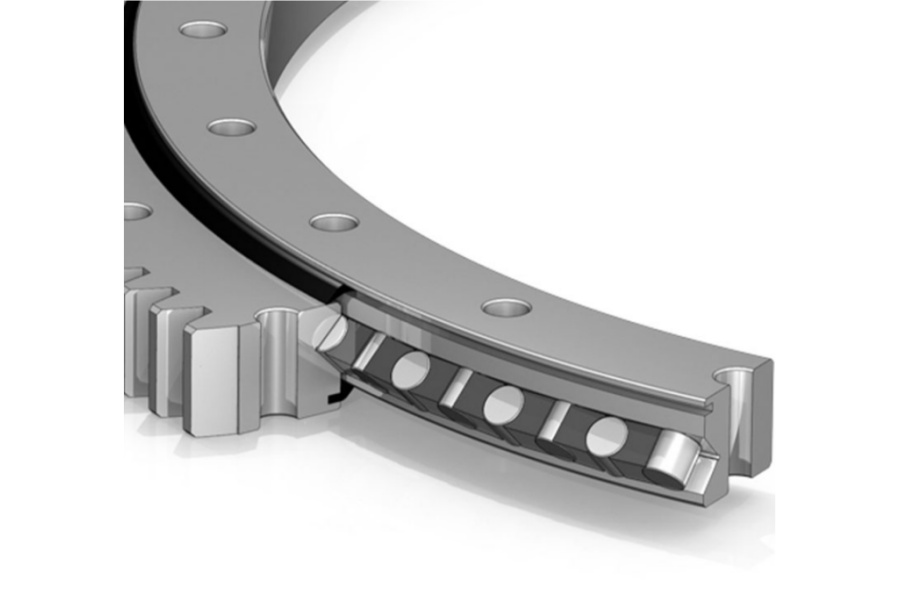
Crossed Roller Slewing Bearings: Pillar of Precision Rotation, Driving Cutting-Edge Technology
What is a Crossed Roller Slewing Bearing?
Imagine a bearing that can withstand huge forces from multiple directions in an extremely compact space - radial forces (trying to separate or press the inner and outer rings), axial forces (thrust along the rotation axis), and overturning moments (torsional forces trying to flip the inner ring relative to the outer ring), while maintaining nearly perfect rotational accuracy and rigidity. This is the core capability of crossed roller slewing bearings. Its name reveals its unique structure: precision cylindrical rollers (or tapered rollers) are arranged in a 90-degree vertical cross pattern between the raceways of the inner and outer rings. This ingenious design allows a single bearing to efficiently replace the radially used radial bearings and thrust bearings that traditionally need to be used in combination, significantly simplifying the mechanical structure, saving valuable space, and achieving excellent comprehensive load performance and motion accuracy.
Axial, Radial and Overturning Moment: King of Bearing in Three-Dimensional Space
The core advantage of crossed roller slewing bearings lies in their unparalleled comprehensive load-carrying capacity:
Excellent Axial Load Capacity: Its vertically cross-arranged rollers provide a large contact area to bear the thrust load along the axis direction (such as the gravity or working pressure of vertical axis equipment).
Strong Radial Load Capacity: Also benefiting from the vertical cross layout of the rollers, it can effectively resist the force perpendicular to the axis direction (such as the weight of the cantilever structure or lateral force).
Amazing Overturning Moment Load Capacity: This is the key that distinguishes it from ordinary bearings. When the load deviates from the rotation center and tends to make the inner ring flip relative to the outer ring, the unique layout of crossed rollers can provide strong resistance to ensure rotational stability. This ability is crucial in application scenarios such as robotic arms and radar antenna pedestals.
This "three-high" (high axial, high radial, high moment) load-carrying capacity makes it an ideal choice for applications with limited space and complex forces, and a single bearing can cope with multi-dimensional challenges.
"Precision Joints" of Robot Arms: Cornerstone of Performance
The agility, precision and reliability of industrial robots, the rotating support of their joint parts (especially the base, shoulder and wrist) is the core. Crossed roller slewing bearings are the ideal choice for these key "joints":
Ultra-high Rigidity: Line contact provides excellent rigidity, with minimal deformation under high-speed movement and heavy load, ensuring the precise positioning and trajectory tracking accuracy of the robot end effector.
Excellent Precision: Excellent rotation accuracy and extremely low repeat positioning error (up to ±0.001° or higher) are the basis for completing precision assembly, welding, inspection and other tasks.
Compact Design: The single-row design provides the function of double-row ball bearings, which greatly saves the valuable axial space inside the robot joint and contributes to lightweight and miniaturization.
High Moment Load Capacity: Perfectly cope with the overturning moment generated by the cantilever structure of the robot arm, ensuring the stability and reliability of joint movement.
Stable Operation: Low friction, low vibration and low noise operation improve the overall performance and service life of the robot. Choosing high-performance crossed roller slewing bearings is a key step in building world-class industrial robots.
