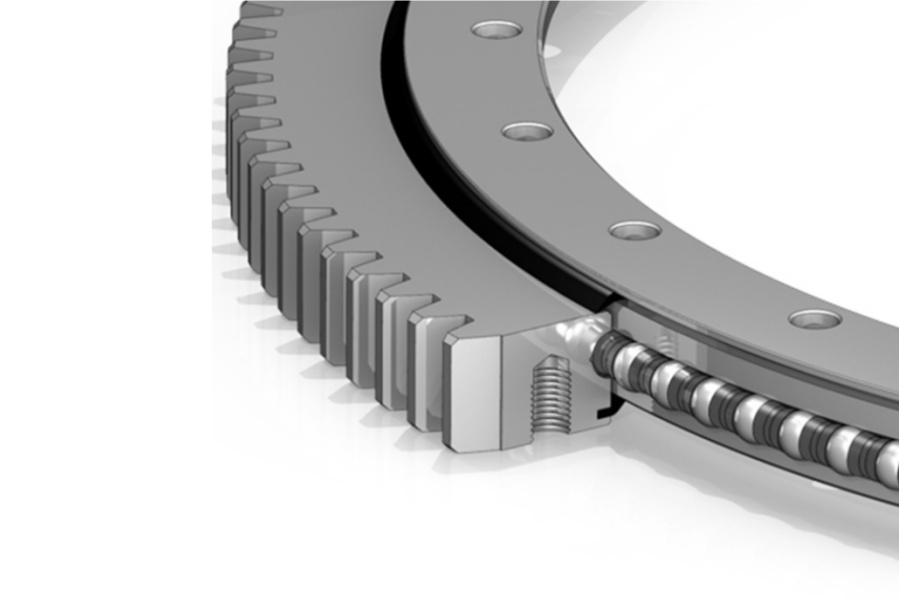
Single Row Slewing Ring Ball Bearings: Small Size, Mighty Power—The Core Pivot of the Rotating World!
What is Single Row Slewing Ring Ball Bearings?
Single Row Slewing Ring Ball Bearings are specialized large rolling bearings designed to simultaneously withstand enormous axial loads (thrust parallel to the axis), radial loads (pressure perpendicular to the axis), and overturning moments. Unlike conventional bearings, they typically exist as large, flat annular units integrated directly into the structure of mechanical equipment (such as between a turntable and base), becoming the core hub for the rotational motion of the device. Their defining feature is a single row of steel balls circulating within raceways, enabling low-friction, high-precision slewing motion between two relatively rotating components (commonly called the "inner ring" and "outer ring"). Their compact cross-sectional height is a significant advantage.
Single Row Slewing Ring: Simple Design, Remarkable Performance
The structure of the Single Row Slewing Ring Bearing is relatively simple and efficient, primarily comprising the following key components:
Inner and Outer Rings: Two large, hardened steel rings with precisely ground raceways. One ring usually features mounting holes (bolt holes) for fixing to the stationary part of the equipment (e.g., the base), while the other is fixed to the rotating part (e.g., the turntable).
Single Row of Steel Balls: The core load-bearing elements, rolling between the raceways of the inner and outer rings. The size, quantity, and material of the balls directly impact the bearing's load capacity and lifespan.
Spacers/Cage: Evenly separates the steel balls, preventing collisions and friction between them, ensuring uniform load distribution and smooth operation.
Seals: Installed between the inner and outer rings, forming an effective sealing cavity to prevent external contaminants (like dust, moisture) from entering the raceways and internal grease from leaking. Crucial for extending bearing life.
Lubrication Channels and Grease Nipples: Facilitate regular greasing, providing continuous lubrication to the balls and raceways, reducing wear and friction heat.
This single-row design offers outstanding advantages: compact structure, relatively light weight, lower manufacturing cost, and smaller installation space requirements. It is particularly well-suited for applications with strict space constraints or cost sensitivity.
Axial and Radial Load Capacity: Small Size Carries Big Burdens
The core value of Single Row Slewing Ring Bearings lies in their exceptional combined load-carrying capacity:
Axial Load Capacity: This is their strongest suit. The single-row design, through optimized contact angles (typically 45° or 90°) between the balls and raceways, efficiently handles enormous thrust loads parallel to the rotation axis (e.g., vertical pressure from a crane boom, thrust from wind turbine blades).
Radial Load Capacity: While axial strength is paramount, the design also allows for significant simultaneous bearing of loads perpendicular to the rotation axis (e.g., centrifugal forces from rotating parts, lateral forces in certain operating conditions).
