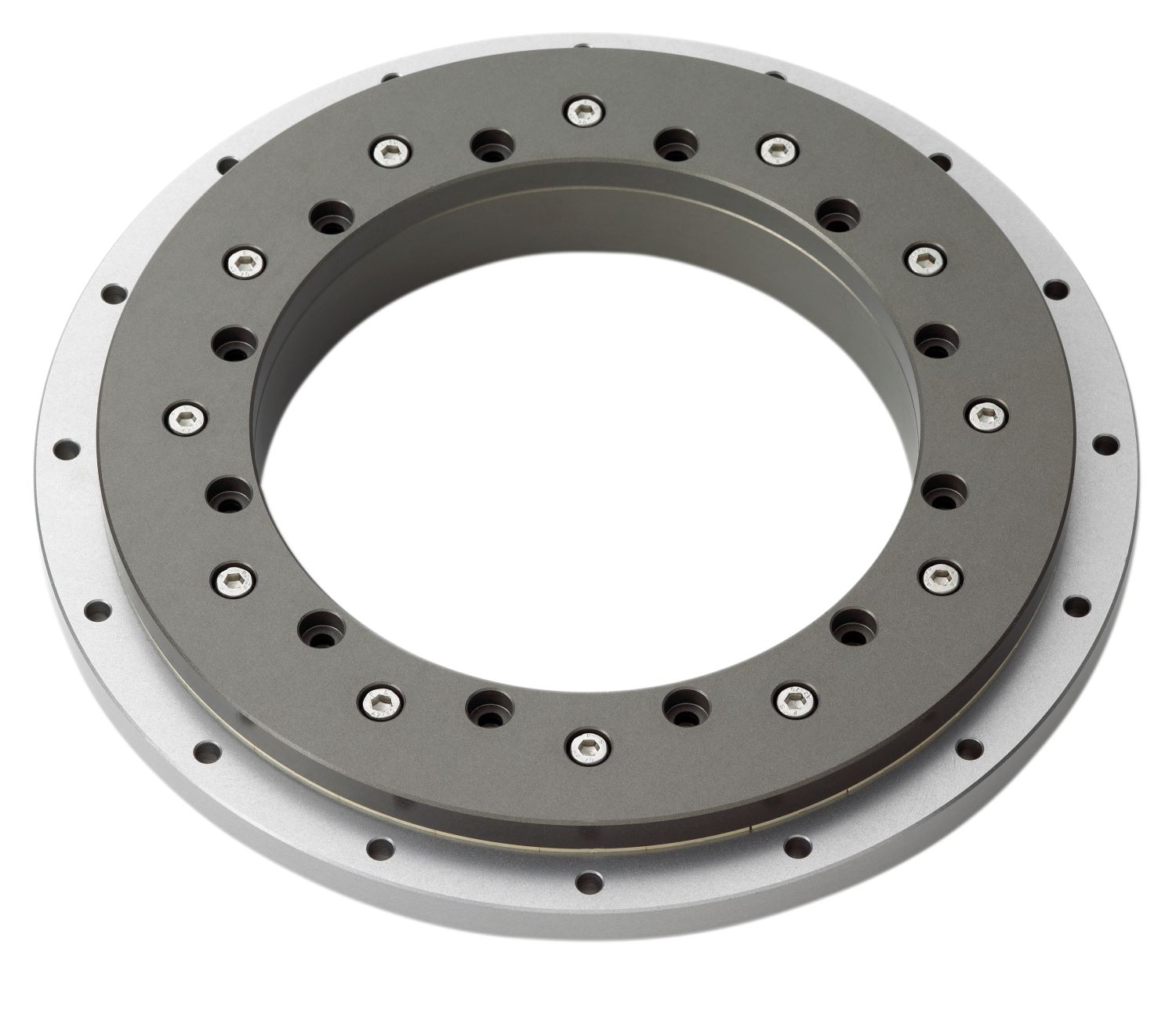
What is a Slew Ring Bearing?
What is a Slew Ring Bearing?
A slew ring bearing (alternately termed slewing ring or turntable bearing) serves as a critical rotational interface in heavy machinery, engineered to facilitate controlled rotation while sustaining complex multi-directional loads. This specialized bearing configuration comprises two concentric rings - an inner and outer race - with precisely arranged rolling elements (balls or rollers) positioned between them. A defining characteristic lies in its integration of mounting features: pre-drilled bolt holes on both rings enable direct mechanical coupling to adjacent structural components, eliminating the need for supplementary housing units.
