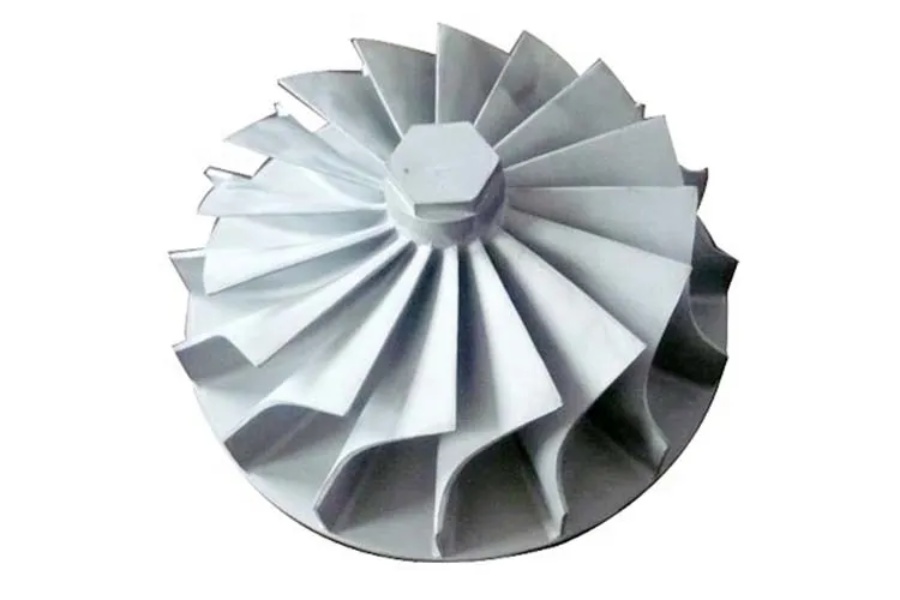
What is a Customized Turbine Pair Parts
What is a Customized Turbine Pair Part?
A Customized Turbine Pair Part refers to specially designed components that work together in a turbine system, engineered to fit exact specifications for a specific application. These "pairs" could be rotor-stator sets, blade-hub assemblies, seal rings, or any two parts that must interact seamlessly to ensure the turbine operates efficiently. Think of them as a "matched set" – like custom shoes for your turbine, ensuring perfect fit, balance, and performance. These parts are tailored to handle unique conditions like extreme temperatures, pressures, or corrosive environments that off-the-shelf parts can’t survive.
Types of Customized Turbine Pair Parts
Rotor & Stator Sets:
Rotor blades and stator vanes designed to optimize airflow or fluid dynamics.
Seal Rings & Shafts:
Precision-matched seals and shafts to prevent leaks in high-pressure turbines.
Bearings & Housings:
Custom bearings and housings for vibration control and load distribution.
Blade & Disk Assemblies:
Turbine blades and disks (blisks) machined as a single unit for aerospace engines.
Nozzle & Bucket Sets:
Steam turbine nozzles and buckets shaped for maximum energy extraction.
Thermal Barrier-Coated Parts:
Pairs with specialized coatings (e.g., ceramic) to withstand extreme heat.
Key Features of Customized Turbine Pair Parts
Precision Fit: Components are machined to micron-level tolerances for perfect alignment.
Material Science: Made from advanced alloys (Inconel, titanium), ceramics, or composites for corrosion/heat resistance.
Balanced Design: Reduces vibration and wear in high-speed turbines (e.g., jet engines).
Custom Coatings: Thermal barriers, anti-erosion layers, or lubricious coatings for specific environments.
Tested Performance: Each pair is validated under simulated operating conditions (heat, pressure, RPM).
Applications of Customized Turbine Pair Parts
Power Generation: Gas/steam turbines in coal, nuclear, or renewable energy plants.
Aerospace: Jet engine compressor and turbine stages.
Oil & Gas: Turboexpanders for natural gas processing or pipeline compression.
Marine: Turbines in ship propulsion systems.
Industrial: Process turbines for chemical manufacturing or HVAC systems.
