for high-speed, low-torque applications. The spur gear meshes directly with the slewing ring’s gear teeth, translating rotational force from a motor or hydraulic system into smooth, precise rotation. These drives are known for their straightforward construction, ease of maintenance, and ability to handle moderate loads efficiently. Think of them as the "workhorses" of rotational systems—reliable, no-nonsense, and perfect for scenarios where simplicity and speed matter more than extreme torque or self-locking features.
Types of Spur Gear Slew Drives
Spur gear slew drives come in several configurations tailored to specific industrial needs. The standard spur gear slew drive is the most common, featuring a single spur gear paired with a slewing ring, ideal for general-purpose applications like rotating platforms or conveyor systems. For heavier loads, the double spur gear slew drive incorporates two spur gears working in tandem, doubling the torque capacity while maintaining efficiency, often used in construction equipment or material handling systems. Hollow shaft spur gear slew drives include a central opening to route cables, hydraulic lines, or shafts, making them popular in robotics or automated machinery where internal wiring is essential. Sealed spur gear drives are built with robust gaskets or shields to protect against dust, water, and debris, perfect for outdoor or harsh environments like agricultural machinery or marine equipment. Lastly, precision spur gear slew drives are engineered with ultra-fine teeth and minimal backlash for applications requiring exact positioning, such as medical imaging devices or optical tracking systems.
Key Features of Spur Gear Slew Drives
Spur gear slew drives stand out for their high efficiency, typically achieving 95–98% energy transfer due to the direct meshing of straight-cut teeth, which minimizes friction compared to angled gears like helical or worm designs. Their simplified construction reduces manufacturing costs and makes maintenance straightforward, as components are easy to access and replace. These drives excel in high-speed applications, where their ability to handle rapid rotation without overheating or excessive wear is a major advantage. While they lack the self-locking capability of worm gears, spur gear drives compensate with smooth, consistent performance under continuous operation. Durability is another hallmark, with hardened steel gears and precision-machined raceways ensuring longevity even in demanding conditions. Customization options, such as varying gear ratios, mounting configurations, and material choices (e.g., stainless steel for corrosion resistance), allow these drives to adapt to diverse industrial needs.
Applications of Spur Gear Slew Drives
Spur gear slew drives are widely used in industries that prioritize speed, efficiency, and reliability over extreme torque. In manufacturing automation, they power rotary tables and assembly line robots that require precise, repetitive motion. Packaging machinery relies on them for rotating conveyor belts or filling stations, where consistent speed is critical. The renewable energy sector employs these drives in solar tracking systems to adjust panel angles efficiently throughout the day. Agricultural equipment, such as irrigation systems or grain augers, benefits from their rugged design and ability to operate in dusty or wet environments. Material handling systems, including warehouse turntables and dock loaders, use spur gear drives for smooth, low-maintenance rotation. Even entertainment industries leverage them in stage machinery or rotating displays, where quiet operation and reliability are essential.
Price Range
The cost of spur gear slew drives varies based on size, complexity, and customization. Entry-level models for light-duty applications, such as small conveyor systems, start around 1,000–3,000. Mid-range drives for industrial machinery, like packaging equipment or agricultural tools, typically range from 5,000–15,000, depending on torque ratings and material quality. High-end models, such as precision drives for medical imaging or large-scale solar trackers, can cost 20,000–50,000+, especially when incorporating advanced materials like stainless steel or custom gear ratios. Factors influencing price include gear size (larger diameters increase cost), manufacturing tolerances (tighter precision demands higher prices), and environmental protections (seals or coatings add 10–30% to the base price). Bulk orders or long-term supplier contracts may reduce per-unit costs by 10–20%.
Lifespan of Spur Gear Slew Drives
The lifespan of a spur gear slew drive hinges on usage intensity, maintenance practices, and environmental conditions. In light-duty applications like solar trackers or stage machinery, these drives can last 15–20 years with minimal upkeep. Industrial settings, such as manufacturing or agriculture, typically see lifespans of 8–12 years, assuming regular lubrication and load management. Harsh environments—think mining equipment or marine applications—may reduce longevity to 5–8 years due to exposure to abrasives, moisture, or extreme temperatures. Key factors affecting lifespan include proper alignment during installation (misalignment accelerates wear), lubrication quality (using high-viscosity grease for heavy loads), and avoiding overloading (operating above 80% of rated capacity strains components). Sealed drives generally outlast open designs in dirty or wet conditions, as contaminants are less likely to infiltrate the gear teeth.
How to Choose the Right Spur Gear Slew Drive
Selecting the ideal spur gear slew drive requires a balance of technical specs and real-world needs. Start by calculating torque and speed requirements—spur gears excel in high-speed, moderate-torque scenarios, so ensure your application doesn’t demand the extreme torque of a worm or planetary gear system. Next, evaluate environmental conditions: opt for sealed drives with corrosion-resistant coatings if operating outdoors, in marine settings, or in dusty factories. For precision tasks like medical imaging or optical systems, prioritize drives with low backlash (under 10 arc-minutes) and hardened steel gears to minimize play. Consider mounting and space constraints—hollow shaft designs save space in cramped installations, while flange-mounted units provide stability for heavy loads.
Material choice is critical: carbon steel suits most industrial uses, but stainless steel or bronze gears are better for corrosive environments. Lubrication needs also vary; high-speed applications require low-viscosity grease to reduce friction, while heavy loads demand high-pressure lubricants. When vetting suppliers, check for certifications like ISO 9001 and request load-test reports to verify performance claims. Always factor in total cost of ownership—cheaper drives may save upfront but cost more in repairs and downtime. Finally, test a prototype under real-world conditions to check for noise, heat, or vibration issues before committing to a bulk order.
Common Mistakes to Avoid
One frequent error is ignoring backlash requirements—too much play in the gears causes inaccuracy in precision tasks, while overly tight tolerances increase friction and wear. Another pitfall is mismatching gear materials, such as pairing a steel spur gear with a softer alloy slewing ring, leading to accelerated wear or pitting. Skipping environmental protections in harsh settings (e.g., using open drives in dusty mines) invites contamination and early failure. Overlooking lubrication schedules is equally risky—spur gears rely on consistent greasing to prevent metal-on-metal contact, especially in high-speed applications.
Improper installation—like misaligning the drive or over-tightening mounting bolts—warps components and strains the system. Assuming all spur gear drives are interchangeable is another mistake; a drive designed for solar tracking won’t handle the shock loads of construction equipment. Lastly, prioritizing price over quality often backfires—budget drives may lack hardened gears or precision machining, leading to frequent breakdowns. Always validate supplier claims with third-party testing or customer references.
Spur Gear Slew Drive Supplier
LYRA Drive is a professional slewing bearings ,slew drive, slewdrives and gears manufacturer provides customizedslew bearing, drive and gears.For application-specific engineering solutions, contact LYRA to discuss technical specifications and implementation strategies.