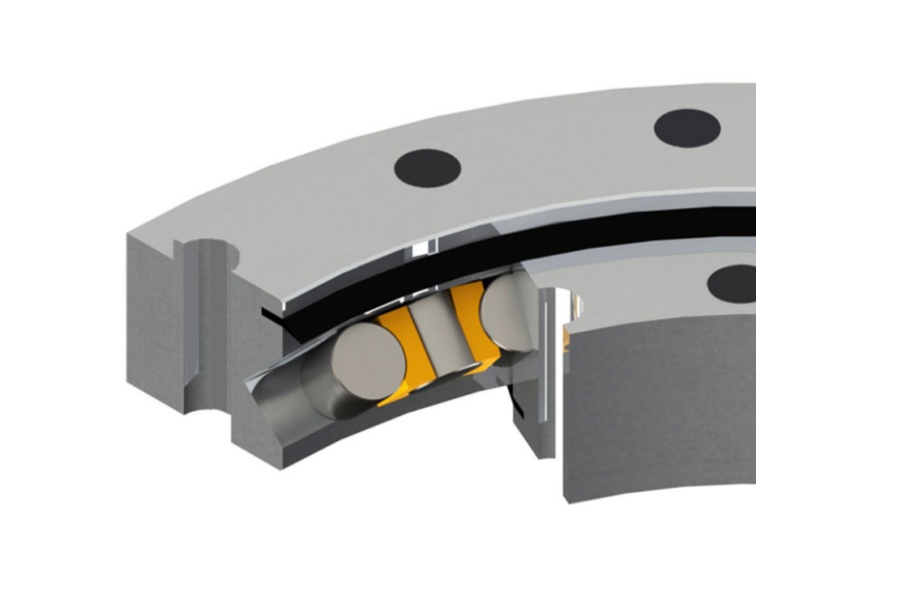
Crossed Roller Slewing Bearings: The Core Powerhouse of Industrial Precision Rotation
What Are Crossed Roller Slewing Bearings?
Imagine a bearing capable of withstanding immense radial forces, axial forces, and even overturning moments within an extremely compact space while maintaining exceptional rotational accuracy and rigidity. This defines the core capability of crossed roller slewing bearings. Their name directly reveals their key structural feature: precision cylindrical or tapered rollers are arranged in a 90-degree cross pattern between the inner and outer rings. This ingenious design allows a single bearing to replace the combination of thrust and radial bearings traditionally required, significantly simplifying mechanical structures, saving valuable space, and delivering outstanding load performance and motion accuracy.
High-Precision Slewing Bearings: The Pinnacle of Precision Engineering
When applications demand stringent requirements for rotational stability, repeat positioning accuracy (often reaching ±0.001° or higher), minimal vibration, and negligible runout errors, high-precision crossed roller slewing bearings stand as the undisputed solution. Their extraordinary performance stems from meticulous manufacturing processes:
Ultra-Precision Raceway Grinding:Raceway surfaces undergo mirror-level grinding, achieving nanoscale roughness to minimize rolling resistance and ensure butter-smooth operation.
Material Science and Heat Treatment:High-purity bearing steel (e.g., GCr15) undergoes specialized heat treatments (such as carburizing or bainitic hardening) to achieve ultra-high surface hardness (HRC 58–62) and a tough core, balancing wear resistance and impact toughness.
Preload Control:Precisely calculated and applied preload eliminates internal clearance, significantly enhancing system rigidity and rotational accuracy while suppressing vibration and noise during high-speed operation.
Strict Dimensional Tolerances and Geometric Precision:Dimensional tolerances for inner/outer rings and rollers are controlled at the micron (μm) level, with roundness and parallelism reaching sub-micron precision, ensuring uniform load distribution and preventing premature failure due to localized stress.
Clean Assembly Environment:Assembled in controlled temperature, humidity, and ultra-clean rooms (ISO Class 5 or higher) to eliminate contaminants that could compromise bearing life and performance.
Crossed Roller vs. Ball Bearings: A Critical Choice
In applications requiring slewing motion, crossed roller bearings often compete with four-point contact ball bearings. Understanding their core differences is key to making an informed decision:
Load Capacity: Crossed Rollers Win!Roller-to-raceway line contact supports several times more radial, axial, and moment loads than the point contact of ball bearings in the same size. This is decisive in heavy-load or complex-force applications (e.g., large robotic arm bases).
Rigidity and Accuracy: Rollers Excel!Line contact delivers higher rigidity, meaning less deformation under load, a more stable rotational axis, and far superior positioning/repeatability accuracy versus ball bearings. This is critical for semiconductor lithography machines and precision measurement turntables.
Compactness: Rollers Lead!A single-row crossed roller design replaces the function of double-row ball bearings, saving up to 50% axial space—a huge advantage in space-constrained devices (e.g., inside articulated robots).
Frictional Torque: Ball Bearings Lower!Point-contact ball bearings typically offer lower starting and running friction. This can be a plus for ball bearings in applications demanding minimal energy consumption or ultra-low-speed smoothness (e.g., astronomical telescopes).
Cost Consideration: Ball Bearings More Economical!The relatively complex manufacturing process makes crossed roller bearings generally more expensive than comparable four-point contact ball bearings. For less extreme precision/load needs, ball bearings offer better value.
