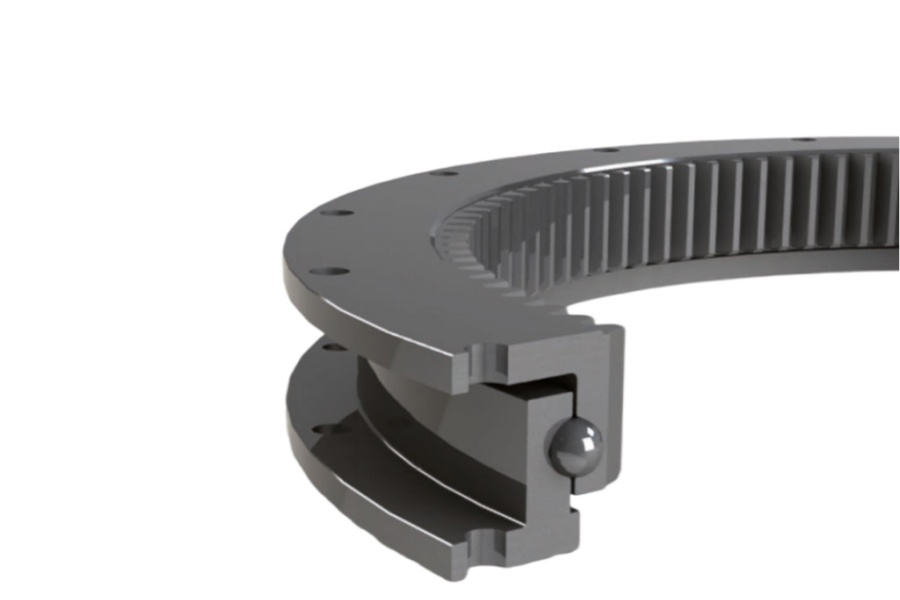
Unlocking Efficient Rotation: The Revolutionary Application Guide for Flanged Ball Slewing Bearings
What is a Flanged Ball Slewing Bearing?
At its core, a Flanged Ball Slewing Bearing is a specialized type of slewing ring bearing. It features a single row of ball bearings meticulously arranged within raceways formed by two concentric rings – typically an inner ring and an outer ring. The defining characteristic, as the name suggests, is the integrated flange. This flange, usually projecting radially outward from one of the rings (most commonly the outer ring, but sometimes the inner), provides a direct and secure mounting surface. This design eliminates the need for separate, complex mounting plates or housings, drastically simplifying installation and enhancing structural rigidity. The balls, often precision-ground, efficiently handle combined loads, making these bearings ideal for applications requiring high load capacity within a constrained envelope.
Flanged Ball Slewing Bearings: Power Hub in Compact Spaces
A Flanged Ball Slewing Bearing is a specialized type of slewing ring (turntable bearing). Its core structure consists of precision-machined concentric inner and outer rings, housing a row of precision-ground rolling steel balls running on carefully designed raceways. Its most distinctive feature, as the name implies, is the integral flange structure. This flange typically extends radially from the outer ring (sometimes the inner ring), forming a robust and flat bolted mounting surface. This revolutionary design eliminates the complex mounting seats or transition flange plates required by traditional bearings, dramatically simplifying installation while significantly enhancing the rigidity and stability of the entire support structure. Thanks to its efficient design, this type of bearing delivers exceptional comprehensive load-bearing capacity within extremely compact installation spaces, making it the ideal choice for space-constrained applications.
The Core of Industrial Robots: Precision Robotic Turntable Bearings
In the joints and rotation units of industrial automation and collaborative robots, robotic turntable bearings demand near-rigorous requirements for precision and reliability. Flanged Ball Slewing Bearings, leveraging their inherent advantages, have become the preferred choice for these critical positions:
Zero Backlash & High Rigidity: Through precision preload technology, near-zero operational backlash can be achieved, ensuring precise positioning and repeatability of the robotic arm end-effector. The integrated flange provides a direct connection, greatly enhancing joint rigidity, suppressing vibration, and improving machining or assembly quality.
