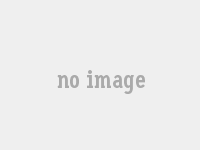
Flanged Ball Slewing Bearings: The Ultimate Guide to Unlocking Performance and Efficiency
What is a Flanged Ball Slewing Bearing?
At its core, a Flanged Ball Slewing Bearing is a specialized type of slewing ring bearing. It features a single row of ball bearings meticulously arranged within raceways formed by two concentric rings – typically an inner ring and an outer ring. The defining characteristic, as the name suggests, is the integrated flange. This flange, usually projecting radially outward from one of the rings (most commonly the outer ring, but sometimes the inner), provides a direct and secure mounting surface. This design eliminates the need for separate, complex mounting plates or housings, drastically simplifying installation and enhancing structural rigidity. The balls, often precision-ground, efficiently handle combined loads, making these bearings ideal for applications requiring high load capacity within a constrained envelope.
The Power of Integrated Flange Ball Bearings
The integration of the flange isn't just a minor convenience; it's a transformative design feature. This Integrated Flange Ball Bearing approach delivers several critical benefits:
Simplified Mounting: Direct bolt-on capability significantly reduces assembly time, complexity, and potential for mounting errors compared to bearings requiring separate housings or adapter plates.
Enhanced Rigidity: The direct connection between the bearing ring and the machine structure through the flange creates a stiffer, more robust assembly. This minimizes deflection under load, improving accuracy and reducing wear.
Space Optimization: By eliminating bulky external mounting hardware, the overall system footprint is minimized. This is crucial in applications where space is at a premium, like robotics or compact machinery.
Improved Alignment: Precise machining of the mounting flange helps ensure proper alignment during installation, contributing to optimal bearing performance and longevity.
Cost Efficiency: Reduced part count (no need for separate housings/plates) and simplified installation translate into lower overall system costs.
Embracing Compact Slewing Ring Design
Flanged Ball Slewing Bearings inherently embody a Compact Slewing Ring Design. Compared to traditional rolling element bearings or slewing bearings without integrated mounting features, they offer a significantly lower cross-section height relative to their load-carrying capacity. This compactness is a direct result of the efficient ball path design and the elimination of external mounting structures. This low-profile nature allows engineers to design slewing mechanisms that are lighter, more streamlined, and can fit into tighter spaces without sacrificing performance. This compactness is a key driver for their adoption in modern, space-conscious machinery.
Crucial Considerations: Flange Mounting Torque Specs
Achieving the full potential of a Flanged Ball Slewing Bearing hinges critically on correct installation, and a paramount aspect of this is adhering to the specified Flange Mounting Torque Specs. Applying the correct torque to the mounting bolts is essential for:
Securing the Bearing: Preventing movement or slippage under operational loads.
Maintaining Preload: Ensuring the bearing internal clearance is correctly set (if applicable) for optimal stiffness and load distribution.
Distributing Load Evenly: Preventing localized stress concentrations on the flange or the mounting structure, which can lead to fatigue failure.
Avoiding Damage: Over-tightening can deform bearing rings, damage threads, or crush components, leading to premature failure. Under-tightening risks bolt loosening, slippage, and catastrophic detachment.
Always consult the manufacturer's specific torque specifications for your bearing model and bolt size. These specs are determined based on bolt grade, material, lubrication, and the specific bearing design. Using a calibrated torque wrench and following the recommended tightening sequence (typically a star pattern) is mandatory. Ignoring these specs compromises safety, performance, and bearing life.
Where Flanged Ball Slewing Bearings Reign Supreme: Key Applications
The unique blend of compactness, high load capacity, and simplified mounting makes Flanged Ball Slewing Bearings indispensable across diverse sectors:
Material Handling: Crane jibs, slewing platforms on forklifts, automated storage and retrieval systems (AS/RS), conveyor diverters.
Construction Equipment: Excavator attachments (like compactors, grapples), compact loader attachments, small crane bases, drilling rig components.
Wind Energy: Pitch and yaw systems in smaller turbines or critical components within larger nacelles.
Robotics & Automation: Robotic arms (especially joints), rotary indexing tables, precision positioning stages, automated welding equipment.
Medical & Imaging: CT scanner gantries, radiation therapy equipment requiring precise rotation.
Defense & Aerospace: Turret systems, radar mounts, missile launcher positioning.
Packaging Machinery: Rotary fillers, capping machines, labeling turntables.
Renewable Energy: Solar tracker systems for positioning panels.
Why Choose Flanged Ball Slewing Bearings? Defining Characteristics
Beyond their integrated flange, these bearings offer a compelling set of features:
High Load Capacity: Efficiently handle combined loads (axial, radial, moment forces) despite their compact size.
Space Efficiency: Significantly reduce the overall height and footprint of the rotational assembly.
Low Friction & Smooth Operation: Precision-ground balls and raceways ensure low starting and running torque, enabling precise, smooth rotation.
Simplified Design & Assembly: The integrated flange drastically reduces parts count and assembly complexity.
Rigidity & Stability: Direct mounting enhances structural integrity and minimizes deflection.
Versatility: Available in various sizes, flange configurations (outer or inner ring), sealing options, and preload levels to suit specific needs.
Pre-Lubrication & Sealing: Often supplied pre-lubricated for life and equipped with seals to protect against contaminants, extending service life and reducing maintenance.
Understanding the Investment: What Influences Flanged Ball Slewing Bearing Price?
Size & Dimensions: Larger bearings naturally require more raw material and complex machining, increasing cost.
Load Capacity & Rating: Bearings engineered for higher dynamic and static load ratings involve more robust designs, higher-grade materials, and stricter quality control, commanding a premium.
Material Grade: The quality of the steel used for rings and balls significantly impacts durability, fatigue life, and cost. High-alloy steels or specialized treatments increase price.
Precision & Accuracy Class: Bearings requiring ultra-high running accuracy (e.g., for medical imaging or precision robotics) demand more meticulous manufacturing processes and grinding, raising costs.
Flange Design & Complexity: The size, thickness, number of bolt holes, and machining tolerances of the flange itself add to manufacturing complexity and cost. Custom flange patterns are more expensive than standard.
Seals & Lubrication: High-performance seals (e.g., multi-lip, special elastomers) and specific, long-life lubricants add cost.
Customization: Standard bearings are most economical. Any deviation – special bolt patterns, unique bore sizes, modified seals, specific preloads, special surface treatments – incurs engineering and setup costs.
Brand Reputation & Quality Assurance: Established manufacturers with rigorous quality control processes (ISO certifications) often command higher prices due to proven reliability and support.
Quantity: Significant volume discounts are typically available for larger orders.
Supply Chain & Market Factors: Raw material costs (steel prices), energy costs, transportation logistics, and overall market demand can cause price fluctuations.
Supplier of Flanged Ball Slewing Bearing
LYRADRIVE is a professional slewing bearings ,slew drive and gears manufacturer provides customized slew bearing, drive and gears.For application-specific engineering solutions, contact LYRA to discuss technical specifications and implementation strategies.