The bearing's core functionality revolves around three fundamental load management capabilities:
Axial load support: Resisting forces parallel to the rotation axis
Radial load absorption: Counteracting perpendicular forces
Moment load stabilization: Managing rotational torque effects
Modern designs frequently incorporate hardened gear teeth on one raceway circumference, enabling direct meshing with drive pinions for power transmission. This integrated gearing system proves particularly valuable in applications requiring controlled indexing or continuous rotation under load, such as wind turbine yaw systems or industrial robotics.
Types of Slew Ring Bearings
Slew ring bearing variants are differentiated by their internal rolling element configurations, each optimized for specific operational parameters:
Single-Row Four-Point Contact Ball Bearings
Utilizing a single circular array of balls within a Gothic arch raceway profile, this design creates four distinct load transfer points per ball. The angled contact geometry enables simultaneous handling of axial, radial, and moment loads while maintaining a compact cross-section. Typical applications include medium-duty construction equipment and material handling systems.
Featuring two parallel ball tracks, this configuration doubles the load path availability while improving moment load resistance. The separated raceways permit independent optimization of axial and radial load capacities, making it suitable for heavy-duty mining equipment and offshore crane systems.
Crossed Roller Bearings
Characterized by alternating orthogonal roller arrangements, this type achieves exceptional rotational accuracy through line contact geometry. The 90° roller orientation provides inherent moment resistance, particularly effective in precision applications like telescope mounts or robotic welding positioners.
Three-Row Roller Bearings
Combining three distinct roller rows dedicated to specific load types (axial, radial, moment), this heavy-duty solution offers maximum load capacity for ultra-demanding applications such as tunnel boring machines or naval artillery platforms.
Ball-Roller Hybrid Bearings
Merging the low-friction benefits of ball elements with the high-capacity advantages of rollers, this hybrid configuration provides balanced performance in applications requiring both smooth rotation and impact resistance.
Features of Slew Ring Bearings
Modern slew ring bearing designs incorporate several critical performance-enhancing characteristics:
Multi-Load Capacity Architecture: Engineered raceway profiles and heat treatment processes enable simultaneous management of combined loads exceeding conventional bearing capabilities
Space-Efficient Packaging: Large diameter-to-height ratios (often exceeding 30:1) optimize structural integration in space-constrained applications
Precision Rotation Control: Grinding processes achieving raceway surface finishes below 0.8μm Ra ensure smooth, low-vibration operation
Environmental Hardening: Multi-stage sealing systems with specialty grease compatibility protect against particulate ingress and moisture corrosion
Modular Customization: Optional features including sensor mounts, lubrication ports, and custom gear tooth profiles enhance application-specific adaptability
Applications of Slew Ring Bearings
The unique capabilities of slew ring bearings make them indispensable across multiple industrial sectors:
Heavy Construction: Excavator swing mechanisms, crane turntables, and concrete pump truck articulation joints
Renewable Energy: Wind turbine yaw/pitch systems, solar tracker rotation assemblies
Medical Technology: CT scanner gantry drives, radiation therapy positioning systems
Defense Systems: Tank turret drives, missile launch platform azimuth controls
Advanced Manufacturing: Robotic welding cell positioners, automated assembly line indexers
Transportation Infrastructure: Container port crane rotators, railway maintenance platform bases
Price Considerations for Slew Ring Bearings
Cost structures for slew ring bearings reflect complex engineering requirements rather than simple mass production economics. Key pricing determinants include:
Material Specifications: Bearing-grade steel alloys versus corrosion-resistant alternatives
Dimensional Parameters: Diameter scaling impacts material consumption and heat treatment complexity
Precision Classifications: Tolerance levels affecting machining time and quality control protocols
Customization Requirements: Special features like integrated sensors or exotic coatings
Certification Needs: Industry-specific compliance standards (e.g., DNV-GL for maritime applications)
While standard catalog bearings serve general-purpose applications, most industrial implementations require customized solutions balancing performance requirements with budget constraints. For engineered bearing solutions combining optimal load capacity, precision, and lifecycle value, professional consultation ensures technical and economic objectives are effectively aligned.
Slew ring bearings Supplier
Slew ring bearings provide essential rotational load management across heavy industries through optimized geometric configurations, with selection requiring careful analysis of operational demands and environmental conditions. For application-specific engineering solutions, contact LYRA to discuss technical specifications and implementation strategies.