Vibration and Noise: Ball Bearings Quieter!Ball bearings usually run smoother with lower vibration and noise—important in noise-sensitive environments like medical or office automation equipment.
Impact Resistance: Rollers Tougher!Roller structures generally withstand shock loads better.
Crossed Roller Slewing Bearings: The Heart of Cutting-Edge Technology
Their exceptional characteristics make them the "rotating heart" in numerous high-precision fields:
Industrial Robots:Serve as core joint bearings (base, shoulder, wrist), providing high rigidity and precision rotation for accurate positioning and smooth trajectory in high-speed motion.
Precision Machine Tools:Used in CNC rotary tables, indexing heads, and milling heads for precise workpiece indexing, multi-face machining, and complex contour milling—central to enhancing machining accuracy.
Semiconductor Manufacturing:Core rotating components in high-precision motion platforms like photolithography wafer stages and inspection equipment carriers—their accuracy directly impacts chip yield.
Medical Imaging Equipment:Support rotation in CT scanner gantries and position gamma knife treatment heads precisely, relying on smooth, low-vibration, high-accuracy rotation for clear imaging or accurate therapy.
Aerospace & Defense:Provide stable, reliable rotation and precise pointing in radar antenna mounts, electro-optical tracking turrets, and missile launchers under extreme conditions.
Precision Measurement Instruments:Ensure stable measurement references and accurate rotational positioning in CMM turntables and laser tracker bases.
Renewable Energy:Enable solar tracker systems to efficiently align photovoltaic panels with the sun.
Why Choose Crossed Roller Slewing Bearings? Six Key Advantages
Unparalleled Load Capacity:Single-row design efficiently handles radial, axial, and high overturning loads simultaneously, simplifying design and boosting reliability.
Exceptional Rigidity:Line contact delivers high rigidity, minimizing deformation under load, stabilizing the rotational center, and enhancing overall equipment accuracy and dynamic performance.
Micron-Level Precision:Built for precision, offering high rotational (running) accuracy and repeat positioning accuracy (commonly ±0.0001°), meeting the strictest demands.
King of Compact Design:Occupies minimal axial space compared to equivalent bearing combinations, enabling smaller, lighter equipment.
Smooth, Stable Operation:Optimized raceway design and precision manufacturing ensure low friction, vibration, and noise, extending equipment life and improving user experience.
Simplified Installation & Maintenance:Delivered as pre-adjusted, preloaded units for easy installation, reducing on-site adjustments and maintenance complexity.
Key Factors Influencing Crossed Roller Slewing Bearing Pricing
Prices range widely—from hundreds to tens of thousands of dollars—driven by these core factors:
.Size Specifications:Inner/outer diameter and height (width) are fundamental cost drivers. Larger sizes require more material and significantly increase machining difficulty and time.
Precision Grade:Precision amplifies cost. Differences between standard (P0), high (P6), precision (P5), and ultra-precision (P4, P2) grades are substantial. Each higher grade exponentially increases requirements for materials, equipment, processes, inspection, and environment.
Material & Heat Treatment:Special steels (e.g., corrosion-resistant stainless, high-temp steel) and advanced heat treatments (carburizing, bainitic hardening) add significant cost.
Structural Complexity:Features like mounting holes, seals, special flanges, lubrication ports, or signal devices (e.g., integrated encoders) increase machining and assembly difficulty and cost.
Brand & Origin:Products from international leaders (e.g., IKO, THK, Schaeffler, SKF) or made in Japan/Germany typically command higher prices due to technology, quality reputation, and brand premium. High-quality domestic brands offer strong value.
Customization Level: Standard items cost least. Non-standard sizes, special clearances/preloads, coatings (anti-corrosion, low-friction), special greases, or extreme-environment (vacuum, high/low temp) adaptations significantly increase R&D, testing, and production costs.
Order Quantity: Volume purchases typically secure better unit prices, especially for standard items. Small-batch custom orders have higher per-unit costs.
Support Services: Professional selection support, installation guidance, training, comprehensive warranties, and after-sales service also contribute to the price.
Master the Core, Choose Wisely for the Future
Crossed roller slewing bearings are the indispensable foundation for modern high-precision rotational motion. Their unique crossed roller design grants them unmatched load capacity, exceptional rigidity, top-tier accuracy, and ultimate compactness. Whether enabling split-second accuracy in industrial robots, pushing manufacturing limits in precision machine tools, or revealing life’s mysteries in medical imaging, they perform critical functions at the heart of rotation.
When selecting, deeply understanding their advantages over ball bearings and their ideal application scenarios, thoroughly analyzing precision, load, space, and cost requirements, and clearly recognizing pricing factors are crucial. This helps strike the optimal balance between budget and technical needs, empowering equipment with robust and precise rotational power. In the era of Industry 4.0 and smart manufacturing, choosing the right "precision rotating heart" is undoubtedly a vital step toward winning future competition.
Supplier of Slew drive
LYRADRIVE is a professional slewing bearings ,slew drive and gears manufacturer provides customized slew bearing, drive and gears.For application-specific engineering solutions, contact LYRA to discuss technical specifications and implementation strategies.