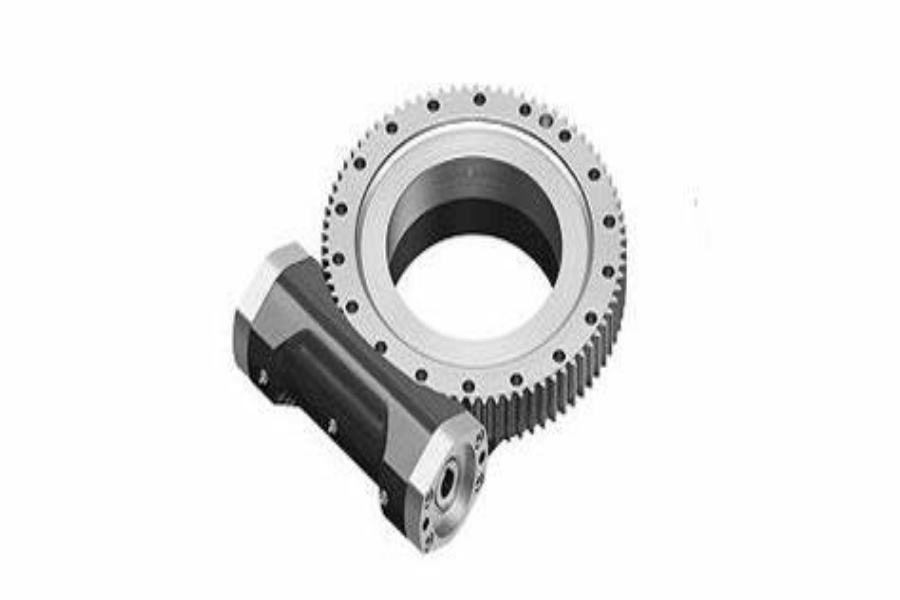
WE Slew Drives Revolutionizing Precision in Heavy-Duty Rotation
In the evolving landscape of industrial automation and heavy machinery, WE Slew Drives have emerged as critical components that redefine rotational control in demanding applications. These advanced systems enable precise movement under extreme loads, powering everything from solar trackers optimizing energy harvest to construction cranes lifting multi-ton materials. As industries increasingly prioritize efficiency, durability, and smart operation, WE Slew Drives stand at the forefront of innovation, merging mechanical robustness with cutting-edge technology to meet the rigorous demands of modern engineering challenges.
What Is a WE Slew Drive
A WE Slew Drive is an integrated rotational drive system that combines a high-capacity slewing bearing with a precision gear mechanism, designed to deliver controlled rotation under significant axial, radial, and moment loads. The system typically incorporates a worm gear or helical gear arrangement coupled with a slewing ring, enabling torque amplification and smooth 360-degree motion. Engineered from hardened alloys and advanced composites, these drives feature optimized heat treatments and surface coatings to withstand wear, corrosion, and extreme environmental conditions. Sealing systems and lubrication channels are meticulously integrated to ensure longevity in applications ranging from dusty construction sites to offshore installations exposed to saltwater.
The significance of WE Slew Drives lies in their ability to balance power and precision. For instance, in solar energy installations, these drives adjust panel angles with sub-degree accuracy to maximize sunlight capture throughout the day. In heavy machinery such as tower cranes, they facilitate the precise positioning of loads weighing hundreds of tons, even in high-wind conditions. Their compact design allows integration into space-constrained equipment without compromising performance, while modular configurations enable customization for specific torque and speed requirements. The incorporation of fail-safe mechanisms, such as self-locking gears, ensures operational safety by preventing unintended movement during power outages or system failures.
Global Innovations in WE Slew Drive Technology
Cutting-Edge Engineering in Leading Markets
Nations with strong industrial engineering traditions, including Germany, Japan, and the United States, continue to pioneer advancements in WE Slew Drive technology. German manufacturers utilize laser-hardened gear surfaces to achieve micron-level precision, reducing friction and energy loss in high-speed applications. Japanese engineers have developed asymmetric gear tooth profiles that optimize load distribution, enhancing durability in mining equipment subjected to constant shock loads. American firms are leveraging additive manufacturing to produce complex gear geometries with internal cooling channels, significantly improving thermal management in continuous-operation scenarios.
The renewable energy sector benefits from WE Slew Drives with corrosion-resistant coatings and sealed lubrication systems, ensuring reliable performance in offshore wind turbines exposed to harsh marine environments. The aerospace industry employs lightweight variants made from titanium alloys and carbon fiber composites, reducing weight while maintaining structural integrity in satellite deployment mechanisms. Robotics applications utilize drives with integrated encoders and real-time feedback systems, enabling collaborative robots to perform delicate assembly tasks with micron-level accuracy.
