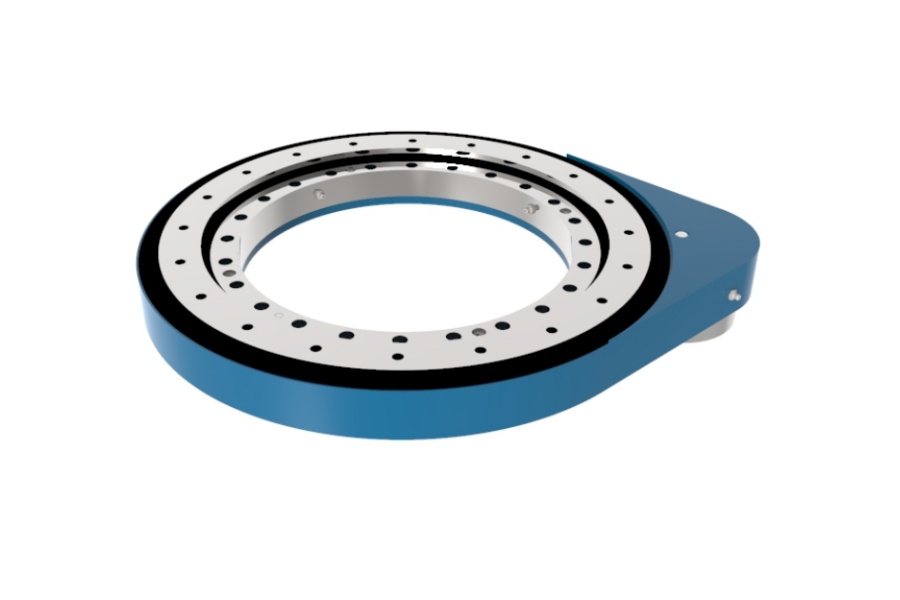
Unlocking Precision Motion: Your Ultimate Guide to the Medium Duty Gear Slewing Drive SP-M 4011
What Exactly is the Medium Duty Gear Slewing Drive SP-M 4011?
The Medium Duty Gear Slewing Drive SP-M 4011 is an integrated mechanical assembly combining a high-capacity slewing bearing with a precision gear reduction unit, typically featuring worm gear technology. This design transforms high-speed, low-torque input from an electric motor (or other prime mover) into controlled, low-speed, high-torque rotational output. Housed within a compact and rigid structure, the SP-M 4011 is specifically engineered to handle substantial radial, axial, and moment (tilting) loads simultaneously. Its "Medium Duty" classification positions it optimally between lighter units for simpler tasks and the massive capacity of heavy-duty drives, offering an exceptional blend of strength, precision, and cost-effectiveness for a vast range of industrial and renewable energy applications. The designation "SP-M 4011" signifies its specific model within a product line, indicating its unique size, load ratings, and performance characteristics.
The Critical Role of Slewing Drives in Solar Tracking Systems
Solar tracker slewing drives are the indispensable workhorses of modern photovoltaic power plants. Their primary function is to precisely orient solar panels or entire arrays throughout the day, meticulously following the sun's path from sunrise to sunset. This continuous adjustment maximizes the angle of incidence between the panels and sunlight, significantly boosting energy capture – often by 25% or more compared to fixed installations. Solar tracker slewing drives must excel in harsh environmental conditions, enduring relentless UV exposure, wide temperature fluctuations, dust, sand, rain, and sometimes corrosive atmospheres. Reliability is paramount, as system downtime directly translates to lost energy production. They require high positioning accuracy for optimal energy gain, robust construction to withstand wind loads (both operational and survival), and often feature integrated safety brakes to hold position during high winds or power failures. Efficiency is also crucial to minimize the energy consumed by the tracking system itself. The SP-M 4011, with its robust design and proven environmental protection, is frequently specified for medium-sized tracker rows or specific tracker architectures demanding its reliable performance.
