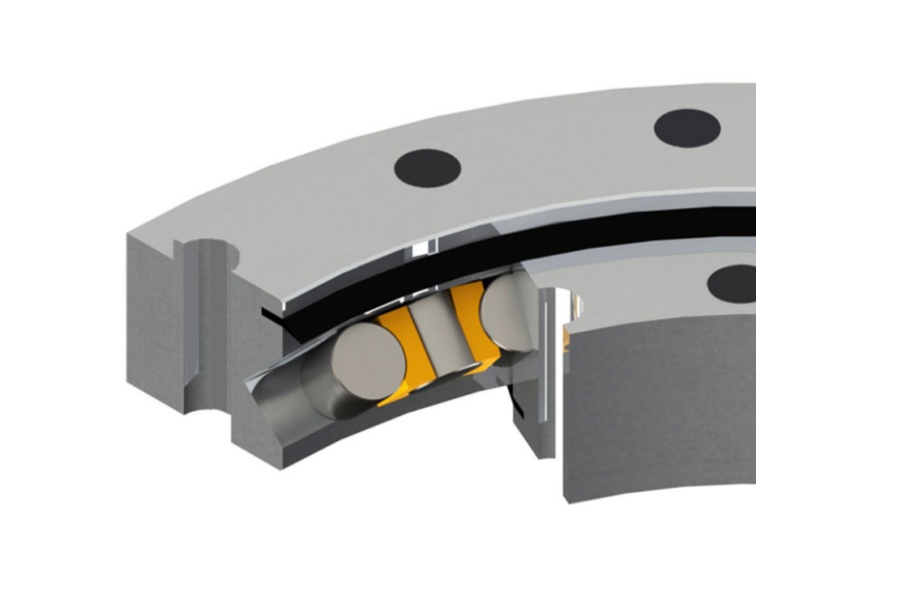
Unlock Nanoscale Precision: The Unsung Engine Powering the Semiconductor Revolution
What Defines a Crossed Roller Slewing Bearing?
Imagine a bearing engineered to conquer physics: simultaneously handling crushing radial loads, powerful axial thrusts, and destabilizing moment forces within a space no thicker than your finger. This is the reality of crossed roller slewing bearings. Their secret lies in a revolutionary 90° cross-arrangement of cylindrical or tapered rollers between hardened steel rings. Each roller aligns perpendicular to its neighbor, creating a dense matrix of linear contact points. This ingenious design achieves what traditionally required multiple bearings: consolidating radial support, thrust handling, and tilt resistance into one ultra-compact unit. The result? Uncompromised motion accuracy, zero wasted space, and rock-solid stability under punishing loads.
Semiconductor Wafer Stage Bearings: Where Atomic-Level Precision Reigns
At the core of every chip-making lithography machine lies a wafer stage demanding movements measured in nanometers. Crossed roller bearings here are non-negotiable:
Sub-Micron Accuracy: Positional repeatability exceeding ±0.001° ensures circuit patterns align perfectly across 300mm wafers, directly impacting yield.
Absolute Contamination Control: Manufactured in ISO Class 3 cleanrooms with vacuum-compatible materials (stainless steel 440C, special coatings) and low-outgassing lubricants to prevent molecular contamination.
Thermal Stability: Engineered with materials and designs minimizing thermal growth, critical when laser energy impacts the stage.
Vibration-Free Operation: Mirror-finish raceways and nanometer-level roundness eliminate micro-vibrations that distort exposure patterns.
Stiffness Under Acceleration: With wafer stages accelerating at >2G, the bearing’s line-contact rigidity prevents distortion during rapid step-and-settle motions. Fail here, and billions in fab investment stall.
Mastering the Art: Preload Adjustment in Crossed Roller Bearings
Preload isn't just a setting; it's the cornerstone of performance. Applying controlled internal force eliminates clearance, transforming bearing behavior:
Eliminating Dead Zone: Zero clearance means immediate response to reversal, crucial for precision positioning.
Boosting System Stiffness: Preloaded bearings can be 300% stiffer, reducing deflection under load for truer positioning.
Suppressing Vibration: Tensioned rollers dampen resonance, critical in high-speed spindles and imaging systems.
Extending Service Life: Proper preload optimizes load distribution, preventing roller skidding and premature wear.
Methods Matter: Precision ground spacers, selective assembly of rollers, or adjustable split housings achieve preload. Under-preload risks inaccuracy; over-preload generates heat and early failure. Expertise is paramount.
Zero Backlash Rotary Tables: The Precision Amplifier
When absolute positional fidelity is non-negotiable, crossed roller bearings are the engine of choice for zero-backlash rotary stages:
Inherently Near-Zero Backlash: The cross-roller design, combined with precision preload, minimizes inherent clearance far below ball bearings.
