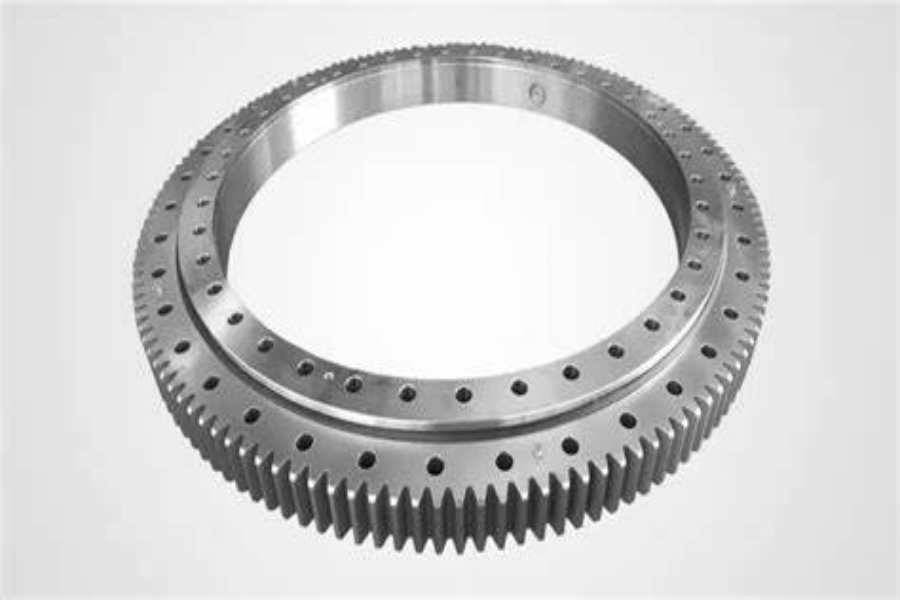
Heavy Load Slewing Bearings The Giants Enabling Modern Mega-Structures
In the world of industrial engineering where scale meets precision, heavy load slewing bearings stand as monumental achievements of mechanical design, enabling the rotation of structures weighing thousands of tons with the finesse of a wristwatch. These colossal components form the rotational backbone of offshore wind turbines battling ocean storms, tower cranes shaping skylines, and mining excavators moving mountains of earth. As global infrastructure projects grow in ambition and scale, heavy load slewing bearings have become indispensable in translating raw power into controlled motion, ensuring both monumental strength and micrometer-level precision in the most demanding environments.
What Is a Heavy Load Slewing Bearing
A heavy load slewing bearing is an engineered rotational support system designed to handle extreme axial, radial, and moment loads exceeding 10,000 metric tons while maintaining precise rotational control. These bearings feature multi-row roller or ball arrangements sandwiched between massive steel rings, often exceeding 10 meters in diameter in mining applications. The design incorporates hardened raceways, specialized heat treatments, and custom sealing systems capable of withstanding abrasive particulates, extreme temperatures, and constant vibration. Gear teeth integrated into the bearing’s outer or inner ring enable direct drive compatibility with pinion gears, creating a unified system for transmitting rotational force.
The critical importance of these bearings lies in their ability to marry immense strength with surgical precision. In container port cranes, they allow 80-ton shipping containers to be rotated and positioned within 5mm accuracy despite gusting coastal winds. Mining draglines use bearings with 15-meter diameters to swing 10,000-ton buckets across open pits, operating continuously for decades under abrasive conditions. Offshore wind turbine nacelles rely on these components to adjust blade angles within 0.1-degree accuracy while enduring saltwater corrosion and hurricane-force winds. Their robust construction enables 360-degree continuous rotation under maximum load without lubrication intervals in some designs, revolutionizing operations in inaccessible locations like Arctic oil rigs or deep-sea research platforms.
Global Innovations in Heavy Load Bearing Technology
Material and Manufacturing Breakthroughs
Traditional engineering powerhouses like Germany, Sweden, and Japan continue pushing the boundaries of heavy bearing capabilities. German manufacturers now employ electron beam welding to create seamless forged steel rings up to 12 meters in diameter, eliminating weak points in traditional segmented designs. Swedish engineers have perfected deep cryogenic treatment processes, immersing bearings in -196°C liquid nitrogen to stabilize molecular structures, increasing fatigue life by 40% in mining applications. Japanese firms lead in adaptive heat treatment systems that vary case hardening depths across raceway surfaces, optimizing wear resistance where contact pressures peak.