Vacuum-grade Slewing Bearings: Precision Rotation in a Dust-free World
In cutting-edge fields such as semiconductor manufacturing, space simulation, and high-energy physics, equipment needs to operate in high vacuum or ultra-high vacuum (UHV) environments. This puts strict special requirements on slewing bearings:
Ultra-low Outgassing Rate: Standard greases and sealing materials will release gas molecules (outgassing) in vacuum, polluting the vacuum environment and affecting processes or experiments. Vacuum-grade bearings use special low-volatility solid lubricants (such as molybdenum disulfide, gold, silver coatings) or vacuum-grade synthetic greases, and adopt metal seals or special low-outgassing sealing materials.
Material Purity and Stability: Bearing steel must have extremely low impurity content to avoid releasing gas or tiny particles in vacuum. Sometimes stainless steel (such as 440C, 17-4PH) or special alloys are used, and undergo special heat treatment and surface treatment (such as passivation) to ensure dimensional stability and corrosion resistance in vacuum environments.
Dust-free Assembly: Cleaning, lubrication and assembly are carried out in ultra-high cleanliness (such as ISO Class 4 or higher) cleanrooms to minimize particle contamination.
Special Design: It may be necessary to cancel or optimize the sealing structure to reduce outgassing sources and ensure reliable operation under vacuum thermal cycles. Vacuum-grade crossed roller slewing bearings are indispensable elements for core components such as lithography machine wafer stages and vacuum coating equipment turrets.
Crossed Roller Slewing Bearings: Core Applications Driving the Future
Its excellent characteristics make it the "rotating heart" in many high-precision fields:
Industrial Robots: Joint bearings (base, shoulder, wrist) provide high rigidity and high-precision rotation.
Precision Machine Tools: CNC turntables, indexing heads, and milling heads realize precision indexing and complex machining.
Semiconductor Manufacturing: Lithography machine wafer stages and inspection equipment stages, whose accuracy directly affects chip yield.
Medical Imaging Equipment: Rotating support of CT scanning racks and positioning of gamma knife treatment heads, requiring stable and low vibration.
Aerospace and Military Industry: Radar antenna pedestals, photoelectric tracking turntables, and missile launchers are stable and reliable in extreme environments.
Precision Measuring Instruments: CMM turntables and laser tracker bases ensure the stability of measurement benchmarks.
New Energy: Slewing support of solar tracking systems for efficient sun tracking.
Vacuum Applications: Precision rotating platforms in semiconductor equipment and space simulation chambers.
Six Core Reasons to Choose Crossed Roller Slewing Bearings
00001. Extraordinary Comprehensive Load Capacity: Single-row design, efficiently coping with radial force, axial force and high overturning moment at the same time, simplifying the design and improving reliability.
00001. Ultimate Rigidity: The line contact structure brings ultra-high rigidity, significantly suppressing load deformation, stabilizing the rotation center, and improving the overall accuracy and response speed of the equipment.
00001. Micron-level Precision: Born for precision, providing extremely high rotation accuracy (running accuracy) and repeat positioning accuracy (±0.001° or higher).
00001. King of Compact Space: Compared with traditional bearing combinations, the axial space occupation is extremely small, which is a key driver for equipment miniaturization and lightweight.
00001. Stable and Quiet Operation: Optimized raceway design, precision manufacturing and preload control achieve low friction, low vibration and low noise.
00001. High Reliability and Long Service Life: High-quality materials, advanced heat treatment and strict quality control ensure durability under harsh working conditions. Special designs such as vacuum-grade and corrosion-resistant meet extreme environment requirements.
Grasp the Core, Wisely Choose Future Power
Crossed roller slewing bearings are the undisputed cornerstone of modern high-precision, high-dynamic rotating motion. Their unique crossed roller design endows them with the kingly spirit to conquer multi-dimensional loads, rock-solid rigidity, precise-to-the-minute accuracy and ultimate space efficiency. Whether it is the high-dynamic joints of industrial robots pursuing millimeter precision, the precision machine tool turrets challenging manufacturing limits, the precision platforms carving chips in vacuum environments, or the telescope pedestals gazing into deep space, they all provide strong and stable core power at the most critical rotating nodes.
When choosing, deeply understanding its core advantages (especially three-way load capacity), clarifying the special needs of the application scenario (such as high dynamic performance of robot joints, ultra-clean requirements of vacuum environments), and clearly recognizing the key factors affecting cost (size, precision, materials, special requirements) are the keys to making the optimal decision. Finding the perfect balance between budget and technical needs will inject strong and precise rotating power into your equipment. In the wave of intelligent manufacturing and technological innovation, choosing the right "precision rotating heart" is undoubtedly a key step to win future competition.
Supplier of Slew drive
LYRADRIVE is a professional slewing bearings ,slew drive and gears manufacturer provides customized slew bearing, drive and gears.For application-specific engineering solutions, contact LYRA to discuss technical specifications and implementation strategies.