Overturning Moment Capacity: When a load acts off-center, creating a tendency to overturn the equipment, the single-row bearing effectively resists this moment through its raceway and ball force design, maintaining equipment stability. Its moment capacity is usually closely related to the bearing diameter and structural design.
Crucial Note: The load capacity of a single-row bearing is a comprehensive reflection under the combined action of the three loads mentioned above. When selecting a bearing, it is essential to perform precise calculations and selection based on the maximum axial force, radial force, and overturning moment in the actual application, combined with factors like speed and duty cycle, and include a sufficient safety margin. Never judge based on a single load data point!
Slewing Ring Mounting Instructions: Precision Placement, Stable Reliability
Correct installation is the absolute prerequisite for ensuring Single Row Slewing Ring Bearings deliver optimal performance and achieve their expected lifespan. Any installation deviation can lead to stress concentration, abnormal wear, or even premature failure. Strictly follow these key steps:
Foundation Preparation:
Support Structure Rigidity: The mounting base (upper and lower flanges) must possess extremely high rigidity and flatness to effectively distribute enormous loads and prevent deformation. Weak structures are a common cause of bearing failure.
Mounting Surface Machining: The mounting surfaces (flange faces) mating with the bearing must be precision machined to ensure their flatness and levelness (or perpendicularity) are within the extremely tight tolerances strictly specified by the bearing manufacturer (often demanding, e.g., 0.1mm/m or stricter). Rough or deformed mounting surfaces are disastrous.
Cleanliness: Thoroughly clean all mounting surfaces, bolt holes, and bolts, removing any contaminants like oil, metal chips, or burrs.
Bearing Handling and Positioning:
Use appropriate lifting tools (e.g., eyebolt holes) to hoist the bearing smoothly, avoiding impacts or deformation. Carefully lower it into position.
Make preliminary adjustments to ensure bolts can pass smoothly through the mounting holes.
Bolt Tightening: Critical!
Use Specified Bolts: Must use high-strength bolts (typically Grade 10.9 or 12.9), flat washers, and high-strength nuts as specified or approved by the bearing manufacturer. Standard bolts cannot withstand the high preload forces.
Thread Treatment: Apply a suitable amount of anti-seize compound (e.g., molybdenum disulfide paste, avoid ordinary grease) to the threads to ensure bolts achieve the intended torque.
Tightening Sequence and Torque:
Follow the manufacturer's diagonally and crosswise tightening sequence diagram (extremely important!). Tighten bolts incrementally in multiple passes (usually at least 3 times).
Use a calibrated torque wrench and tighten strictly to the manufacturer's specified final torque value. Insufficient torque causes joint loosening and fretting wear; excessive torque risks bolt breakage or ring deformation.
After final tightening, it's recommended to re-check and tighten the bolts once more in sequence after a period of operation (e.g., 24-48 hours).
Alignment Check (Critical Step):
After tightening the bolts, use precision measuring tools (e.g., dial indicator) to check the face runout (axial runout) and radial runout of the bearing's inner and outer rings. Values must be strictly controlled within the manufacturer's allowable tolerances. Exceeding tolerances indicates a serious installation problem—find the cause (often support structure deformation or uneven mounting surfaces) and correct it.
Lubrication and Seals:
Before or after installation, fill with the specified type and sufficient quantity of grease via the grease nipples.
Carefully inspect seals to ensure they are intact and correctly installed.
Applications of Single Row Slewing Ring Ball Bearings: Ubiquitous Rotational Power
Thanks to their compact efficiency and cost-effectiveness, Single Row Slewing Ring Bearings play a central role in numerous devices requiring reliable rotational support:
Construction Machinery: Rotation bases for small to medium excavators, loaders, forklifts, truck cranes, aerial work platforms.
Material Handling: Light to medium stackers, small port cranes, slewing mechanisms for conveyor belts.
Renewable Energy: Rotating supports in solar photovoltaic single-axis and dual-axis tracking systems (requiring lightness and low torque).
Agricultural Machinery: Rotation components in irrigation equipment (e.g., center pivot irrigators), harvesting machinery.
Industrial Automation: Welding positioners, small rotary tables, indexing devices, robot bases.
Medical Equipment: Components requiring precision rotation in CT scanners, X-ray machines (special high-precision, low-noise requirements).
Defense & Aerospace: Radar antenna pedestals, missile launchers, ground support equipment (special environmental adaptability requirements).
