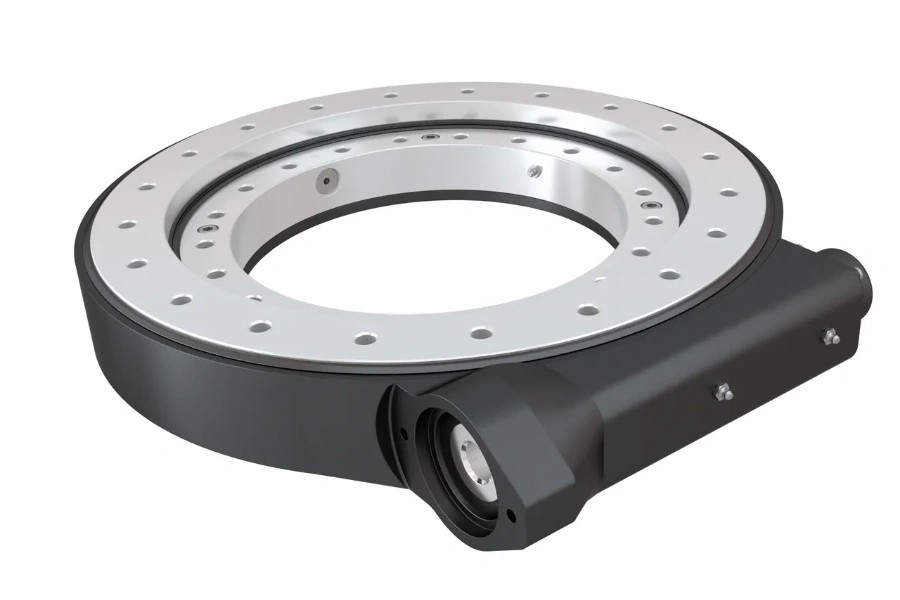
What is a Slew Drive?
What is a Slew Drive?
A Slew drive (also called a slewing drive or slewing ring) is a mechanical component designed to handle rotational movement and axial/radial loads simultaneously. Think of it as a combination of a gearbox and a large bearing – it allows heavy equipment to rotate smoothly while supporting massive weight. It’s commonly used in applications where precise rotation and high load capacity are required, like cranes, solar trackers, or wind turbines. The core parts include a gear (worm, helical, or planetary), a slewing ring (the bearing part), seals, and housings. Unlike regular bearings, slew drives integrate gearing mechanisms to control rotation speed and torque.
Types of Slew Drive
Worm Gears: Affordable, self-locking, but lower efficiency.
Planetary Gears: High efficiency, great for speed and torque.
Helical Gears: Smooth and quiet, ideal for precision.
Cycloidal Gears:
How They Work: Use eccentric cam mechanisms and cycloidal discs to transmit motion.
Pros:
Extreme Durability: Handles shock loads and vibrations better (common in mining or heavy machinery).
High Reduction Ratios: Achieve massive torque in compact sizes (e.g., robotic joints).
Zero Backlash: Critical for ultra-precise motion (medical devices, aerospace).
Cons:
Complex Design: More moving parts = higher manufacturing costs.
Maintenance: Requires specialized knowledge for servicing.
Best For: Harsh environments (e.g., rock crushers), high-precision robotics, or applications needing shock resistance.
Key Features of Slew Drives
Compact Design: Combines rotation and load-bearing functions into a single unit, saving space.
High Load Capacity: Built to handle heavy axial (vertical), radial (sideways), and moment (tilting) loads.
Precision Control: Gear systems enable accurate positioning (e.g., adjusting solar panels by 1° increments).
Durability: Made from hardened steel or alloys to resist wear, corrosion, and extreme temperatures.
Integrated Braking: Many models include brakes to lock rotation under load.
Customizability: Gear ratios, sealing types (for dust/water resistance), and mounting options can be tailored.
Where Are Slew Drives Used?
Construction & Mining: Excavators, cranes, and drilling rigs use slew drives for 360° rotation under heavy loads.
Renewable Energy: Solar trackers tilt panels toward the sun; wind turbines adjust blade pitch.
Robotics: Heavy-duty robotic arms in manufacturing or logistics.
Medical Imaging: MRI machines and CT scanners require smooth, precise rotation.