Price Range
Customized turbine parts are expensive, but cheaper than turbine failure. Costs depend on:
Complexity: A simple seal pair might cost
5,000.Afullrotor−statorsetforajetenginecanhit500,000+.
Materials: Inconel 718 parts cost 3–5x more than stainless steel.
Precision: Mirror-polished or EDM-machined parts add 20–40%.
Testing: Fatigue testing or CFD analysis adds
10,000–50,000.
Volume: Bulk orders (10+ units) reduce per-part costs by 15–30%.
Example: A mid-complexity bearing-housing pair for a gas turbine costs
25,000–80,000.
Lifespan of Customized Turbine Pair Parts
Lifespan varies wildly:
Material Quality: Inconel parts in a jet engine last 20,000+ hours; cheap alloys in industrial turbines may fail at 5,000 hours.
Operating Conditions: High heat or corrosive fluids can slash lifespan by 50%.
Maintenance: Regular inspections and coatings renewal extend life.
Typical Lifespan:
Aerospace turbines: 15–25 years (with overhauls).
Power plants: 10–20 years.
Harsh environments (offshore oil rigs): 5–10 years.
How to Choose the Right Customized Turbine Pair Parts
Don’t wing it – follow these steps to avoid blowing your budget (or turbine):
Define Your Operating Conditions
Temperature: Will parts face 500°C or 1,500°C? Dictates material choice (e.g., ceramic vs. superalloy).
Pressure: High-pressure steam? Requires thicker walls and stronger alloys.
Corrosion: Saltwater, H2S gas, or acids? Choose corrosion-resistant coatings.
Speed: 10,000 RPM or 100,000 RPM? Affects balance and tolerance requirements.
Material Selection
Superalloys (Inconel, Hastelloy): For high heat and corrosion.
Titanium: Lightweight + high strength (aerospace).
Ceramics: Extreme heat resistance but brittle.
Stainless Steel: Budget-friendly for moderate conditions.
Precision Requirements
Tolerances: ±0.001mm for aerospace vs. ±0.01mm for industrial turbines.
Surface Finish: Polished surfaces reduce friction and fatigue cracks.
Supplier Expertise
Industry Experience: A supplier who’s made jet engine parts won’t blink at your specs.
Certifications: AS9100 (aerospace), ISO 9001, or NORSOK (oil/gas).
Testing Capabilities: Can they simulate thermal cycling or vibration?
Prototyping & Testing
3D Printing: Use additive manufacturing for rapid prototypes.
Non-Destructive Testing (NDT): X-ray, ultrasonic, or dye penetrant checks for defects.
Performance Testing: Spin tests, pressure tests, or thermal shock trials.
Total Cost of Ownership (TCO)
Upfront Cost: High-quality parts cost more but last longer.
Maintenance: Coatings or modular designs that simplify repairs.
Downtime: A $10,000 part that avoids 3 days of downtime pays for itself.
Lead Time & Scalability
Lead Time: Custom parts can take 12–24 weeks – plan ahead!
Scalability: Can the supplier handle batch production if your needs grow?
Documentation
Material Certs: Mill reports for traceability.
Inspection Reports: Proof that parts meet specs.
Warranty: At least 1–2 years for industrial parts; longer for aerospace.
Common Mistakes to Avoid
Ignoring Thermal Expansion: Materials expand under heat – mismatched pairs can seize or crack.
Over-Engineering: A titanium part where steel would work = wasted money.
Skipping Prototyping: “It looks good on CAD” ≠ real-world performance.
Cheaping Out on Coatings: Saving 5koncoatingscanleadto500k in repairs.
Forgetting Logistics: A 2-ton rotor pair needs heavy transport planning.
Customized Turbine Pair Parts Supplier
LYRA Drive is a professional Customized Turbine Pair Parts ,slewing bearings ,slew drive, slewdrives and gears manufacturer provides customizedslew bearing, drive and gears.For application-specific engineering solutions, contact LYRA to discuss technical specifications and implementation strategies.