Amusement Rides: Rotation support structures for medium and small amusement rides like Ferris wheels, carousels.
Shining Characteristics of Single Row Slewing Ring Ball Bearings
Compact Structure, Space-Saving: The single-row design offers minimal cross-sectional height, ideal for space-constrained applications.
Lightweight: Significantly lighter than multi-row bearings, helping reduce overall equipment weight and rotational inertia.
High Cost-Effectiveness: Relatively simple structure results in lower manufacturing costs than multi-row bearings, offering an economical solution.
Low Starting Torque & Running Resistance: Optimized raceway design and precision balls ensure smooth, effortless operation.
High Precision Rotation: Precisely ground raceways and strict tolerance control provide stable rotational accuracy.
High Load-Carrying Efficiency: Achieves an excellent combination of axial, radial, and moment load capacities within a compact space.
Easy Installation & Maintenance: Supplied as a self-contained unit for relatively straightforward mounting; grease points facilitate routine maintenance.
Diverse Configurations: Available with different gear ring options (internal, external, non-geared), seal types, lubrication methods, and mounting hole patterns to meet specific needs.
Factors Influencing the Price of Single Row Slewing Ring Ball Bearings: Considerations Behind Value
Size and Specifications: Diameter (D) and Cross-Section Height (H) are the most fundamental determinants. Larger diameters and greater heights (even within the single-row category) significantly increase material requirements, machining time, and energy consumption, naturally driving up the price.
Materials and Heat Treatment:
Ring Material: Typically high-hardenability alloy structural steel (e.g., 42CrMo, 50Mn). Steel grade, purity, and flaw detection requirements directly affect cost and performance.
Ball Material: High-purity bearing steel (e.g., GCr15) is standard; special applications (e.g., corrosion, high temperature) may use stainless steel or ceramic balls, increasing cost.
Heat Treatment Process: Ring raceways and balls undergo complex, rigorous quenching and tempering to achieve required hardness and toughness depth. Process control level (e.g., quenching uniformity, distortion control) greatly impacts lifespan and is a major cost component.
Manufacturing Precision and Tolerance Grade: Higher requirements for raceway geometric accuracy (roundness, straightness), surface finish, grinding precision post-heat treatment, and clearance control (e.g., for medical, precision turntable applications) increase machining difficulty, potentially raise scrap rates, and make the bearing more expensive.
Gear Ring Machining
Geared vs. Non-Geared: Non-geared rings are the least expensive. Geared rings (internal or external) require additional gear machining processes (hobbing/shaping, grinding).
Gear Accuracy Grade: The precision grade of the gear (e.g., DIN 6 vs. DIN 8) greatly affects meshing smoothness, noise, and lifespan; high-precision gear machining significantly increases costs.
Sealing System:
Seal Type and Quantity: Simple single-lip rubber seals are low cost. Complex multi-lip seals, labyrinth seals, or seals using special materials (e.g., fluorocarbon rubber, polyurethane) for extreme environments (high/low temperature, corrosion resistance, wear resistance) substantially increase costs.
Lubrication System: Standard grease nipples and internal passages are basic. Special requirements like centralized lubrication interfaces or more lubrication points add cost.
Special Requirements and Certifications:
Special Conditions: Requirements for cryogenic resistance (below -40°C), high-temperature resistance (above 120°C), vacuum environments, ultra-high cleanliness (semiconductors) necessitate specific materials, processes, and validation, significantly increasing costs.
Special Coatings: Surface treatments like zinc plating, Dacromet, or phosphating for corrosion protection add cost.
Certification Requirements: Meeting specific industry standards (e.g., CE, DNV GL, API) or customer-specific certifications involves additional testing and documentation, also raising the price.
Order Quantity: Bulk purchases usually secure better unit prices (spreading tooling, fixture, and setup costs).
Brand Premium and Supply Chain: Reputable brands command higher prices due to technological expertise, quality consistency, and after-sales service. Supply chain efficiency (raw material procurement, production management, logistics) also impacts final cost.
Market Supply/Demand and Raw Material Fluctuations: Fluctuations in the prices of raw materials like steel and alloying elements directly affect manufacturing costs. Market supply and demand dynamics at specific times also influence pricing.
Supplier of Single Row Slewing Ring Ball Bearings
LYRADRIVE is a professional slewing bearings ,slew drive and gears manufacturer provides customized slew bearing, drive and gears.For application-specific engineering solutions, contact LYRA to discuss technical specifications and implementation strategies.