Direct Drive Compatibility: Their high rigidity and smooth motion integrate seamlessly with direct-drive motors, eliminating gear-induced backlash entirely.
Microradian Repeatability: Essential for laser machining, optical alignment, and coordinate measuring machines (CMMs) where arc-second repeatability is standard.
Dynamic Stiffness: Maintains positional integrity even under changing cutting forces or high acceleration/deceleration.
Integrated Solutions: Often supplied as pre-assembled units with mounting surfaces, motor interfaces, and integrated encoders – plug-and-play precision.
Powering Innovation: Where Crossed Roller Bearings Reign Supreme
These bearings are the silent enablers across critical industries:
Semiconductor Front-End: Lithography scanners, wafer inspection systems, etching equipment stages.
Industrial Robotics: Articulated arm joints (base, shoulder, wrist), collaborative robot precision axes.
Medical Technology: CT/MRI gantry rotation, surgical robot arms, proton therapy nozzle positioning.
Aerospace & Defense: Satellite antenna pointing systems, EO/IR targeting turrets, flight simulator platforms.
Advanced Manufacturing: 5-axis CNC trunnion tables, ultra-precision grinding spindles, laser cutting rotary axes.
Metrology: CMM rotary tables, optical comparator stages, interferometer bases.
Energy: Concentrated solar power (CSP) heliostat trackers, fusion reactor component positioning.
The Unbeatable Edge: Six Hallmarks of Crossed Roller Superiority
Triaxial Load Mastery: Uniquely conquers combined radial, axial, and moment loads in a single row – unmatched space efficiency.
Ultimate Rigidity: Line contact provides 3-5x higher stiffness than comparable ball bearings, minimizing deflection under load.
Nanoscale Precision Capability: Engineered for sub-micron runout and arc-second repeatability – the gold standard for critical motion.
Compact Revolution: Delivers the performance of a multi-bearing stack in a fraction of the axial space – ideal for miniaturization.
Buttery-Smooth Motion: Precision grinding and optimized roller geometry ensure low torque variation and ultra-quiet operation.
Simplified Integration: Pre-engineered, pre-lubricated, and often pre-mounted units drastically reduce assembly time and complexity.
Decoding the Investment: Key Drivers of Crossed Roller Bearing Cost
Understanding price variables (from $1k to $100k+) ensures optimal value:
Precision Grade: The dominant factor. Jumping from ABEC 1 (P0) to ABEC 7 (P4) or ABEC 9 (P2) precision multiplies machining, inspection, and handling costs exponentially. Semiconductor-grade bearings command premium pricing.
Materials & Treatments: Standard bearing steel (GCr15) is baseline. Corrosion-resistant stainless steels (440C, 17-4PH), specialized coatings (CrN, DLC), vacuum-hardening, or cryogenic treatments add significant cost.
Size & Capacity: Larger diameters and widths increase material volume exponentially and demand larger, more expensive machining centers. High moment capacity designs require robust structures.
Specialized Features: Vacuum compatibility (special seals, low-outgassing materials), integrated encoders or motors, custom flange patterns, dedicated lubrication systems, or extreme environment (cryogenic/high-temp) certification add layers of cost.
Preload & Accuracy Requirements: Ultra-low backlash specifications or tightly controlled friction torque demand selective grading of rollers and painstaking assembly, increasing labor time.
Brand Provenance & Support: Premium European/Japanese brands (Schaeffler, THK, IKO) carry R&D and reliability premiums. Comprehensive technical support, custom engineering, and global service networks add value reflected in price.
Order Volume & Customization: High-volume standard parts offer economies of scale. Prototypes or highly customized one-offs incur substantial setup and engineering charges.
The Indispensable Axis of Progress
Crossed roller slewing bearings are more than components; they are the bedrock upon which modern precision is built. Their mastery over space constraints, multidimensional loads, and microscopic accuracy makes them irreplaceable in the machines defining our technological frontier – from creating chips that power AI to enabling robots that perform delicate surgery.
Choosing the right crossed roller solution demands more than a catalog lookup. It requires a deep understanding of your application’s true demands: the interplay of forces, the criticality of precision, the constraints of space, and the rigors of the environment. Partnering with experts who grasp the nuances of preload, material science, and manufacturing tolerances is key to unlocking performance and value. In the relentless pursuit of smaller, faster, and more precise, selecting the perfect "precision motion engine" isn't just an engineering decision – it's a strategic imperative for leading the next wave of innovation.
Supplier of Crossed roller slewing bearings
LYRADRIVE is a professional slewing bearings ,slew drive and gears manufacturer provides customized slew bearing, drive and gears.For application-specific engineering solutions, contact LYRA to discuss technical specifications and implementation strategies.