When Extreme Forces Demand Heavy Duty Solutions
Heavy duty slewing drives represent the pinnacle of load-bearing and torque transmission capability within the slewing drive spectrum. Engineered for the most arduous applications, these drives are characterized by massive slewing bearings with hardened raceways and large-diameter rolling elements, coupled with extremely robust gearboxes featuring hardened and ground worm sets or high-ratio planetary gears. They are built to withstand colossal radial, axial, and moment loads encountered in industries like mining (excavators, stackers/reclaimers), heavy construction (cranes, tunnel boring machines), large-scale material handling (ship-to-shore cranes), and massive defense systems. Construction involves heavy-section housings, oversized shafts, and premium materials throughout. Sealing systems are exceptionally robust to prevent ingress of contaminants like water, dust, or abrasive particles in challenging environments. While offering unparalleled strength, heavy-duty drives are significantly larger, heavier, and more expensive than medium-duty counterparts like the SP-M 4011, making them essential only where the application's sheer scale and forces demand nothing less.
Harnessing Immense Rotational Power: High Torque Slewing Drives
High torque slewing drives are engineered specifically to deliver exceptional rotational force (torque) relative to their size or input speed. This high torque density is crucial for applications requiring significant force to initiate movement or overcome resistance while rotating heavy loads, often at slow, controlled speeds. Achieving high torque typically involves significant gear reduction ratios – worm gears are common due to their inherent high reduction potential and self-locking capability, though advanced planetary or hybrid systems are also used. Key design focuses include optimizing gear tooth geometry and material hardening processes to handle immense stresses without failure, minimizing friction losses for efficiency, and ensuring robust bearing support to manage the resulting high thrust and radial forces. Applications demanding high torque slewing drives include large industrial valves, heavy-duty positioning stages, certain types of construction equipment attachments, and specialized machinery where brute rotational force is essential. While the SP-M 4011 delivers substantial torque suitable for its medium-duty class, dedicated high-torque drives push the boundaries of torque output for their frame size or input power.
Standout Features of the Medium Duty Gear Slewing Drive SP-M 4011
The SP-M 4011 distinguishes itself through a carefully engineered set of features designed for reliable performance in demanding scenarios. Its core is a high-quality slewing bearing featuring robust raceways and precision-ground rolling elements, optimized to handle the specified combination of axial, radial, and moment loads efficiently. The integrated worm gear reducer is a key highlight, typically employing a hardened, ground steel worm meshing with a bronze or wear-resistant alloy worm wheel. This configuration provides a high reduction ratio, delivering substantial output torque from a compact motor input, and crucially, offers a self-locking characteristic that prevents back-driving under load, enhancing safety and stability without needing an external brake in many situations. The drive is housed in a rigid, often cast or machined housing providing structural integrity and precise alignment for internal components. Comprehensive sealing using high-quality lip seals or labyrinth designs protects critical bearings and gears from dust, water, and other environmental contaminants, significantly extending service life. Pre-lubrication for long intervals and strategically placed grease fittings facilitate straightforward maintenance. Mounting flexibility is ensured through multiple tapped holes or precision machined surfaces on both the stationary and rotating rings. Optional features often include integrated rotary encoders for position feedback, auxiliary hydraulic ports for rotary unions, electric parking brakes for enhanced safety, and specialized coatings for extreme corrosion resistance. The overall design prioritizes durability, operational reliability, and ease of integration.
Diverse Applications Leveraging the SP-M 4011's Capabilities
The versatility and robust performance profile of the Medium Duty Gear Slewing Drive SP-M 4011 make it a sought-after solution across numerous sectors. In solar energy, it's a prime choice for driving single-axis and certain dual-axis solar trackers, reliably positioning panels under wind and environmental stresses. Within material handling, it powers rotating sections of conveyors, positions robotic arms, operates rotary feeders, and drives indexing tables requiring precise angular movement. The construction industry utilizes it on equipment like compact cranes, aerial work platforms (for rotating booms or platforms), drill rigs, and concrete pumpers. Industrial automation heavily relies on the SP-M 4011 for tasks such as precisely orienting welding fixtures, rotating heavy workpieces on machining centers, actuating large valves in process control, and positioning inspection equipment. It also finds application in specialized sectors like antenna positioning for communication systems, stage and entertainment machinery for moving sets or lights, certain agricultural machinery for positioning implements, and even in medical equipment requiring robust, controlled rotation. Its balance of strength, precision, self-locking capability, and environmental resilience underpins its widespread adoption.