The renewable energy sector showcases these advancements through 20MW offshore wind turbine bearings using graded-density steel composites that transition from impact-resistant cores to ultra-hard raceway surfaces. The construction industry benefits from bearings with laser-clad gear teeth that self-heal micro-cracks during operation, extending service intervals in tower cranes operating 24/7. Aerospace launch platforms utilize titanium hybrid bearings that reduce weight by 30% while maintaining strength for rotating 5,000-ton rocket assembly structures.
Emerging Markets Building Technical Capabilities
While established leaders dominate ultra-heavy applications, manufacturers in industrializing nations are making strides through technology transfer and automation. Chinese producers now manufacture 8-meter diameter bearings for cement kilns using AI-controlled quenching systems that optimize hardness profiles in real time. Indian engineers have developed abrasion-resistant coating techniques using recycled industrial diamonds, tripling service life in coal handling plant bearings. Brazilian manufacturers employ blockchain-tracked steel to ensure material consistency in bearings for Amazonian hydropower projects.
Persistent challenges include mastering residual stress management in ultra-large forgings and predictive lubrication systems for desert environments. European manufacturers use neutron diffraction scanning to map internal stresses in 15-meter bearings, while emerging markets often rely on trial-and-error methods that increase rejection rates. Access to marine-grade alloys and space-certified lubricants remains limited, constraining participation in specialized sectors like offshore drilling or satellite launch systems.
Overcoming Engineering Challenges in Heavy Applications
The technological divide centers on three critical areas: material innovation, precision manufacturing, and smart monitoring systems. Premium bearings incorporate self-healing polymer seals that regenerate when scratched, maintaining integrity in sandstorm-prone regions. In contrast, conventional rubber seals used in developing markets degrade rapidly in Arctic conditions, requiring monthly replacements in mining operations.
Collaborative initiatives are driving progress. International research consortia are developing 3D-printed bearing prototypes with internal cooling channels that reduce operating temperatures by 200°C in steel mill applications. Another breakthrough involves acoustic emission sensors embedded within roller elements, detecting subsurface cracks years before surface pitting appears. Workforce development programs focused on augmented reality maintenance are reducing turbine bearing replacement times from weeks to days through holographic installation guides.
The Future of Heavy Load Slewing Bearings Intelligent and Sustainable
Next-generation heavy bearings will prioritize energy efficiency, self-diagnostic capabilities, and circular lifecycle management. Prototype regenerative lubrication systems now under test in cement plants capture and filter used grease, reducing consumption by 70%. Material scientists are experimenting with bio-inspired steel alloys mimicking abalone shell structures, offering 50% greater fracture resistance with equal weight.
In smart infrastructure networks, these bearings will evolve into sentient system components. Imagine offshore wind farms where bearings communicate tidal data to adjust nacelle positions preemptively, minimizing wave impact loads. Smart mining systems could employ bearings with strain-based load sensors that automatically redistribute weight during unstable lifts, preventing catastrophic failures. These innovations align with global demands for autonomous, eco-efficient heavy industry.
Strategic Implementation Considerations
Precision Installation Planning:Deploy laser tracker systems to align 10-meter bearings within 0.1mm tolerance during stadium roof installations, preventing premature wear from misalignment.
Environmental Hardening Protocols:Specify zinc-nickel matrix coatings for coastal crane bearings and phase-change thermal buffers for steel mill applications facing 800°C radiant heat.
Condition Monitoring Integration:Implement fiber-optic sensing grids that map temperature and stress across entire bearing surfaces in real time, enabling predictive maintenance.
Circular Economy Design:Develop modular bearing architectures allowing individual roller replacement, reducing material waste during refurbishments.
Heavy load slewing bearings supplier
Heavy load slewing bearings represent the pinnacle of mechanical engineering, enabling humanity’s most ambitious structural achievements. As global industries confront escalating demands for sustainability and automation, these components are transitioning from passive load carriers to intelligent system orchestrators. While technological leaders continue advancing through nano-engineered materials and embedded AI, emerging markets demonstrate that digital manufacturing and collaborative R&D can accelerate technological parity. The future will see these bearings not just supporting weight but actively optimizing load distribution, predicting failures, and adapting to environmental challenges—transforming from steel behemoths into cognitive partners in industrial progress. For engineers and industry leaders, success lies in balancing relentless innovation with sustainable practices, ensuring these mechanical marvels continue enabling achievements that redefine the possible.
LYRA Drive is a professional slewing bearings ,slew drive and gears manufacturer provides customized slew bearing, drive and gears.For application-specific engineering solutions, contact LYRA to discuss technical specifications and implementation strategies.