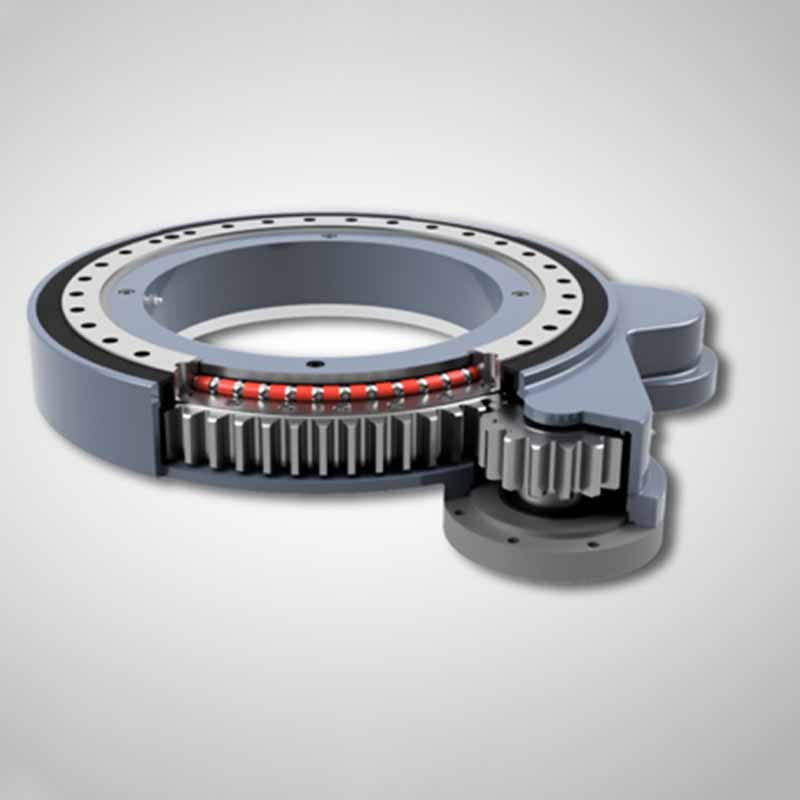
What is slewing drive?
What is slewing drive?
A slewing drive is a ready-to-install unit consisting of a slewing bearing, worm shaft, housing, and sometimes a motor, designed for applications requiring both rotational and axial load-bearing. This device combines the rotational capability of a slewing bearing with the power of a drive system to control movement precisely. Slewing drives are widely used in heavy machinery and equipment that require precise rotational torque and control.
Function of Slewing Drives
Slewing drives are utilized to facilitate and control rotational movement with high torque capabilities. They convert axial movement into a full rotational movement, allowing for controlled, powerful rotation of heavy loads. This is accomplished through the integration of a gear or worm wheel within the slewing bearing, which is driven by an external motor, often an electric or hydraulic motor.
Design Features of Slewing Drives
Integrated Unit: Combines a slewing bearing and a drive mechanism (usually a worm gear) in a compact, enclosed unit. This integration helps in achieving higher torque transmission and greater load capacity.
Gearing: Typically, slewing drives use worm gearing, which allows for high gear ratios and self-locking capabilities, making them ideal for applications requiring precise positioning and safety.
Sealing and Protection: Slewing drives are designed with robust seals to prevent ingress of dirt, dust, and water, ensuring reliable operation in harsh environments.
Motor Integration: They can be equipped with various types of motors (electric, hydraulic) depending on the application requirements. This integration allows for easier control and automation of the system.
Material and Construction: Made from high-grade materials that can withstand environmental and operational stresses, ensuring durability and longevity.
Key Considerations for Slewing Drives
Load Capacity: It is crucial to select a slewing drive that can handle both the axial and radial loads imposed by the application. The unit must also manage the required torque without failure.
Precision and Backlash: The precision of movement and the amount of backlash (play between the teeth of the gears) are important factors, especially in applications requiring very accurate positioning, such as robotics or solar trackers.
Durability and Maintenance: Considering the operational environment and the expected lifespan of the slewing drive, it should be designed for durability with minimal maintenance needs.
Environmental Resistance: The ability to operate under various environmental conditions (temperature extremes, corrosive environments, etc.) should be considered.
Customization and Compatibility: The ability to customize the slewing drive to meet specific requirements and ensure compatibility with other system components is often necessary.
Applications of Slewing Drives
Solar Trackers: Used extensively in solar energy systems to rotate solar panels towards the sun throughout the day, maximizing energy absorption.
Wind Turbines: Controls the angle of the turbine blades and the orientation of the nacelle to optimize wind capture.
Cranes and Manlifts: Provides rotational movement and load-bearing capabilities in the base or the arm of cranes and aerial lifting platforms.
Industrial Machinery: Used in various industrial applications where controlled rotational movement is required, such as robotic arms, turntables, and assembly platforms.