Compact & Lightweight: The low cross-section height and lightweight design reduce the inertia at the robot arm's end, increasing movement speed and responsiveness, while lowering the load and energy consumption of drive components.
Simplified Integration: Standard or custom bolt hole patterns on the flange allow the bearing to connect directly to the robot arm body and drive motor (e.g., direct-drive motor or harmonic reducer output), significantly reducing intermediate components, simplifying assembly, and improving system reliability.
Smooth & Quiet Operation: Precision raceways and steel balls ensure extremely low starting and running friction torque, enabling quiet, smooth rotational motion, crucial for scenarios requiring delicate operations.
Cornerstone of Precision Installation: Bolt Circle Diameter Calculator
Correct installation is fundamental to unleashing the full performance and safe operation of Flanged Ball Slewing Bearings. Determining the position distribution of bolt holes on the flange – the Bolt Circle Diameter (BCD) is a critical step in installation design. An online Bolt Circle Diameter Calculator becomes an indispensable tool for engineers:
Accurately Determine Hole Positions: Input the bearing model or basic flange parameters (e.g., outer diameter, number of bolts), and the calculator quickly and accurately provides the diameter of the circle on which the bolt hole centers lie (PCD - Pitch Circle Diameter). This is the basis for drilling mounting holes or designing matching interfaces.
Avoid Design Errors: Manual PCD calculation is error-prone. Incorrect hole positions can lead to difficult installation, uneven stress distribution, or even bearing failure. The calculator provides rapid verification, ensuring design drawing accuracy.
Improve Efficiency: Saves time spent consulting manuals or performing complex calculations, accelerating equipment design and installation preparation.
Adapt to Diverse Needs: Whether for standard models or custom bearings requiring non-standard hole patterns, the calculator offers flexible support.
Driving Green Energy: Solar Tracker Flange Bearings
In solar power plants striving for maximum power generation efficiency, Solar Tracker Flange Bearings are the core motion components ensuring photovoltaic panels always accurately face the sun. Flanged Ball Slewing Bearings demonstrate unique value in this application:
All-Weather Endurance: Featuring special seal designs (e.g., multi-lip seals, weather-resistant rubber) and long-life grease, they effectively resist sand, rain, UV rays, and extreme temperature fluctuations, ensuring long-term maintenance-free operation in harsh outdoor environments.
High Wind Load Resistance: The design must withstand the enormous wind-induced overturning moments from large-area PV panels. The structural strength and rigidity of the bearing are paramount. The flanged design provides a stable mounting foundation.
Low Driving Torque: The low-friction design ensures smooth rotation of the tracking drive system (typically linear actuators or slew drives) with low power consumption, even during cold starts or under snow load.
Precise Angular Positioning: Smooth running characteristics and low backlash guarantee accurate control of solar tracking angles, maximizing energy capture efficiency.
Compactness & Cost-Effectiveness: Compared to other large slewing bearing solutions, the compactness of Flanged Ball Bearings reduces the complexity and cost of the top structure of the mounting tower.
Flanged Ball Slewing Bearings: The Ubiquitous Rotation Solution
Their unique advantages make them the preferred solution for rotational motion in numerous fields:
Industrial Automation & Robotics: Robotic arm joints, rotary tables, precision indexing plates, welding positioners, automated assembly line turntables.
Solar Power Generation: Azimuth and elevation adjustment bearings for single-axis and dual-axis solar tracker systems (core application).
Medical Equipment: CT scanner rotating gantries, X-ray C-arms, rotating components of radiotherapy equipment.
Packaging & Food Machinery: Rotary fillers, capping machines, labeling machine turntables, material distribution turntables.
Construction Machinery: Small crane base rotation, excavator attachment quick coupler rotation, drilling rig components.
Material Handling: Forklift rotating work platforms, stacker rotating forks, conveyor line diverting turntables.
Security & Aerospace: Surveillance PTZ rotation mechanisms, radar antenna mounts, missile launcher azimuth adjustment.
Testing Equipment: Test benches requiring precise rotational positioning.
Why Choose Flanged Ball Slewing Bearings? Core Advantage Analysis
Exceptional Combined Load Capacity: Optimized single-row design efficiently handles combined axial, radial, and overturning moment loads within compact spaces.
