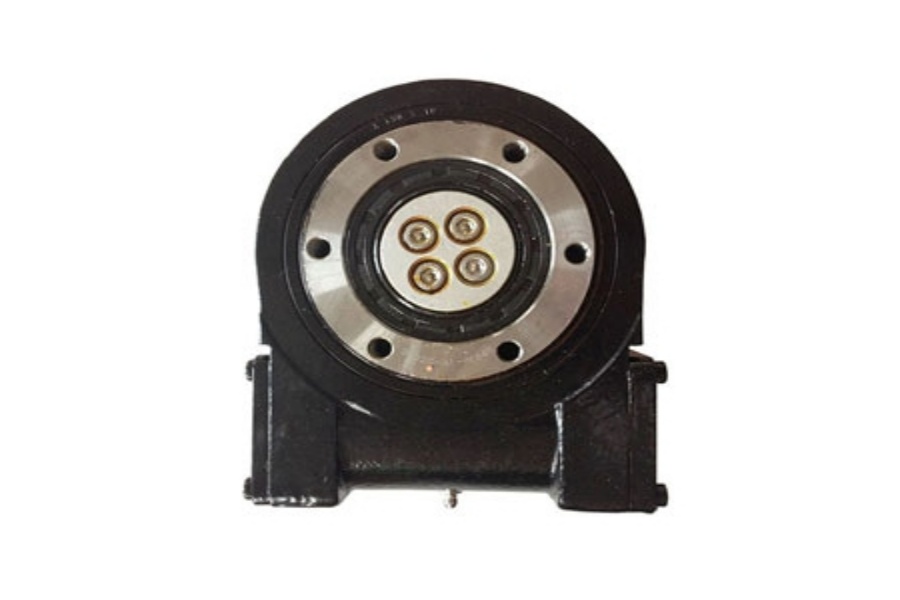
What is SE Slew Drive
What is an SE Slew Drive?
An SE Slew Drive is a specialized rotational mechanism engineered to deliver precise and reliable motion control in heavy-duty applications, integrating a slewing ring bearing with a high-efficiency gear system—commonly a worm or planetary gear setup. The "SE" designation typically signifies a series optimized for specific performance criteria, such as enhanced durability, compact design, or adaptability to extreme environments. These drives are designed to handle combined axial, radial, and moment loads while ensuring smooth 360-degree rotation, making them indispensable in industries like construction, renewable energy, and industrial automation. Unlike generic slew drives, SE models often incorporate advanced sealing technologies, modular components, or custom gear ratios to meet unique operational demands, balancing power and precision for tasks ranging from solar panel tracking to robotic arm positioning.
Types of SE Slew Drives
SE Slew Drives are categorized based on their gear configurations, load capacities, and specialized features. The worm gear SE Slew Drive uses a worm and wheel system to provide self-locking functionality and high torque output, ideal for applications like crane booms or satellite dish positioning where safety and stability are critical. Planetary gear SE Slew Drives, with their compact and efficient gearboxes, excel in high-speed scenarios such as automated assembly lines or medical imaging equipment requiring rapid, precise adjustments. Hollow shaft SE Slew Drives feature a central bore for routing cables or hydraulic lines, making them a preferred choice for robotics or solar trackers where streamlined cable management is essential. For harsh operating environments, sealed SE Slew Drives with IP68 ratings and corrosion-resistant coatings are built to withstand dust, moisture, or chemical exposure, commonly used in offshore drilling rigs or wastewater treatment machinery. Customizable SE Slew Drives offer tailored solutions, such as split housings for easy maintenance or hybrid gear systems combining worm and spur gears to optimize torque and speed for niche applications.
Key Features of SE Slew Drives
SE Slew Drives stand out due to their robust engineering and adaptability. Their precision-ground gears ensure minimal backlash (often under 5 arc-minutes), crucial for applications like radar systems or optical alignment tools where positional accuracy is non-negotiable. The use of high-performance materials—such as case-hardened steel gears and polymer-reinforced seals—enhances wear resistance and extends service life, even under constant heavy loads or temperature extremes. Modular design allows for quick replacement of individual components, reducing downtime during repairs, while integrated sensor ports enable real-time monitoring of parameters like temperature, vibration, and torque, supporting predictive maintenance strategies. Additionally, adaptive lubrication systems ensure optimal grease distribution in both high-speed and low-speed operations, preventing overheating and extending gear life.
