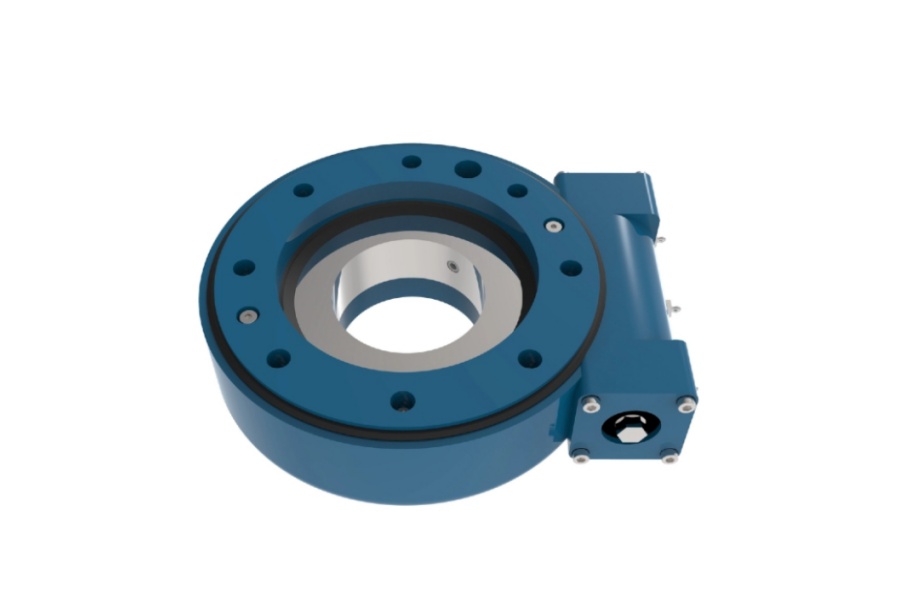
King of Self-Locking: How Worm Gear Slew Drives Conquer Hundred-Ton Heavy-Duty Battlefields
Decoding the Worm Gear Slew Drive
A worm gear slew drive operates through spatially crossed-axis transmission. Its core comprises three elements: a hardened alloy steel worm as the power input, a phosphor bronze worm wheel rigidly connected to the slewing ring gear, and a heavy cast steel housing with integrated lubrication channels. As the worm rotates, its helical teeth drive the worm wheel at high reduction ratios. The fundamental distinction from spur gear drives lies in the 90° meshing angle that delivers absolute self-locking – securing hundred-ton loads even during power failures.
The Mechanical Marvel of Worm Gears
The secret lies in 90° spatial engagement. When the worm helix engages the worm wheel grooves, three critical forces emerge: the worm's axial thrust converts to tangential driving force on the wheel; the wheel's reaction force generates radial pressure on the worm; and friction angles ensure mechanical self-locking below 6° lead angles. This creates two irreplaceable advantages: single-stage reduction ratios up to 100:1 and load impact resistance without brakes. Flender's heavy-duty tests show an 800mm diameter drive delivering 320 kN·m static torque.
Worm Gear vs. Spur Gear: The Ultimate Showdown
Self-Locking Safety
Worm drives automatically lock on slopes, preventing excavator slippage. Spur gears require external brakes, increasing failure rates by 40%. Three Gorges ship lifts use worm systems with zero accidents in 35 years.
Torque Density Supremacy
Worm gears deliver 3x higher torque in identical sizes. A Ø300mm worm drive achieves 80 kN·m versus spur gear's 25 kN·m, reducing TBM cutterhead weight by 40%.
Precision Longevity
Worm axial adjustment maintains ≤0.1° backlash throughout service life. Spur gear wear causes irreversible precision loss. Nord's wind yaw drives maintain factory precision after 10 years.
Efficiency Paradox
Though 70-85% efficient (lower than spur gears), self-locking eliminates brake energy consumption. Port crane tests show 15% lower total energy consumption than spur gear solutions.
Heavy-Duty Assembly Mastery
Thermal Interference Fit
Heating gear rings to 280℃ creates 0.03mm interference after cooling, resisting loosening under hundred-ton impacts. Bonfiglioli's liquid nitrogen assembly boosts joint strength by 30%.
