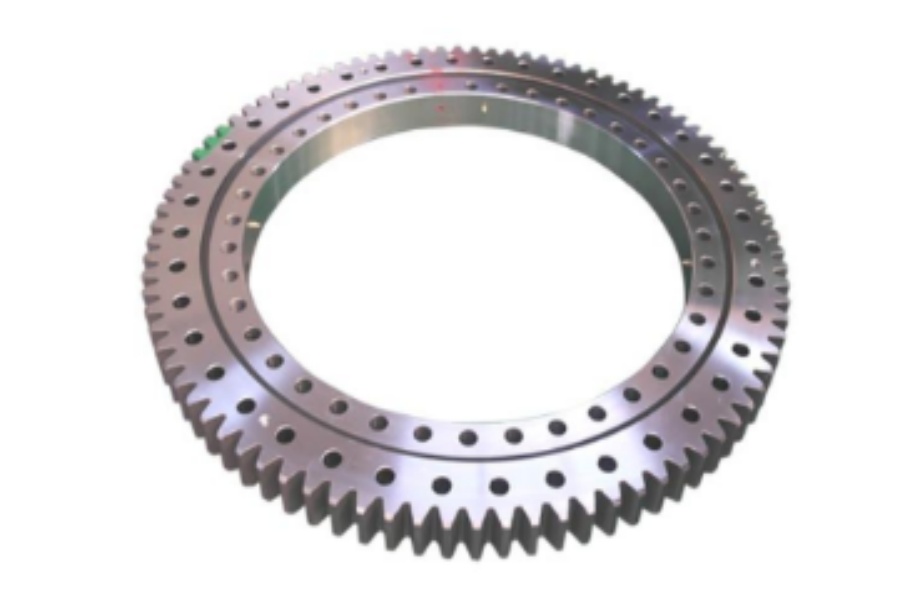
Truck Crane Slewing Bearings The Pivotal Force in Mobile Lifting Solutions
In the dynamic realm of construction and logistics where mobility meets heavy lifting, truck crane slewing bearings serve as the critical nexus between hydraulic power and precision movement. These specialized components enable the seamless rotation of crane booms, allowing operators to position multi-ton loads with centimeter accuracy across busy urban construction sites or remote infrastructure projects. As global demand for faster project completion and safer material handling intensifies, truck crane slewing bearings have evolved into sophisticated systems that balance rugged durability with exacting performance standards, ensuring both operational efficiency and regulatory compliance in high-stakes environments.
What Is a Truck Crane Slewing Bearing
A truck crane slewing bearing is a precision-engineered rotational assembly that forms the core of mobile crane rotation systems, designed to handle combined axial, radial, and moment loads while enabling 360-degree boom movement. This component integrates a large-diameter bearing raceway with gear teeth, typically constructed from case-hardened alloy steel to withstand the punishing cycles of load lifting, swinging, and sudden stops. The bearing’s multi-row ball or roller arrangement distributes stresses across multiple contact points, while integrated sealing systems protect internal components from dust, moisture, and debris encountered in harsh job sites.
The operational significance of these bearings stems from their dual role as structural supports and motion controllers. When a crane operator swings a 50-ton concrete panel into place on a skyscraper frame, the slewing bearing ensures smooth rotation despite wind loads and uneven weight distribution. In port logistics, these components allow mobile harbor cranes to transfer shipping containers between docks and vessels with millimeter precision, even during tidal shifts. Their compact yet robust design enables installation within the crane’s limited spatial envelope while maintaining the strength to handle dynamic load factors up to 1.5 times the rated capacity during emergency stops or unexpected load shifts.
Global Innovations in Truck Crane Slewing Bearing Technology
Advanced Manufacturing in Traditional Industrial Hubs
Countries with longstanding expertise in heavy equipment manufacturing, such as Germany, Japan, and the United States, continue to pioneer advancements in slewing bearing technology. German engineers employ induction hardening with laser tempering to create raceway surfaces with gradient hardness profiles—rock-hard contact zones for wear resistance transitioning to tough core material that resists cracking under impact loads. Japanese manufacturers have developed ultra-compact bearing designs that reduce overall crane weight by 15% through optimized cross-sectional geometries, crucial for meeting road weight regulations while maintaining load capacity.
The construction sector benefits from bearings with integrated load moment indicators, where strain gauges embedded in the bearing structure provide real-time data on load distribution and structural stress. Mining applications utilize abrasion-resistant overlay coatings applied via high-velocity oxygen fuel spraying, extending bearing life in environments filled with silica dust and rock particulates. The renewable energy field sees specialized variants in wind turbine installation cranes, featuring corrosion-resistant alloys that withstand offshore salt spray while maintaining precise rotation under 100-ton component lifts.