Ultimate Space Efficiency: Integrated flange design eliminates additional mounting seats, significantly reducing the overall system height and space occupation.
Ultra-Low Friction Operation: Precision raceways and ball interaction ensure extremely low starting and running torque, guaranteeing smooth, quiet rotation.
Revolutionarily Simplified Installation: Direct bolting drastically reduces part count, shortens assembly time, and lowers installation error risks.
Superior Rigidity & Stability: The rigid, direct connection between flange and main structure effectively suppresses deformation, enhancing system precision and dynamic response.
Highly Flexible Customization: Offers various sizes, flange positions (outer/inner flange), sealing grades (IP protection), preload levels (zero clearance, light preload, etc.), special coatings (anti-corrosion) to meet demanding applications.
Long-Life Sealing & Lubrication: Factory-preloaded with high-performance long-life grease, standard-equipped with efficient seals for effective dust and water protection, extending service life and reducing maintenance frequency.
Insight into Cost Structure: Factors Influencing Flanged Ball Slewing Bearing Price
Bearing price results from the combined effect of technical specifications, material processes, and market demand. Key influencing factors include:
Size & Specifications: Larger physical dimensions (diameter, height/cross-section, flange size) increase material consumption and machining difficulty, naturally raising costs.
Load Capacity Rating: Bearings required to withstand higher dynamic and static rated loads (especially overturning moments) need more robust structural design, higher-grade steel (e.g., vacuum degassed bearing steel), stricter heat treatment processes, and quality control standards, leading to significantly higher prices.
Material & Process:
Steel Grade: Base material cost varies greatly; high-purity, high-hardness bearing steel and special alloy steels cost more.
Heat Treatment: The depth and quality of strengthening processes like carburizing and quenching directly impact life and cost.
Surface Treatment: Zinc plating, Dacromet, special anti-corrosion coatings, etc., add extra cost.
Precision Grade: Bearings used in robots, precision machine tools, or medical equipment require extremely high rotational accuracy (e.g., P4, P2 class) and dimensional tolerances, necessitating ultra-precision grinding and strict inspection, substantially increasing costs.
Flange Customization Degree:
Bolt Holes (BCD): Standard hole patterns have the lowest cost. Non-standard PCD, special hole diameters, counterbores, or additional locating pin holes increase machining difficulty and cost.
Flange Shape: Special contours or non-standard flange sizes require additional machining.
Seals & Lubrication:
Seals: Standard rubber seals are cost-controlled. Special material seals (high-temperature resistant, corrosion-resistant, ultra-low friction like PTFE) or multi-seal structures cost more.
Grease: Long-life, wide-temperature range, food-grade, or special-performance greases add cost.
Preload Requirements: Achieving zero clearance or specific preload requires more precise manufacturing and selection, costing more than standard clearance products.
Brand & Certification: Reputable brands (e.g., LYRADRIVE), known for reliable quality, technical support, and industry certifications (ISO 9001, etc.), typically command higher prices than ordinary manufacturers.
Purchase Quantity: Significant volume discounts are usually available for large orders.
Market & Supply Chain: Fluctuations in raw material prices (especially special steels), energy costs, international logistics fees, and market supply-demand dynamics all impact the final price.
Choose a Professional Partner, Unleash Rotation Potential
Flanged Ball Slewing Bearings are indispensable rotating cores in modern precision machinery. Understanding their principles—from the precise positioning of robotic joints to the reliable operation of solar trackers, and the precise calculation of bolt hole positions—is key to successful application. Facing diverse needs and cost considerations, choosing an experienced, technologically strong supplier is paramount.
Professional Supplier of Flanged Ball Slewing Bearings
LYRADRIVE, as a leading manufacturer of slewing rings, slew drives, and gears, focuses on providing customized solutions for customers. Whether you need standard Flanged Ball Bearings, special specifications for robotic turntables or solar trackers, or complex non-standard designs, LYRADRIVE can leverage deep engineering expertise and a comprehensive production system to provide full-service support from technical consultation and design assistance to manufacturing.