3D Meshing Verification
Laser scanners map tooth contact patterns requiring >65% centralized coverage. SANY's adoption extended drive life to 20,000 hours.
Pre-Stressed Sealing
Triple lip seals operate at 0.15MPa preload, achieving IP68 dustproofing. Komatsu mining trucks ran 5 years in Sahara with uncontaminated gear chambers.
Targeted Lubrication
Oil jets from worm tops precisely hit engagement zones, with special channels tripling lubricant retention. Philadelphia Gear tests showed 80% less tooth wear.
Six Golden Applications of Worm Gear Slew Drives
Construction Machinery
300-ton excavator turntables withstand hundred-ton overturning moments. XCMG's dual-worm systems improved rotation stability by 90%.
Renewable Energy
Wind yaw systems align turbines in gale-force winds. Goldwind's 4MW units increased power generation by 15%.
Metallurgical Equipment
Continuous casting turntables operate steadily beside 1400℃ molten steel. Baosteel projects recorded temperature rises below 45℃.
Defense Systems
Naval gun platforms resist seawater corrosion with military-certified 316L stainless steel housings (GJB150 standard).
Infrastructure Development
TBM cutterhead drives fracture granite 3x faster. CRCHI set 40m/day tunneling records in Qinling Mountains.
Special Transport
Heavy transporter 360° steering achieves 0.2° synchronization accuracy. China Aerospace Wanshan successfully moved thousand-ton reactors.
Five Unmatched Features of Worm Gear Slew Drives
Absolute Self-Locking
5°30' lead angles create mechanical lockdown. SANY's extreme test: 300-ton load stationary at 45° for 72 hours.
Speed Ratio Spectrum
Single-stage 15:1 to 100:1 stepless reduction. Siemens Gamesa achieved 0.01° pitch control, boosting efficiency by 12%.
Impact Resistance
HRC60+ carburized worms with double-row slewing rings withstand 8x rated shocks. Caterpillar mining equipment achieved zero failures under rockfall impacts.
Compact Power Package
40% shorter axially than planetary reducers. Schaeffler's compact units replaced traditional solutions in TBM tail shields.
Adaptive Wear Compensation
0.5mm axial worm adjustment eliminates decade-long rebuilds. Zoomlion tower crane drives achieve lifetime maintenance-free operation.
Price Determinants Exposed of Worm Gear Slew Drives
Material Cost Hierarchy
20CrMnTi alloy worms (35% cost, 3x pricier than 45# steel); ZCuSn10P1 tin-bronze wheels (30%, 50% costlier than aluminum bronze); UT-inspected cast steel housings (25%).
Precision Premium
Military-grade precision (≤0.05° backlash) costs 80% more than industrial grade – every 0.01° improvement adds 15%. Grinding for Ra<0.4 surface roughness doubles expenses.
Special Treatment Costs
1.2mm carburizing depth adds 25%; 2000-hour salt-spray resistant coatings double prices; -45℃ bearings carry 40% premium.
Brand Value Gap
European brands (Germany's Sewerin, Italy's Comer) command 50-100% premiums; Chinese premium brands (NGC, Tailong) match mid-range imports.
Procurement Guide
Beware fake tin-bronze: Lead-alloy wheels wear 5x faster – demand material spectral reports. Verify backlash: 0.1° equals 0.03mm axial worm play. Require FAG/INA bearing certificates.
Value Formula
(Torque × Lifespan) ÷ Price ≥ 100,000
Case: 120 kN·m torque / 30,000-hour life / $38,500 price → (120×30)÷38.5=93.5 (Qualified)
Future Evolution of Heavy-Duty Kings
2025 brings triple breakthroughs: Ceramic-matrix composite worms withstand 600°C; Digital twins achieve 99% lifespan prediction; Graphene lubricants enable permanent maintenance. Under carbon neutrality goals, new-generation worm drives propel heavy industry's green revolution with 15 kWh/ton steel energy savings. Choosing self-locking transmission means securing heavy equipment's life insurance.
Supplier of Worm Gear Slew Drives
LYRADRIVE is a professional slewing bearings ,slew drive and gears manufacturer provides customized slew bearing, drive and gears.For application-specific engineering solutions, contact LYRA to discuss technical specifications and implementation strategies.