Emerging Markets Elevating Production Capabilities
While established manufacturers dominate high-end markets, producers in rapidly industrializing regions are closing the technology gap through strategic innovation. Chinese manufacturers now utilize AI-powered grinding machines that adapt wheel paths in real time to compensate for material variances, achieving surface finishes comparable to premium imports. Indian engineers have pioneered composite seal materials combining PTFE with carbon fiber, outperforming traditional rubber in high-temperature asphalt plant crane applications. Brazilian firms employ blockchain-based quality tracking systems that document every production step from steel smelting to final assembly, ensuring traceability for safety-critical components.
Persistent challenges include mastering dynamic load simulation software and fatigue life prediction models. European manufacturers use multi-body dynamics simulations that account for wind loads, hydraulic pulsations, and driver behavior patterns, while emerging markets often rely on conservative safety factors that result in over-engineered, weight-penalized designs. Access to ultra-clean steel alloys with controlled inclusion sizes remains limited in some regions, impacting bearing longevity in high-cycle applications like urban high-rise construction.
Overcoming Technical Challenges in Crane Bearing Applications
The technological divide between market leaders and developing manufacturers centers on three key areas: material science, predictive maintenance integration, and smart manufacturing processes. Premium bearings incorporate micro-alloyed steels with boron and niobium additives that enhance hardenability without brittleness, crucial for bearings subjected to frequent shock loads during steel girder placement. In contrast, conventional carbon steels used in cost-sensitive markets exhibit accelerated spalling in applications requiring 500,000+ rotation cycles, such as municipal utility maintenance cranes.
Collaborative initiatives are driving progress across the industry. University-industry partnerships are developing self-lubricating bearing surfaces using graphene-infused composites that reduce maintenance intervals by 80% in arid region cranes. Another breakthrough involves edge computing modules mounted directly on bearing housings, processing vibration data to predict roller element wear months before failure. Workforce training programs focused on augmented reality-assisted installations are reducing bearing replacement times from days to hours through holographic alignment guides.
The Future of Truck Crane Slewing Bearings Intelligent and Sustainable
Next-generation slewing bearings will prioritize energy-efficient operation, self-monitoring capabilities, and eco-conscious material cycles. Prototype regenerative braking systems now in testing capture rotational inertia during crane deceleration, storing energy to power onboard sensors and control systems. Material scientists are experimenting with bio-based hydraulic fluids and recyclable polymer seals that maintain performance while reducing environmental impact during component disposal.
In smart construction ecosystems, these bearings will evolve into intelligent system nodes. Imagine crane bearings that communicate with building information modeling systems to automatically adjust rotation speeds based on real-time wind data and load positioning requirements. Autonomous mobile cranes could utilize bearings with embedded inertial measurement units to stabilize loads during movement over uneven terrain, revolutionizing logistics in disaster response scenarios.
Strategic Implementation Guidelines
Precision Alignment Procedures:Implement laser-guided mounting systems to ensure bearing concentricity within 0.05mm tolerance during crane assembly, critical for achieving advertised service life in high-use rental fleets.
Environment-Specific Material Selection:Specify zinc-aluminum coatings for coastal operation cranes and ceramic composite seals for mining applications exposed to abrasive dust clouds.
Condition-Based Maintenance Integration:Deploy acoustic emission sensors that detect early-stage raceway pitting through ultrasonic signature analysis, enabling planned maintenance during natural work breaks.
Circular Design Principles:Develop modular bearing architectures allowing individual raceway segment replacement, reducing material waste during overhaul procedures.
Truck crane slewing bearings supplier
Truck crane slewing bearings embody the convergence of mechanical robustness and technological sophistication, enabling feats of precision lifting that shape modern skylines and infrastructure networks. As global construction trends demand faster project timelines and greener practices, these components are transitioning from passive mechanical elements to active system participants. While technological leaders continue pushing boundaries through advanced metallurgy and digital integration, emerging markets demonstrate that focused R&D and smart manufacturing adoption can accelerate technological parity. The future promises bearings that not only withstand immense forces but also actively optimize performance, predict failures, and adapt to operational contexts—transforming from steel assemblies into cognitive partners in construction innovation. For industry stakeholders, embracing both technological advancement and sustainable practices will be paramount in maintaining competitiveness within an increasingly complex and regulated operational landscape.
LYRA Drive is a professional slewing bearings ,slew drive and gears manufacturer provides customized slew bearing, drive and gears.For application-specific engineering solutions, contact LYRA to discuss technical specifications and implementation strategies.