Emerging Markets Advancing Through Technology Adoption
Manufacturers in rapidly industrializing regions are closing the technological gap by adopting advanced production techniques. Chinese producers now implement AI-driven quality control systems that detect microscopic defects in gear teeth during manufacturing, achieving parity with global standards. Indian engineers have innovated hybrid lubrication systems combining solid and liquid lubricants, extending maintenance intervals in arid regions prone to dust contamination. Brazilian companies are utilizing recycled aerospace-grade materials to produce cost-effective yet durable drives for agricultural machinery, supporting sustainable farming practices.
Despite these advancements, challenges remain in areas such as dynamic load simulation and material consistency. European manufacturers employ finite element analysis (FEA) to predict stress distribution under variable loads, while emerging markets often rely on iterative testing, which can prolong development cycles. Access to high-purity specialty steels and advanced polymer seals remains limited in some regions, affecting the reliability of drives in extreme-temperature applications.
Overcoming Technical Challenges in WE Slew Drive Applications
The disparity between industry leaders and developing manufacturers primarily revolves around material innovation, manufacturing precision, and smart system integration. Premium WE Slew Drives incorporate nanostructured coatings that reduce surface friction by up to 40%, significantly enhancing efficiency in high-cycle applications like packaging machinery. In contrast, conventional coatings used in cost-sensitive markets degrade faster under heavy loads, necessitating frequent replacements in industrial automation systems.
Collaborative efforts between academic institutions and manufacturers are driving progress. Research initiatives focus on 3D-printed gradient alloys that combine flexibility and hardness within a single component, ideal for drives used in earthquake-prone regions. Another breakthrough involves embedded IoT sensors that monitor lubrication levels and wear patterns, transmitting data to centralized maintenance platforms for predictive servicing. Workforce training programs utilizing virtual reality simulations are reducing installation errors by 50%, ensuring optimal performance in critical applications like bridge construction cranes.
The Future of WE Slew Drives Intelligence and Sustainability
Next-generation WE Slew Drives will emphasize energy efficiency, self-diagnostic capabilities, and eco-friendly materials. Prototype regenerative drives now under development capture kinetic energy during deceleration, converting it into reusable power for onboard systems. Material scientists are experimenting with bio-based composites derived from agricultural waste, offering comparable strength to traditional metals with a 60% smaller carbon footprint
In smart industrial ecosystems, these drives will function as autonomous units within IoT networks. Imagine solar farms where WE Slew Drives adjust panel angles based on real-time weather data and grid demand, optimizing energy output autonomously. Autonomous construction equipment could utilize drives with machine learning algorithms to predict load shifts and adjust torque dynamically, enhancing safety on unstable terrain.
Strategic Implementation Best Practices
Precision Alignment and Calibration:Use laser-guided alignment tools during installation to ensure gear meshing within 0.05mm tolerance, critical for minimizing wear in high-precision robotics applications.
Environment-Specific Material Selection:Opt for chromium-carbide coatings in coastal environments to combat salt corrosion and ceramic composite seals in high-dust mining operations.
Predictive Maintenance Integration:Deploy vibration analysis systems that detect early-stage bearing wear through spectral frequency monitoring, scheduling repairs during planned downtime.
Modular Design Principles:Develop drives with interchangeable gear modules to facilitate quick repairs and upgrades, reducing waste and extending product lifecycles.
WE Slew Drives supplier
WE Slew Drives exemplify the synergy between mechanical engineering and technological innovation, enabling advancements across industries from renewable energy to advanced manufacturing. As global demands for sustainability and automation intensify, these components are evolving from mere mechanical parts into intelligent systems capable of self-optimization and environmental adaptation. While established markets continue to lead with breakthroughs in material science and digital integration, emerging economies demonstrate that strategic investments in smart manufacturing and collaborative R&D can accelerate technological parity. The future promises WE Slew Drives that not only deliver unmatched performance but also contribute to a greener, more connected industrial world. For industry stakeholders, embracing innovation while adhering to sustainable practices will be pivotal in driving the next wave of engineering excellence.
LYRA Drive is a professional slewing bearings ,slew drive and gears manufacturer provides customized slew bearing, drive and gears.For application-specific engineering solutions, contact LYRA to discuss technical specifications and implementation strategies.