Applications of SE Slew Drives
SE Slew Drives are pivotal across industries requiring reliable rotational control under demanding conditions. In renewable energy, they adjust wind turbine nacelles to face changing wind directions or tilt solar panels for maximum sun exposure. Construction equipment such as tower cranes and excavators rely on these drives to rotate booms and platforms smoothly under heavy loads. Aerospace and defense applications include missile launch systems and reconnaissance drone gimbals, leveraging their precision and shock resistance. Marine technology utilizes waterproof SE Slew Drives in shipboard cranes and sonar arrays, while industrial automation integrates them into robotic welding arms and conveyor systems for consistent, repeatable motion. Even medical devices like CT scanners employ low-noise SE Drives to position patients accurately without disrupting sensitive imaging processes.
Price Range
The cost of an SE Slew Drive varies widely depending on size, complexity, and customization. Entry-level models for light industrial use, such as small-scale conveyor systems, start around 2,500–6,000. Mid-range units designed for solar trackers or medium-duty construction machinery typically range from 10,000–25,000, influenced by torque requirements (e.g., 15,000–60,000 Nm) and material upgrades like stainless steel or specialized coatings. High-end custom drives for aerospace, defense, or extreme environments can exceed $60,000, particularly when incorporating features like titanium alloy components, integrated IoT sensors, or explosion-proof housings. Bulk purchasing agreements or long-term partnerships with suppliers may reduce costs by 10–15%, while expedited production or rare material sourcing (e.g., ceramic bearings) can add 20–40% to the price.
Lifespan of SE Slew Drives
The operational lifespan of an SE Slew Drive depends on usage intensity, maintenance practices, and environmental conditions. In moderate applications like solar farms or periodic industrial automation, these drives can operate efficiently for 12–18 years with regular lubrication and alignment checks. Heavy-duty use in 24/7 mining operations or offshore wind turbines typically results in a lifespan of 7–10 years, assuming annual inspections and timely replacement of worn components. Harsh environments—such as saltwater exposure, abrasive dust, or extreme temperature fluctuations—may shorten longevity to 5–7 years, even with advanced sealing systems. Key factors influencing lifespan include adherence to load limits (staying below 85% of maximum capacity), using manufacturer-recommended lubricants, and ensuring precise installation alignment to prevent uneven gear wear.
How to Choose the Right SE Slew Drive
Selecting the ideal SE Slew Drive requires a strategic evaluation of technical and operational needs. Start by calculating load requirements—determine axial, radial, and moment loads using engineering calculations or simulation software, then apply a safety factor of 1.5–2x for dynamic or shock-prone applications. For speed and precision, prioritize planetary gear drives for high-RPM tasks or worm gear models for self-locking safety in vertical load scenarios. Assess environmental challenges: sealed drives with IP68 ratings and corrosion-resistant materials are essential for marine or chemical-heavy settings, while standard models suffice for indoor machinery.
Consider space constraints—compact hollow shaft designs simplify cable routing in tight installations, and flange-mounted units provide stability for heavy equipment. Material selection is critical: carbon steel suits general use, but stainless steel or bronze alloys are better for corrosive or high-temperature environments. Collaborate with suppliers who offer industry-specific expertise (e.g., renewable energy or aerospace) and request certifications like load-test reports or ISO compliance documentation. Finally, evaluate total cost of ownership: a lower upfront cost may lead to higher maintenance expenses, while premium drives with predictive maintenance features reduce long-term operational risks.
Common Mistakes to Avoid
A frequent error is neglecting alignment precision during installation—even minor misalignment can cause uneven gear wear, leading to premature failure. Use laser alignment tools and follow manufacturer torque specifications for mounting bolts. Using incompatible lubricants, such as generic grease instead of high-pressure, temperature-stable variants, accelerates component degradation. Ignoring environmental factors—like deploying unsealed drives in dusty or humid conditions—invites contamination and operational failures.
Mismatching gear materials (e.g., pairing a hardened steel worm with a softer alloy wheel) risks galling and pitting, while overloading the drive beyond 85% of its rated capacity drastically shortens lifespan. Assuming all SE Slew Drives are interchangeable across applications is another pitfall—a drive optimized for slow, high-torque crane operations won’t perform efficiently in high-speed robotics. Lastly, prioritizing initial cost over quality often backfires; budget models may lack hardened gears or precision machining, leading to frequent breakdowns and costly downtime.
SE Slew Drive Supplier
LYRA Drive is a professional slewing bearings ,slew drive, slewdrives and gears manufacturer provides customizedslew bearing, drive and gears.For application-specific engineering solutions, contact LYRA to discuss technical specifications and implementation strategies.