Understanding the Price Factors for the SP-M 4011
The investment cost of a Medium Duty Gear Slewing Drive SP-M 4011 is influenced by a complex interplay of factors reflecting its engineering and manufacturing. Core material costs are significant, encompassing the quality and quantity of steel for bearings, housings, and shafts, specialized bronze or alloys for worm wheels, and high-grade seals and lubricants. Precision manufacturing processes like grinding gear teeth and raceways, heat treatment for hardness and durability, and meticulous assembly under controlled conditions contribute substantially to the final price. The specific load ratings (axial, radial, moment) and torque output required directly impact component sizing and material grades – a drive rated for higher loads will inherently cost more. The chosen gear ratio also plays a role, as more complex or higher reduction ratios require more intricate gearing. Optional features significantly add to the base price: integrated electric brakes, high-resolution encoders for position feedback, specialized corrosion protection coatings (e.g., offshore-grade), auxiliary hydraulic passages, or custom mounting configurations all incur additional costs. Order volume is crucial; bulk purchases typically benefit from economies of scale, reducing the unit cost compared to one-off orders. Fluctuations in global raw material markets (steel, copper) directly influence the base manufacturing cost. Finally, the level of engineering support, testing, documentation, warranty coverage, and the supplier's reputation for quality and reliability are intangible factors embedded in the price. Choosing solely on the lowest initial cost can be risky, potentially leading to higher lifecycle costs due to premature failure or downtime.
Supplier of Medium Duty Gear Slewing Drive SP-M 4011
When sourcing a critical component like the Medium Duty Gear Slewing Drive SP-M 4011, partnering with an experienced and reputable manufacturer is paramount. LYRADRIVE has established itself as a leading provider of high-performance slewing drives, including the SP-M 4011. They bring deep engineering expertise in designing, manufacturing, and testing slewing drives for demanding global applications. LYRADRIVE's commitment to quality is typically demonstrated through rigorous quality control processes, adherence to international standards, and the use of premium materials and precision manufacturing techniques. Beyond supplying the physical product, LYRADRIVE often provides significant value through comprehensive technical support. This includes assistance with selecting the optimal drive configuration for specific application requirements (loads, speed, environment), detailed integration guidance, and troubleshooting expertise. Their engineering team can frequently offer customization options to tailor the standard SP-M 4011 design with specific mounting patterns, seals, lubrication, or auxiliary components like brakes or encoders. Furthermore, reliable suppliers like LYRADRIVE ensure consistent product availability and offer robust after-sales support, including warranty services and access to spare parts, minimizing downtime risks. Choosing a supplier with a proven track record in delivering reliable medium-duty slewing drives offers peace of mind and contributes significantly to the long-term success and reliability of the end application.
The Engineered Advantage
The Medium Duty Gear Slewing Drive SP-M 4011 stands as a testament to precision engineering, offering an optimal balance of strength, controlled motion, and reliability. Its integrated design, combining a robust slewing bearing with a high-efficiency worm gear reducer, delivers essential high torque and self-locking capabilities in a versatile package. From harnessing the sun's power on solar trackers to driving critical automation processes and heavy-duty positioning tasks, the SP-M 4011 proves its mettle across diverse industries. Understanding its features, applications, and the factors influencing its cost empowers engineers and procurement specialists to make informed decisions. Partnering with established, quality-focused manufacturers ensures access not only to a superior product but also to the technical expertise and support vital for seamless integration and long-term operational success. In a world demanding ever more precise and reliable motion control, the SP-M 4011 provides a proven, medium-duty solution.