Defense: Turret systems in military vehicles.
Agriculture: Harvesters and irrigation systems.
How Much Does a Slew Drive Cost?
Prices vary wildly depending on:
Size: Small units (for solartrackers)start at ~500.Industrial−gradedrivesforcranescanexceed20,000.
Load Capacity: Higher load ratings = more materials and machining = higher cost.
Gearing Type: Worm gears are cheaper but less efficient; planetary gears cost more but offer better torque.
Brand/Origin: European brands (e.g., Liebherr, Thyssenkrupp) are pricier than Chinese manufacturers.
Customization: Modifications like special coatings or seals add 15–30% to the base price.
Example: A mid-range slew drive for a medium-sized excavator might cost 8,000–12,000.
How Long Do Slew Drives Last?
Lifespan depends on:
Maintenance: Regular lubrication and inspection can extend life by years.
Load Conditions: Overloading or sudden shocks accelerate wear.
Environment: Exposure to saltwater, dust, or extreme temps reduces longevity.
Quality: Cheap drives with poor heat treatment may fail within 5 years; premium units last 15+ years.
Typical Lifespan:
Industrial applications (e.g., cranes): 10–15 years with proper care.
Harsh environments (offshore wind turbines): 7–12 years.
Light-duty uses (solar trackers): 15–20 years.
How to Choose the Right Slew Drive
Picking a slew drive isn’t just about specs – it’s about matching it to your exact use case. Here’s a step-by-step guide:
Define Your Load Requirements
Axial Load: Vertical weight (e.g., the tower of a wind turbine pressing down).
Radial Load: Sideways force (e.g., a crane arm extending horizontally).
Moment Load: Tilting forces (e.g., uneven weight distribution on an excavator bucket).
Tip: Add a 20–30% safety margin to your max calculated load. Determine Speed & Precision Needs
Rotation Speed: Slow, high-torque applications (e.g., solar trackers) vs. faster movement (e.g., robotics).
Backlash: Low backlash (minimal gear play) is critical for precision tasks like medical imaging.
Assess Environmental Conditions
Sealing: IP ratings matter. For dusty mines or offshore use, choose drives with heavy-duty seals.
Temperature: Standard drives work in -30°C to +80°C. Extreme temps require special grease or materials.
Corrosion Resistance: Stainless steel or coatings like zinc-nickel for salty or humid environments.
Choose the Gear Type
Worm Gears: Affordable, self-locking (no external brake needed), but less efficient (60–70% efficiency).
Planetary Gears: Higher efficiency (~95%), better for high-speed applications, but costlier.
Helical Gears: Quiet operation, ideal for medical or indoor machinery.
Check Mounting & Size Constraints
Measure available space for the drive. Compact designs (e.g., flange-mounted) save room.
Verify bolt patterns and shaft compatibility with existing systems.
Brand & Supplier Reliability
Established brands offer better QC and warranties but cost more.
For budget projects, verify certifications (ISO 9001) and ask for load-test reports from cheaper suppliers.
Maintenance Requirements
Will you have easy access for lubrication? Sealed/lubricated-for-life drives reduce upkeep.
Check grease intervals – some need servicing every 500 hours, others every 2,000.
Budget vs. Long-Term Value
Cheap drives may save upfront costs but lead to downtime and repairs.
Total cost of ownership (TCO) includes energy efficiency – e.g., planetary gears cut power use.
Customization Options
Need anti-explosion certifications for mining? Or a custom gear ratio? Confirm with the supplier early.
Test Before Full Commitment
Request a sample or trial unit for real-world testing, especially for critical applications.
Common Mistakes to Avoid
Ignoring Moment Loads: Even if axial/radial loads seem manageable, tilting forces can kill a drive.
Overlooking Lubrication: Wrong grease type or intervals cause 40% of premature failures.
Mismatched Gear Ratios: Too high a ratio slows rotation; too low reduces torque.
Assuming All Drives Are Equal: A slew drive for a Ferris wheel won’t work in a high-precision radar system.
Slew Drive Supplier
LYRA Drive is a professional slew drive,slewing bearings, slewdrives and gears manufacturer provides customizedslew bearing, drive and gears.For application-specific engineering solutions, contact LYRA to discuss technical specifications and implementation strategies.